Introduction: Modern Walnut Bed & Headboard | DIY
This bed is made from solid walnut, walnut plywood, and steel. I don’t have much experience working with metal so it was fun working with something new. If you don't have access to these types of materials, or you're not a fan of walnut, you can substitute to wood for anything else that close in size. Comment below with your questions and I'll be more than happy to answer them.
This project consists of three main parts. The footboard box, bed frame, and headboard. We'll go through it in that order.
**The dimensions included in this article are for a queen size mattress. Check your mattress size before cutting materials**
Tools I used in this project:
Sawstop table saw - https://amzn.to/2ILhw5L
Drill press - https://amzn.to/2VFVSaF
Miter saw - https://amzn.to/2RHklNs
Router - https://amzn.to/2ILhw5L
Router edge guide - https://amzn.to/2CdaV2y
Marking gauge - https://amzn.to/2RMOfjC
Dowel centers - https://amzn.to/2VCtQN0
Dead blow mallet - https://amzn.to/2M3hwkA
Jointer - https://amzn.to/2ILhw5L
Chisels - https://amzn.to/2ILhw5L
Japanese handsaw - https://amzn.to/2ILhw5L
Drill & driver set - https://amzn.to/2ILhw5L
Brad nailer - https://amzn.to/2Cf2svP
Spring clamps - https://amzn.to/2ILhw5L
Step 1: Footboard Box - Top and Bottom
The first part I’m tackling in this project is the box that acts as the footboard. The four sides are solid walnut and the back panel is walnut plywood. I prefer to work with solid wood as often as I can but I used plywood for the back so I don’t have to worry about designing and building around wood expansion and contraction.
We'll start with ripping the top and bottom boards to width. Next tape them together and crosscut one end to make them square. Then flip them around and cut the other side. I like to crosscut on my table saw with a slide but a miter saw will work just as well.
Taping them together makes sure they are exactly the same length.
The top board is 10" wide and the bottom is 7 3/4" wide. Both of these are 66" long and 7/8" thick.
Tools in this step
Sawstop table saw - https://amzn.to/2ILhw5L
Spring clamps - https://amzn.to/2ILhw5L
Step 2: Footboard Box - Short Sides
The next pieces to cut are the short sides of the box. They are 9 1/2" long. If you have enough material, use the off cut from the top and bottom boards so the grain and color match perfectly.
Next draw and cut an angle on these pieces so they flow seamlessly from the wider top board to the narrower bottom board. Measure in 7 3/4" (width of the bottom board) on the bottom of the side pieces and connect that point to the opposite top corner.
Tape these pieces together before you cut them to make sure these are exactly the same. A tapering jig would work great here but I don’t have one so I lined this line with the kerf cut in my crosscut sled and held it securely while making the cut. I don't recommend doing this if you aren't comfortable with it.
Tools in this step
Sawstop table saw - https://amzn.to/2ILhw5L
Step 3: Footboard Box - Short Sides Joinery
The box is being put together with dowel joinery so I mark a centerline on the boards using a marking gauge and drill holes for dowels. The dowels are 3/8" and are spaced about 2" apart.
I came up with a far too complicated way to hold these boards to my drill press table. I used a wooden clamp to keep them from spinning and a clamped a square to the table to make sure I’m drilling these holes perfectly square. After drilling all the holes I remembered the table tilts all the way to 90 degrees. That would’ve made it easier. If you don't have a drill press you can use a dowel guide or drill as straight as you can by hand.
To transfer these hole locations to the top and bottom boards, I’m using dowel centers. This is the first time I’ve used them and I highly recommend including these in your workflow. Use a straight edge to to line up the side and back of the board and then press them together to leave indents. Drill in these spots with a 3/8" drill bit and add a tape flag so you know when to stop drilling. I drilled about 5/8" deep in the top and bottom pieces and 1" deep in the sides.
Tools used in this step
Drill press - https://amzn.to/2VFVSaF
Marking gauge - https://amzn.to/2VFVSaF
Dowel centers - https://amzn.to/2VFVSaF
Drill & driver set - https://amzn.to/2VFVSaF
Step 4: Footboard Box - Rough Assembly
Next cut 3/8" dowels to length. The total hole depth is 1 5/8" but I recommend cutting the dowels to 1 1/2" to make sure they don't get in the way.
