Introduction: Mark I Arc Reactor Prop
Hi all!
Thanks for checking out my attempt at recreating the Mark I Arc Reactor from Iron Man. I had a lot of fun building this (so much so, that I made two), and hopefully that comes across here. I've divided the steps by what part is being made, and I use my own terminology for the different part names. The reference shot included above shows what I mean by each part name.
While working on this model, I read through a bunch of other great Arc Reactor Instructables for inspiration, including:
- Sam DeRose's build (and Gordon Gecko's, linked in Sam's)
- backwards lamb's build
- DoggieDoc83's build (a great source of painting/weathering tips)
Thanks to everyone in that list (and the other ones I happened across) for the help.
Most of the major parts are made from laser-cut acrylic pieces, or 3D printed models. The laser cut designs are attached here (.svg, .dxf, and .pdf formats are included). Any 3D models are included in the step where they're introduced.
Throughout this build, I tried to minimize cases where two pieces were joined together by glue/solder/something permanent, opting for a mechanical join instead (nuts and bolts, mostly). I also worked to make it so I can actually disassemble the guts of the model, without having to un-glue anything. This worked, but did lead to some assembly steps being more difficult than necessary (mostly, the control circuit). A lot of these mechanical joins can be easily replaced with glue, and I would recommend that if anything here becomes particularly difficult to work with.
Hopefully, these instructions are clear enough to follow. Unfortunately, I didn't decide to heavily document this build until after I had already started the second model, and I was working to have all the parts ready in short order, so I missed some of the steps. My apologies in advance; Please let me know if there are questions and I can clear anything up.
Parts:
- Plastics:
- 3/8" clear acrylic - Outer capture ring, the large fake solenoid (and an optional stand)
- 1/16" clear acrylic - Perforated metal ring, stacked rings, reactor ring
- 1/8" black acrylic - Reactor cage
- 1/8" clear acrylic - Reactor ring
- PWM circuit
- 2x 1N4148 / 1N4150 / 1N914 Si Diode, 100V 2A - NTE519
- 1x 220uF 16 Volt Electrolytic Capacitor (220uf16vdc)
- 1x ceramic capacitor 0.1 uF +- 20% 16V (VUPN7498)
- 1x ceramic capacitor 0.01 uF +- 10% 100V BX (VUPN6654)
- 1x 8-pin IC Socket (NTE-423-8)
- 1x NTE955MC - CMOS monolithic Timer (555) (NTE955MC)
- 1x NTE 2390 - MOSFET N-Channel Enhancement, 60V 12A (NTE2390)
- 1x Prototyping Board - 1.75" x 1.75" QTY:2 (PH-12-603)
- 1x 10K rotary potentiometer - PCB mount (VUPN6534)
- 1x 10K 1/4 watt resistor
- 1x 1K 1/4 watt resistor
- 1x Male and female JST connector leads
Assorted hookup wire (26 gauge)
- Nuts and bolts:
- M2 x 12mm phillips machine screws, flat washers, nuts (control circuit, crossbrace)
- M5 x 16mm socket cap screws (affixing perforated metal to the reactor ring)
- M5 x 20mm socket cap screws + nuts (harvested for the reactor holding brackets)
- M4 x 20mm mixed head screws + flat washers, lock washers, nuts (fake inductor)
- Assorted accessories
- 26 gauge gold jewelry wire
- 26 gauge magnet wire (red)
- 18 gauge bare copper wire
- 26 or 28 gauge bare copper wire
- 24 gauge tarnished copper colored jewelry wire
- Thin brass sheet metal
- Small ferrite core inductor (non-functional/scavenged is ok)
- A scavenged capacitor of reasonable size
- Male and female jumper wire
Tools:
- Screwdrivers (Philips/flat head), needle-nose pliers, tweezers, sidecutters, wire strippers; Generic hand tools.
- Soldering iron (plus accessories like helping hand clamps, board vice, etc)
- Super glue, plastic model cement, normal white glue (Elmer's)
- 3D printer, or 3D printing service
- Laser cutter, or access to tooling required to cut specific shapes from plastic
Paints:
- Rustoleum flat gray primer (ensure it works on plastic)
- Testors spray enamel gloss copper (number 1251)
- Tamiya Color light gun metal (TS-42)
- Testors spray enamel gloss metallic gold (1244)
- Testors spray enamel chrome (1290)
- Tamiya Color gun metal (TS-38)
- Tamiya Color metallic black (TS-40)
- Tamiya Color semi gloss black (TS-29)
- Testors spray enamel flat black (1249)
- Testors metallic silver (1146)
- Testors flat aluminum (1181)
- Testors flat rust (1185)
- Generic black acrylic paint
Attachments
Step 1: Creating the Reactor Cage - Parts
First up to be built is the reactor cage. All the parts for this are cut from 1/8" black acrylic.
Couple things to note:
- Only 10 of each of the vertical pieces will be used, but there are two extra shown. These were cut just in case any of the 10 broke or were otherwise rendered unusable.
- The base plate and the spacers are missing from the above picture (I had these made already, and forgot to include them).
- The smaller of the three rings has four small holes cut out, two on opposite ends. These line up with the same holes in the crossbar piece (far left). The orientation of these holes is important, and will be noted.
- The thickness of the plastic can vary. The slots are cut assuming the acrylic is a little less than 1/8" thick, with a little variance to account for the laser's kerf. The slots should mesh easily together, with next to no force required (they should actually be a little loose). If the parts don't mesh easily, either widen the slot or thin out the meshing piece of plastic. Forcing the parts together could snap them (and is the reason 2 extras are cut).
- For now, the cross-brace piece won't be used. However, it should be painted and weathered the same way as the rest of the cage.
Attachments
Step 2: Creating the Reactor Cage - Testing the Fit
Before gluing the cage in place, we'll temporarily assemble the pieces together to test the fit and make sure everything can be glued in place nicely.
For this step, we'll be working with the three rings, the 10 taller vertical supports, and the baseplate. We won't need the crossbrace or the short vertical supports just yet.
