Introduction: Purpleheart Pen: Turning Your First Pen
Before we get started, I am new to woodturning. I in no way intend to give an expert look at pen turning. Rather, I'd like to share my perspective after scouring the internet for guides and applying that knowledge to my first turnings. This guide will point out pitfalls and explain things that were unclear once I got in the trenches and turned my own pen.
For my first pen, I was equipped with the mini-lathe from Harbor Freight and their High Speed Steel chisel set. You could spend more, but my research and budget dictated this as a starting point. My initial reservations about reliability and build quality have been cleared -- it's very stable, as compared to their scroll saw and some of my other consumer-grade power tools. Mine requires manual belt tensioning to change the speed, but it's very straightforward.
The rest of my supplies for this were purchased from Craft Supplies USA/WoodTurner's Catalog. I searched for the best prices on blanks, pen kits, starter sets (mandrels, bushing, etc...) and found no one cheaper. I bought the apprentice starter kit, some extra blanks, and a micro mesh kit.
Step 1: Preparing the Blank
The blanks in the kit were already cut to rough thickness, but still needed to be cut to rough length for the brass tubes. Most guides will talk about all the different options for cutting the blanks and how you should leave about a 1/4 inch extra per tube. I got the bright idea to use my scroll saw. It's not the most accurate thing in my shop, but the blade definitely wandered on me and nearly left me with a short blank. I would recommend something like a hand saw or table/chop saw for a more predictable cut. I corrected the wandering by nibbling away some of the angle it left and utilizing the guide to keep the piece from bouncing off the blade. I've been used to working with pine and pallet oak, so the harder purpleheart was a little bit of a surprise. Be sure to mark the blank so you can better match the grain direction. If there's a prettiest part of the blank, make sure it's in the pen (and not the off-cut) portion of your layout. My grain was pretty even throughout.
My blanks, and most of the commercially sold blanks, were very square. I did not purchase a center finder, but instead opted to trace a straightedge corner to corner and drill in the intersection. Getting a straight cut when dividing them makes this easier! Not having a drill-press, I drilled carefully and slowly with the provided 7mm bradpoint bit. The bradpoint keeps the bit centered, more so that a regular twist-bit, but won't hide poor drill alignment. To hold the workpiece, I used an unmodified wooden handscrew. Many people make or modify them to hold the blank, but I had very little issue using it as-is. It is recommended to drill the hole from the center for better grain-matching, since any angle to it would be magnified by the length of the blank.
Step 2: Brass Barrel
Once the holes are drilled, they're ready to receive the brass tubes which are provided with the pen kits. They come pristine and need to be scuffed to better hold the glue or epoxy.
I used some old, leftover 220 disks from my random orbital sander -- there's nothing precise about this step. My kit included some medium thickness Cyanoacrylate (CA/Krazy) glue. You could also use epoxy, but the CA is probably cheaper and easier to use. Accelerator is not required for this application of the CA glue, and for me, it sets up fast enough not to need any help.
After the glue is set, and I figured it was set after the spilled stuff on my fingers hardened, the blanks will need to be trimmed to the length of the tube. My starter set came with a barrel-trimmer and center bits for various diameter pen tubes. Select the one that matches your pen kit and tighten the mill with an allen wrench, generally provided with the trimmer. The tube will act mostly like a bearing around the central bit, but the mill will cut through the brass -- trim until just a hint of the brass tube is trimmed. You'll know you're done when the brass shines. This is another operation that is often done on the drill press. I had less trouble with this on the handheld drill than the hole itself. Both ends of both blanks need to be trimmed. I got fairly close with the length of my blanks, but I imagine they can be as proud in either direction as the gap that the bushings allow. It is possible to trim too much with the barrel mill -- while your pen length can be slightly shorter and still accommodate the refill, it could be too short for the mandrel (ask me how I know).
Step 3: Mounting and Safety
The morse taper end of the pen mandrel is mounted in the headstock, following the lathe manufacturer's instructions. There should be a knurled wheel on the opposite end. Mine arrived with the knurled piece frozen in place from shipping. I was able, due to impatience, to unscrew the mandrel from the tapered end and load my bushings and blanks opposite of the normal order, rescrew the mandrel into the taper, tighten the tailstock's cup center to the divot in the end of the mandrel. This should only be tightened enough to support it; not enough to bend or warp the mandrel. I'll probably make the small investment in a mandrel saver, which is designed to put the force on the bushings instead of the mandrel, keeping it from warping or causing the blank to run out of true and making for sloppy turnings.
Following best safety protocol, I checked several things:
- Ensure all pieces are locked in place
- Manually rotate the headstock (mine has a handwheel) and ensure work does not wobble or contact tool rest
- Ensure lathe is set to lowest speed
- None of the work pieces shows any signs of cracking
I won't preach the merits of dust collection/respirators/hearing protection or any of the other boilerplate shop safety. One thing I will mention, though, is a face shield. There WILL be pieces flying off of lathe, and though they'll normally be shavings, it's quite common for pieces to crack and become airborne. Protect your face!
