Introduction: Salvaging Electronics: Desoldering
Hello fellow users of the internet! Before I get started, it should be noted that this is my first instructable, and as result it may not be particularly polished. As such, I would appreciate some feedback on this so I can continue with what I got right and fix what I got wrong. Anyways, on with the show!
Have you ever found yourself short on part and funds? Have you ever found yourself saddened by the shear mass of electrical waste that is thrown out without a care? In either case, this tutorial may be able to help you! With the power of desoldering, you can obtain a variety of electrical component cheaply, all while following through with excellent reuse of parts that would otherwise be thrown away! If you haven't guessed already, I am submitting this to both the first time author and green electronics contest, so I would appreciate your support in either, or even both if you are feeling generous! Now that I am done begging, we can carry on to the first step.
Step 1: Discretion Is the Better Part Of... Desoldering?
That's right. Before desoldering anything, it might be best to ask yourselves a few questions:
- Do I have permission to destroy this device? (Just for the other youngsters out there ;D )
- Is this device more valuable to me in it's current state, or as a pile of individual components?
- What are the safety hazards of this device's contents (charged capacitors, high voltages, lasers, etc) and if necessary, how do I account for these dangers?
- Which components should I bother to extract?
Each question will help you decide upon the appropriateness of any plan of action. If you want to get a more in depth look at what to expect, a quick google search can help you come up with various parts you may come across.
Step 2: A Note About Safety
Safety is very important, as a few components are probably not worth your good health. As such, I advise that you have a couple pieces of personal protective equipment to keep you safe. For instance, the first picture above is of me wearing a couple of common types of safety equipment.
- Safety Glasses: These are a must, and are advisable during all stages of this tutorial. It obviously protects your eyes from stray bits ranging from shards of plastic to droplets of splashed solder. In either case, you'll be glad that you wore safety glasses.
- Gloves: These can be worn if you are dealing with anything rough, sharp, or hot to the touch. While a pair might come in handy in the earlier steps, I wouldn't advise that you use them when using a soldering iron or similar. On a side note, some thin nitrile or latex gloves could come in handy (pun intended) if you are dealing with a messy material.
- Particulate Mask: While not incredibly useful, it can help when using tools that produce a lot of dust, such as a dremel. Other than that, we have some other tools to help us.
Beyond those common wearables, there one more tool that can help you stay safe is a fume extractor. When melting solder, potentially dangerous fumes can be produced. While not immediately dangerous, they can contribute to long term issues such as asthma. A fume extractor sucks up and filters these fumes, preventing any potential harm to you. If you don't have one, there are plenty to by and even more to make, such as this one. In fact, you will find dozens of tutorials to make your own on this website alone. But is these still aren't an option, it is acceptable to simply solder in an area with plenty of ventilation.
In particular situations, electricity itself can pose a threat. Shorts can generate large amount of heat with even small power sources, while higher voltages can deliver painful and even deadly shocks. The first step to mitigate these risks is to remove power sources, everything ranging from coin batteries to connections to a wall socket. Hopefully the later of the two was obvious. Unfortunately, certain components can retain energy from their last exposure to electrical energy, extending the threat. The most common culprit is the capacitor. Luckily, they can often discharge into the surrounding circuit in a matter of minutes. As such, I advise at least ten minutes between the last connection to power and the start of disassembly, especially in devices that can be connected to mains voltage. If at any time you find a particularly beefy capacitor which you suspect may still hold a charge, a good course of action is to deliberately short the capacitor with screwdriver with insulating handle. If all goes well, any remaining charge will be dispelled. If you don't feel conformable doing this, you may want to reconsider your disassembly project. And as a reminder, I take no responsibility for your mistakes should you attempt to follow my instructions. Regardless, we can finally go onto the less extreme part of safety.
A final thing that you would not be safe without is common sense. Obviously, make sure you know how to use your tools correctly. And to minimize the absorption of lead from leaded solder you may encounter, it is a good idea to wash your hands after you are done. With this done, we can finally begin the actual process.