Locate the larger ring that has three interior tabs. On that ring, there's a rectangular slot cut that lines up with one of the three interior tabs. Take one of the taller support pieces and thread it into this cut, and slot it into the ring at the second slot from the top.
Take the other large ring, and slot it into the same taller vertical support piece in the top slot. Use a small piece of tape to hold it in place.
Now, with the smaller ring, orient it so that the vertical support piece falls halfway between the two sets of holes. Counting from the slot in between the holes, the vertical piece should mesh with the 6th slot. Tape this in place as well. Note: When assembled, the slots on the smaller ring will alternate between the tall and short vertical support pieces. The slots between the holes on this ring will have a short vertical support, then the next one will have a tall support piece, then a short piece, etc.
Slot in another tall vertical support piece opposite the one that's already in place. Make sure that this piece gets slotted into the correct slots on the three rings. Tape this in place.
Now, the reactor cage should start to hold its shape a little better. Take the remaining 8 taller vertical support pieces, and slot them into the appropriate places. Tape these in place. Note that all of the slots on the large rings should be filled, but only half of them are filled in the smaller ring.
Once all 10 tall support pieces are in place, drop the baseplate in to help keep the shape.
Step 3: Creating the Reactor Cage - Gluing (1 of 2)
With the 10 tall vertical pieces in place on the three rings, we can start gluing these in place.
NOTE: The baseplate is not going to be glued in at this step. It will only be used to preserve alignment. Be sure not to apply any glue on this piece.
Pull out one of the tall vertical support pieces, and apply a little glue to the slots, and press it back into the rings. Note that the baseplate may need to be popped out to get the piece in and out. While the glue is drying, I'd recommend leaving the baseplate in.
For gluing, I ended up using plastic model cement. It takes longer than super glue to dry, but it's a lot more forgiving about mistakes, and dried clearer. Leaving these sit for a minute or two was usually enough for the glue to hold, but make sure this is the case before moving on to the next one.
For the vertical piece that goes through the larger ring, tip the piece out of the slot, and you should be able to slide it up or down enough to apply glue to the slots. Then, press it back in place.
Step 4: Creating the Reactor Cage - Adding + Gluing Short Vertical Supports
Once the glue is dry on the large vertical supports, we'll add the short vertical supports next.
NOTE: Once again, we're not gluing the baseplate in just yet. Be sure not to apply glue to this piece just yet.
Collect all 10 of the short vertical supports. Note that 2 of these will have an extra notch cut out of the top. These are the "crossbrace support pieces".
Take the two crossbrace support pieces, and slot these into the smaller ring in the slot between the two holes. These can be glued in, the same way as the taller support pieces: Apply a little glue to the slot that meshes with the ring, and hold them in place. Use the baseplate to keep the alignment while the glue dries.
Once those two pieces are in, repeat the same process with the other short support pieces.
In the end, all of the slots on the three rings should be filled, and the small ring will alternate between tall and short pieces. The baseplate is not glued in just yet.
Step 5: Creating the Reactor Cage - Aligning and Installing the Baseplate
At last, we get to add the baseplate. The baseplate is made up of the small notched disk, plus the two spacer pieces. Before gluing the baseplate into the cage, glue the spacers in place over the smaller two holes on the notched disk. For now, it doesn't matter which side they're glued to, as long as both are glued to the same side. I found that using a bolt (size M2) kept the spacer aligned nicely while the glue dried: Thread the bolt through the hole in the notched disk, apply a little glue to one side of the spacer, and drop this over the bolt. Pull the bolt out, and let the glue finish drying. This makes sure the bolt will fit through both holes again later on.
Once the baseplate is fully assembled, it's time to align and glue it into the cage. Steps later on will depend on particular alignment, so be sure it's correct before gluing.
The two holes in the baseplate will align between a specific set of vertical support pieces: Counting counter-clockwise (looking down from the top) from the crossbrace support piece, the holes will align in the gap of the 6th and 7th vertical support pieces.
When assembling this piece, I found the correct alignment without gluing first. Once I had that, I carved a notch in the slots on the baseplate which align with the crossbrace support pieces. Then, I applied a little glue to each vertical support piece where the baseplate rests, and dropped the baseplate back in. This way, I was sure of the alignment before gluing, and didn't have to rush against the glue drying (I also used the plastic cement again, which gave a lot more time).
Once the baseplate is in, allow the glue to completely dry. The next step will be painting and weathering.
Step 6: Creating the Reactor Cage - Painting an Weathering
Once all of the glue is dry on the cage, the next step is to paint and weather this piece.
NOTE: Up until now, we've been ignoring that crossbrace piece. Bring it back in here, because the painting and weathering schemes used on the cage will apply to this piece too.
First up, apply a solid coat of primer. For this, I used rustoleum's primer that says it worked on plastic. I can confirm it worked on plastic pretty well. Make sure that all sides are covered, both inside and outside. Pay particular attention to the undersides of the rings. I sprayed the cage upside-down first, and then right-side up to get full coverage. Allow the primer to dry fully (usually 24 hours)
Next up, apply a silver/chrome color. I used Testor's chrome spray enamel paint (number 1290). Follow the same process as the primer, making sure everything gets covered. We'll be sanding the topcoat down to reveal this one, so making this layer a little thicker (by applying multiple light coats, not one heavy one) will probably help. Allow this coat to dry.
Finally, apply a black color on top of this (or whatever you want the cage's primary color to be. I used black because it contrasted with the silver). For this, I used a semi-gloss black color (Tamiya Color's TS-29). Make sure that all of the chrome paint is covered. Allow this final coat to dry.
(Reminder: make sure that the crossbrace is painted the same way).
