Introduction: Poor Mans Fiberglass, Permanent Exterior Paint, Never Paint Again (almost), Waterproofing With Out Epoxy, Fiberglass Epoxy Allergy Relief
Back in 2011 I built a teardrop camper, at the time I needed a place to sleep a few nights a week as the long drive home was causing me to fall asleep behind the wheel way to often. I got the plans for the teardrop free from the best teardrop trailer site in the world.
In the discussion forums many different ways to cover plywood are mentioned, from today's most common one, skinning with aluminum sheet (very expensive!), to fiberglass and marine epoxy ($$$), Duraback (a bed liner product that comes in many colors), FRP, the shower wall liner sold in home improvement stores. FRP is cheaper, but it isn't UV stable and over time it will fade and crack in the sun. Filon, the UV stable version of FRP is an option, but unless you live in an area where RV's are manufactured shipping will be an issue.
Good old paint is the cheapest and lightest option, but as anybody who has to paint their house knows, paint will need to be redone every few years, and the wood underneath may end up getting damaged or weathered.
Reading about boats and boat building, (my real hobby) a simple cheap covering was mentioned, canvas and paint. Many old boats built before fiberglass and marine epoxies had canvas impregnated with paint for the decks. If you can find one of those old wooden boats rotting away in the back of some boat yard, some digging with a knife will show that the wood under the painted canvas is as sound as the day the paint was put on.
Wanting to save money and make my trailer as light as possible, I bought exterior paint and drop cloth canvas, some people use Titebond II instead of paint, Titebond II is cheaper per gallon than paint. you will still need paint though to fill the weave of the fabric and make it inert.
When you used fiberglass and epoxy, the epoxy sticks to the surface of the wood and binds the fiberglass sheet too it, then the epoxy fills the weave in the fiberglass making a skin over it to protect the fiberglass from damage. The fiberglass gives strength to the epoxy that epoxy alone doesn't have by itself. A sheet of plywood with fiberglass and epoxy skin is much stronger than plywood by itself, something used to make wooden boats and airplanes stronger.
Painted canvas works much the same way, the paint (or titebond II) sticks to the wood surface, and binds the canvas (or any natural fiber fabric) to it. Then the paint fills the fabric weave and protects it from UV breakdown. The fabric gives the paint the strength paint doesn't have on its own.
After using my teardrop for one summer, I ended up taking it off of the trailer I had it on, I was moving and needed a way to move stuff between houses. The teardrop body spent the only winter in a garage it ever has. The next summer I put the body back on the trailer and used it for camping, As part of putting it on the trailer, I added a second door for my wife to use (very important for a teardrop) and removed some unneeded framing I had built into the floor of the teardrop, This removed some weight and made the trailer shorter, making it easier to tow over all. I ended up having to peel some of the canvas loose from the framing, in every case the painted canvas ended up pulling the top layer of wood off with it, proof enough to me that the painted canvas bond is strong and stuck for good!
Unfortunately I don't have any pictures of the covering process, my teardrop was built over a few weeks as I needed a place to stay NOW! Pictures only happened when I reached a milestone in the project or at the end of the day (usually in the dark) what I have for a build log is here storm warning teardrop build
In 2014 I got the bug to build a foam camper, while the teardrop is nice, it only sleeps two. We have four kids and not every campground allows extra tents with a camper. I wanted the new camper to be made almost entirely of foam, since foam doesn't rot, and is much lighter. To get familiar with the foamie building process I built a small eight foot boat out of foam, using a design I had already built in plywood. You can see how that turned out here seafoam facebook album. Seafoam proved the concept had great potential, so over the winter of 2015 I designed and created another foam kayak called Sawfish the kayak is a great success, the Instrucable for it won two contests here, and generated a ton of interest on the web.
Armed with the experience I learned from the first two foam boats, I also created a Foam camper in the spring of 2015. It is not finished yet, but has already gone on a 10 hour drive and camping trip in the Adirondack Mountains of New York State.
There are two ways to do PMF, with one better for covering foam, and the other a little bit cheaper, and better for covering wood.
To show the two slightly different processes that can be used, I've broken it into two different sections. The first will be called Foamie, this is the best process to use over foam projects. Most of the people reading this will be looking for how to cover a foam camper or boat.
The second section starts on page 7, it shows the process I used to cover my plywood teardrop. It doesn't use any glue to attach the fabric to the wood. Instead a heavy coat of paint is used to stick the fabric, just like the old timers did.