After rough assembling the side (no glue yet) and making sure all the holes are in the right spots, you can mark the holes for the top board using the dowel centers and how they were explained in the previous step.
Tools used in this step
Sawstop table saw - https://amzn.to/2ILhw5L
Dowel centers - https://amzn.to/2VFVSaF
Dead blow mallet - https://amzn.to/2VFVSaF
Step 5: Footboard Box - Back Panel
Next we need to cut a stopped rabbet on the top and bottom boards to accept the back panel. I clamped a straight edge to the board for my router to ride up against and cut the rabbet in two passes. The corners can be squared with a chisel.
Lining up the straight edge took quite a bit longer than I anticipated so after cutting these grooves I bought an edge guide for my router.
The back panel is an off cut from the headboard, which we’ll get back to later. I cut this panel to size slowly sneaking up on the fit to get it nice and snug.
Tools used in this step
Sawstop table saw - https://amzn.to/2ILhw5L
Router - https://amzn.to/2VFVSaF
Router edge guide - https://amzn.to/2VFVSaF
Chisels - https://amzn.to/2VFVSaF
Step 6: Footboard Box - Assembly Tip
This step isn't nessecary but makes the glue up easier. While the box is rough assembled, clamp it together and predrill and drive screws through the bottom board into the back panel. These screws won't be seen since they'll be under the box and putting the screws will help you line up and attach this piece during the glue up.
Tools used in this step
Drill & driver set - https://amzn.to/2VFVSaF
Step 7: Footboard Box - Glue Up
After that, pull it all apart and sand the inside faces since they’re easier to get to now.
With that done, we can start putting it all together. Start by glueing the bottom panel to the back panel and hold them together with the screws.
Next glue on the side panels with the dowels. Make sure to add plenty of glue in the dowel holes since this is the only long grain to long grain connection and it’s what’s holding everything together.
After adding the top we can start clamping it all together. Be sure to add clamps in every direction you can. The more, the better!
Tools used in this step
Dead blow mallet - https://amzn.to/2VFVSaF
Drill & driver set - https://amzn.to/2VFVSaF
Step 8: Bed Frame - Wood Stretchers
There are 4 stretchers in total. The two outer ones are 81" x 6" x 2 1/2". The two inner stretchers are 81" x 2 1/2" x 3" and these two pieces in my case came from a board that was the same size as the outer stretcher. I ripped it in half and turned each piece 90 degrees. Turning them allows you maximize on thickness and adds strength.
The outer stretchers receive a rabbet to later except the bed slats. The rabbet is 2 1/2" wide and 7/8" deep.
Next I use a miter saw to square up one end of these boards and cut them to length. The saw wasn’t able to cut this full thickness so I had to finish the final ½” with a hand saw. The center stretchers are narrower so the saw was able to fully cut them.
Tools used in this step
Sawstop table saw - https://amzn.to/2ILhw5L
Japanese handsaw - https://amzn.to/2VFVSaF
Miter saw - https://amzn.to/2RHklNs
Step 9: Bed Frame - Inner Wood Stretchers
Next we need to remove material from the middle stretchers to accommodate for the slats later. You can skip this part by by simply attaching them lower to the steel bar in the next step.
I cut this by doing a stopped cut on the table saw. Alternatively it can be cut with a bandsaw or jig saw.
Since these pieces are 3" and the outer stretchers are 2 1/2" thick, we need to remove some material from the bottom so all the legs can sit flat. I do this a router.
These legs are made by Chris from Make Everything. He also has an instructables page and you can watch him make the legs here.
Tools used in this step
Sawstop table saw - https://amzn.to/2ILhw5L
Router - https://amzn.to/2VFVSaF
Japanese handsaw - https://amzn.to/2VFVSaF
Drill & driver set - https://amzn.to/2VFVSaF
Step 10: Bed Frame - Steel
To tie the wood stretchers together we're using steel. There are two steel bars. One on the foot side of the bed and one on the head. I highly recommend using a good cutting/drilling fluid when drilling these holes. I ending up going through a couple drill bits.