Once the paints are dry, it's time to weather the cage. To accomplish this, we'll be sanding off parts the black topcoat to reveal the chrome paint beneath. The goal of this is to make it look like the actual coating on the cage wore off over time, so the focus here will be on any exposed areas such as corners, outer edges, etc. Take a piece of fine sandpaper (I used 400 grit, but anything higher will work even better), and lightly start removing the black paint on the exposed edges. I tended to focus on the baseplate, and the three rings, and didn't do so much on the interior. When removing the paint, take off just a small amount at a time, until the desired effect is achieved. Just be careful not to remove any of the chrome paint. Once everything looks good, clean off any dust, and give the paint another day or so to completely dry.
With the weathering now completely dry, I applied a clear coat sealer to the entire cage, to keep the paint safe. This step is optional. For this, I used the matte clear coat sealer from rustoleum. There's also a gloss clear coat, but I liked the look of the matte version better. Apply a couple light coats of this, ensuring once again that everything is covered.
Once everything is dry, set the cage + crossbrace piece off to the side. We're done with these for now.
Step 7: Creating the Capture Ring - Cutting the Capture Ring
With the cage in place, next up is the outer capture ring. With the wire-wrapped magnets and wires, this is one of the primary defining features of the reactor.
The ring itself is cut out of 3/8" clear acrylic. Note that the ring is not perfectly circular. Around the edge, I flattened out 10 different sections, equally spaced around the edges. This was a holdover from an earlier design, where I applied magnetic tape around the ring. These flat sections made aligning the tape a lot easier, since it was hard to bend already. Now, they just provide a convenient way to align the new magnet pieces.
Once this piece is cut, it can be set off to the side for now. If desired, you can use a light sandpaper or scouring pad to give this ring a frosted look. I tried both clear and frosted, and preferred clear. If you want a frosted version, I'd recommend frosting it now before the magnets are attached.
Step 8: Creating the Capture Ring - Preparing the Magnets
The magnets are 3D printed (.stl file is attached), prepped, painted/weathered, and sealed. I had these printed by shapeways, but most any 3D printer should work with enough finishing work. The pieces came back a little rough texture-wise, but this is easily fixed with a light sanding. I also found that one of the grinding bits on a dremel worked really well for this. It might not be as visible, but I'd recommend cleaning up the inside faces too, to make sure the piece still fits around the capture ring.
Once the pieces are smoothed out, the next step is to paint, weather, and seal the magnets. This follows a similar process as the cage, but using different colors, since I wanted these pieces to look like they were made out of a different material than the cage. The base coat of primer is the same. For the middle layer, I used a "light gun metal" color (Tamiya Color's TS-42), and the top color was a "metallic black" (Tamiya Color's TS-40). Once all these layers are dry, "weather" the parts in the same way as the cage. For this part, I focused mostly on the outside faces of the magnets, and the top edges. I didn't bother weathering the interior as much. Once this is done, apply a clear coat sealer (optional. I used the same matte clear coat as last time).
Step 9: Creating the Capture Ring - Installing the Magnets
With the painting done, the magnet pieces will now be attached to the clear ring, and wrapped with magnet wire.
These should slide onto the capture ring without much force. If it is hard to install them, use a little light sanding to clean up the inside edge of the magnets, or the flat face on the clear ring. Once the fit is confirmed for each of them, apply a little glue to the inside of the magnet piece, and glue it to the clear ring. I used the plastic cement for this (clear-drying was a priority here). Use just a tiny amount, and be careful of any glue bleeding out around the edges.
To wire-wrap the magnets, I used 26-gauge magnet wrapping wire. The red coating contrasted nicely with the black of the magnets, and it was easy enough to work with (plus, one spool could cover 80 or so magnets, based on my testing).
I couldn't easily fit the spool itself through the center of the capture ring, so I harvested a smaller spool from elsewhere and used this. This had the added benefit of securely fitting over the magnets, so I could keep the spool in place while switching hands. I unrolled about 20-ish turns of wire from the big spool, which ended up leaving about a foot or so left over.
To start wrapping the magnets, I found gluing one end of the wire in place on the magnet made this significantly easier. For no discernible reason, I wrapped from right to left, when looking at the magnets from the top. So I glued the leading edge of the wire in place on the inside of the magnet. I left a little bit hanging over the edge, which I just tucked under while winding. Once the glue is dry, pull the wire taut and start wrapping it around the magnets. Keep each rotation as close as possible to the last one. When you need to switch hands, "dock" the spool on the magnet piece, swap hands, and resume. Once you've reached the end, finish one more rotation that sits on top of what was wound already. Apply a little glue to this on the inside edge of the magnet, and once it's dry, cut off the excess. Optionally, I put a line of glue across the wire on the bottom edge. My hope was that this would prevent unraveling (and so far, it has worked).
Repeat the same process for the other 9 magnets.
After the wire wrapping was done, I decided to weather the magnets a little, since I felt that the bright red didn't look like it fit in with the other pieces. I dry-brushed a "rust" colored paint onto the wire all around. I was mostly careful to avoid the body of the magnet. No real harm if a little bit of this paint gets onto the body. I also took a knife or file, and scraped off bits of the red sheathing, to expose the silver color beneath, focusing mostly on the corners. This could also be replicated with some silver paint. I also covered the glue from the wrapping step with a little silver paint, making it look like a solder joint.
For now, this part is done. Once it's attached to the cage, we'll need to attach the gold jumper cable things that go between each magnet, but that's a lot easier at a later step. Stash this part safely until then.
Step 10: Creating the Perforated Metal + Floating Ring Assembly
The next piece up on the list is the perforated metal + floating ring assembly. Besides the capture ring, this is the other prominent feature on the reactor.
The perforated metal piece is just cut out of 1/16" clear acrylic. Not much else to do there for now.
The floating ring assembly is more interesting. It's made of four pieces: The three holding arms, and the ring in the center. The center ring is just a repurposed keychain ring. I found a two-pack of these at a hardware store, and they're about an inch in diameter. The holding arms are designed for a specific diameter ring, so if you have something different, it may require re-designing the holding arms.