You can also mix the two processes, like this builder did.
Step 1: Tools and Supplies
Foamies
-Titebond II , get a gallon it is slightly cheaper and you can use it for many projects
-enough fabric to cover the project, make sure you can overlap at the seams and still have enough. (cheapskate tip, ask at hospitals, around here they give away used sheets, AFTER washing them)
-Warner 250 wall paper removal tool (also can be found as the Silverline 221199) I got mine off of Amazon, but cheaper ones show up on Ebay from time to time. Your local wall paper store may also have them.
-Isopropyl Alcohol (if you don't want to perforate the foam surface, this will remove the foam release agents, sanding can also work)
-everything listed below in traditional
Traditional
-a paint roller handle and a couple rollers
-small paint brush
-exterior paint, I prefer Glidden porch paint after multiple failures with Behr paint and none with Glidden. Swing by the paint department of your local hardware store often, they sell the oops or mistint paint at a discount, use the wrong color paint to fill the fabric weave, then top coat with the color you want. Around here I get gallons for $9, and sometimes a 5 gallon bucket for $30.
-paint tray for the roller
-drop cloth for the area you are working in.
-coveralls Titebond sticks to everything, if you are messy like me you will need them
-gloves, unless you like sticky messy hands that stay dirty looking until the outer layer of skin falls off.
-razor knife
-scissors
-sand paper, sander, or router, for rounding over sharp corners.
-respirator, Titebond II and latex paint both give off vapors, I did the gluing in my unvented basement work shop and got a wicked head ache from it. I did the painting in my unheated, but well ventilated, garage, then brought the hatch inside to dry (cold out, with a snow storm coming) while the vapors aren't as bad as epoxy they can still build up in your body and make you allergic to them.
Even sanding wood can make you allergic to it over time, keep that stuff out of your lungs!
Step 2: Foamies-surface Prep
Foam is a weak substance, if you test the bonding properties of foam, you quickly discover that the glue only sticks to the top layer of foam particles. Put that bond under stress, and the top layer will shear off, leaving the rest of the foam behind. Not only that, but during the manufacturing process, the machines leave a waxy "release agent" on the surface of the foam. Some people use Isopropyl Alcohol to remove the release agents and prep the skin for a good bond.
Others like to sand the foam skin lightly to break the skins outer shell to get a better bond.
Neither of these treatments will give a deeper bond for the glue layer. To give the strongest bond, one that goes beyond the top layer of the surface, I perforate my foam with the warner 250 wall paper removal tool. I do this to every surface of the foam before applying glue. On my foam kayaks this has proven to be the strongest bond possible. I have a thread on tnttt.com with the results of multiple foam sample tests if you care to look.
As the founder of tnttt.com described it, perforating the foam, and then filling the perforations with glue, is like making a thousand tiny nails of glue, into the foam. He is very correct.
I find one heavy pass over each section of foam is fine, you can do multiple passes to increase the perforations if you want. The more holes showing, the better. These perforations also give the best indication that you have the perfect amount of glue on the foam.
The perforations will tend to tear out little beads of foam, to avoid any bumps under the PMF skin, a light sanding by hand will remove these hangers.
You can also wipe the surface with the Isopropyl to get the best bond possible, I don't bother, and have never had an issue.
This is the time to prepare any sharp corners on the object you are covering, fabric will fight being folded at sharp angles, a quick rounding off with sand paper will make it stick without bubbling and fighting you.
If you have any dents in your foam use some lightweight spackle (patching compound) you can tell it is the right stuff because the tub will feel empty compared to normal weight spackle. Fill the holes, then sand once the spackle cures.
Step 3: Foamies-fabric Layout
Cutting your fabric before the glue is on and curing is critical! I prefer to work in sections, tacking the fabric to the foam with pins or skewers, cutting it to a 6 inch overlap on each side, then marking the edges and cut outs with a soft lead pencil to help with alignment when the glue is curing.
The more prep you do here, the easier it will be to work with glue getting everywhere and on everything.
Covering objects like boats is harder, all those odd angles and rounded edges make the fabric want to pull, wrinkle and stretch in ways you aren't expecting. Leave a good edge to cover the edges on twisted edges, fabric tends to stretch one way better than others, and this may change where the fabric edges fall from where you cut them to lie. The fabric, even the heavy canvas I use on teardrops, will stretch as you glue it.
