Introduction: Scratch-built R/C Fanboat, Part 1: Construction.
Someone recently handed me a non-working weed trimmer and said, "You're welcome!"
Thanking him for his 'generosity', I proceeded to repair the stupid thing. About 2 hours later, I had a working weed trimmer, but no desire whatsoever to go out and trim weeds.
Having built a few model airplanes as a kid, I wasn't ignorant to the fact that a weed trimmer motor makes a great motor for air-powered craft, so I set out to see what I could do with this thing...
Thus begins the journey...and the headache...xD
I did end up learning quite a bit of how-to and how-not-to, so the experience has been well worth it. I hope you'll feel the same.
Step 1: Supplies & Materials...
Believe it or not, this boat's superstructure is composed entirely of cardboard...yeah...a box. Master model builders prefer lightweight woods, such as balsa for their framework, but I'm not a master model builder, and cardboard is cheap, easy to cut and shape, and available everywhere.
Anyway...here's what I used...your mileage may vary:
-BOAT HULL & FLAPS-
*LARGE cardboard box...the bigger the better...
*Super adhesive masking tape (the kind that will stick to AIR if you leave it long enough)...
*Fiberglass cloth....
*Glue (I prefer gorilla glue)...
*Epoxy resin...
*Bondo...
*High-build filler primer...
*Exterior paint.
-PROPULSION & MOUNTING-
*Gas weed trimmer engine & components...
*Lightweight perforated angle...
*5/8" aluminum flat stock...
*Small galvanized hinges and machine bolts w/nuts...
*Wire hangers...
*Various bolts, nuts and hardware...
*Propeller w/mounting hardware...
-Control-
*2-Channel radio kit (transmitter, receiver, servos & batteries)...
-Tools-
*Utility knife...
*Scissors...
*Dust mask...
*Safety glasses...
*Latex gloves...
*Heavy gloves...
*Dremel tool...
*screwdrivers, sockets & wrenches...
*Rubber bondo spatulas...
*Beer...
Step 2: Building the Rough Hull...
Since you're here on Instructables, I'm going to assume that you're already well-versed in taking things apart, so I'll skip the whole "how to strip down a weed trimmer" step...Let's just say that you're not going to throw anything away until your project is done, right?
Moving on...
I went to everyone's favorite Chinese retailer (WalMart) and bought the biggest box they carried, eyeballed the heck out of it (admittedly, I rarely used a tape measure for this particular project), and began cutting up my interior supports, using a framing square to keep the strips of an equal width.
I didn't really consult any plan on this...I just used a little common sense to figure out how much infrastructure I'd need to make my hull rigid once joined. I used extreme-surface masking tape to line up and join the interior girders to the bottom portion of the hull, and reenforced them with gorilla glue once everything was correctly aligned.
After the interior and bottom had a chance to set up, I used HVAC silicone to join the deck to the rest of the frame, and held it in place with more super-duper masking tape.
*LEARNING MOMENT*
Since this is my virgin build, I have learned a few things that will help me on the next one. Consider these little tidbits as you continue.
Eventually, a motor is going to me attached to this thing...a pretty heavy, high-torque one. If I ever build another one like this, I'll fill the entire rear half of the hull with expanding foam, so I can bolt through the entire hull, instead of settling for a surface mounted plate.
Step 3: The Fins, Rudders...whatever...
I probably could have saved some time and effort with my fins, but I decided that I wanted to aggravate myself even further by scratch-building the them as well (rather than doing the smart thing and cutting them from a piece of 1/4" lexan laying right under the table).
I cut out a shape on a piece of cardboard until it looked like what I thought a fanboat fin should look like, then used the prototype as a template for three more. I should say that the only measurement I considered here was in my own head...I figured that the fin should be around as tall as the boat is wide.
After gorilla gluing them together in pairs (being careful to "mirror" the bends in the cardboard, so as not to end up with curled fins), I taped them along their seams and prepared them for a fiberglass cloth and resin coating.
Did I mention aggravation? Now fiberglass cloth can be stretched and pulled to get it to lay where you want it. Problem is, I'm no fiberglass pro, and getting the cloth to stay flat and clean around these fins was a pain in the *ss...
However, I did manage to get it done, and taped one side tightly to keep the first side clean and ready for resin.
After applying the resin to one side and allowing it to dry, I just flipped it over, cleanly laid the other side and applied resin to it.
