Introduction: Mechanical Arm Test Fixture
I was wanting to test software for an upcoming project and required a mechanical arm to do so.I chose basic forms since the goal was to test function. Future revisions have better aesthetics.
This was designed and built on the fly with little more than an idea of the finished arm.
There were mistakes made in both thinking and implementation but the arm did its job in the end. Corrections are included in the files for printing where necessary
This is just the mechanical parts. Electronics and operation will not be discussed here.
This is printed from ABS files and build instructions are all included.
Any changes recommended with be noted.
Parts 2 and 3 will cover the electronics and work holder.
Step 1: Printed Materials
Using the provided files it is possible to print the components needed for this build.
I use break away supports so some concessions were made with the files to optimize printing.
For example some of the vertical print holes were changed to diamond shape to prevent being clogged with support material.
Some parts were also split for faster printing.
Some parts have been embossed with my website for design protection.
Attachments
Step 2: Arm Stand
The base shown is the first generation, it is designed to hide the rotation mechanics.
Files here are BearingMotorBase1, BearingMotorBase2, and SwivelMotorBase
There are two bearing elements. this first is a standard 6203 bearing (super overkill here but I had several on hand) the and second is a large printed race with captive 3/8 balls.
The first mistake here is that the lower large bearing race can be integrated into the base and printed as 1 item instead of 2.
I used heat set inserts for plastic. These were installed using the heat from a soldering iron. The tip is both used to heat the insert and press it into the plastic when it gets hot enough.
Sizes of the inserts here 6-32 for the green base and 4-40 for the lower bearing race. These are installed as shown into the base and the motor support.
The 6203 bearing is pressed into the base bearing support. Here was mistake number 2... In re-designing this part I made the bearing cutout 2mm too shallow this has been corrected for the print file.
2 of the motor securing screws are installed the the lower race is fastened to the motor support.
All fasteners are installed to make this a single assembly.
Later I had to remove the motor to attach the belt drive gear to the motor then reinstall it to the base.
Step 3: Base Bearing
Files here are BaseBearingRaceFull and UpperBearingMotorBase
I used 3/8 steel ball bearings and the ball carrier was designed for these. The balls are held in place by the shape of the holes on the carrier. They protrude about 1.25 mm from either side.
This carrier is loose enough to press the balls in with minor force.
The carrier sits on top of the lower race and the upper race sits on top of this.
Step 4: Split Shoulder
This part was bisected to allow for quicker printing and less material waste.
Files here are LowerArm1 and LowerArm2, the small bearing race is ShoulderBodyPivot, the drive gear is Lower60GearToothWide
The inner drive securing points were wrong on the models and the prints had to be prepared by hand the files have been corrected.
The race mounting holes have 4-40 heat set inserts installed. this is both on the base and for the shoulder race.
Both races are then attached using 4-40 screws.
The lower drive gear was aligned using the wrong holes then marked, drilled and heat set inserts installed. There is a provision for a 1/4-20 bolt which is needed to secure the base together. a washer and lock nut are needed here.
The motor mount is for a NEMA24 stepper and the screw holes had 10-32 heat set inserts installed.
From here the shoulder 6203 bearing was installed.
Before assembly a drive belt is needed this is a GT2 - pitch 162, 6mm wide. This is placed and the lower bearing assembly is secured.
Step 5: Shoulder Bearing and Drive
The only reason that the green to blue colour change here is that I was using up my old materials.
Parts needed here are ShoulderPivot, BicepRace, ShoulderGear60, BicepThin1, BicepThin2,
As before the holes need to have inserts installed, again I used 4-40.
This race was printed with sparse interior while the pivot was printed solid.
There is provision for a 1/4-20 bolt which is used to attach the rotating joint together.
The 3/8 inch bearing balls are pressed into the BicepRace part. There are 3 of these needed.
The Shoulder Pivot is fastened to the BicepThin1 part on the end with no center hole.
The shoulder pivot is assembled as shown then inside the lower arm section is secured by pressing the ShoulderGear60 part onto the hex shaft of the Shoulder pivot. You may need a thin washer between the gear and bearing.
This is held in place and friction adjusted with a fender washer and lock nut.
Step 6: Upper Arm and Elbow Pivot
I wanted to keep the arm light so the motor was mounted away from the joint. I used a fixed position printer tooth pulley to change the rotation axis.
Parts here are ElbowPivot(2),
The printer pieces have inserts mounted then they are assembled as shown. The motor is Nema17 with a 20T GT2 pulley.2 of the connecting screws are under the bearing race.
The two halves of the upper arm assembly have to be connected before the outer bearing race is attached.
The bearing surfaces were attached to the appropriate places.
Step 7: Forearm
The parts here are ElbowForearmPivot, Forearm, ForearmCover, forearmTube, ForearmWristSupportRace, ForearmSkateBearing, ForearmWristSupport1, WristDrive, ForearmGear44Skate, ForearmWristLink, ForearmDrive40
Prepare the Forearm part with heat set inserts; the bearing race holes require 4-20 heat set inserts and the opening requires the 2-50 inserts, the rear requires 3 holes to secure the ForearmSkateBearing part.
Insert a 2.5 inch 4-20 bolt into the ElbowForearmPivot and secure it to the Forearm part.
Begin by pressing a standard 6203 bearing into the forearmWristSupportRace.
From here the the forearmTube is pressed onto the race flared side to the race.
The forearm part is then pressed onto the tube.
These parts are all interference fit and will lock together.
the ForearmWristSupport1 requires 10-32 inserts put in from the shaft side and the ForearmCear44Skate requires 4-40 inserts and one M6 insert
The WristDrive is pressed into ForearmWristSupport1 and secured with adhesive it is then inserted through the 6302 bearing.
Attach the ForearmWristLink with adhesive.
Place the belt and ForearmGear44Skate and secure with a 8mm shoulder bolt
Secure the ForearmWristLink to the ForearmGear44Skate with 4-40 screws.
The drive motor and ForearmDrive40 are put in place
Change here. I had to add a part to the shoulder bolt for spacing this is called SkateCover
Step 8: Final Assembly
The forearm is attached to the upper arm using two of the previously assembled bearing races. one inboard and one outboard.
In the center is the drive pulley named BicepGear60 and a drive belt as shown
The outer race is placed and the joint is secured with a 4/20 washer and locknut
The shoulder drive motor and belt are attached as shown. The correct belt was out of stock so a 3mm was substituted but will be changed
The base drive pulley and belt were installed as shown and secured with a 14-20 washer and lock nut.
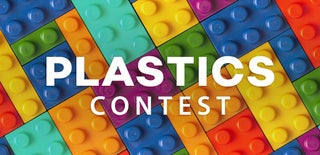
Second Prize in the
Plastics Contest