Introduction: Speaker With Subwoofer From Broken Old Computer Speakers
I doubt I'm the only one who does this: every now and then, I go online and search for broken electronics for sale – stuff that I can fix and use or take apart and salvage its parts. This was the case a couple of months ago when I came across a set of used JBL Creature 2 computer speakers priced at $25. They didn't work, according to the seller, but I decided to buy them anyway.
The speakers were old indeed. This particular model came out in 2005: when mp3 players were all the rage and Mariah Carey topped the charts with "We Belong Together". But they were made by JBL – a premium brand – so trying to fix them seemed worth the effort. Besides, how hard could it be to repair something as simple as a set of computer speakers?
And so, the speakers arrived, and I didn't just fix them. I turned them into a tabletop speaker unit that looks great and sounds even better. Let me show you how this project came together.
Step 1: Introducing the Donor: JBL Creature 2
This is the JBL Creature 2 speaker set that I bought. It is a 2.1 system, which means that there are two smaller speakers reproducing the mids and the high frequencies, while one subwoofer – shaped like Darth Vader's helmet – pumps out the bass. The dials on the sub are for adjusting bass and treble levels. Volume is controlled with touch-sensitive buttons placed on one of the satellite speakers. The system is rated for up to 40 watts of output – more than enough for a typical living room. As with most computer speakers, inside the housing of the subwoofer is contained an amplifier – an electric circuit that takes the weak audio signal from your computer or music player and amplifies it to a level capable of driving the speakers. And that brick-shaped device is the power supply for the system.
Step 2: Testing What Works and What Doesn't
Clearly, whoever owned these speakers before me didn't care much about them. They had stains and scratches all over, and the dents on the edges suggested that someone may have tried to pry them open at some point. There was a worrying crack on the plastic body of the power brick, probably caused by a drop on the floor. The membranes of the small speakers looked like someone had poked them with a pencil – and that was damage I probably couldn't fix.
Were these speakers repairable in the state they were in? Had I bitten off more than I could chew?
To find out, I first tested the power brick with my multimeter. It was rated for 18V AC on the output, according to the label, so I set my meter to AC, then carefully touched the black lead to the outer terminal of the barrel jack and the red lead to the inner terminal. The voltage was 20V AC, according to my meter – slightly higher, but that was normal since the transformer wasn't connected to any load. If you ever decide to buy and/or repurpose old computer speakers, my advice is to make sure that their power adapter works, as finding the right replacement could be costly.
Having confirmed that my power brick was working properly, I connected it to the subwoofer and pressed the power button. LEDs on the sub and the satellites lit up: another good sign! This meant that the system was powering up properly.
Unfortunately, when I connected my phone to the speakers to test them, there was absolutely no sound. Only the sub made a faint "pop" when I turned the system on or off. This meant that the amp was probably working fine, but the signal wasn't reaching it. To confirm my theory, I had to take the speakers apart.
Step 3: Taking the Speakers Apart
This JBL Creature 2 teardown went down pretty smoothly. All that I needed to take all speakers apart was a Phillips screwdriver and a pair of needle-nose pliers.
I started by unscrewing the 8 screws from the bottom of the subwoofer. Then I pulled out the caps for the bass and treble controls with moderate force. Next, I used the pliers to unscrew the nuts holding the bass and treble potentiometers in place. Then I lifted the top of the subwoofer with ease, exposing the main circuit board. I found it cool that JBL used the heatsink for the amplifier chip as part of the bass reflex vent!
The small speakers were even easier to take apart. They were held together only by four screws at the bottom. Inside the left one was a simple board with what seemed to be a high-pass audio filter (a single electrolytic capacitor) which let through only frequencies that the driver was made to reproduce. But inside the right satellite, I found more circuitry that appeared to handle the touch-operated volume control.
Step 4: Finding Out What's Broken
The first thing I check when fixing something electrical is whether the power source is functioning properly. But since I already knew that the power brick was okay, I moved on to the next step: a visual inspection.
You don't have to be an expert to spot a faulty component on a circuit board. When a resistor, a transistor, or a diode burns out, they usually leave a brown burn mark on the board around them. When an electrolytic capacitor fails, it usually pops from the top or the bottom, releasing nasty fumes or brownish goo. Nothing on any of the boards seemed out of order.