The holding arms are 3D printed (shapeways again). They're made out of the same material as the magnet bodies, so they'll need some cleanup. Most of this can be done the same way as before, and I used a small set of files to clean up the interior parts of the holes. Due to the fine detail on these parts, I chose to leave these a little rougher, rather than risk breaking them. Some of it will be cleaned up automatically during painting.
The holding arms have a notch on the end onto which the inner ring will rest. To assemble this piece, I dropped a bolt through the holding arms and perforated metal, and attached a nut to the other end. From there, the inner ring can be test fitted, and once the alignment is correct, it can be glued in.
Both pieces are now ready for paint. The inner ring of the floating ring assembly should be taped off, since that doesn't need to be painted. I suppose these steps could be done in reverse (paint the holding arms, then glue everything together), but I've had mixed results when gluing after painting, so I did it this way). The paint scheme here is not as complex as the other pieces: A coat of primer, and then a coat of "gunmetal" (Tamiya Color's TS-38). I didn't bother with a clear coat on these pieces.
For weathering, I just dry-brushed a little silver and rust colored paints on the pieces after the gunmetal color dried. While I had them out, I did the same thing to the bolts.
In some of the reference shots, there's a coil of wire behind the perforated metal ring. To copy this, I printed a frame/template thing that was the same outer diameter as the bolts, and wound some dark copper colored wire around that frame. 10-12 times around looked sufficient. There's a slot cut into the frame so I could put a piece of electrical tape around the wire to hold it in place. I left about a foot or so of extra wire on one of the ends, and trimmed the other back at the tape. With the extra foot of wire, I wound that around the wire, to keep everything in place. At the end, I just tied this off, and cut off the extra. This ring then should fit around the three bolts, but may need to be deformed a little bit.
We'll need to disassemble this piece later on, but it can be kept assembled to prevent damage.
Step 11: Creating the Stacked Rings/heatsink Assembly
Next up is stacked rings assembly. Unfortunately, I don't have many "in progress" shots of this piece, as I finished it before documenting the build. It should be fairly straightforward though.
The pieces are cut out of 1/16" acrylic. There will be a total of 5 rings, one of which has three notches cut around the outside, and a small ridge carved into one side. This ridge will eventually hold the screen mesh. Note that the ridge side of the smallest ring is facing down (e.g. facing "out" of the assembly). The three vertical support pieces will slot into the notches on the smallest ring, and the other four rings will rest on the flat, horizontal areas of the vertical supports. Before assembling the pieces, I'd recommend lightly sanding the edges, to give the primer/paint a better surface to adhere to. This can be done after assembly too, but it's significantly easier here.
We'll start by gluing two of the three vertical pieces into the slots in the smallest ring. The bottom of the ring and the bottom of the vertical piece will be co-planar, so it should be easy to glue these in roughly the correct alignment. Once these two are in place, we can add one of the rings to pull all three vertical pieces into the correct alignment. Drop the ring in (but don't glue it in yet). Glue the last vertical piece into the smallest ring, while using the other ring to hold the vertical piece in the correct alignment while the glue dries.
When all of the vertical pieces are dried to the smallest ring, glue the four remaining rings in, one by one. We'll be painting this first, so don't add the mesh yet.
For this piece, I used a metallic gold color (Testor's 1224). Weathering will be done once the mesh is in place.
For the mesh, I used a piece of a screen door repair kit. Cut out a piece roughly the size of the ridge in the smallest ring, and compare it to the actual size. Iteratively trim this piece down until it fits into the ridge. Once that's done, apply a little bit of glue to keep it in place.
To weather this piece, I dry-brushed more of the "rust" color on. Cover the mesh and the stacked rings. I also had a wash of black acrylic paint left over from a different piece, so I used a little bit of this as well. The goal here is primarily to take away the shine of the gold paint.
At some point in the future, we'll need to attach this to the perforated metal piece. It doesn't have to be done now, but there's little reason not to. This will just be glued to the back of the perforated metal piece. Because I cut 7 notches in between each bolt hole in the perforated metal piece, we're not going to be able to get this piece exactly in the center, so just choose either the left or the right of the center. Apply a little glue (I used the plastic cement again) to the top of the vertical support pieces, and attach it to the back of the perforated metal piece, centered as best as possible. Hold this in place until it dries.
This piece is done for now. The floating ring/perforated metal/stacked ring assembly can be stashed somewhere safe for now.
Step 12: Creating the Control Circuit - Circuit References and Breadboard
Alrighty, the control circuit. This piece probably presents the most challenges in this build, between building it and actually getting it into the cage. However, the benefits outweigh these challenges (I think, at least). My original intention for this part was to just glue a bunch of components to a protoboard and call it a day. Then I found out that PWM circuits can be built using easy to find, discrete components, and I couldn't pass that up. The circuit looks like something that could be built in a cave with a box of scraps, and it allows the LEDs in the reactor ring to be dimmed? Yeah, we're going for it.
I used a number of different references for building this circuit. Instructables has a number of references for PWM circuits, but unfortunately a lot of those rely on a microcontroller to generate the PWM wave. Sparkfun has a brief discussion of dimming LEDs using a 555-based circuit, here: https://learn.sparkfun.com/tutorials/led-light-bar-hookup/all. The circuit diagram on that page is what I ended up using to design my circuit. This page (http://www.555-timer-circuits.com/pin-configuration.html) also does a good job of talking about how the 555 timer works, and explaining the pin configuration. There are a number of other references available online that do a really good job of explaining the theory of the circuit, presenting examples, etc.
