Introduction: Mars Attacks Martian Saucer Candy Dish
Let me start by saying that, as a fan of sci-fi movies, none is more iconic than the classic, 'Mars Attacks'. There are so many props for die hard enthusiasts to recreate, but none is more beautifully designed than the Martian saucer. Based on the 50's 'B' movie model, it is both simple, and elegant in its form while still appearing ominous with its windowless hull and spider like retractable legs.
This particular project represents several months in planning, creating, altering, then recreating until I was happy with the finished model. In building this ship, my existing rule of form AND function still applied, so my saucer not only had to look the part, but needed to fulfill another function other than being a shelf ornament. Now, calling it a candy dish is a very flexible term. Rather that's what I intend on using it for, however there are a hundred other potential uses including, jewelery box, lidded candle holder, cookie jar, or whatever else your imagination can conjure.
In its original incarnation, it was due to have a shiny coat of metallic gray paint, however, when I saw the final wood grain, I knew that I couldn't hide it under a coat of enamel or stain. Instead, I sanded it to a smooth finish, then sealed it with half a dozen coats of satin Varathane diamond wood finish to bring out the natural color and patterns in the material.
I also designed the saucer to be modular. The legs can be a tricky build, so I created this project in two parts, making the saucer, and base two separate and exclusive pieces. This allows the saucer to be used on its own, as a center piece, or set on its leg base and displayed in a place of honor.
In an earlier incarnation, I had planned on recreating a scene where a saucer is blasting the Washington Monument to try and tip it onto a boyscout troop. Instead of legs, there is a ray gun protruding out of the bottom of the ship with a red laser firing at the base of the statue. The laser would have been created using a steel rod, painted with a metallic red paint which would have suspended the ship in the air, beside a large wooden recreation of the monument. As I said, this project went through many incarnations before I settled on this one.
Get ready for a long ride with this project, as there is a lot going on here and a lot of details to be explained.
Step 1: Tools and Supplies
Tools;
- 12" Wood Lathe (You can do this by hand, but seriously...I don't recommend it)
- Table Saw
- Scroll Saw (Coping saw will work)
- Jig Saw
- Drill Bits 3/8", 21/64", 9/32", 1/4"
- Bench Sander (Optional)
- Router with 3/4" flat bit
Supplies;
- Wood Block 10"x10"x1.75" thick (Can glue two blocks together to attain proper thickness) (Hardwood preferable)
- Wood Block 10"x10"x1" thick (Hardwood preferable)
- Wood Block 5"x5"x1.75" Thick (Hardwood preferable)
- Wood Block 5"x5"x1" Thick (Hardwood preferable)
- Additional Hardwood (Must be 1" thick)
- Wood Glue
- Sand Paper
- Wood sealant, Metallic Gray paint or Wood stain
Step 2: Prepping Your Blocks
To create our saucer, we need to cut our disk shapes to make the transition to the lathe a bit easier. Find the center of your board, mark it, then drive a small finishing nail in. Now, cut a piece of string, tying a look in each end, ensuring that it is exactly half the diameter of your ship (4.5"). Wrap one loop of the string around the nail, and the other around your pencil. Now, as you draw around you will create a perfect circle.
Using your jigsaw, cut out your circle. There's not need to be perfect, as we will be rounding it with greater precision on the lathe, however it's best if your didn't go inside the lines, for obvious reasons.
Once your disks are roughed out, mount your top half on the bowl making faceplate of your lathe, using your center as a guide. Be sure to use short screws positioned at their widest setting on the plate as we will be gouging out the inside of the block to create our bowl.
Now, mount your block on the lathe, then, using our gouge, begin rounding it, ensuring that its final size is exactly 9".
**This process is identical on both the upper and lower half of your saucer.**
Step 3: Creating the Saucer Halves
The Top and Bottom Half Bevel;
Begin by tapering the outside 1.5" of your bowl so that it terminates in a sharp edge. Next, find the center of your spinning bowl. This can be done by removing a thin layer to the center with your scraping tool. From the center, make a mark 2" out toward the edge, then, while the wood is spinning, use the tip of your pencil to highlight that mark all the way around the top center of the saucer half. This marks the demarcation between the beveled surface of the saucer, and its inner "ring", leaving a flat edge in the center. Finish rounding the outer edge of your saucer creating a smooth transition from the demarcation to the outside edge. The bottom half is essentially complete
The Inner Bowl In The Top Saucer Section;
To create the inner bowl, use a diamond parting tool and carve a lip, on the inside of the demarcation, that is 1/4" wide by 1/8" deep. Then, using your gouge or round scraper, begin boring out the remaining core of the wood to a depth of 1.6", ensuring you don't penetrate the bottom of the board. Because the center is spinning tightly, you'll need a finer edged tool to remove it, or you'll need to remove it manually later on.
Finishing;
Finally, once you've carved your two halves, you'll need to do some sanding. Use 80 grit paper to remove the more course tool marks, then graduate to finer and finer grits until you reach 400.