Then I took a cable I had made (picture #1 above) – with a 3.5mm jack on one end and exposed wires for ground and the right channel signal on the other end. The 3.5mm jack I plugged into my phone and played some music. The bare wires I touched to the main circuit board at the inputs at the back (pictures #2 and #3 above), ensuring that my ground and signal wires weren't switched around. And all of a sudden, the speakers came to life! Well, kinda.
It looked like a faulty input cable – the one with 3.5mm jacks on both ends that connects a computer or a music player to the input port at the back of the subwoofer – was the reason for the entire speaker system not working. I got lucky because a new cable costs only about $2.
But there was another problem: the left satellite speaker was crackling when music was trying to play through it. Upon taking a closer look, I noticed that the magnet of the driver had come loose – picture #4 shows the speaker with the broken magnet on the left. This was probably the reason why the membrane was also torn. To me, this speaker was beyond repair.
Step 5: Coming Up With a Plan
Finding a new audio input cable was an easy job, but repairing the broken satellite speaker driver and its torn membrane was beyond my skill level. However, after some digging on the internet, I found out that this particular JBL driver has a tendency to fall apart. Therefore, replacing it with an identical component didn't seem like a good idea as it was bound to fail again anyway.
So instead, I decided to design a brand new tabletop speaker, with all three speaker drivers housed inside the same unit. It was going to use the amplifier board, subwoofer, volume and tone controls, and power supply from the Creature 2 system, but I wanted to replace JBL's failing satellite drivers with different, more reliable ones – the substitutes are pictured above and came out of a THX-certified Logitech audio system.
I have to make an important note: when replacing speaker drivers, you have to make sure that the replacement has the same or higher power rating, measured in watts (W). Drivers that can't handle the power the amplifier can deliver may fail if you turn up the volume too high. In my case, the small JBL speakers were rated at 8W, and the replacements could handle at least 12W. Another important spec to consider is impedance, measured in ohms (Ω). JBL's original drivers had an impedance of 4 ohms, but my replacements were 8-ohm speakers, and twice the impedance meant that at the same volume level, half as much power was going to go through them. Luckily, I tested them and they were just as loud as the originals, presumably because the much greater surface area allowed them to move more air. And they were also going to put less strain on the amplifier because they needed less power to get loud! #winwin
I laid down all of the components on the floor and tried to visualize a suitable enclosure in my head.
Step 6: Designing the New Speaker
Measurements are approximate and in centimeters.
When thinking about how to approach this project, I made a list of things to consider, including factors I couldn't change and features I had to include. These later served as guidelines around which I could more easily visualize what the final design would look like – and at the end, I was imagining a speaker that looked as in the drawing above. Here's what was on my list:
Speaker drivers and enclosures:
- My speaker had to be big enough to contain the 4.5-inch JBL subwoofer inside an enclosure of size as close to the original as possible. That's because loudspeakers perform best, especially when it comes to bass, when they're put inside an enclosure of an ideal size – and I was pretty sure that JBL had chosen the right one for its sub. So I measured the internal volume of the JBL subwoofer... by filling it with water! It turned out to be around 3 liters.
- The subwoofer needed to be inside of a ported/vented enclosure. This is also called a bass reflex design and it means that the box for the speaker has a hole with a pipe in it. The length and diameter of the pipe produce a boost in bass output around a specific frequency. Again, I was just going to copy JBL's design. The metal heatsink on the amplifier board already formed part of the bass reflex pipe, and I was going to add the missing length at a later time.
- I needed to place the two smaller, 3-inch speakers on the front. Since I didn't have any specs for those, I couldn't calculate an ideal enclosure size, so I decided to put them in a sealed enclosure (simply a box without a pipe). This wasn't optimal, but there wasn't much that could go wrong with such a design, especially since there was a high-pass filter limiting the amount of bass the speakers would produce.
Amplifier board:
- The amplifier board was fairly large – roughly 20 by 18 by 5 centimeters. It had to fit inside the subwoofer enclosure somehow, and its dimensions were going to determine the overall depth of my speaker.
Inputs, controls, miscellaneous features
- My speaker needed to include two touch-sensitive buttons for volume adjustment since that was how the speakers were originally designed and I didn't want to mess with the circuitry.
- I also needed a 3.5mm input jack for connecting an audio source. I wanted it to be on the back.
- Also at the back, I needed to include an input for the power supply.
- A power on/off button was required.
