Introduction: Shoji Lamp (3D Printed)
Sometime ago I made a Shoji Lamp with Kumiko panels (check out the last three images in this step), this one off lamp was fully 3D printed using two types of wood filament (coconut and olive), plus PETG and PLA filaments. While it looked amazing the assembly process was a pain so a redesign was in order as I wanted one to myself, albeit a simpler looking one.
So what is a Shoji Lamp? Well, wikipedia explains it better than I will ever be able to "In traditional Japanese architecture, a shōji is a door, window or room divider consisting of translucent paper over a frame of wood which holds together a lattice of wood or bamboo. While washi is the traditional paper, shōji may be made of paper made by modern manufacturing processes; plastic is also in use." (https://en.wikipedia.org/wiki/Sh%C5%8Dji)
Traditionally a Shoji lamp is composed of a wooden frame and rice paper shade panels. They instantly add a traditional Japanese look to your interior and set an atmosphere in the room. They provide a soft and non-aggressive light for the most relaxing ambiance. Floor lamp, table lamp or even hanging lamp, they come in various shapes and sizes and you will find a lot of different designs (https://japanesebeds.org/how-to-pick-a-japanese-shoji-lamp/)
So lets start this project modelling the lamp and gathering the required supplies.
Disclaimer: The stl's for building this lamp are now available at: https://cults3d.com/en/3d-model/home/shoji-lamp for a reasonable price, so if you wish to build it head over there and help support the work that went into developing this model.
Step 1: Modelling
I won't be making a detailed tutorial on the modelling phase, there are plenty of other people much better than me at this and I'm certain you can learn much more with them. I'm using Fusion 360 for modelling and if you are interested in learning more check out Desktop Makes youtube channel at https://www.youtube.com/channel/UCxgunnLdsV72eAez... and Lars Christensen at https://www.youtube.com/channel/UCxgunnLdsV72eAez...
All of the structural parts, that in a traditional lamp would be made out of wood are assembled with M3 screws and M3 Brass Inserts, all of the side/top panels fit onto channels were they should fit snugly with no margin for rattling.
All of the panels and respective channels have tight tolerances, so ensure your printer is well calibrated before attempting to print this design, especially if you have "elephant's foot" in your prints, if that's the case checkout this guide for help dealing with this issue https://support.3dverkstan.se/article/23-a-visual-ultimaker-troubleshooting-guide#elephanthttps://support.3dverkstan.se/article/23-a-visual-ultimaker-troubleshooting-guide#elephant, otherwise the channels will be too tight for the panels to fit correctly.
Step 2: Base, Cover and Lamp Holder.
The bottom cover is bit over-enginered but I wanted to ensure that there would be no sagging, so I added a center cross rib, several chamfers and corresponding channels on the bottom piece to perfectly fit the cover. Adding to this I also wanted to ensure that the design did no require any supports therefore the weird shape on the supports that will receive the cover and the screws that will keep these parts together.
On the bottom cover there also a the holes, the bigger one, will receive the lamp cable and has chamfers to ensure that there are no sharp edges that could cut it. The two small one are meant to be used as a strain relief by feeding a nylon cable tie through them and stopping the cable from moving.
The center support for the the lamp holder is the only part in this whole design were screws are directly used in a plastic parts, simply because I forgot about it and while I could modify the design to accomodate brass inserts there's no need for them if you add the cable tie as a strain relief.
Step 3: Top and Side Panels
In order to ensure that design was printable on the standard 200x200mm reprap printer bed, I was forced to be creative with the assembly of the top part of the lamp. These parts fit one on to the other using slots through with a screw will pass, ensuring they dont separate and that they are firmly fixed on to the rest of the design.
The side panels are a single piece and should be printed in transparent/translucid filament, like natural PLA or PETG, or you can do as I did and used white PLA Filament. For the design on the surface of the panel I used black filament. To achieve this print correctly you will need to replace the panel filament of your choice at the 0.8mm height with a darker filament, (tip use the M600 gcode to trigger a filament swap at the heigh you require).
Step 4: STL's
The stl's for this project can be obtained over at: https://cults3d.com/en/3d-model/home/shoji-lamp
You will need to print
- 4 x Pilars
- 4 x SidePanel
- 1 x Ceiling1
- 1 x Ceiling2
- 1 x Ceiling3
- 1 x Ceiling4
- 1 x Top
- 1 x TopLight
- 1 x Base
- 1 x Bottom Cover V2 (if you downloaded this part before 14/01/2019 00:45 UTC, please download and use this new version as it allows for better/simpler printing without supports)
All of the parts were printed in PLA at 200ºC, 20% infill, 0.3 layer height.
Step 5: Materials
Required hardware:
- G9 Lamp Holder
- G9 Light bulb
- I used some cool looking retro one I found on a local hardware store, but you can use any G9 bulb you want just ensure that is a Led one, otherwire it might emit too much heat, and if you are using PLA plastic it might melt your printed pieces
- https://www.xanlite-store.com/en/our-batch-offers/...
