Introduction: Subsonic F-22 Raptor: RC Plane DIY
The Lockheed Martin F-22 Raptor is a fifth-generation, single-seat, twin-engine, all-weather stealth tactical fighter aircraft developed for the United States Air Force (USAF). The aircraft was designed primarily as an air superiority fighter, but also has ground attack, electronic warfare, and signal intelligence capabilities. The Raptor's combination of stealth, aerodynamic performance, and situational awareness gives the aircraft unprecedented air combat capabilities. It is the first operational aircraft to combine supercruise, supermaneuverability, stealth, and sensor fusion in a single weapons platform. The USAF considers the F-22 critical to its tactical air power, and says that the aircraft is unmatched by any known or projected fighter.
Our team consists of aero-modelling enthusiasts currently enrolled in an undergraduate degree in Aerospace Engineering. In our first year we had made a few Trainer RC Airplanes, but due to poor piloting skills, had experienced a number of nose-down crashes, breaking quite a few propellers and even a motor.
This summer, we sat and jotted down a few design considerations for a new RC plane:
--Vital electronic components must be in the rear part of the plane which effectively makes it a pusher type.
--The aircraft must be stable yet agile for basic flying and practicing aerobatic maneuvers (we had a good pilot among other bad ones). Thus it should be designed for neutral stability with zero camber flat-plate airfoil. Basically a flat plate for a wing.
--The aircraft must be able to fly at low speeds hence the large wing area.
--Large control surfaces with aileron mixing offer good pitch and roll authority. This comes with a reduction in the number of control surfaces and required servos.
--An 8 inch propeller with 1200 KV Brushless DC Motor (what we had at the time) will provide the propulsion for the aircraft.
--Foam board or corrugated plastic sheets can be used to make the plane. We built our previous planes using balsa wood which took a lot of time to build and were difficult to repair when crashed. Coroplast would be a better build material as it was easier to cut and paste together and gave good strength perpendicular to the braided direction.
The design considerations suggested a preliminary design that came out to look a lot like the F-22 Raptor, so we decided to build a similar one and performed a few simulations on it with ANSYS. Because, Why Not?
Step 1: Simulations
Being aerospace engineering students, we thought of simulating and refining our model. Note that a good RC plane can be made following simple thumb rules which may be found on any good sites like flitetest.com, etc. Also keep in mind that these simulations are only for our own gratification.
A model was built in Solidworks, the blueprint for which is given in the images above.
The CFD flow analysis for this model was performed using Fluent solver code of ANSYS software. All the simulations were performed using K-ε turbulence model with a free stream velocity of 15m/s. The flow visualization of streamlines and pressure gradients was obtained for specific cases where they may be noteworthy of interest.
The following quantities were determined computationally:
Lift, Drag, Pitching Moment, Movement of center of pressure, and Flow visualization for different angles of attack and different deflections of control surfaces. Control surface stalls and full plane stalls were also visualized.
Following inferences were made from the simulations:
--As the angle of attack of the plane increases, the center of pressure moves backward which has a pitch stabilization effect, since a negative pitching moment is produced about the center of mass which tends to bring the plane back to neutral position. This would prevent the plane from flipping under high aerodynamic loads.
--The weight of the plane was estimated to be around 500 grams. The plane should undergo level flight at less than 5 degree angle of attack.
--At 0 degree angle of attack, the Lift to Drag ratio is around 11.34 and at 5 degree angle of attack it is 3.587. Since the cruise angle of attack is between 0 and 5 degree, the L/D ratio should be between 11.34 and 3.587. This range allows for very less unpowered gliding but since the aircraft was not intended to function as a glider, this is satisfactory.
--There seems to be maximum shear at leading edges and maximum bending moments at the wings and control surfaces and their joints with the fuselage. Hence they must be made strong enough to withstand the aerodynamic stresses. The braiding of the corrugated plastic should be placed perpendicular to the maximum bending direction. If that is not possible, thin carbon rods/cycle spokes can be inserted to provide stiffness.