To make the seams in the fabric strong, overlap the fabric by at least 4 inches. On a teardrop, have 6 inches of the wall fabric go up onto the roof, and 6 inches go down under the bottom of the floor. Figure the same overlap on the roof panel.
Step 4: Foamies-glue
The best glue to stick fabric to foam is titebond II. Many tests and builds have proven this, you can try other glues, and you might get good results, but you won't get one result that TBII has, Heat activation.
The best foam for building with, due to cost and ease to buy, is XPS foam. Just about every hardware store and big box home supply house sells it. Those of us who live in areas of the country that see below zero weather, will have thicker panels at the stores near us, with 2" foam being the maximum in most cases.
XPS is formed in part by heating it. If you heat your foam panel beyond 190 F it will get soft and bendable, much like boiled pasta. TBII is also a heat activated glue, heat cured TBII above 190 F and it will become rubbery and easy to form. If you use TBII to glue your fabric skin to the foam, you can removed most dents and creases in the camper or boat you build, using a steam iron.
simply place a left over section of canvas or a dish towel you don't care about, over the dent, apply the steaming iron to the area, and let the heat work it's way in. The steam will keep the heat applied to the area below 220 F, (the boiling point of water) and that heat will cause the TBII and foam to become soft. When the foam is softened it will swell back into the dent or crease.
The other reason I prefer to perforate my foam, is that the tiny holes make the perfect indicators of a good glue application.
I use vinyl gloves for this step, as the TBII will just shed off of them as it cures.
Put the TBII into the paint tray, roll or brush the glue onto the foam, the perfect amount of glue is indicated by looking seeing that every perforation has a dot of glue in it. If you don't perforate your foam, you will have to figure out how much is too little, and how much is too much glue.
Work with areas of foam small enough that it doesn't cure before you get the fabric stuck to the glue. For teardrop walls, which are normally 4 feet or so high, I work in three foot wide sections.
Once the fabric is stuck along the far edge of the glued surface, work it into the glue, and stretch it toward the next strip to be glued.
The cheap drop cloth canvas will have a seam every 4 feet or so, I prefer to cut these seams out of the fabric, and work with sections as wide as the remaining fabric.
When you overlap the fabric, paint some glue onto the fabric already stuck to the foam, then glue the overlapping fabric on, overlap by 4 inches minimum. You can sand the seams afterwards to get a smooth finish. Some people like to use thinned glue painted onto the cut edges to keep the fabric from coming apart.
Step 5: Foamies-edge Treatment
On a teardrop, I take the roof fabric panel and cut the edge away exactly even with the wall of the teardrop, that way I don't have a seam showing on the sidewalls.
On a boat, and the front and rear curves of a teardrop camper, you will get wrinkles in the overlapped fabric as it goes around the joints. I started out cutting darts into the fabric with shears, but now use a simpler method.
With the edge fabric glued down into still tacky glue, stretch it into place until the wrinkles are revealed as tight folds. Take the razor blade, and slice the top of the fold from the point to the edge.
Stick one side of the sliced wrinkle down into the glue, so that it lays flat.
Apply glue to the underside of the section still sticking up, and press it flat onto the other section, stretching it as it tacks.
This will ensure that the edge stays down.
Step 6: Foamies-water Proofing
To ensure that your fabric skin won't rot away from exposure to water and sun, you must seal it fully.
On thin fabric, like the bed sheets I used to cover my foam kayaks, only one coat of paint will be needed, use the finished color you want, and paint the fabric.
For Canvas, you will need multiple coats, of paint, and possibly a glue layer first.
Some foamie builders use a coat of TBII thinned 25% with water, or exterior oops paint thinned 50%. They paint the canvas with this thinned coat to fill and seal the fibers, let it dry, then apply the finished paint colors they want. For a smooth finish, sand the fabric surface between each coat. Another trick I've heard is to add cabosil, or micro ballons, normally used to thicken marine epoxy, to the final paint coats to make a thickened layer you can sand smooth. The idea of flour has also been mentioned. This youtube video mentions sanding between coats for a great finish.
I prefer to use Oops paint to do the sealing, as Oops paint is cheaper. I get wrong-colored or mis-tinted paint by the gallon of five gallon bucket at my local Orange borg (home center) all spring and summer people find out they ordered the wrong color paint, this happens when the paint coloring machine isn't cleaned correctly, if two gallons of the same color are bought from different stores, or if the paint matching process isn't exactly correct.