I ending up going over board with the amount of holes. I recommend drilling 3-4 holes per middle stretcher and 4-5 holes per outer stretcher. After countersinking these holes, we can transfer the holes to the wood and screw all the parts together. Adding paste wax to the screws help them go in easier.
This is a good time to also pre-drill and screw in the footboard box.
The steel is 2 1/2" x 66" x 1/2" and I drilled 5/16" holes and 3" long #14 screws.
Tools used in this step
Drill press - https://amzn.to/2VFVSaF
Drill & driver set - https://amzn.to/2VFVSaF
Step 11: Headboard - Panels
Moving on to the headboard I ripped two sheets of plywood into 12” panels. This made them much easier to move to their final destination since they needed to fit in an elevator. The bottom three panels where keep as one unit to add some stability since that’s where the head of the bed would be supported. This was tight fit in the elevator but luckily it worked.
Next I route a groove on the end of each panel and that’s how they’ll be screwed into the wall. Add blue tape to reduce the risk of tear out on the thin walnut veneer.
This rabbet is 3/4" wide and 3/8" deep.
Tools used in this step
Sawstop table saw - https://amzn.to/2ILhw5L
Router - https://amzn.to/2VFVSaF
Router edge guide - https://amzn.to/2VFVSaF
Step 12: Headboard - Caps
The last pieces needed are the caps that run vertically on the ends of the headboard. I cut a rabbet in them and that’s how the screws in the plywood panel will get covered.
After cutting them to length, in this case 90", I can start the install.
These rabbets are slightly larger 3/4" x 3/8". This extra play allows for any misalignments when putting up the headboard.
These are all parts needed the bed. Now we can sand all the way up to 220 grit or higher and apply finish. I applied 3 coats of wipe on poly.
Tools used in this step
Sawstop table saw - https://amzn.to/2ILhw5L
Miter saw - https://amzn.to/2RHklNs
Step 13: Install - Headboard
The first thing to install is the headboard. We added strips to wall to add a gap between the headboard and wall. We used a stud finder to screw these strips into studs. Adding these strips compensates for any unevenness in the wall and also adds a space where we can add wires and lights in the future.
We arrange the headboard panels on the floor first to get a nice pattern. Then we can screw them on the end strips and use a brad nailer to secure then to the middle strips. These end strips are 5" thick and half of it is behind the headboard panels and the other half sticks out and thats where the headboard caps are secured to. These are tacked in place with a brad nailer.
Tools used in this step
Japanese handsaw - https://amzn.to/2VFVSaF
Drill & driver set - https://amzn.to/2VFVSaF
Brad nailer - https://amzn.to/2VFVSaF
Step 14: Install - Bed Frame
The rest of the bed is then put together just like in the previous steps. The steel bar on the head of the bed is screwed into the headboard. For added stability, make sure the bottom headboard panel is resting on the floor.
There are a total of four legs. Two get screwed in on the center stretcher where we cut the pockets. The other two are attached to the foot end on the outer stretchers. Half of the foot is under the stretcher and the other half is under the box. This is also a good time to screw in the bed frame to the box.
The slats here are simply firing strips (1" x 4"s) cut to length and screwed in place. After adding the mattress, it's all done!
Tools used in this step
Japanese handsaw - https://amzn.to/2VFVSaF
Drill & driver set - https://amzn.to/2VFVSaF
Brad nailer - https://amzn.to/2VFVSaF
Step 15: Get a Good Night's Sleep and Enjoy the Bed!
That's it! You're all done!! Let me know if you build this bed by posting your photos below and feel free to ask questions.
You can watch the video here on how I built this bed.
You can also find me on Youtube
Instagram to see what I'm currently working on
Facebook and Twitter for behind the scenes shots
Note: This post includes affiliate links. Thank you for your support!
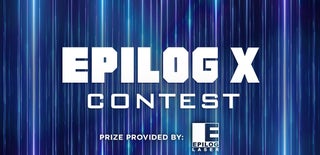
Participated in the
Epilog X Contest