- The LED lights to show when the speaker was on had to be unobtrusive.
- Finally, I needed to include the original bass and treble controls.
Step 7: Making the Front Piece
Since the front piece needed to hold all three drivers, I chose to use the thickest (18mm), most solid piece of plywood that I had. I marked the required dimensions with a pencil. I also marked where the circular openings for the drivers needed to go. Then I cut the piece to size with a jigsaw.
To make the circular openings, I used my Dremel tool and a 2.8mm drill bit to drill holes around the perimeter that I needed. This is definitely NOT the best way to do this, but I didn't have access to any more precise tools at the time. If you have a CNC or a router, then do use that instead! Or if you have your own hole-cutting technique, that's also fine. What matters is that the holes are cut precisely – so that no air can escape between the driver and the plywood.
To clarify, my plan was to screw in the drivers from the front simply because their design allowed for a better seal this way. A few steps later, I'll show you how I added a nicer piece of wood in the front to make it look nicer.
Step 8: Gluing the Sides, Back, and Top Piece
I made the side, back, and top pieces out of plywood. Using thicker pieces makes for a more solid construction, and in general, a solid, heavy speaker sounds better than a small, puny one. Since the sides of my pieces were pretty thick, they were easy to glue in place at a right angle, but to be on the safe side, I also used my right-angle clamps. When gluing the top piece, I used as many clamps as I could to make sure that I had a good seal all around. All electronics were going to be inserted in place from the bottom.
Step 9: A Test Fit of the Amplifier Board
I wanted to secure the amplifier board to the top side of the speaker (which was now glued in place), so I cut two small pieces of wood, cut slits into them, and glued them to the inside of the speaker. The slits were as wide as the thickness of the board and about half a centimeter deep. This allowed me to simply slide the board in place, without having to screw it yet. On the opposite side, I glued a thin piece of plywood for support. I was going to screw in another piece on top of it at a later time so that it would hold the board in place.
Step 10: Making Walls for the Speaker Enclosures
After confirming that the amplifier board fits perfectly, it was time to make the individual enclosures for the speakers. Picture #3 above shows them clearly: there are two small, sealed enclosures for the small speakers, seen on the bottom right and bottom left. In the middle is the bigger enclosure for the subwoofer. The two smaller enclosures on the upper left and right are not used by any speaker. They're isolated so that I could achieve the desired volume for the sub's enclosure.
In case it isn't clear, the speaker looks like one single unit from the outside, but on the inside, every driver enclosure is separate – kinda like having three individual boxes inside a bigger box. This may seem like a small detail, but it is very important; you do NOT want to place multiple speaker drivers inside the same enclosure, unless they're the exact same drivers reproducing the exact same signal. Basically, you do NOT want different drivers to "interact" with each other by moving inside the same enclosure. That's why every dividing wall between enclosures needs to be glued well in place, with a hermetical seal around the edges.
Note that I added thin pieces of plywood around the perimeter of the enclosures for the small drivers. This was to get a better seal at the end when the bottom piece is inserted. I was going to add more thin plywood pieces around the whole perimeter at a later time.
Step 11: Completing the Bass Reflex Port for the Subwoofer
As I mentioned earlier, I wanted to place the subwoofer inside a ported enclosure identical to that of the original design. Getting the correct volume of 3 liters was the easy part. Getting the correct bass reflex port was kind of tricky.
That metal piece you see on the amplifier board is the heatsink for the amplifier (picture #7). Its purpose is to dissipate the heat generated by the amplifier as it does its thing, and without it, the amplifier chip would either refuse to start or burn out from its own heat.
As I also mentioned in a previous step, that flared, horn-shaped thing on the heatsink is part of the bass reflex port. The remaining length was part of the original subwoofer's plastic enclosure, so I couldn't use it. That's why I made the missing piece myself. I glued multiple pieces of plywood on top of each other and then drilled the missing port length with my Dremel tool. I used a special bit – Dremel's 5/16" high-speed cutter, model #115 – to shape the piece. It was tedious work, honestly, but I couldn't come up with any better solutions at the time. The result may look rough in the photos, but I made the ends and inside part smoother with a little sanding and grinding.
As you can see in pictures #4, #5, and #6, the wooden piece fits the bass reflex port well. I glued it to the back of the speaker, then drilled a hole from the outside, widened it with my Dremel tool, and sanded the edges to make a flared opening.