I bought most of the parts from a local electronics supply store (Vetco). Below are the components I ordered:
5 x 1N4148 / 1N4150 / 1N914 Si Diode, 100V 2A - NTE519 (NTE519) = $5.95
2 x 220uF 16 Volt Electrolytic Capacitor (220uf16vdc) = $1.44
2 x ceramic capacitor 0.1 μF ±20% 16 volts (VUPN7498) = $0.58
2 x ceramic capacitor 0.01 μF ±10% 100 volts BX (VUPN6654) = $1.00
2 x 8 Pin IC Socket (NTE-423-8) = $1.50
2 x NTE955MC - CMOS Monolithic Timer ( 555 ) (NTE955MC) = $3.42
1 x 26 AWG Solid Single Conductor Hookup Wire - Red - 25' (NTE-WHS26-02-25) = $4.28
1 x 26 AWG Solid Single Conductor Hookup Wire - Black - 25' (NTE-WHS26-00-25) = $4.28
2 x NTE2390 - MOSFET N-Channel Enhancement, 60V 12A (NTE2390) = $6.60
1 x Prototyping Board - 1.75" x 1.75" QTY: 2 (PH-12-603) = $4.39
Note that the quantities there are two build two of these circuits. When I started building this reactor, I had plans to build a second one too, so I ordered doubles of this right away. Some other parts for the circuit I ended up scavenging from what I had lying around (namely, a couple resistors, and the 10K potentiometers that I used instead of the 100K ones on that order). I also picked up the JST connector cable (that ends up connecting to the power supply) from a local hobby store. I think Vetco sells them too.
With all the parts on hand, I next prototyped the circuit on a breadboard, to see how it would work (or more accurately, if it would work). In the circuit diagram resistor R1 (the 50K) is replaced by the 10K potentiometer, but that's really the only difference.
Couple notes on the circuit itself:
Note the orientation of the diodes attached to the potentiometer. Reversing these causes the LEDs to dim the wrong way (i.e. turning the potentiometer down will make the LEDs brighter, and turning it up will dim them).
The blue capacitor (the electrolytic one) must be installed so that the "- -" end is tied to ground. Reversing this is dangerous. The orientation of the other two capacitors does not matter.
One note on transistors: For anyone not familiar (this was definitely me going into this, and still is), there are three pins on the transistors: Source, Drain, and Gate, marked S, D, and G in the diagram above. Gate is self-explanatory: This is connected to whatever's going to trigger the transistor (in this case, pin 3 of the 555 timer). Source and Drain are misnomer-y though. "Source" does not mean the source coming into the transistor, but rather the source coming out of the transistor (i.e. "Source" means the output from the transistor). Likewise, "Drain" refers to what is coming in to the transistor (i.e. the input). This threw me off initially, and I still have to stop and think about it. Just something to keep in mind.
Step 13: Creating the Control Circuit - Protoboard and Soldering
With the circuit working on the breadboard, the next step is to copy it to the protoboard. Since I had purchased enough parts to make two circuits, I was able to leave the breadboarded circuit as it is, and use it for reference (checking orientations and connections).
Most of this circuit design will be an exercise left up to the reader (sorry, I had to finish the circuit under a time crunch and didn't finish collecting pictures). I'll provide what references I can, but the actual design is a little hard to convey via words.
A couple important things to note though:
1. The protoboard I used is not perfectly square, in the number of through-holes along each side. It's actually 15X16, rather than a square 16X16. This orientation is important, and is noted in one of the pictures.
2. Since this circuit will be dropped in to the cage later on, I needed a way to attach it. Rather than use glue, I opted to use a small set of nuts and bolts. To that end, there are two symmetrical holes drilled into the protoboard that line up with the small holes and spacers on the baseplate. When assembling this circuit, be aware of these holes, and allow enough clearance for the nuts, bolts, and spacers on either side. This piece was a major source of frustration in the final assembly stage, so if you can find an easier way around this, I'd recommend it. There are definitely cheats that are possible (namely, glue)
Some basics about this overall design:
The 555 timer can be seen in the first couple photos. Note the orientation of the timer, specifically that the dot (marking pin 1) is towards the center of the board.
I used the longer leads on some of the components to make a 5V and Gnd rail on either side of the board. The other leads could just tie into this.
Most of the parts were packed to avoid the mounting holes as much as possible. There's probably a better orientation for these parts, but this design worked.
The area behind the potentiometer is intentionally left empty. I had a solenoid lying around that was the perfect fit to drop in there. It's not actually connected to anything, but does a good job filling up the space. Right next to that, I added the female end of a 2-pin JST PH connector. The leads from this get threaded below the board, through the baseplate, and connected to the fake plug.
Apart from this, the rest of the parts were kind of just dropped in wherever they fit, and connected in however I could. As long as it fits in the bottom section of the cage at the end, we should be good. The overall aesthetic of this is "built in a cave with a box of scraps", so having the jumper wires running all over the place helped with that.
Once the board is all assembled, we'll need to trim it down to fit into the cage. For this part, I cut off the excess parts of the board as close as possible to the assembled pieces, and used a file or dremel's grinding bit to clean up the edges. You can test fit in the cage, and see what needs to be removed as you go. It should fit all the way in the bottom, squarely on the spacers attached to the baseplate.
Step 14: Gap-filling With a Fake Inductor
Above the control circuit but below the primary reactor ring, I had a significant gap to fill. To fill that space, I created a fake wire-wrapped inductor that sits on the crossbrace piece. This piece also has a lead that threads through the baseplate on the reactor and connects to the (non-functioning) plug.
The "core" of the inductor is a piece cut out of the same 3/8" acrylic as the capture ring. There are two holes cut into opposite ends which allow this piece to be connected to the crossbrace.
This piece is primered and painted with a metallic black color (Tamiya Color TS-40). Once that's dry, a dry-brushing of silver all around makes the piece look worn. I didn't bother sealing this piece.
Once all that paint is dry, I wrapped some 18-gauge bare copper wire around most of the core, leaving space near the holes for the bolts. 8-9 feet of the wire should be sufficient to wrap the core as shown. To make the winding a little easier, I threaded the wire through the core to the halfway point, and then wrapped the core as two halves rather than all in one go. Dealing with 4 feet of ungainly wire is easier than 8 feet. For the most part, this wire kept its shape when bent, but I added a little glue to the ends to keep them in place. Once that glue is dry, a little silver paint makes these look like a solder join.
I didn't do anything specific to weather the copper wire. Just handling it was starting to tarnish it, and I was happy with that look.
