Introduction: Paper Aeroplane Wind Tunnel
For a while Mark (my maker faire partner in crime and co-projecter on jellyandmarshmallows.co.uk) and I had been wanting to do something with paper aeroplanes, so when looking for a more interactive Maker Faire project we decided to go big and make a wind tunnel with a working section fit for A4 aerodynamics.
With most of our projects we try to make our builds accessible and inexpensive so in this case we have built our wind tunnel mostly from cardboard and scrap. This does not, of course, prevent it from being a fully functioning wind tunnel... that happens to be very similar to a NASA design (but more on that later!)
Purpose
Generally we want to encourage kids to be more interested in science and engineering and this seemed like a good way to do that.
Why paper aeroplanes? Well, first of all we are both engineers so have been making paper planes for as long as we can remember, but there’s more than that; paper planes are an evocative symbol of frivolity that strikes a chord with many. You take a piece of paper that could oh so easily become the base for recording meeting minutes or some other such boring dreariness, and instead you turn it into something aspirational, something that can defy gravity and achieve flight, not to mention catch the back of an unsuspecting colleague’s head by surprise.
You can wow the masses with the pin straight stable flight you can achieve or with your best triple loop-the-loops.
Ok… they might not admit to being impressed but, you know, they’re just jealous of your aerodynamic stationery skills.
3 things above all others make paper planes brilliant:
They are accessible, paper is cheaply available to any budding aeronauticist of any age.They are custom and individual with infinite scope for creativity of design both by folds and by felt-tips.The simplest are so easy to make a six year old can do it, thereby starting a life time of creating minor irritation by letter-headed aerial bombardment.
Ahem, so back onto the wind tunnel…
Step 1: Intro to Wind Tunnels
If you aren’t familiar with wind tunnels, I suggest a quick wiki on the topic.
Wind tunnels are a useful tool for development of high speed cars and aircraft, but we’re a little short of projects that big; in this case we decided to focus on letting people see the aerodynamics for themselves. Most people without an engineering background have never had an opportunity to see how air flow forms around objects, and given the chance find the results both interesting and often quite pretty. Using the tunnel to explain how paper aeroplanes generate lift gave us purpose, gave the young kids something to do to get involved and hopefully may have got someone a little more interested in aerodynamics or technology. It also allowed us to demo the wind tunnel to show people that they can make a working wind tunnel without much expense or difficulty.
The tunnel we built is called an open loop wind tunnel, meaning it sucks air in from the room one end and blows it out the other end. This is the easiest type to build and has the largest working section for its size.
There are 5 key parts to open loop tunels, illustrated in the diagram above:
- Flow straightener
- Collector
- Working section
- Diffuser
- Fan
The next few steps will detail how each was made for our tunnel...
Step 2: Flow Straightener
This project has seen some keen skip-diving, and the acquisition
of our flow straightener is not an exception.
Our first thought was to use some honeycomb composite core material, but the price turned our stomachs a little.
We then looked into the more usual drinking straw approach. While cutting down hundreds of straws to inch long sections and gluing them together works well, it isn't free and takes a lot of time so I jumped at the opportunity to avoid the hassle when I saw a skip full of office lighting diffuser grids of roughly appropriate dimensions. These grids have a 20mm square grid of shiny plastic that controls the illumination from office strip lights. Taping three grids together in series results in lots of square 80mmm long tubes and seems to work well for straightening the air entering the tunnel.
If you can't find something suitable then grouping together lots of chunky straws is probably the best way to go. Aim for a length to diameter of at least 4 to 1 on your tubes to get a good straightening effect.
Step 3: Collector
The ducting on the right between the straightener and the working section is the collector. This leads the straightened air into the working section. The larger area of straightener brought into the collector helps both reduce back pressure and give a more constant flow of air in the working section rather than a gaussian distribution.
In an initial build we guessed a suitable shape for the collector (having seen a couple of open loop wind tunnels at uni), thinking we would remake it later...
...In further research I found a NASA wind tunnel design aimed for schools to build that was almost identical, so we decided to leave it as it was.
In order to achieve the curves we used a thick but non-corrugated card from a Lego box. It is slightly less tidy than the rest because we never expected it to be permanent. Ah well...
Step 4: Working Section
The working section is where testing can be performed as the airflow is smooth and straight.
When all is said and done the working section shape is a simple box of constant cross section. We added screens to the front and top to allow viewing and hinged the top screen for easy plane insertion.
Our working section is the only part not built from scrap. The body of this section was laser cut from plywood and the screens were cut from new acrylic for clearer viewing. Small hinges were added to allow the top to be opened, and some draught seal tape was put around to improve the seal.