In one gallon cans I can pay as little as $9/gallon, and in five gallon buckets, as little as $30. Mostly it depends on how ugly the shade they changed it too before they stuck it on the Oops rack. I Use only exterior house paint, I do not know if interior paint will do the job, and don't want to learn the hard way.
To fill your fabric with Oops paint, fill the paint tray with Oops paint. take a dripping wet roller of paint and roll it on the canvas as heavy as possible. Once the whole surface has been coated, go on to the next. You will see a wet shine off of a fully saturated surface, I call it a run coat, as it will probably be dripping along the lower edge.
Come back to that panel in ten or fifteen minutes, it will appear dull now, as the fabric will have soaked up most of the liquid paint. Roll another run coat into the fabric, make sure the paint has a wet shine when you are done.
Repeat this process as needed, until you come back after ten min. and the fabric is still shiny with paint.
You have now fully saturated and sealed the fabric fibers all the way underneath.
Once the paint cures, paint it the color you want. If you notice the pictures of the steeple I painted, part of it was grey, and part was ugly green, this was the Oops paint colors I had on hand. When finished, I sprayed the whole steeple white.
Step 7: Traditional-surface Prep
To truly do this the traditional way, you would need lead, oil based paint. Since this has been determined to kill people and make children dumb, the paint makers have come up with paint that almost does the job of the good old stuff. I really don't know how we all survived all those years of lead paint, you realize the whitewash Tom Sawyer fooled his friends into putting on the fence for him, was sour milk mixed with lead. Not only that but I grew up in a house covered with many layers of lead paint, inside, on the windows and doors I touched and chewed on!
Anyway, to get as close to those old wooden boat decks, you first want to have a smooth surface to cover. Sand the rough grain, remove any loose paint, sand the rest lightly to give the new paint something to grab, round over any edges, and fill any pockets or holes. Sand the filler.
Make sure any joints are tight, I like to use PLpremium adhesive to seal any cracks, then sand the PLp off smooth.
It is a good idea to seal any wood with THE MIX at this point.
THE MIX- mix oil based polyurethane with 25% oil based paint thinner. Mix well and paint onto the wood until it isn't soaked in.
Lightly sand the surface with coarse grit to give the paint some tooth.
IF YOU ARE USING THIS ON A WOODEN BOAT!
I don't recommend PMF for a boat that sees more than day use. The house paint is not waterproof, and water will get to the wood. Plywood will be damaged over time from this. Treating it with THE MIX may stop this, but really this is one place you won't beat marine epoxy in the long run.
Step 8: Traditional-prep
Start by laying out the fabric to cover your wood object. In this case I am demonstrating on a church steeple. I had to fabricate new plywood panels, and also glue some of the trim boards back together as they had cracked and fallen apart.
Make sure your fabric will cover the whole area, plus a few inches to wrap around the edges, Sealing the edges keeps the fabric stuck down hard, and keeps the wood from rotting again.
Mark the corners to help you know where they should lie.
Lay out a board or something hard, that is clean, to lay the fabric on for painting.
Step 9: Traditional-painting
Unlike the TBII process shown before, this process happens in one big step.
Start by painting the back of the canvas panel you cut and marked for the area with a heavy coat of paint.
Now paint a heavy coat of paint onto your prepared wood object.
Apply the painted side of the canvas to the painted wood panel, for large areas you may want to fold the canvas to make it easier to move.
Using a dripping wet roller of paint, roll paint into the center of the canvas, working outward all the way around. Keep filling the roller with more paint as you go. Once the whole canvas is wet with paint, paint the ends and back edges with a heavy coat of paint, then use the dripping wet roller to smooth the fabric into the edges and back of the panel, a staple can be used to help secure the fabric until the paint is dry.
Roll paint into the fabric until the whole surface is glossy wet with paint.
Come back to the panel in ten minutes or so, and roll some more wet paint into the fabric until the surface is glossy again.
Repeat until the surface is glossy with paint after ten minutes, this shows that the fabric is completely saturated with paint.
Once the surface is dry, paint with the color you want it finished with. The fabric will take a while to dry completely, there is a ton of paint in there.
Step 10: Old Houses, the Fun Never Ends!
As the caretaker for a church, I get plenty of chances to do repairs caused by neglect and age. The steeple was showing it's age, after scraping the paint, I found the plywood skin panels were in tough shape. a few of them had delaminated, or had corners missing. Even the solid wood trim was weathered badly. A perfect project for the poor mans fiberglass!