I also decided to add an extra capacitor to this piece (to take up even more space). This is just soldered to somewhere on the wire, near one of the ends. To the other end of the capacitor, I stripped and attached a female jumper wire (keep this length as long as possible) and covered that with some shrinkwrap. This wire will eventually connect to the fake plug in the end.
When this piece is complete, it can be attached to the crossbrace piece. For this, I used some M5 x 20mm stainless steel bolts. To add to the scavenged look, I used different bolt heads on either side (phillips on one side, socket cap on the other). The arrangement from top to bottom is:
M4 x 20mm bolt -> M4 flat washer -> fake inductor -> 1/8" plastic spacer -> crossbrace -> M4 flat washer -> M4 lock washer -> M4 hex nut.
I used the lock washer because the nut kept coming loose. If you can get it to stay in place without the lockwasher, go for it.
I also attached a diode to one of the bolts, opposite the capacitor's lead. One lead on the diode is wrapped around the bolt head, and the other is soldered to a short female jumper wire. This will end up attaching to a pin on the control circuit. This piece was optional, and I just used it to fill space, and make the inductor look more functional.
Step 15: Creating the Reactor Ring - Building the Supports and Heatsink
Nearly there. The final pieces to make are the reactor ring itself, and the structure that holds it in place. Up first is the supporting brackets and heatsink (STL files for both are attached).
The heatsink part is 3D printed. I had this piece printed in a higher-detail material (again from shapeways), so these required less clean up/smoothing than some of the other parts. Depending on the orientation in the print bed, the underside of the ring, or the pipes, are most likely to require smoothing. As before, this can be done (carefully) with the grinding bit in a dremel. After everything is cleaned up, I sprayed a coat of primer on the piece, and when that was dry, I taped off the three pads, leaving just the pipes exposed, and painted it using a gloss copper color (Testor's, number 1251). After the copper paint is dry, I removed the tape, and brushed on a couple light coats of an aluminum color on to the pads (Testors flat aluminum number 1181).
I did a little less weathering on this part. On the pads, I used a fine sandpaper and lightly roughed up the corners/edges, to make it look a little worn. For the copper parts, I used a rinse of black acrylic paint to get a little color into the corners and between the pipes. I left this pretty subtle.
The supporting brackets were similarly built. I 3D printed these again (but not shapeways this time), and the individual layers are pretty visible. A rough sandpaper (220 or 320 grit) makes pretty short work of this. I also used a fine file to make sure that the faces were still square and the edges were distinct after sanding. For any large holes or gaps (depending on print quality), I had good results using a model body filler, and sanding that down. The interior faces of the brackets were left a little rougher (since they'll be hidden anyway). There were a couple places where the printer missed material, or the shell was a little thinner leaving a small hole. Rather than try to fill all of these gaps and get a perfectly smooth finish, I left some of the smaller marks as they are.
Before painting these pieces, we'll need to attach the threaded portion. Trying to print this model with threads built in was not working, so I opted to attach these separately. To accomplish this, I cut about 1/2" off of an M5 bolt, and glued it into a small indent in the bottom of the model. The actual thread pattern doesn't really matter, as long as you have a nut to match it. The hole was designed for an M5 bolt, so using other sized may not produce the best results.
After installing the bolt, these pieces were painted the same way as the heatsink pads. I taped off the bolts because I wanted to keep them a different color. These can be either sprayed or brushed; I opted to brush since I didn't have the aluminum color in a spray version. I also didn't bother primering these parts this time around; It seemed to work out fine. Weathering was done the same way as before: fine sandpaper to rough up the edges. I also dry-brushed a little silver and rust colors on to the bolts, and a little rust on the nuts (since they were already silver).
To make painting the brackets a little easier, I printed out a holding rack thing (stl file is attached). The pieces can be set into here while they dry, allowing all sides to be painted at once.
Step 16: Creating the Reactor Ring - Building the Plastic Case
Two more parts to build for the main reactor ring. There is the plastic case for the LEDs, and then the LED ring itself. We'll start with the plastic case.
This went through several different iterations. I first tried embedding the LEDs directly in clear epoxy but the first attempt constricted as it was drying, making one face curved rather than flat (this was not unexpected, based on the epoxy used). The second attempt, using a different epoxy, dried flatter. However, this epoxy was more susceptible to heat, and leaving the LEDs running for longer than 5 or 10 minutes would generate enough heat to start melting this epoxy. No good.
The end result that I settled on consists of four different parts: A top and bottom plate, and two walls. The LED ring fits inside here. The top and bottom plates are cut out of 1/16" acrylic, and the walls are cut out of 1/8" acrylic (giving a total height of 1/4", the same size as the supporting bracket opening). However, the LED's I'm using (blue LED sequins from Adafruit) are just a little bit taller than 1/8". To combat that, I used the laser cutter to etch out a groove in the top and bottom plates, giving enough space for the LEDs while preserving the total piece height of 1/4". The bottom plate also has two holes cut into it, through with the + and - leads for the LED ring is threaded.
Since we still need to add the LED ring, assembly for now consists of gluing the inside and outside walls to the top plate (the one that does not have the small holes cut into it).
Step 17: Creating the Reactor Ring - Building the LED Ring
At long last, we can start building the heart of the reactor, the glowing LED ring.
For this part, I used 12 of the blue LED sequins from Adafruit, in 6 pairs spaced equally around the ring. Rather than guess at the spacing, I printed out a wiring guide (attached) that holds the LEDs in place while they're soldered. The LED's are placed back to back, so that they shine out sideways, away from eachother. Having them in this orientation helped to dissipate the glow more, as opposed to having the LEDs shine straight up. I used a thin bare copper wire (26 gauge, maybe?) to connect them together.