Step 12: Modifying the Input/output Board, Filter and Tone Control Boards
In JBL's original design, the power button, power LED, power input, 3.5mm input audio jack, and output jacks for the left and right speakers were all placed on a small, separate board, with two ribbon cables connecting it to the main board. Unfortunately, I couldn't use the small board as it was because my box design couldn't allow good access to the inputs and outputs. That's why I had to perform some modifications.
I desoldered the power button, LED, power input, and all audio jacks from the board. My solder removal copper braid came in handy for the task.
My plan was to have all of these mounted on the back of my speaker. Except for the jacks for the left and right satellite speaker –these connections were going to be made inside the enclosure.
Next, I modified the small boards that I found inside the small satellite speakers (back in Step 3). These boards contain high-pass audio filters. One of them also had the touch-sensitive volume controls. I didn't mess with any of the electronics. I simply moved the signal input wires on the other side of the board so that it could be mounted inside the speaker more easily. I also replaced the output wires with longer, thicker ones.
I also had to modify the small boards that held the potentiometers for the tone controls (which turned out to be rotary encoders, not pots). Again, I simply moved the connecting cables to the other side of the boards to make them suitable for mounting on the back, next to the touch-sensitive volume buttons. Picture #7 shows these boards after the modification.
Step 13: Preparing the Inputs, Power Button, Power LED, Volume Buttons
In picture #1, from left to right: audio input, power LED, power input, power button.
Since the original power button got damaged during the desoldering process, I bought a new one that was bigger and easier to mount on panels. I soldered two thin pieces of wire to it. Why didn't I use something thicker? Because after studying JBL's circuit, I realized that the voltage from the power supply doesn't actually run through the switch. Its job was simply to tell the amplifier chip to go from standby mode to powered state.
For the power input, however, I used two thick wires that I salvaged from an old computer power supply. They were more than capable of handling the current.
The power LED I wired up with two thin wires. It didn't require anything more sophisticated than this.
As for the audio input, I cut a piece from the cable of the right satellite speaker. It was ideal for the purpose. Inside the cable were three wires: two for the left and right audio channels and one for the common ground and shielding.
The volume buttons were tricky to make. Since JBL's circuit involved touch-sensitive buttons, they had to be made of metal. After quite some pondering, I simply picked up two buttons from our sewing supplies. Yes, those two you see in picture #2 are actually buttons that go on clothes! There's lots of improvisation in DIY.
Step 14: Mounting the Inputs and Outputs Onto Plywood Panels
I decided to mount all inputs and outputs on two pieces of plywood. I was later going to glue these plywood panels to the back of my speaker, behind the hollow enclosures that weren't used by any driver.
I used 3mm plywood for the purpose. It was super easy to work with, and I easily cut two pieces about the size of credit cards with my hand saw. I rounded the corners to make them look better.
Using a small drill and a sharp chisel, I made cutouts for the power button, power LED, Power input and audio input on one of the plywood pieces. I placed the thin piece on a scrap piece of thicker plywood while making the cutouts to minimize chipping. Next, I glued the power LED, power input and audio input jack in place with 2-component glue. I placed an additional piece of wood in between the power input and audio jack so that the glue had more surface to stick to. Note that I didn't put the power switch at this point.
The volume and tone controls were going to go on the other piece of thin plywood. I only glued the volume buttons for now. The bass and treble controls would be simply screwed in place at a later time.
On the back of my speaker I cut openings where the two plywood panels would later go. These openings were cut just wide enough for the wires to go through. I wanted to have enough surface around the openings so that the plywood would stick well to the back.
Step 15: Mounting the Filter and Input Boards
I needed to find suitable locations for the other circuit boards inside the enclosure of the sub. The small filter boards – the ones I took out of the satellite speakers – already had mounting holes in them, so I simply used short wood screws to mount them on the side of the box. I also drilled small holes through which I could run the wires for the smaller left and right speakers.
The input board also had a couple of mounting holes, but several tall components were sticking out. To secure the board to the back of the enclosure, I first glued a thin piece of plywood to act as a riser (picture #5). Then I drove a couple of short wood screws through the holes. No wires were soldered to the input board yet. I was planning to do this last, once all the woodworking jobs were done.
Step 16: Making Recesses for the Speaker Drivers
This wasn't something I planned on doing, but I had to. When I placed the drivers inside the openings at the front, they were sticking out a bit too much. This was a problem as the piece of wood that was supposed to cover them (will be shown in a bit) wasn't going to fit.