--The control surfaces have a tendency of stalling at moderate angles of attack of the plane but since the aircraft has a tendency to auto stabilize if airflow over the aircraft is achieved, it does not present much risk unless the aircraft is flown at very low height from the ground at high angles of attack.
--Larger control surface is required for the elevator provide adequate pitching moment, since the center of pressure is located towards the rear of the plane, reducing the moment arm.
Step 2: Things You Need
Structure
1. Coroplast (Corrugated Plastic Sheet) - (120cm x120cm) sheet
2. (3 nos.) Control Rods - Connecting the servo to the control surfaces (length depends on where servo is fixed)
3. (3 nos.) Control Horns - Movable joint for the control surfaces and the control rods
4. 3mm Carbon Rods - Provide extra structural integrity to the coroplast, to withstand flutter and other aerodynamic loads. Number required is a trade off between weight and structural integrity. Read step 5 to decide. Can also use control rods or bicycle wheel spokes (3mm dia) from a repair shop.
5. (1 nos.) Fibreglass Sheet - minimum (5cm x 5cm) - Rigid attachment for motor mount to coroplast
Electronics
1. (1 nos.) Brushless DC motor -1000KV
2. (3 nos.) Servos - 9g
3. (1 nos.) ESC - 30A
4. (1 nos.) Propeller - 8x4
5. (1 nos.) LiPo Battery - 3S (11.1V), 1250mAh or more, 20-30C
6. (1 nos.) RX-TX pair - RX should have at least 4 channels and TX should be configurable to implement aileron mixing.
I won't go into the calculations done for the motor torque, rpm required, or the choice of the other electronics. However, eCalc is a useful easy-to-use online tool which can be used to estimate the electronics requirements according to various input parameters like model weight, wing area and propeller configurations. We can use it to fix one of the electronic components and then see what other electronics are efficiently compatible with it.
http://www.ecalc.ch/motorcalc.php?ecalc&lang=en
Tools
Paper cutter knife, glue gun, pliers, screw driver, ruler, tape, scissors.
Step 3: Download Design.
Find and download the design blueprint image and the solidworks part file attached below for the design. The design will be used for cutting out the coroplast sheets into the different parts - wings, fuselage, tail, and so on. It is recommended that Solidworks be used for better understanding of the dimensions of the plane, than just consulting the blueprint. The Solidworks model would be able to provide insight into which parts of the airplane are attached exactly where and if they are hollow (made by partially cutting and bending the coroplast) or just a single piece of coroplast.
The total wing span is 90cm and the length of the plane from the tip of the nose and the tip of the elevator is 93.8 cm.
The surface area was calculated to be around 8100 sq. cm., therefore a 90cm x 90cm coroplast sheet is enough for the build. But a 120cm x 120cm sheet is recommended because the wing cut-out would lead to some inaccessible areas and it may not be possible to cut out other parts like fuselage in a single continuous piece. Also, the remaining coroplast can be used to add strength by making supports for weak points on the wing or for repairs in the future. It is better if you can get as much coroplast as you can find just to be on the safe side.
Attachments
Step 4: Cutting the Coroplast
Use the solidworks file and the blueprint image to sketch the different parts on the coroplast sheet. Make sure to draw the designs efficiently, such that maximum amount of coroplast can be saved. Please read the full step before proceeding to cut the coroplast.
The wings, fuselage, vertical stabilizers (tails), and the control surfaces should all be cut out separately and have to be joined together later. Now refer to the solidworks part and the blueprint image. We require:
1) Wing surface is a single continuous cut-out from the coroplast. Make sure that the braids of the coroplast are horizontal while sketching the design, as carbon rods would be inserted inside them later so that they remain rigid. The cut-out should come out something like the one shown in the figure. (It has to be cut further to make a slit for the motor and propeller)
2) 1 elevator surface as shown in the files. The rear edge of the elevator can be either zigzag as shown or a straight line as we decided in the actual build. The coroplast braids have to be horizontal here too.