Step 4: The Saucer Lid
Install your 5"x5"x1.75" block on the faceplate, then using your gouge, gradually reduce it to a diameter of 4". Don't worry too much if it leaves a small lip close to the faceplate as your tools won't be able to reach that close. We will be sanding it off when the top is complete.
Begin tapering it using your gouge or round scraper creating a half moon shape. Initially, I didn't create the angle steep enough, however it's not difficult to reinstall the disk and continue cutting to the exact correct shape.
Once the shape is complete, sand, as you did with the saucer halves and set it aside. Be certain to sand of any lip that may have been left behind from the faceplate and test fit before moving to the next step.
Step 5: Assemble Your Saucer
This the last point, before sealing, that you'll need to do if you chose not to create the leg base.
Begin by adding glue to the flat underside of your saucer halves, ensuring 100% coverage, then clamp them together, allowing several hours of dry time. Be certain that the seam is closed up perfectly and that there are no gap, tho smaller seams will be sealed using the wood finish.
Once your pieces are glued, you should sand the seam to ensure a smooth transition between the halves. Now set them aside or proceed to the final sealing process if you want to stop here.
Step 6: Cutting the Leg Pieces
You'll need to prep your material for your leg sections. Set your table saw to cut .175" slices from your 1" board. Depending on your board length, you'll need to cut enough to create 36 different pieces.
Your section is as follows;
12 x ship mounts (2 per leg) - 3/4" tall x1.5" long
12 x top leg sections (2 per leg) - 3/4" tall x 3.25" long
6 x lower leg sections (1 per leg) - 3/4" tall x 2.75" long
6 x claw foot (1 per leg) - 3/8" tall x 1" long
Making Them Identical;
This is where the bench sander comes in handy. Clamp all of your like pieces together (or if your confident you can hold them) and run all of the edges on your bench sander to make all of the pieces uniform and square. This will provide a symmetrical shape so that all of your pieces fit together cleanly.
Step 7: Creating Your Leg Sections
I was going to put this into 4 independent sections, however, them methods and shaping are essentially identical for each, even if their end shape isn't. With that, I'll set them into their own sections in one step with the photos following the described creation. A completed view of all sections will be posted in the last image.
The Mount - Images 1 & 2;
The mount is a perfectly rectangular piece with one beveled edge. A 3/8" hole is drilled into the beveled end, centered, and is exactly 1/4", on edge from the end of the wood.
The Upper Leg Portion - Images 3,4,5,6 &7
A 1/4"x1/4" tab is created by clamping all pieces into a vise, then using a dovetail saw, cutting out the unwanted material (Image 3). The hard corners of the tabs are sanded round (Image 4). There is a slight arc to the overall shape of the piece (Image 5) with the bottom edge slightly concave, and the top slightly convex. This was accomplished by running the entire batch, together on the corner of the bench sander. Finally, a series of 3/8" holes are drilled along the leg piece (Image 6) by clamping them together and using a press to drill through them all at the same time. The Final portion can be seen in Image 7.
The Lower Leg Portion - Images 8,9 & 10
The lower leg section is created by tapering one top edge down, then forming a concave angle on the underside of the piece using the bench sander. The tapered end is rounded, as are each corner of the wider end (Image 8). A series of evenly spaced holes are drilled along its length, in the same way they were done for the upper portion, using the 21/64, 9/32, and 1/4 bits respectively (Image 10). Using a dremel with a rotary bit, or a coping saw, cut a notch in the tapered end (Image 9). This will accommodate the claw foot which your will see in the next section.
The Claw Foot - Image 11
The claw foot is created in the same way that the lower leg portion was, except the tapered end is shaped into a point. The rear edge of the foot is tapered to fit in the groove created in the lower leg portion.
Dowel Pivots
The legs are mounted to the leg mounts via 3/8" dowel posts. Each post is cut to 3/4" in length with their edges slightly sanded bevel.
Finishing
When all pieces are complete, sand them all down using progressively finer grits. A quick way of doing this is to clamp an orbital sander, inverted, into a vise and run each piece over it. Be certain to sand each drilled hole removing all burrs.
Step 8: The Leg Dome
For lack of a better name, I'll call this the leg dome. On a standard model, this would be a flat, molded piece of plastic, however, since I wanted this project to be all wood, I decided to create it out of a solid wooden block which, as it turns out, is immensely more difficult.
I had a few failures, in creating this piece, that I thought would be valuable to others, as can be seen in image 1. Initially, I created the dome on the lathe, then attempted to run it through a jig I created on my table mounted router. After that failed, I decided to set the dome into a bench jig, and run the router over it by hand. Both were absolute failures due to the hardness of the wood, the depth of the cut, and the width of the bit.
