Introduction: Penny Engine- Micro Air Powered Engine!
Please consider subscribing to my YouTube channel: Rusty Phoenix Motors
So I've been playing with Hot Wheels lately, and this developed as kind of a side project to something else I was working on. I've built a couple of other engines based on other designs I've found here on instructables but this one for me takes the cake! Originally I didn't intend for it to actually work, but I thought I could at least give it a try. And guess what? IT WORKS!!!
Here are two other instructables that helped inspire this one- the first is not a wobbler but very simple to build with cardboard and hot glue.
https://www.instructables.com/id/Toilet-Paper-Engin...
This is one of my all time favorite builds, and I used this model to design a much simpler version that I have my 8th Grade students build using only a drill press, a welder, and basic hand tools. No instructable on that one yet, but it's coming! The FANCY version is found here:
https://www.instructables.com/id/Air-Engine/
The Penny Engine is a Wobbler engine that runs on compressed air. This type of engine is called a wobbler because there is no connecting rod or wristpin- the entire cylinder and piston pivot as the crank spins, and as it pivots side to side compressed air (or steam or compressed CO2) is ported in at the right time to push the piston down.
There's a basic run down for you, so here's how we build it!
Step 1: Gather Supplies.
You'll need a lot of random bits and pieces as seen here. Small tubes and metal rods are usually available at hobby stores. The rod I used is actually aluminum welding rod. Tubes came from Hobby Lobby. You will also need a chunk of scrap aluminum or other thin sheet metal to act as the frame, a teensy screw, a small spring that can be robbed from a clicky pen, and of course a penny!
Step 2: Get the Tools Out!
Lots of tools needed, and the smaller the better. The hard part of this instructable will be drilling teensy holes. I'm using a cheapo pin drill or jewelers drill and bits that I bought off of ebay. The Jewelers Saw also came from the same place- and a word of advice on both tools- GET EXTRA BITS and BLADES. They break VERY easily. Everything else is pretty standard- Crazy Glue, hammer, pliers, aviation snips, file, dividers, and a tap or nut for the small screw you got.
Step 3: Overview- the Pieces.
Here they are. Several small spacers cut from the tubing using the jewelers saw. Chunk of aluminum sheet metal for the frame, penny makes the flywheel and crankshaft. Spring pictured is cut down from one stolen from a Bic ballpoint pen.
I took a bunch of measurements after it was built and have them written in on the drawings. These are just estimates, and I can't guarantee that these will work if you try to replicate the engine...
Step 4: Crankshaft.
Start with the crank. Take your time and mark the center of the penny. Very carefully drill as straight a hole as possible that matches the size of the rod / tubing you are going to use for the crank. I used 1/16" aluminum tubing, so my hole was 1/16".
Decide how long you want your stroke to be, and using the dividers, mark half of that distance from the crank hole. Drill another hole for the crank pin.
Cut a short length of tubing. Pinch one end of it and push it through the center crank hole. Add a drop of crazy glue and tap it in as far as you can. The pinched end will hopefully be a very tight fit, and the glue will hold it all together without any play.
Cut another short length of tubing and repeat the process for the crank pin hole, but it should stick out the other direction.
Step 5: Cylinder and Piston.
This can be the hard part. Find a piece of rod that fits nicely in some tubing. It should be able to slide freely, but be a tight enough fit that not too much air is going to escape around the rod.
Once you have the cylinder tube, crimp about 1/4" of it tightly as shown in the pics. Mark the center of the crimped area and drill a hole big enough for the screw you found to fit through it. Near the top of the cylinder area (below the crimped part) drill another hole. Mine was 1/16" hole. This is where the air pressure gets into the cylinder to push the piston down.
The piston should be roughly the same length as the entire cylinder, with a hole the same size as your crank pin drilled through it on one end. This should be a loose fit, so you may have to gently run the drill bit through it a couple of times testing with a piece of rod to make sure it spins easily in the hole.
Now its time to start on the valve plate!
Step 6: Valve Plate.
Mark where you want the cylinder to attach to the valve plate. Everything else will be measured from this hole. Using the dividers, measure the distance from the center of the hole of the pivot on the cylinder to the center of the air hole. Transfer it to the valve plate, scribing an arc as shown in the pics.
Bend the valve plate a little past the arc you just scribed as shown. This bend allows room for the flywheel. Now you can start figuring out the rest of the holes.
The hole for the crankshaft cannot be too far from the cylinder pivot hole, or else the piston will fall out of the cylinder. Estimate at minimum that 1/4 of the piston will remain in the cylinder with the crank pin is as at the bottom of the stroke, or as far from the cylinder as possible. Mark where the center hole needs to be. You can now drill the pivot hole and the crank hole.
Marking the valve holes can be tricky. Install the crank and turn it so the crank pin is as far to one side as possible. Using a straight edge of some kind, line up the pivot hole with the crank pin as shown, and mark where the straight edge crosses the arc you scribed earlier. In my pictures, the holes are already drilled to 1/16".
On the back, drill one of the holes almost all of the way through. This is to allow for the pressure tube to be installed later. I used 3/32" tubing, so the hole was drilled to 3/32".
Step 7: Assemble and Test!
Put it all together!
You will likely need to make some spacers for the crankshaft, crank pin, and cylinder pivot. The main things to keep in mind when adjusting your engine are these:
1. You need a good seal between the valve plate and the cylinder. This is achieved by making sure the cylinder is PARALLEL to the valve plate by adding a tiny spacer at the pivot point as shown in the pics.
2. The piston needs to be spaced away from the crank / flywheel a little so it doesn't snag on it as it spins.
3. The flywheel / crankshaft shouldn't be able to wander in and out, as this will throw the piston out of alignment with the cylinder and cause binding.
4. The entire thing should move EXTREMELY EASILY. If there is binding ANYWHERE, carefully disassemble the engine piece by piece until you discover what is causing the binding and adjust as necessary. Common areas where the engine can get hung up are the piston being too long hitting the top of the cylinder, the piston out of alignment with the cylinder, or the cylinder pivot screw can be too tight.
I strongly recommend wearing eye protection and testing in a safe location- there is a good possibility that parts are going to turn into missiles that are going to be bouncing around the room. Start with low pressure. I can get mine to spin a few turns with just my breath- but it feels like I'm going to pop a blood vessel... Mine seemed to run pretty good on about 20 p.s.i., but I'm still tinkering and as I get the engine more aligned and loosened up I think it will get better.
Good luck, and have fun! Please post any questions and I will try and get them answered. I hope to amend this instructable with a better video and more accurate plans as to the layout of holes and spacers but for now this is it.
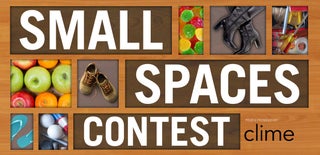
Participated in the
Small Spaces Contest
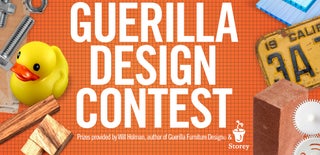
Participated in the
Guerilla Design Contest