Introduction: Oregon Pine Bench, From Roof-beams.
This is an instructable showing a wooden bench I made for my dining room, from reclaimed Oregon Pine beams. I tried to make it using predominantly hand-tools, however some sanding, drilling, and routering was done with powertools.
I did my plan and calculations using CorelDraw, which allowed for material use calculation, angle and intersection of the legs, and the placement of the dowel pins
Materials:
The materials used were as follows: one Pine Beam, 210mm by 70mm, by approx 6 meters.
One smaller beam, about 120mm by 70mm, also about 6 meters.
Fasteners:
One meter length of M8 threaded rod
M8 washers
4x 90mm by 8mm Coach bolts
16mm x 80mm dowel pins,
Wood glue.
Tools: General wood-working tools, explained throughout the instructable.
Step 1: Prepare the Wood, TLC
The wood was in a sorry state, caked with paint, filler, and nails. This all needed to be removed to allow for rough planing.
Planing was done by hand with several Stanley planes.
Some of the pieces were extremely splintered, and wouldn't have been suitable for use. These were repaired and glued, and then planed once dried.
Step 2: Joining the Beams for the Seat: Doweling
Once the two beams were nice and plumb, square and even, they needed to be joined.
I wanted to use doweling as I dont have a biscuit joiner, nor a Domino. I figured that all I needed was a guide block to help me get the holes normal to the surface.
I cut a length of dowel (about 16mm diameter) down to pins 80mm in length. These were to assist with alignment and strength.
I cut a piece of pine pallet wood which was about 70mm by 70mm, to a 250mm length. I carefully marked the edges and cut out a notch for aligning to marks on the wood. This jig was then clamped to the joining edge and a hole drilled from above with an Auger and bit slightly larger than the dowel pins. I carefully made sure that I use the same reference edge/side for each of the mating surfaces.
When all the holes were suitable and aligned , i coated each pin with glue, coated both mating faces of the boards, and clamped till dry.
Step 3: The Bench Legs & Cross Strut
The legs and cross strut all came from a single beam (as illustrated in step 1).
I used CorelDraw to calculate the lengths, angles, intersection according to what the optimum seating height should be. I made the seating hight the same as a dining chair, so that everyone is on the same level.
I marked all of the cut lines on the leg, using pencil and a ruler, referring to printed plans from Corel. This helped with getting the assembly relatively snug. I used a japanese saw, chisel& mallet to remove the bulk of the material out of the half-lap joints where the legs cross.
The profile of the cross strut was marked with pencil & a plastic template, allowing for a recessed face to be routered out. This was done by hand, but I know a router template would have been better.
Finally I used an auger to drill holes in the centre of crosses, where the legs would get bolted to the cross strut.
Step 4: Oiling.
Sanding and oiling was undertaken on the legs & cross strut first, followed by the top surface. Sanding was undertaken with 80 grit, to 200 grit on an orbital sander. Any harsh edges were sanded with a belt sander as it is more aggressive in removing the material, followed by 80 to 200 grit.
The oil I used was a Danish Oil, which soaked deep into the wood. This will need a fre more sanding + oiling sessions until it reaches its optimum, however what you see here is the freshly oiled wood. AsA
Step 5: Attaching the Base to the Seat.
I placed the base onto the seat, upside down to alighn where the legs will locate. I measured in from the edges to make sure it was perfect (perfect enough). One the legs were marked with tape, I calculated where I wanted the coach bolts to enter the legs.
My plan was to drill a small hole from the bottom, through the entire plank, then countersink from the top surface down slighlty. This didnt go to plan as the Auger cant alight nicely in the existing hole. I had a plan with the router, and router template. The hole in the router template was drilled with a hole-saw and made a suitably sized hole. This worked out well and the holes were clean and crisp.
Once the holes looked good, and the bolt was able to sit sufficiently beneath the surface of the wood as well as extend sufficiently below the surface, the holes in the legs were marked. These were pre-drilled with a 5mm drillbit, to allow the bolt to bite into the wood, but not split the legs.
Step 6: Final Assembly.
Once all the pieces have been oiled, and all the fasteners are ready, assembly was undertaken.
It will need a bit more light sanding and additional coats of danish oil, but I'm happy with the outcome.
I think I will shape plugs of wood an tap them into all of the recessed holes. I will do this without glue, as I like the idea of having the bench being able to dismantle, possibly for a monster-long bench in the future, if I find some more suitable beams and a larger house.
I hope you liked my instructable, please feel free to tell me how you would have done it differently.
Cheers.
Step 7:
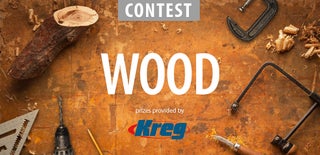
Participated in the
Wood Contest 2016