Introduction: Settlers of Catan Table Top Game Piece Tray
The table top game Settlers of Catan is one of my favorites and is consistently in the board game night rotation. I wanted to enhance my crew's gaming experience by creating some fun Catan accessories. I decided a piece tray would be the perfect place to start.
Inches will be used for measurements in this instructable and represented by the shorthand symbol of double quotes (").
Supplies
- CNC Router
- CAD/CAM Software (I used Fusion 360)
- 8" x 5" X 0.5" Lumber (or other material)
- Small diameter end mill. (I used 0.157")
- Sand Paper
- Any Wood Finish / Stain (optional)
- Settlers of Catan Board Game
Step 1: Design the Tray
For this Catan piece tray, I am using only the pieces found in the original game (no game expansion pieces). In addition to the main playable pieces, I decided to include a spot for the game's rules reference card that each player uses during the game. Next it was time to determine how to layout the items on a tray.
I grabbed a sheet of white paper and started by cutting a rectangle about the size needed to hold 2 reference cards with a 1/4" border around the outside (6 3/4" x 4 1/2").
I moved the pieces around until I liked the look of the layout. This confirmed that the 6 3/4" x 4 1/2" tray size would work well to hold all the various size items.
Step 2: Measure the Pieces
Having decided on the basic layout of the tray, the next task was to count the pieces and determine what size pocket would be needed to hold each type. Digital calipers help make determining the sizes super simple. But a ruler / tape measure would work at this step as well.
The pieces we need to account for are:
- 4 Cities (0.377" x 0.75")
- 5 Settlements (0.377" x 0.55")
- 15 Roads (0.185" x 1")
- 1 Reference Card (3.25" x 4")
These are general averages found while measuring multiple pieces. There was variance of about 2-3 hundredths of an inch. This will be accounted for when building the 3D model and generating the CNC machine g-code.
Step 3: Build the 3D Model
I used Fusion 360 for the CAD step. However, the model itself does not contain complex geometry and should be possible to build using any CAD software. If you want to try Fusion 360, the personal use version is currently free for 1 year.
The bit I used to make the cut is about a 0.16" diameter end mill. With that size bit, the corners of each pocket would be too tight if we create the model to exact size. To account for this, each pocket will be oversized by 0.05" on the vertical measurement. This will give enough wiggle room to ensure the pieces fit without being too loose.
The first step toward building the model is creating a sketch that contains the basic layout of the various pockets needed to store our game pieces. Next, the sketch is converted into a 3D model. The video below shows the full process.
Here is a description of the steps taken to create the model:
- Create a new sketch on the XY plane
- Draw a 6.75" x 4.55" rectangle
- Add a 0.25" radius to the corners using the Fillet Tool
- Draw a 3.3" x 4.05" rectangle spaced 0.25" from the left side, top and bottom.
- Use construction lines to help position the other pockets relative to the right side of this initial box.
- Draw a 0.377" x 0.83" rectangle against the left or right edge of construction lines. Using the Rectangle Pattern Tool evenly space 4 rectangles to fill space.
- Repeat step 6 for the other piece sizes.
- Use the Extrude Tool to convert the 2D sketch into a 3D model. I extruded each city and settlement pocket by 0.4", the reference card and roads by 0.45" and the main body by 0.5". (TIP: Once you extrude one part of your sketch, the sketch will be hidden by Fusion 360. Click the eye icon to show the sketch again and keep extruding).
Attached are the model's STEP file and the sketch's DXF file on this step for anyone that wants to jump ahead to the manufacturing step. I have also included a STL file for 3D printing, however, I do not have a 3D printer and cannot test how well that works. (Let me know if you try it!)
Full Video Creating the Sketch
Step 4: Generate the Toolpaths
The process of generating the machine code to run on your CNC is pretty straightforward and Fusion 360 typically does a good job of providing workable settings by default. I chose 3 different cutting operations that will be executed in sequence without any tool changes.
- 2D Adaptive Clearing - Used for pockets created to hold the player rules reference card, settlements and cities.
- 2D Pocket - Used to cut the pockets for roads. They are too skinny to process using Adaptive Clearing.
- 2D Contour - Used to cut out the final exterior shape of the tray.
The process of generating toolpaths can be very dependent on the machine you will use to cut out the model. The CNC I use is small and does not have a lot of cutting power. For this reason, I need to enable the Passes > Multiple Depths setting. This ensures that the machine does not attempt to cut the entire pocket in one operation.
The toolpaths generated will then need to be converted into a format that the CNC can understand. This step is known as a post processor. Fusion 360 has post processors available for many common CNC models in their Post Library for Autodesk Fusion 360.
TIP: It is a good idea to only generate the toolpaths for one of each pocket type and run that program on a test board. It's better to find out early if any of the pockets are a little too small. There can be some variation in fit depending on material and cutting bit used. You can also use this test run to verify your post processor.
Video example of generating toolpaths:
Step 5: Run the CNC
Load the generated G-Code file into your CNC's control software. Each machine will have its own specific interface. You will need to consult any related documentation for your machine if you encounter issues at this step. Remember to follow the safety procedures outlined for your CNC.
Here is a video of my small CNC engraving machine working its hardest!
Step 6: Verify the Pieces Fit
Now that the cutting is complete, it is time to test fit your pieces. I created multiple trays using cherry and maple wood. The game pieces fit much tighter on cherry than on maple. If I create more cherry boards I plan to use the Stock to Leave option when building toolpaths to cut over the model lines by a set amount. In this case, I might over cut it by an additional 0.005".
If you find that any piece doesn't quite fit, you can use the same setting to adjust the cut or you can modify the model itself and generate new toolpaths. Since the reference cards are varied in final size, if any card is still too big after modifying the model you could hit the side of it with some sand paper to slim it to fit.
Step 7: Sand & Finish
With the cutting operation complete it is time to clean up any marks left by the tool and get the wood ready to receive finish. Work your way up through the grits from most course to most fine. I used grits 150 & 220.
I used an aerosol spray polyurethane as a finish. The small pocket size made a spray finish a good option. A wipe on oil finish would also work well for this item. You can use any type of finish or stain/dye at this step. Follow the instructions provided on whatever finish product you pick.
Step 8: Game On!
Now it's time to show off your new Settlers of Catan piece holders!
Impress your friends; Awe your co-workers; Amaze your family!
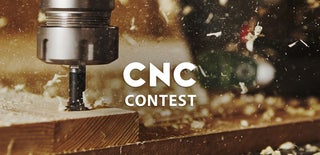
Runner Up in the
CNC Contest 2020