Step 3: Extracting the Boards
Before you can actually warm up your desoldering equipment, you need to separate the printed circuit board (PCB) from the rest of your device. Depending on the device you have a lot of techniques at your disposal. The only real concern you should have is about the destruction of the PCB itself. So long as it stays safe, so will all of its electrical components. While it is difficult to create a definitive list of tools to use, I can suggest a few that I use particularly often.
- screwdrivers
- pliers of all types
- wire cutters
- remodel/rotary tools
- tin snips
Combined, the above tools should be able to pry, cut and unscrew until the PCB is removed. Just remember to heed my prior warning and use the appropriate personal protective equipment. This is relatively self explanatory, and should go rather swiftly. As a side note, some of the components may actually be attached to the casing itself, and can be removed accordingly. And in the spirit of the Green Electronics contest, remember to recycle all of the plastic, steel, aluminum and screws you had to remove to extract your prize.
Step 4: Desoldering the Components
There are actually two approaches I will show. The first is with an ordinary soldering iron, and the second is with a hot air rework station or similar tool.
Step 4a:
The first approach to desoldering is with an ordinary soldering iron and a desoldering pump. And to proactively disregard one method I can foresee people might bring up, I would not advise that you use solder wick. It is good for more precise work, but if you want to desolder in bulk, it becomes irritating on many levels. Regardless, an ordinary soldering iron can deal with most through-hole components. With that dealt with, I can get started with a list of materials.
- soldering iron and associated tools (scrubber, stand, etc)
- desoldering pump
- PCB vise
- needle nose pliers
- tweezers (anti-static preferably)
- anti-static equipment if dealing with sensitive electronics
With those tools at the ready, we can begin with the actual process! For convenience sake, you can just watch my video below.
(insert video)
Step 4b:
The second option is to use a hot air gun. Just like the plain soldering iron and sucker, it can be used for most through-hole components. However, it can be particularly useful for the occasional tricky component as well as for actual surface mounted devices. But be wary that SMD components can be extremely small and tedious to work with, store, and eventually use. In other words, consider whether your time is best spent extracting hundreds of dirt cheap components, or if there is something else worth more to you. That being said, SMD components are a must for tiny electronics projects, and you can occasionally find some genuinely good ICs, such as PIC and AVR microprocessors. As with the above option, I will provide a list of essential materials as well as video showing the actual desoldering process.
- hot air rework station
- PCB vise
- needle nose pliers
- tweezers (anti-static preferably)
- anti-static equipment if dealing with sensitive electronics
(insert second video)
Step 5: Sorting, Testing, and Enjoying Your Loot
Though I could finish off with the last step, it is worth mentioning that it is good to get into the habit of organizing and testing parts. If your device was destined for the garbage can, you may have to worry about damaged components. Additionally, there are components such as electrolytic capacitors that can simply prove inoperable due to time. In either case, a quick test can prevent the woeful possibility that you use faulty components in your future projects. Tests vary, but in most cases a multimeter can do the job. In fact, some even have special transistor tester, such as in the first picture.
If a multimeter can't do the job, then a quick google search should be able to unearth some way to test any device in question. After testing the extracted components, it is then time to stow away your goodies for later use. This can pose a slight challenge as the extracted components are not necessarily any standard hobbyist model. Admittedly, I am currently between organization systems now and am currently storing most of my stuff in a single bin, though I intend to populate a set of miniature drawers at some point. Some of those parts and the drawer can be seen in the second image.
With your components finally tested and sorted (theoretically), you can now use them in any of your upcoming electronics projects. Whether you extracted a few resistors and buttons or a huge bin of parts like me, I hope this tutorial helped you in some way. Thank you for reading this far!
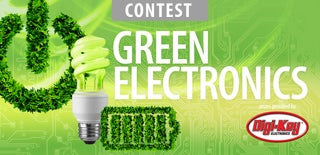
Participated in the
Green Electronics Contest 2016