I started by removing the solid wood trim, as it covered the top edges of the plywood sides. Any delaminated plywood will be replaced, the rest will just be given the PMF treatment. Since the Steeple gets baked in the sun on three sides, and blasted by wind, rain and snow, from all sides, I decided to wrap each panel individually instead of just wrapping the steeple in place. This means that each plywood edge has fabric wrapped back around it, since the sides are 3/8" ply, this makes a kind of tight corner, I used a staple gun to keep the eges stuck down while the paint dried. Once the paint dries, the staples are unneeded.
I started with the plywood panel, laid the fabric (eight ounce canvas drop cloth) over it. cut out the panel shape, leaving an inch or two all the way around.
depending on the shape you are doing, the panel is your best place to apply the paint to the back of the fabric, flip the canvas over, roll a good heavy coat of paint into it, lay the canvas somewhere safe, then roll a heavy coat of paint onto the wood. Take the prepainted canvas and lay it onto the wet plywood. this is your chance to work out any wrinkles or bubbles.
Once your are happy with the fabric, apply the paint, use a dripping wet roller to apply and spread the paint, a sticky roller will tend to roll the fabric up around it.
After the panels were dry, put them back up, once they all are done, I will use a paint sprayer to shoot it all in white. The blue paint was a great deal, 5 gallons for the price of one, from the oops shelf.
We also did the crown mouldings with each piece getting it's own wrap since the wood was very dry and cracking, some parts needed some gorrilla glue to keep together.
Step 11: PMF and Boats...
As I claim in the title of this I'ble, PMF works for coating boats also. As I mentioned on the first page, I got this idea from the Foamies section of TnTTT.com. The orginal idea came from foam RC airplanes that are coated with glued on tissue paper. Planes made like this are cheap, light and super tough, able to stand up to more abuse than any other build medium and easy to repair with a couple drops of glue after a crash. The idea GPW (screen name) floated was, can we apply this type of construction to a teardrop camper? The answer is yes, just expect every knuckle head you tell that to, to punch the side of your camper, expecting it to shatter or crumble, then walk away nursing his sore knuckles. There are now Foamie campers that have gone more than 5,000 miles, and been around for years. The only prediction of the nay sayers that came true, one rather boxy, over tall (IMO) camper was blown over by the wind while traveling in the southwest US. THis was on a day that 18 wheelers were being given wind warnings, so no big surprise there. Even then the trailer just tipped up until the forward corner dragged on the road, the driver got out, pushed it back down, only to have it happen again. Even after all that, the camper made it home just fine, other than some road rash on the front corner, there was no real damage.
Reading on this and being a boat builder, I decided to try the Foamie concept of construction out in a small cheap, easy to build boat design that I have already build 7 times before in plywood. The Mouseboat, a simple, but very useful design, shared for free with the world by Gavin Atkin. Album of the build and boat
The foam mouse cost about $100, it weighs about 15 lbs! (I redid the decks on the ends twice, and am still not done, with paint on the new decks)
Instead of plywood, I built the boat entirely of 1" XPS (expanded polysterene foam insullation), instead of marine epoxy and fiberglass tape, I used Great Stuff expanding foam to stick all the joints together and waterproof them. XPS is waterproof closed cell foam, Great Stuff (GS) is open cell foam, it will suck up water and not let it go, it also cannot stand up to UV.
Foam is great for loads in compression, 1" thick foam takes a lot of force to crush very far on edge, for loads in tension, foam is weak and will crack. To give the foam strength it needs a strong skin, in this case I used cotton bed sheets to make the skin.
First I broke the smooth skin of the foam with a wallpaper perforating tool, imagine a wooden roller with a whole bunch of nails sticking out of it, it does a great job of giving some tooth to the foam. (and your hands if you aren't carefull) Next I coated the perforated foam with TiteBond II (TB II) and then smoothed the cotton bed sheet into the TBII. Once the fabric was glued down, I filled the weave with exterior oops paint, then top coated it with my favorite color, yellow.