When wiring the LEDs, be sure that the + and - sides are correct. I opted to keep the - end on the inside of the ring, and the + end on the outside. To get started, thread about 12 inches of the copper wire through two of the LEDs, leaving about 1 inch on one side of the LEDs and 11 inches on the other. Drop this into the wiring guide such that both LEDs are sitting in the slot on the outside of the guide, and solder in place. Feed the 11 inches of wire into the grooves in the guide, to help hold it in place. This will also start to bend these wires into a circle. Because of the back to back orientation, soldering here requires two steps. Solder one LED (both + and -) while it's in the guide. Pull the ring out, and then solder the other LED in place.
Once the first set of LEDs is done, thread on the next two. Remember to keep the correct orientation. The LEDs that were just soldered will now fit into the slot in the middle of the wiring guide, and the next set of LEDs to be soldered rests in the slot on the outside. Solder these new LEDs in place, and repeat until you've added 6 pairs of LEDs (12 total). While building this, I tested the ring after each LED pair was added, to make sure the joints came out correct. I plugged the ring directly into the 5V power supply, but you can always test this through the control circuit too (this tests both at the same time). This isn't necessary, but it's a lot easier to fix a bad join now rather than later.
After the last LEDs are soldered in, there will be a couple inches of the excess wire to trim off, from both ends. These can all be cut as close to the LEDs as possible. The end result will be something that looks like a "C", rather than a true "ring".
With the ring of LEDs glowing nicely, the next step is to get them in the case. Cut a pair of female jumper wires to about 3 inches, and strip off the insulation on the ends. I'd recommend test-fitting these pieces into the cage, to get an accurate measure of how long the leads should be. Take the bottom plate from the previous step (the one that does have the holes in it), and thread the leads through here. Ensure that the smooth part of the plate is still on the outside. Solder these leads to the LED ring.
Now, we should be able to drop this piece onto the other half of the reactor ring case. The ring may have to be bent into shape a little to get the LEDs in, but for the most part everything should align automatically. Both sides of the case should meet without any gaps.
Note 1: I opted not to glue the two sides of the case together. The support brackets will hold them closed anyway, and this makes it a lot easier to change something out if I decide to go with a different design later on, or an LED burns out, or whatever.
Note 2: Due to the kerf of the laser, and how well each piece was aligned when making the case, the outside edges are likely to not be perfectly vertical, and the gap between pieces is probably visible. To fix this, I went around the edge using a sanding drum on a dremel, and afterwards a file, to smooth out the edges and get it to as close to 90 degrees as possible. After this was done, I also took a piece of fine sandpaper, and went around all the exposed faces on this piece. This accomplished two things: smoothing out what the file might have missed, and giving the top and bottom a frosted look, to help with diffusing the LEDs.
Note 3: I also added a little bit of glue around the LED leads where they entered the case, as a form of bending strain relief.
Whew. Apart from some minor detail work, this ends the "make pieces" portion of this build. The rest will be assembly.
Step 18: Assembling the Reactor - Adding the Control Circuit and Inductor
Ok, we're finally done building things. Now comes the other part: assembly. The first part will be to get the control circuit and the large inductor in place.
Feed the ends of the two wired coming from the control circuit and the one wire from the inductor through the baseplate in the cage. Drop the control circuit in, and try to line up the holes with the spacers in the baseplate as much as possible. The inductor will drop in next. As this part is dropped in, keep pulling the wire out through the baseplate, around the control circuit. It will take some tries, but the inductor will/should fit through the top part of the cage without forcing anything. Try to remove as much slack on the three wires (red, black, and white in the above pictures) as possible while dropping these pieces in, and try to keep them from getting pinched in between the board and the spacers in the baseplate. They should easily fit in the gap.
Once both pieces are roughly in the correct position, attach the control circuit to the baseplate. I used the two bolts (I also included a washer on the outside as well) to hold the circuit in roughly the correct position (at least, the correct position rotationally). With a small pair of tweezers, align one of the M2 nuts over the bolt, and try to catch the bolt on the nut. These can be tightened down securely at this point. Based on the way that I set everything up, this part was probably the most difficult step in the final assembly (why I had to have that extra wire from the inductor feed through the baseplate, I'll never know). It was really easy to drop the nut, or miss the bolt, or have the circuit move out of alignment. A fair amount of patience will be required here. I promise that this is the most difficult part.
The inductor can also be bolted in at this point. The same M2-size bolts which hold the circuit in place will hold the inductor too. On the crossbrace piece, there are two holes on either side that line up with the holes in the cage ring. Drop a bolt + washer through each of these, and attach a nut to the other end.
If you opted to include the fake diode on the other side of the inductor, this can be attached now. For this part, I just found an empty hole on the circuit board near the diode, glued in a header pin (to the board, not the diode), and attached the diode's female end to it. The nut holding the inductor in place can be loosened a little bit from outside the cage, and the other end of the diode can be wrapped around the bolt. Re-tighten the nut, and this is good to go.
Step 19: Assembling the Reactor - Adding the Reactor Ring, Attaching the Capture Ring
The next piece to be added is the reactor ring.
If it's not done already, assemble the reactor ring, the support brackets, and the heatsink into one piece. With the two sides of the reactor case mated (and the LEDs secured inside), slide the three support brackets over the case. The open ends of the brackets will be facing out (so, attach them from the inside of the reactor ring). Space them roughly equally around the ring.
Next slide the heatsink over the support brackets, threading the bolts through the pads of the heatsink. This part is pretty fragile, so don't force the pieces together; They should fit together without much effort. If not, check the alignment of the support brackets, and space them out more or less, whichever direction is needed. Also, make sure that the brackets slide on to the reactor ring as much as possible. Also also, try to push the heatsink on as evenly as possible (i.e. don't push one pad all the way on then try to push the other two on).
Now, fit this piece into the cage. This should fit into the three tabs on the middle reactor cage ring. Due to variances in how the brackets were printed, how the bolts were attached, how the reactor ring case was assembled, etc, these might not fit perfectly. This piece should drop in with only a little force required. If the fit is too tight, use a file to widen the holes a little bit at a time until the piece fits. When dropping the ring in, be aware of where the + and - lines will end up. These need to attach to a specific place on the control circuit, noted in a previous step, so make sure that the leads line up on this side of the board.