Step 4: Turn, Turn, Turn
After all the safety checks, I turned on the lathe and it was apparent that I could have really used a drill press! I had plenty of thickness left, even given the angle I'd inadvertently drilled my holes at. I first brought my pieces to round with a roughing gouge. It's best to start lightly until the flats have been brought down. If the pieces stop turning along with the mandrel, there's probably not enough tension across the blanks/bushings. If the knob on the mandrel is fully engaged, an extra bushing or spacer could help. I moved from the gouge to a flat, round-nosed chisel for most of the shaping.
I chose a fairly even cylinder for the rear half of the pen and a bulbous tear-drop for the front. Most of this was by feel and was helped by taking my time and going slowly. The bushings, while also keeping the blanks apart and in place, are the same diameter as the pieces of the pen kit they represent. I used these to visualize how I wanted the parts to flow, tapering to and from the diameter of the bushing, but also to ensure that I didn't carve too deeply into the blank. It is important to keep from hitting these with the chisels or sandpaper and altering them. It wouldn't be unreasonable to order a replacement set of bushings - If not for when they get damaged, they're also very small and easily lost.
Step 5: Sanding, Smoothing, Polishing
One thing that surprised me, maybe more than anything else, was how aggressive sandpaper shaped on the lathe. It stands to reason from the rpm of the lathe, but wasn't readily apparent or explicit in what I'd read/watched beforehand. I started with 60/80 grit, moved onto 120, 220, and 320. I used all previously used, dry sandpaper. It's important to keep the paper moving -- it gets pretty warm from the friction.
After getting everything to a satisfactory finish with the 320 grit, I moved on to micro mesh. The first grit in my pack was equivalent in coarseness to 400 grit sandpaper, but according to the manufacturer has a much higher uniformity pattern. Following the manufacturer's instructions, I used circular motions and kept the pads moving to keep them from melting/burning. I went all the way through to 12,000 grit micro mesh. It's probably pretty unnecessary to go that far.
My starter pack included a bottle of friction polish. I applied it to the work piece while the lathe was powered down, using some Taco Bell napkins. Though some instructions I read mention using a rag, it's safer to use a paper towel or napkin to apply finish on a lathe. Cloth can snag and wrap around between centers, but paper is more likely to tear/break before damage to one's hands could occur. The instructions say to apply while stopped and turn after the finish soaks-in/dries, then using friction and heat, the finish turns high gloss. I didn't have any wax on hand, but I understand that this increases both the look of the finish and the durability. I'm quite pleased with the finish, even without the wax. It was somewhere around this step that I took a victory lap indoors to announce to my wife that I was God's gift to woodworking.
Step 6: Assembly
Removing my pen from the lathe was more difficult than what I'd read, mostly because I'd stubbornly gone ahead with it even though the knurled knob wouldn't release on it's own end. I dropped the pen blank on the lathe bed while removing it the wrong way. I'm pretty sure it caused a scratch on the pen, but I can't be sure. I'll probably lay down a cloth the next time I do the removal process, just in case.
I laid out the parts at the suggestion of the instruction sheet that came with my kit. It seems silly, but it probably went a little faster as a result. First, I inserted the pen tip into the front half of the blank and tightened a pistol grip clamp around it. There are plenty of store-bought unitasker presses to do these operations, but I didn't see the need and experience has now proven that they're not necessary. It was easy to see what everyone was talking about -- the pen kit parts will quite easily not stay straight as you go to press them together, but it doesn't seem difficult to right them along the way either. Next was the twist mechanism. Another big unknown for me was how far to press in the twist mechanism. My instructions said something like "to the line," but there were multiple lines or stops. I'd also been warned with all the parts that pressing too far would be permanent, so I was worried about accidentally going too far. As it turned out, I didn't press far enough the first two times. I figured this out when the pen's tip didn't extend far enough. It ended up being the furthest mark on the twist mechanism, not just the brass section.
Finally, the cap fits into the clip and both are pressed into the rear of the rear blank. A beauty ring slides over the twist-mech, the ink refill drops in, and the rear blank slides on to meet the ring. Now we have a pen! If you did any solid grain-matching, make sure to slide the rear down with the grain lined up while the nib is closed or open.
Step 7: Complete!
I'm super stoked about how my pen turned out. Is it perfect? No. I'll be researching and practicing my technique, particularly on how to apply finish and seeking alternatives. I also damaged the clip from carrying the pen in my pants pocket a few days later, so I'll be looking at making boxes or something to put the pens in when they're traveling.
I'd love to hear from you all. Do you have tips or suggestions? Have you made something similar? Be sure to leave a comment, tell me what you liked or disliked. If you're so inclined, I'd appreciate your votes. I have other articles on things from bookshelves to sock puppets. You can also find me on social media:
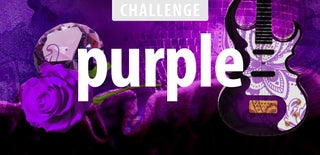
Runner Up in the
Purple Challenge
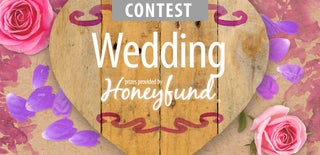
Participated in the
Wedding Contest 2016