The solution was to cut recesses for the speaker drivers. First, I marked the area covered by every driver with a pencil. I had to hold the pencil vertically for this step to get accurate markings. Then I used a routing attachment for my Dremel tool and made several passes until the recesses were done. The speaker drivers were now laying flush with the front piece.
Step 17: Making a Fancy Cover Piece for the Front
To make the speaker look good, I wanted to make a cover of sorts for the front so that I could hide the plywood and the uglier bits of the speakers.
I started by laminating two pieces of American white oak wood. They were 6mm thick and measured 10 by 45 centimeters. I bought the pieces several months ago on Etsy from a store called AlwaysHobbies and I was happy that I was finally going to use them in a project.
Once the glue was dry, I cut the oak piece to size and sanded down its faces to eliminate the marking left by the glue up. Then I made openings for the speaker drivers using the same technique I described earlier. I spent a lot of time sanding the edges of the openings to make them smooth and uniform.
Since the screws for the small speakers were still sticking out somewhat, I decided to carve small indents on the back side of the oak piece. To know where I had to carve, I dropped a small drop of nail polish on the tip of each screw, then pressed the piece against them so that the polish would leave a mark. It worked perfectly!
Finally, I took the piece out and gave it a nice coat of spray lacquer. If the grain raises, give the piece 24-48 hours to dry completely, sand it lightly, and apply another coat of lacquer.
Step 18: Gluing Fancy Wood Pieces to the Top and Sides
For the top and sides of my speaker, I chose to use mahogany wood panels. They were darker in color, which I expected to create a nice contrast with the lighter oak piece in front. The mahogany wood panels were also bought online from AlwaysHobbies. I cut them to size and glued them flush with the top and front of my speaker. These two wood panels were the most expensive component of the entire build, but they looked so much better than bare plywood!
Step 19: Applying Finish to the Top, Sides, and Back; Gluing the Input Panels
Once the top and side pieces were glued in place, I sanded them finely and thoroughly, then rounded the edges for a nicer look and feel. Using a few damp paper towels, I wiped all the fine wood dust that had accumulated on their surface. This makes the finish look better.
Before applying the lacquer, however, I glued the two panels with the buttons and inputs to the back. I wasn't too worried about getting a bit of spray lacquer over them, though I did put a paper towel in the bass reflex port so that nothing would go in. I also covered the openings for the speakers in the front with paper.
Next, I gently applied multiple coats of spray lacquer to the top and sides. I applied just two light coats to the back. Picture #2 and #3 show the speaker before and after the application of finish.
Step 20: Completing the Wiring
Time to bring out the soldering iron again. With nearly all wood pieces in place, I now had to complete all the wiring before sealing the speaker. First, I drilled the necessary holes for the wires to pass through. I wish I had planned ahead, as drilling these holes with my tiny drill was a long and tedious task.
With the holes drilled, I hooked up the speakers, input wires and power cables to the correct boards. I used 2-component adhesive to hermetically seal the holes again so that no air would pass through. For the tone controls, I used JBL's original caps.
Step 21: Putting the Bottom Cover
There was nothing fancy about the bottom that I made. It was simply a piece of plywood cut exactly to size. Note that the inner support pieces are recessed by 1 centimeter relative to the outer walls – exactly the thickness of the bottom piece. I drilled pilot holes in the four corners of the bottom piece and then secured it in place with screws.
Step 22: Complete!
And that's how this project came together! It was long, tiring, and cost me several sleepless nights as I was trying to catch the deadline for Instructables' Audio Contest, but I think the effort was worth it. If I had more time, I would have probably applied a few more coats of finish, but the speaker does look good even as it is. I may also open it back up and fine-tune the sound using some acoustic dampening material to reduce some of the boominess. But overall, I'm pretty happy with how the speaker turned out, and I hope that you learned something new!
If you liked this project or if you think that I could have executed something better, I'd appreciate it if you let me know in the comments!
Also, feel free to follow me on social media and to subscribe to my YouTube channel:
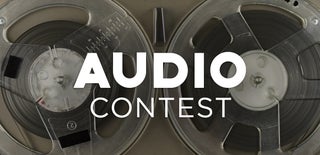
Runner Up in the
Audio Contest 2018