- Threaded M3 brass inserts
- M3 Screws
- I used M3 slotted pan head 12mm screws because I had them readily available, but If didn't I would buy M3 phillips head 12mm ones
- Terminal blocks
- Power cable with a switch
- Nylon cable tie
Step 6: Brass Inserts
First you need to insert the brass inserts on the correct holes, to place these I use a soldering iron heated to 210ºc, I placed them on top of the hole and them place the soldering iron tip on top of them, as soon as they start "diving" be careful as it's really easy for them to tilt.
You will need four inserts for the base, these will later receive the screws that will hold the bottom cover and lamp holder
Check this tutorial for more detailed instructions:
Step 7: Bottom Cover
Slide the power cable through the bigger hole on the side, then pass a nylon cable tie through the smaller holes and tighten the cable to the cover.
Screw the power cable and the G9 lamp holder to the terminal block.
Using two M3 screws screw the lamp holder to the holes on the bottom cover, these screw directly to the plastic
I used a small piece of kaption tape to stop the terminal block from moving around, but any type of electric tape will also work.
Step 8: Bottom Part
Place the bottom cover in the correct slots in the base and using 4 M3 screws fix both pieces together.
Step 9: Light Bulb
Grab your G9 light bulb and insert it on to the holder. Now it's a goo time to test if it's working correctly.
Step 10: Pillars
The pillars are the next part to receive the brass inserts. Both sides require them, so you will need 8 for this step. Insert them as per the previous tutorial.
Afterwards start adding the pillars to the bottom part, by placing M3 scews in the base legs and screwing the pillars to it. Ensure that they correctly aligned, the cut out portion should face the interior, and the channels on the base should be visible.
Step 11: Side Panels
Slide the side panels on to the channels, the side panels have chamfers along the edges to ensure they correctly mate to eachother.
In the end all panels should just barely peek through the top of the pillars.
Step 12: Top
For the top piece, you will need 4 brass inserts, these go to the inner most holes.
Afterwards insert the TopLight part onto the channel made for it, this should be just a press fit, but if required you can glue it to the top part.
Finally place the top part on top of the previously assembled pieces, if the side panels have been correctly placed they will slide on to the correct channels on the top part and you can then screw these two pieces together using M3 screws placed inside the outer most holes.
Step 13: Ceiling
The final piece is composed of four different pieces that fit on to one-another using slots. Also because there's a slight taper on these pieces ensure they are correctly placed by checking if the flow smoothly from piece to piece.
Step 14: Final Piece
Finally you can screw the ceiling part on to the previous assembly, simply slide M3 screws on the four holes and screw them to brass inserts on the previous piece.
That's it the lamp is done.
Step 15: Enjoy
Our shoji lamp is done,the final build size is around 190mm x190mm x 300mm and should fit nicely on a bedside table. Now the only thing left is to enjoy the fruits of your labor an turn it on.
I hope you enjoy making this lamp as much I did, don't forget to share your builds.
Step 16: Extra Panels
I've created some additional side panels, so if you something a bit more custom, you can use these extra panels to create your very own personal shoji lamp. I also added a blank panel if anyone wants to further customize their personal design or if you just want an even cleaner look.
Step 17: E27 E14 Modification
If you would rather use a E14/E27 bulb in your build, I modified my original model to fit the lowest profile holders I could find.
You will need to print the modified BottomCoverE14E27 and optionally an M10 thread bolt.
After much searching I came to the conclusion that it doesn't seem to exist a standard for lamp holders. The large majority of those that I found didn't show the dimensions and screw sizes, adding to that the ones that I could find in local stores seemed to be different from most that I could find online. Eventually I found these ceramic holders, that seem to be used in chandeliers, both of them (E14 and E27) have a center bracket with a M10 thread on them, so this seemed the best bet.
To attach the holder you will need a M10 bolt, as these are not that common and a bit expensive, I modified a bolt from this project https://www.thingiverse.com/thing:126141 to the correct height required to attach the holder to the bottom cover, M10x12. Please print this with at least 50% infill, ideally 70%.
If you order the M10 screws mentioned below, you will probably need to cut them or add washers to the E14 holder, otherwise the screw might touch the leads and make a short-circuit, BE CAREFULL.
Also don't forget to use LED lightbulbs to keep the heat to a minimum.
Disclaimer: I haven't printed this modification and while I believe that it should work properly, you might need do modify it slightly to make it work.
Holders:
- https://www.aliexpress.com/item/E14-E27-high-tempe...
- https://www.aliexpress.com/item/E14-white-plastic-...
M10 Screw:
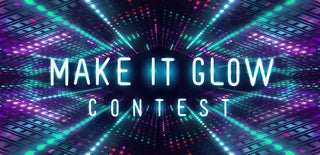
Runner Up in the
Make it Glow Contest 2018