Introduction: Mother's Day Art
For this project I used the following tools, technology, and materials:
Software:
Smart Carve 4.3 laser cutting software
Fusion 360
Corel Draw
Tools:
Drum Sander
Jointer
Vertical bandsaw
Oscillating spindle sander
CamFive CMA 1080 CO2 Laser
Betsy wood clamps
Materials:
Walnut
Maple
Mahagony
Titebond 3 wood glue
Sand paper
Danish oil (Watco)
Step 1: Obtain Species of Wood
First step is to obtain the materials you are going to use to assemble your project. I decided to use some off cuts of Walnut, Mahogany, and Maple solids that I had laying around the shop from previous projects. What materials you have at your disposal will determine how large your project can be.
Step 2: Design
After browsing around online, I found a .JPG of a heart I liked, but it wasn't really refined for a project like this. I took the .JPG into Corel Draw and did a bitmap trace on it to give me vectors that I can work with on my laser. Because my strong point is not in Corel Draw, I saved the artwork as a .DXF and uploaded it in Autodesk's Fusion 360. Here I was able to correct a lot of the vectors, clean them up, add fillets, and make it cutting ready.
Step 3: Re-Sawing Lumber
Re-Sawing lumber is very dangerous. To help with the process, I modified my band saw's fence and machined a re-sawing bar out of 6061 T-6 aluminum I had laying around. After turning it on the lathe to the diameter I want, adding a radius on one end and a chamfer on another, I used our mill to machine a flat on it, then drilled and tapped it. It fit perfectly, and worked amazing as it allows the material to be able to pivot off the radius while keeping pressure on your material to ensure somewhat of a straight cut.
Before I re-sawed the lumber, I ran it through the drum sander to ensure the sides were somewhat flat and parallel. I re-sawed all species of lumber I had. Most was approximately an 1" thick, so it yielded about .450".
Step 4: Gluing Up the Walnut
After the pieces were re-sawed, the long grain needed to be nice and straight to create an edge to glue and join the two pieces together. I used a jointer to give both pieces a straight, perpendicular edge to work on. I applied the Titebond 3 Ultimate to the long grain (length) of the boards, and clamped them together using the Betsy Parallel beam clamps and some sacrificial glue up boards I cut out on my laser previously.
After about 3 hours, the .450 x 16 x 16" piece of walnut was ready to be worked with.
Step 5: Cutting It Out on the Laser
I've found that Fusion 360 does not always complete vectors when exporting as a DXF. I use Corel Draw's Join Curves feature to help correct these incomplete paths before loading the file into Smart Carve (laser CAM software).
My CO2 laser is 100W, and I have two different focal length pens for it. I used the shorter focal length pen to etch the wood (laser parameter: 10% at 20IPS), and I used the longer focal length pen to cut the wood out since it was over 1/4" (laser parameter: 100% at .35IPS)
The cuts were really good considering lasers like to cut a small bevel. Some of the parts were cleaned up using our oscillating spindle sander to ensure that they were going to glue up properly.
Step 6: Gluing Up the Pieces
I placed a piece of craft paper down on the cast iron of the table saw, and used it as a flat surface to glue up all the species of hearts. I wanted the etched side to sit perfectly flat with the walnut perimeter since the etching wasn't super deep. I applied liberal amounts of Titebond 3 wood glue to the perimeter of the components, and tapped them in using a broad faced rubber mallet until all components sat flush with the outside.
Step 7: Sanding the Backside
I double sided tape to temporarily fasten the project to some scrap plywood I had lying around the shop to act as a rudimentary sled so the backside could be sanded through the drum sander. I sanded the backside till all components were flush with the walnut.
Step 8: Raising the Grain
On finished projects like this, I like to use reverse osmosis water (RO) to raise the grain of the wood before the final sand. I use a hand spray bottle to lightly mist the wood, and let is soak in. I then hand block sand the wood using 400 grit paper with the grain to avoid scratches.
Step 9: Finish
Final project was treated with Natural color Danish oil (Watco) as directed on the container.
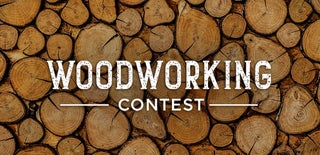
Participated in the
Woodworking Contest