*LEARNING MOMENT*
Let me reiterate: This is my first time EVER doing fiberglass work. Now I know that I made it harder on myself by not pre-taping the seams with fiberglass. In this build, you'll notice that I laid entire faces with cloth and worked the cloth over and around corners and seams. Had I known the right way to do it, I would have saved myself a lot of time and effort...
By "taping" the seams, I mean applying thin strips (about 2") to the corners and seams of your project, applying resin, drying, and then applying your cloth to the faces, overlapping the tape edges.
So now you know...save time, effort and beer...pre-tape...xD
Step 4: Body Work...
Now that my fins were out of the way, it was time for the "easy" part...fiberglassing the hull. The flat faces of the hull did make for a lot less frustrating laying, even though I didn't yet know about pre-taping the seams (see learning moment-step 3).
After a good cure overnight, it's time to smooth everything out with some mild bondo, to even up the surface and prepare for the paint job.
Bondo can be mixed either "mild" or "hot" by varying the amount of hardening cream. Hot bondo hardens faster and sets stiffer than mild bondo. I choose to coat the boat in a milder mixture so that it would retain some flexibility and avoid cracking under stress.
A 12" drywall knife sufficed to even out some of the high ridges in the boat hull. This is more important for the bottom, as ridges will add drag and impede performance, but I did the top too, so I'd have a better looking ship.
To make my sanding easier, I used an electric palm sander. It helped, but went a bit too far in some spots, which had to be redone with hot bondo and hand sanded again.
Adding the bondo to the hull also should provide some ballast, since the top will be saddled with a large, heavy engine and rigging. Bondo, however, is pretty heavy, so try not to add too much, so your boat doesn't become an anchor.
After your body work is done and dry, apply some primer and whatever paint scheme suits your fancy. Your base coat of primer will probably reveal imperfections that you should address along the way...mine sure did, and hot bondo came in handy again and again...xD
Step 5: Mounting the Motor...
Again, I have no math...just an eyeball idea of where stuff might need to be. I know that for a boat of this size, I want to have a pretty large prop to push the weight around, so I mounted my engine high enough to accept a 15" propeller (with about 1 1/2" of clearance between blade tip and hull when mounted).
I used lightweight perforated angle stock to bolt the engine to a large piece of rigid PVC sheeting I cut from an old tank. Once the setup was to my liking, I gorilla glued and bolted the whole assembly to the boat deck just behind the mid point of the hull, being certain that the prop shaft would be centered and parallel with the boat once fixed.
Also, don't forget to leave room for your rear fin assembly.
I decided to make this a "pusher" rather than a "tractor", because it more closely resembles the real deal.
Step 6: Mounting the Fins...
The fin assemblies are probably the easiest part of this build so far...
I pulled the pins from some small galvanized hinges and glued and bolted them to the fins along the leading edge for attaching to the masts, and on the inside of each fin to mount the control linkages to.
Then I used the aluminum stock to form the booms and struts and a few lengths of clothes hanger wire to form the linkages.
Each mast is bolted and glued to the hull with self-tappers and gorilla glue, then sealed with clear silicone for more strength and water-tightness.
Adding a few struts here and there will help to ensure that the masts and fins stay put under stress. Just make certain that they won't interfere with the prop when mounted.
Step 7: Getting Ready for Running Gear...
Now it's time to decide how you want to start this thing. Some prefer the old method of pulling on the prop until the engine catches, some prefer to use a model plane starter. I decided to retool the pull starter and mount it to the rig so I don't have to do either.
I also tooled a bolt to tap into the square hole where the original drive shaft seated and added a couple of nuts and washers to mount the prop.
Plumbing the gas tank is easy...just get some fuel line and run to the tank wherever you decide it looks best.
I don't know whether I'm going to reinstall the muffler or not yet...it's a very loud runner without it, but weight is an issue, too. If I do end up muffling it again, I might just fabricate a better looking one from copper tubing...we'll see.
A little more paint touch up and she's ready for the next phase: running gear.
When the radio kit comes in, we'll conclude this project with part 2: "Installing a Remote Control System." I'll also be attaching a video of the maiden voyage somewhere in part 2...until then...
Hope you enjoyed this, my 7th 'ible, and learned from my mistakes as much as I did...I'm certainly looking forward to wrapping it up and getting out on the lake to see if it runs like I imagine it should...???
Don't forget -if you're interested- check out my personal website for handyman tips, rants and raves, etc...www.htwtusa.com.
Now go BUILD SOMETHING!
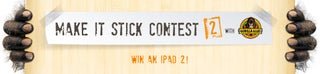
Participated in the
Make It Stick Contest 2