Introduction: NYLON Windmill Flange to Reduce Bird Mortality
This is the mounting flange for a standard 2.5 meter 8 blade electrical
generation windmill. This is similar to several commercial windmill flanges.
The flange is printed in NYLON so as to provide a shore 45 single piece flexible connection to the main drive shaft from eight fiberglass blades.
The parts were printed in NYLON on a 2BEIGH3 3D Printer.
Details of the printer can be seen at:
https://www.instructables.com/id/Combination-CNC-Machine-and-3D-Printer/
The .stl file for printing is at:
http://www.thingiverse.com/thing:23961
The part is designed to be printed in NYLON or NYLON6 as this material provides the flexability and streangth needed for this type of blade connection flange.
Usage:
The user requested a single unit to replace multi-part flanges on 29 existing installations located over a 2200 acre hillside farm and
residence. Each unit connects to a self regulating alternator/inverter/battery system built by the owner from a kit provided by an ecological web site.
All units are controlled and monitored via WiFi to help the owner oversee the property as he could not afford any help.
Usage includes spot irrigation, animal surveillance, pump and other reservoir levels.
Due to the type of crops, there has been an increase in mortality of birds in the past few years. There was a request to modify all of the blade flanges in such a way as to provide a considerable “give” or “deflection” of the blades, yet keep generation efficiency at its current level. The “shore” value was provided by a local university intern.
Previous designs used spring-loaded hinges. After a short time, these would break and the mill would become unbalanced, and therefore unusable.
It was pointed out that while NYLON would provide the needed blade flexability or “shore”, it was susceptible to water absorption from the elements. This would mean that the flanges would probably need to be replaced every 20-24 months depending on usage. The end user believes it’s less costly to simply "3D print" flanges and change them out when the mills are brought out from winter storage as opposed to a more expensive alternative.
If you print this part on a 2BEIGH3 3D Printer, then you can experiment with the fill to get different "shore" or flexability of the flange.
The author is currently working with other plastics that are not suceptable to the elements, yet provide the desired flexability.
As adjustments or changes are made to the 2BEIGH3 3D Printer to handle these new materials, the author will try to update this and the main instructable.
As crop rotation takes place next year, effectively of the flange could take 4-5 years and even then, will be more of an estimate than a hard number.
The only surprise in actual usage came from the fact that the NYLON replacement flange was so light, the mill’s alignment vane required some minor re-balancing.
A 12 unit field test will take place in late June.
The Flange:
Each blade is aligned via two alignment pins, and held in place by an oval clamp.
This part is the REV “A” design, but the fill has been changed to decrease the “shore” value after initial testing.
The part is low res and designed to be printed in NYLON or NYLON 6 on a 2BEIGH3 3D Printer with a .56 - .62 mm nozzle.
Even as the part is large, there is no corner lifting at 80% fill.
A heated table is not used. As in the photo, the part is printed on plain masking tape.
Material color on-hand is a "caution" orange – Field test parts will be printed in a dark tan.
The part was designed in Rhino, skinned in Slic3r v6 with no retraction and printed on a 2BEIGH3.
Retail material cost = $0.26
It is hoped that with both a combination of the ability to print with NYLON and other new materials, along with the extremely low cost of these materials, the "3D Printed part replacment" door has opened a bit wider!
As the number of common and unique parts and assemblies are printed on the 2BEIGH3 grows, the author will share a mojority of these designs here and on the http://www.thingiverse.com web site. simply do a search on "2BEIGH3".
Attachments
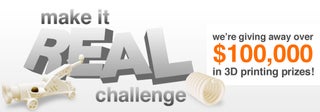
Participated in the
Make It Real Challenge