After the ring is inserted into the cage, attach the + and - leads from the LEDs to the appropriate pins on the board. If you want, you can test the LEDs at this point, and make sure everything works. The next step will be to secure the ring to the cage, using the nuts that match the bolts used on the brackets. Because I am a sadistic designer, there is a very small amount of clearance between the inductor and the bolts. So much so, that the nuts can't actually be dropped onto the bolts. Instead, we'll need to slide the brackets into the nuts, and tighten them slowly (I'm strangely proud of this part).
Flip the cage upside down, and pull the ring out of the cage just a little bit, until the bracket bolts are all flush with the "bottom" (which is now, visually, the top) of the tabs in the cage. Then, align a nut over the bolt, and push that bracket back into the cage just a little bit. Start tightening the nut onto the bolt, just until it catches. Repeat this process for the other two bolts.
Once all of the nuts have been started, rotate around the ring and slowly tighten each nut until the ring is secured. Try to keep the bolts roughly level during this process (i.e. tighten one nut a little bit, and move on to the next. Don't try to tighten one all the way down in one go).
Attaching the capture ring is, thankfully, easier. It's just glued to the cage. For this part, I used a mix of plastic cement and super glue. Apply one glue or the other to the tops of the 10 taller vertical support pieces on the cage, line it up with the backs of the magnets of the capture ring, and drop it on. Note that this will be glued to the wire that we wrapped around the magnets, so be sure to use enough glue to provide a solid hold. In retrospect, using glue on all 10 was probably overkill, but I'm not taking any chances. Let this glue dry completely (I opted for overnight).
Step 20: Assembling the Reactor - Perforated Metal + Floating Ring Assembly, Detail Work
Once all of the glue is dry, and the capture ring is securely attached to the cage, we can start adding some of the detail pieces, the first of which being the jumper wires and solder pads going between each magnet.
To create the solder pads, I cut up a piece of thin brass sheet metal into roughly square shapes, about 1/8" square. Then I glued these (using a tiny amount of superglue) to the magnets. There's four per magnet, making for 40 total pieces. Luckily, accurate alignment, or consistency in the shape, or anything like that is not required, so this approach worked great for that.
After the solder pads are dry, it's time to attach the the jumper wires. I used some 26 gauge craft/jewelry wire, and chose the color to match the solder pads as closely as possible. Cut out some short lengths to span the gap, and clue these in place. I used superglue again for these, but anything would probably work. There's 20 of these total to do (10 larger gaps, and 10 smaller gaps). Once these are dry, I dabbed some silver paint on the pads, to (a) cover the glue and (b) look like actual solder.
At this point, we can also add the perforated metal/floating ring assembly to the reactor. The M5 x 16mm bolts will attach directly to the reactor ring support brackets. Be careful screwing these in, to not break anything. I tended to just tighten these enough to hold everything in place. The pieces should stay securely attached though.
The final piece that needs to be done is the plug on the end of the external wires. For the actual plug, I used one of these microphone connectors: http://www.vetco.net/catalog/product_info.php?cPat... I cut off the threaded portion covering the pins (which had the beneficial side-effect of leaving a shredded pattern on the end). The red and black leads coming out of the reactor will be a bit longer than the white lead, so these need to be trimmed back. I ended up having about 5 or 6 inches of wire extending out the back. For the white piece, I cut a male jumper wire to about 1.5 inches, and attached that to the plug instead (this way, I can still disassemble the reactor, if needed). The red and black wires can just be attached directly to the plug. I used glue (easier), but solder will also work. To complete the look, I applied a bit of shrinkwrap to the joints on the plug end.
Optionally, I also added a rubber grommet to where the wires leave the baseplate, to clean up the look. If you want to add this, cut it so it can be pulled open, and cut off one of the overhanging parts, so it ends up looking somewhat like a mushroom. This can be wrapped around the external wires, and pushed into place.
To power the reactor, connect a sufficient power supply to the JST connector. Anything around 5V should be good. Too high will risk damaging the 555 timer or the LEDs, and too low may prevent the 555 timer from working.
Step 21: Reacting to the Reactor - Wrap Up, Final Thoughts, Next Steps
Welp, you made it! (in that you either just completed your own version of this, or you just happened to arrive on this page. Either way, well done!). Having now completed two of these builds, I had some final thoughts to share, that might be useful, or inspire your own variations:
- Next time, I don't think I'd try so hard to make the model disassemble-able. It obviously wasn't impossible to do, but the control circuit in particular caused quite a bit of frustration. It's cool that I can take it apart if I want to change something, but I don't think it's vital.
- Keeping the parts modular definitely did help, and I'd definitely do this again. This is probably a consequence of number 1 above. There were several times during construction where I changed the design somehow, and I was able to introduce the new part without scrapping everything I had done up to that point (see: the reactor ring, the perforated metal assembly).
- I've considered using a denser set of LEDs to get more light for the ring (such as the neopixel rings from Adafruit, one of which is surprisingly the exact dimensions I need), but the problem I have with these is the light only shines in one direction; I'd rather have a dimmer omni-directional light than a brighter, focused light. But maybe I'll experiment with these, and see what they look like. This would also allow me to change the color from solid blue to a mix of blue and white, or add different effects like a pulsing glow.
- I haven't yet tested running this at full power for extended periods of time. For about the last month, I've had it running at about 1/3 or 1/2 power, for 9 or so hours at a time, and I haven't had any problems yet. I don't expect full power to cause an issue, but be careful if you're going to attempt it.
Since completing the build, I've also added a stand, to make this something I can put on my desk. If there's interest, I can add information on this.
Thanks again for checking it out, and I hope this was helpful! If you build one of your own, please share! I'd love to see what everyone else comes up with.
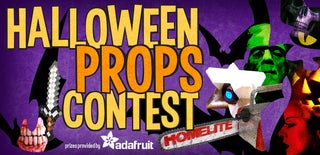
Participated in the
Halloween Props Contest 2015