Introduction: Pewter Casting
Pewter casting is easy and you probably already have most of the things you need to try it out. There are lots of ways to cast pewter, I'll be talking about three ways: using foundry casting sand, using silicone molds, and using cuttlebone.
This Instructable just covers the basics, there are a lot of more complex techniques and methods that can be utilized in casting pewter, but what you'll read about here is pretty basic. So, what you'll need:
Supplies
pewter (ingots or scrap)
a mold (I'll talk about these 3):
1. foundry casting sand, frame or other container for sand
2. two-part silicone mold making kit, mixing cups, molds (I used dixie cups and yogurt cups)
3. cuttlebone, tools for carving: knife, nail, clay tools
torch
stainless steel ladle
objects to cast (I used pinecones, fossils, and clay stamps)
Pewter Black
Step 1: Get Some Pewter...
First you'll need some pewter. Pewter is an alloy of 85–99% tin, mixed with approximately 5–10% antimony, 2% copper. Historically it was made with lead, but lead hasn't been used in pewter since the 1970's. If you are going buy pewter ingots, they shouldn't have any lead in them. If you use pewter scrap, it is possible that they contain lead. Lead must be ingested or inhaled to be toxic-if you use old pewter scrap, be safe-wear a respirator while cutting and when heating any pewter and wash your hands after handling it. Lead does not pass through your skin, but if you touch something, get some lead trace on it, and then eat it, I suppose you could transfer it that way.
You can buy pewter ingots on Amazon and Ebay (and other places). You can also get scrap pewter on ebay and make your own ingots. I usually go down to the second-hand shops and look for pewter from time to time. I almost always find some dented old sugarbowls or candlesticks. You need to be sure the pieces you get are pewter-check for the hallmark or maker's mark. Since most shops are closed during the pandemic, buying ingots or scrap pewter online is probably the best choice now.
Use an angle grinder or hacksaw to cut your pewter up into small pieces that will fit into your ladle (remember to wear your respirator or mask). Don't worry if it's scuzzy, you'll clean it up later.
Step 2: If You Are Using Scrap Pewter, You'll Need to Make Ingots. Also-this Step Shows You How to Melt and Pour
When making your own ingots from scrap, this step cleans up the crud that was on the old sugarbowl (or whatever you're recycling).
I always make little doll face ingots. You can use any kind of sand stamp you want to make yours.
I use casting sand to create my ingots. I made a little wood frame (with a bottom) and filled it 3/4 full with casting sand. I use another piece of wood to press the sand down firmly and smooth. Press something (the end of a big dowel, your thumb, whatever) into the sand and lift it straight out, I use a clay stamp made from a doll's face. It should leave a nice indentation in the sand. It may take a few tries to get the hang of this. I press a bunch of them in-I'm not too picky about them yet since they are going to get melted down again.
NEXT YOU WILL BE HEATING PEWTER UNTIL IT IS MOLTEN-IT IS SUPER HOT!!!! BE CAREFUL, HAVE A FIRE EXTINGUISHER NEAR, DON'T TOUCH ANYTHING YOU'VE HEATED UNTIL IT TOTALLY COOLS OFF. WEAR SHOES AND GLOVES. DO NOT TRY TO UNMOLD YOUR INGOTS BEFORE THEY ARE COOL.
Put some pieces of pewter into your ladle and heat it with your torch, put the flame on the pewter, or heat it from below (sometimes the torch won't stay lit if it's held horizontal). It melts at about 450F so you will see it begin melting in a few seconds. (I pinched the spout of my ladle a little to help get the pewter to flow where I want, and bent the handle to make pouring more comfortable). Once the pewter is in it's liquid form, carefully pour it into your mold, filling each indentation you've made. You will see a dirty skin form on the liquid pewter in your ladle, this is slag or impurities. As you pour, you'll see the clean pewter coming out from under the skin. Just let the slag cool in the ladle and knock it out to be discarded later when it's cool. After your ingots are cool, remove them and brush off all the sand. Sometimes they come out golden or rainbow-y. I don't know why, but it looks kind of cool.
Step 3: Pouring Pewter Into a Casting Sand Mold (see Previous Step)
So you just learned how to pour a flat backed piece of pewter (an ingot) using the casting sand. This method can be used with all kinds of impressed objects. I made some great fossil casts with this way. The trilobite on the left is the actual fossil.
There are ways to cast a full front/back piece using sand, but I'm not going there! I'm all about easy...
And if you get a bad cast, just remelt it and try again.
Step 4: Pouring Pewter Into a Silicone Mold
I'm not including full instructions on making silicone molds, for the flat backed castings I just poured silicone into disposable cups and suspended the object halfway into the silicone. For the front/back casting the entire object is suspended in silicone with a sprue attached to pour the metal into. That's how the peanut, the acorn button, the redwood cone, the solid pinecone and the shell were made.
I inserted a bolt into the molten pewter in the large pinecone mold to create a drawer pull. After you pour the pewter into your mold, and holding the bolt with pliers or gloves-it will heat up a bit, carefully (but quickly) sink the bolt in just past the head and hold it for a few seconds until the metal sets up. At first I tried tapping the back of the pewter, but this was way easier. I use a couple of nuts and sometimes a bit of tubing to get the right gap behind the drawer pull so you can get your fingers behind it. They look so great, I've got them all over the place!
The great thing about these molds is that you can create multiple copies as the silicone is pretty strong up to a point heat-wise, and pewter melts around 450F. The mold does degrade over time, but I've made dozens of the big pinecone drawer pulls and they are still coming out great.
Step 5: Pouring Pewter Into a Cuttlebone Mold
Remember the weird scratchy white thing you used to put in your budgie's cage? That's a cuttlebone from a cuttlefish. Birds and other animals like to use them to sharpen their beaks and to eat them, they are high in calcium, yum!
Anyway, you can carve into them (use nails, paperclips, dremels, the bone is soft), pour in pewter and cast beautiful swirly patterns in your piece. I just bought some cuttlebones at the petshop and carved a design into it, leaving an uncarved "hole" (really a bump). Poured in some pewter and got this beautiful necklace piece. You can do a full front/back pour, but it requires a bit more prep than I was willing to do. Even with just a one piece cast, I've seen great rings made-just the top edge is "unfinished" but the flat part of the ring looks beautiful.
It's a one shot deal, the mold gets burned up a bit during the process--and it's super stinky!! But looks great.
Step 6: Finishing Your Pewter Piece
When your pewter pour is cool enough to handle, you can give it a nice patina by dipping it into something like Jax Pewter Black. Let it go as dark as you like, be ready, it works quickly! The process starts to slow after you treat a few pieces. Wash it off with water, dry it and then rub off what you don't want. I used a green scrubbie, but in the past I've also used a wire brush, or a buffing cloth. You can also use liver of sulfur. Warm up your pewter piece in hot water and then dip it into liver of sulfur solution until it darkens to your liking. Rinse it off with water and rub off what you don't want.
Pewter is fun to work with because you don't really need too much to do it, no forge or burn-out oven, it melts at a low temperature, it's pourable and cheap. Plus, fire and molten metal? What's not to like?
Have fun, be careful, stay safe!
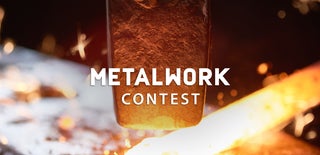
Second Prize in the
Metalworking Contest