Finally, I decided to leave the block square, mount it in a jig and run the router over it. This worked well enough, however the big test was in remounting it on my lathe and turning it with the holes cut. This seemed to work very well which ended up being my final piece. Notice that the bevel is much smaller than the saucer pieces. That's to leave enough material to support each strut.
The legs are set 1.5" apart (on center), coming out of each side, with a 2.5" gap for the front and the back.
**Note** It's important to set your block on your lathe faceplate and mark the mounting holes prior to routing as, if it's even a bit off when the holes are cut, you could end up with crooked legs.
Step 9: The Stand
The reason for the stand is simple. Due to the weight of the saucer and the fragility of the wooden legs, I wanted some extra support for the ship. With the legs set permanently, it would have stood up fine on its own, however, over time the legs would have started bowing and warping, ruining my work. The stand is especially useful if you intend on making your legs articulating (described in next step).
The stand is a simple creation consisting of a 3" wide x1" thick base, with a 2" long x1" wide spindle, mounted directly to the leg dome, both turned on the lathe. There is a 1/2" hole drilled in the center of the base and another in the center of the leg dome. On each end of the spindle, a 1/2" socket is cut into it and the whole thing is glued and set into place.
Step 10: Leg Assembly
To Articulate, Or Not To Articulate;
Each joint, in the legs, is designed to articulate and fold up, much like they do in the movies. In my model, I wanted them static, however, if you prefer to be able to move them, it can be done without much alteration. Holes are drilled in the tabs of the top leg portion, the bottom edge back of the lower leg portion, the center of groove end of the lower leg portion, and the center bevel of the claw portion. Then, using metal rod (paper clips work well) insert them into the holes to create the pivot points. The pivot point, at the leg mount is handled by the 3/8" dowel that was cut in the last step.
Setting The Leg Mounts;
Using the dowel pieces to line them up, glue each leg mount piece into its appropriate slot. They should adhere cleanly to the walls of each routed channel and should meet at right angles, to each other, inside the channel. To keep the pieces properly spaced, use a piece of balled up paper or towel to keep them pressed against the sides, then invert the entire thing on a table to ensure they are all level.
Attaching the Remaining Pieces;
It's a good idea to do a test fitting of all your pieces to ensure the angle you want your legs to sit. Once you have the right position, you can begin gluing them into place.
The claw attaches to the lower leg piece by fitting its beveled end into the groove that was created. All 6 pieces can be fabricated at the same time by stacking them.
Attaching the lower to the upper portion will require some shims to ensure the fit is even and straight. Lay one upper strut with the tab down flat on a surface, and apply glue to the tab. Then set the lower strut with its bottom edge overlapping the tab and a shim underneath it to raise it to the height of the upper piece. Place a shim on top of the upper piece. Next, take a second upper piece and, applying glue to its tab underside, lay it on top. You can use the 3/8" dowel to ensure it is centered properly. Apply weight to the glue joints to ensure they fit snuggly.
Finally, when all pieces are dry, attach the legs to the leg mounts using the dowel pieces, but don't glue them yet. You'll want to do a test fit to ensure everything lines up perfectly.
Step 11: Sealing and Finishing Your Work
As mentioned before, how you finish your saucer is up to you. If you prefer to keep it, somewhat, authentic, you can paint using silver metallic paint then highlight some detail work with other colors as required. Staining the wood is also an option as this project uses several different wood types that all react differently to color.
If, however, you prefer to keep it "au naturel", then I recommend using a satin finish that will enhance the grain, but not overdo it.
The process is simple;
1 - Lay out all of your pieces on a sheet of paper using leftover strips of wood to prevent them from sticking. Wipe down everything with a damp cloth. Apply a light coat of Varathane and allow to dry for several hours.
2 - Once the initial coat has dried, you'll need to do a light sanding with 400 grit paper. Courser if the sealant has raised the grain dramatically. Just don't sand too deeply as to completely remove the layer you applied.
3 - Wipe off the pieces with a damp cloth, then apply a second layer of Varathane, allowing it to dry. Feel your pieces to see of the grain has raised more. If it has, repeat the first step. If it has remained smooth, apply another coat.
Optimally, I like to do 5 coats, but three should be sufficient.
Finishing Touch;
To hide all of the channels in the leg dome, and to cushion the saucer I cut a 4" piece of leather and glued it to the top using 5 minute epoxy. If you don't have leather, felt, or even hobby foam will work fine.
Final Assembly;
Now you can fully assemble your legs. You can glue the 3/8" dowel into place, making your legs static, or you can leave them loose, allowing the legs to articulate. Your choice.
Step 12: Finished
That's it. What you've created is a center piece for your table, and a new prop to feed your nerd hunger for all things Martian. More than that, you've created a cache for anything you decide to fill it with.
As usual, I hope you enjoyed the instructable, and thanks for following.
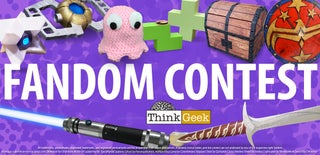
Participated in the
Fandom Contest