I launched the boat into a beaver pond, since the pond is a flooded meadow, it is full of dead trees, stumps, and rocks. I spent the day following my kids around the pond as they explored it in their plywood mouseboats. Many times I ran up on sunken objects. To test the strength of the skinned foam hull, I didn't take it easy on the boat, instead of shifting my weight to allow me to float off the problem, I just paddled harder and forced the boat over the object. The foam did not break, the hull didn't fail, the fabric didn't tear, in fact the paint didn't even get scraped off, the way it does from my plywood boats painted with the same exterior porch paint. Instead there are some shallow grooves in the foam, and I know from the experience other Fomies have had, a steam Iron would remove those dents like they never happened. (TBII and EPS foam are both brought to the "limp spagheti" stage at about 190 F)
check out my Sawfish foam kayak instrucable, in the last picture on page one, the 23 pound boat is holding my 180 lbs, with only the ends supported on sawhorses.
Step 12: Foam Camper, a "foamie" Called Mercury
I mentioned that I built the first foam boat to get the building methods down for a foam camper. Then I went and built a great foam kayak. This has lead to another design, a foam kayak for kids. However I did end up building, (but not finishing) the foam camper.
I started with an old pop up camper I dragged home for free. It actually sat for a few years until spring of 2015 when I tore it all down to the frame, burned the bits of wood, trashed the mouse eaten fabric, and scrapped all the metal. I got about $30 at the scrap yard for the aluminum and steel, but even better, I found a working camp stove, battery powered fan, air mattresses, a table, a working stove and sink and some other stuff that will come in handy on the new build.
My new foamie takes the definition of a tear drop to the max, 13 feet long, 6 feet wide, 4 feet tall (the only normal dimension) and all square. It has two rooms and a huge galley, four doors, and (when it is complete, will have) a second story that stows downstairs for towing.
To get the extra length I added the rear bumper section to the frame by bolting on some frame rails removed from another pop up frame I tore down and then trimmed to fit my original teardrop. This made the rear axle too far forward for proper tear balance, so I removed the axle and moved it back so that the rear spring slipper shackle became the front spring shackle.
I put a plywood deck on for strength, coated it with deck sealer paint I got on clearance, and began to put up walls. The walls are all 2" thick, 4'x8' panels. I used gorilla glue to stick the foam and wood together. I used stainless nails driven up through the floor every 8" or so to spike the foam onto. These nails held the foam in place until the glue cured. I added a roof of plywood, as there will be at least three kids sleeping on it when done.
I started the PMF process, but only got as far as getting the fabric on. We took the camper on a 5 hour drive for our family camping trip in the Adirondack mountains of New York state. The fabric was well secured using TB II to stick it on, with only a few edges here and there that came unstuck in the rain. For all that Mercury is so large, it is also so light that it tows like nothing is there behind my Dodge Grand Caravan. After a spin on the road to test how it towed, I loaded it up for the big trip. The van knew the load was there climbing the mountains, but otherwise our gear and boats were no issue.
The camper performed just fine, it was rather cool a few nights, more like October weather than August, but the 40 degree nights were just fine inside our foam camper.
Just like putting PMF on a foam boat, the best glue for PMF on a foam camper is Titebond II (TBII) I used the wallpaper scoring tool to rough up the surface of the foam, then sanded any loose hanging edges to make a smooth glue surface.
I had the whole body of the tear jacked up and sitting on blocks of wood to allow me to glue the bottom edge of the canvas to the bottom of the plywood. I did the same to the top edge, wrapping the fabric up onto the roof about 4". The cheap drop cloth canvas from Home Depot and Harbor Freight now has a seam every 4 feet or so. We cut the seams out and overlapped each panel of canvas by a few inches. I started canvasing from the back of the tear, this way each seam faces aft, not forward.
Once the walls, windows and doors were glued down, I laid a layer of canvas on the roof. Once again starting at the back and working forward. For a nice clean finish I used a razor blade to cut the roof canvas off flush with the edge of the roof. Staples were set along the edge to keep the canvas tight.
Once the camping trip was done, I used a five gallon bucket of oops paint to fill the weave. The tear is sitting out for the winter, I expect it to be ready to finish the second story cabin in the spring.
full details and updateson my build can be found here and here
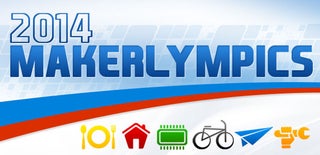
Participated in the
Makerlympics Contest
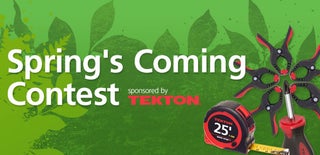
Participated in the
Spring's Coming Contest