The clips used to mount the paper plane were 3D printed on an PP3DP Up! 2. The base of the clip has a neodymium magnet push fit inside for easy swapping of planes. The clip magnets were stuck onto a steel rule taped to the bottom of the working section allowing easy positioning. While an elegant solution, I do rather miss this rule in my workshop!
To visualise flow within the working section we used smoke trails introduced by another 3D printed part, an aerodynamically streamlined splitter nozzle. The smoke itself is actually a non-toxic vapour generated by heating a water/glycerine/propylene glycol mix. To do this safely we used a ‘Zero Blaster’ toy smoke ring gun with 3D printed adapters (you may have guessed I recently got access to a new Up! 3D printer at work), with a small fan to blow the smoke out of the chamber and into the tunnel through a straw.
In testing we also used a 2 litre bottle with hot water and dry ice to create smoke. This gives a much better visual effect but doesn't last long enough for demonstrating at Maker Faire. If you go down this route the evaporating/subliming CO2 drives the smoke out of the bottle so there is no need for a fan, but I recommend cutting a 20mm hole in the bottle and sticking tape over it as a pressure relief in case the outlet gets blocked.
To help see what is going on we fitted a strip of LEDs running off a DC
power supply. These are angled back from the join between the screens for best viewing and the inside of the working section was painted black to help see the smoke trails.
Step 5: Diffuser
The ducting between the working section and the fan is the diffuser.
The design is based on one by NASA. Yes NASA baby!
Our original build saw an ugly square to hexagon to circle diffuser, but on discovering the NASA plans linked above we remade it to a design that was similar albeit of cardboard and gaffa tape construction.
The diffuser must be gently widening to keep the flow stable... don't make it spread too quickly or the air flow won't be stable as it will oscillate, separating from one side and then the other.
Straight, flat isosceles triangles come from the square end with points finishing at the fan. Larger triangles are cut with one edge 1/4 of the fan circumference, and the other two edges matching the length of of the sides of the smaller triangles. Making sure the corrugations go straight up the large triangles allows them to be curved, and taping inside and out holds it together quite well. We made a few holes to cable tie the fan guard into the end of the diffuser one end, and the other end we made a sliding friction fit onto the wood of the working section.
A small cardboard stand at the fan end stops it from rolling and levels the wind tunnel. The working section is on a small really useful box to make it the right height, and the flow straightener grids sit straight on the table.
Step 6: Fan-tastic
When we started out we were worried that a standard pedestal fan wouldn’t have the beans to create the required airflow, but a quick 'pre-build' build showed that my living room fan could easily kite my favourite paper plane design – the most stable design I know – on a short tether from a crocodile clip.
Call me psychic, but I soon sensed that filling our living room with a very untidy cardboard wind tunnel taped to our only fan the very day the UK plunged into a 35°C heatwave was not the romantic gesture my relationship needed.
The obvious solution was skip diving (of course). Mark and I liberated a pedestal fan with a broken pedestal from a nearby skip and the tunnel was relocated to my garage. One happy girlfriend and one problem solved.
Step 7: Finished
So that's that really.
As you can see it doesn't cost much to make quite a good scientific demonstrator that definitely seems popular with the kids.
We definitely succeeded in our target of encouraging kids to get excited about science and engineering... Sorry to everyone who had to clear up all the paper aeroplanes over the cities of Derby and Brighton!
Next steps
It seems like a good idea to try to improve the smoke a little. The vapour was difficult to see on all but the lowest of air flow speeds and the CO2 set up needed refilling every 5 minutes. Perhaps an automated bottle CO2 filler...
Aside from that, adding a way to measure lift/drag ratio might be a nice way to add a competitive edge to the plane testing (for the older participants to enjoy;)
If you enjoyed this please vote in the contests!
Thanks:)
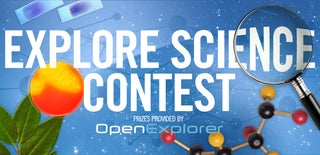
Participated in the
Explore Science Contest
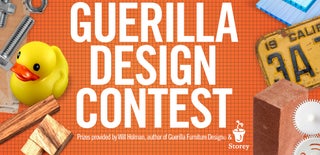
Participated in the
Guerilla Design Contest
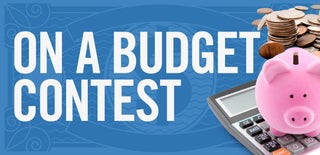
Participated in the
On a Budget Contest