3) 2 identical vertical tail trapezium cut-outs as shown in the files. The braids have to be vertical such that a carbon rod can be inserted and then attached to the wing surface easily.
4) 2 identical rectangular aileron surfaces. THESE ARE NOT SHOWN IN THE SOLIDWORKS/IMAGE FILES. A single aileron would be a rectangular coroplast sheet of (3cm x 35cm) area with braids running along the length.
5) Fuselage is a cuboid which would be attached on the upper surface of the wing. It has a volume (lbh) of (50cm x 6cm x 3cm). The fuselage will be hollow and would be used to store the battery and other electronics. It has to be made from a coroplast sheet of area (50cm x 18cm), with partial cuts at 3cm, 9cm, and 12cm from any edge. By partial cut it is meant that the coroplast is cut only on one side such that it can be hinged from the other direction, and then can be attached together to form a cuboid.
6) Part of the fuselage is to be attached on the lower wing surface, so as to form a 6cm x 6cm square support for attaching the fibreglass sheet for the motor mount. As shown in the files, this has a length of 7cm for the cuboid part and 12.5cm for the pointed pyramid part. See figure for understanding.
7) This is important. The nose is a separate part from the fuselage. It has a volume slighty less than the fuselage and can slide tightly into the fuselage. It serves as an ATTENUATOR, such that on impact it can slide further inside and damp the force such that the impulse felt by the entire plane is reduced. It has a piece of thermocol stuffed inside so that it does not crumple on impact. See figure for understanding.
The width and height of the nose is just slightly less than the fuselage. The length of the attenuator dependts on the battery size as the battery is to be slided right behind the attenuator. We took a length of 6cm for the cuboid part and 3cm for the pointed pyramid part.The cut-out looks like 4 towers stuck together with partial cuts at the bends as in the fuselage.
8) Reinforcing cut-outs - Rectangular pieces of coroplast having a braiding perpendicular to that of the surface it would be attached to. Length can be taken as per requirement.
Step 5: Reinforcing the Coroplast
Due to such a large surface area, the wings and elevator surfaces would surely undergo flutter, which is bad for maneuverability. In an actual plane, a wing is reinforced using spars (webs and flanges), ribs and longitudinal stringers. Reinforcements have to be applied in such areas and also near the middle, where the weight of the fuselage is concentrated. To tackle this we tried three approaches as shown in the images (also have a look at the images on the next page):
1) 3mm Carbon rods/Cycle spokes/Control Rods were inserted into the braidings of the coroplast at regular intervals (for example, at 10cm intervals in the wing). This would give it extra resistance to bending about any direction perpendicular to the rod.
2) Another piece of coroplast was attached on the considered area with braidings in a direction perpendicular to that of the considered piece. This criss-crossing would give it strength in the 2 perpendicular directions.
3) A plastic box packaging sheet was rigidly attached at areas of maximum stress (from simulations/intuition) near the fuselage with a glue gun.
Although these tend to increase the weight of the plane, they are necessary for better strength, structural integrity and maneuverability.
Step 6: Pasting It All Together
The following procedure was employed while assembling everything together:
1) Wingcut-out serves as a base for the whole plane. It is better to mark the center line of the wing.
2) The upper fuselage cutout was taken and folded at the partial cuts made at the mentioned distances. This forms a 3cm x 6cm rectangular cross-section cuboid. Apply a thin line of glue with the glue gun along the joining edges and join them together. A small amount of tape can also be used to hold them together. This is our fuselage which is to be attached to the upper surface of the wing.
3) Similarly, take the lower fuselage cutout and fold it at the partial cuts to get the shape as shown in the blueprint image/solidworks model. You can also refer to the image in the last step. It shows the finished lower fuselage attached to the wing surface. The attenuator (nose) has almost the same shape, and should be done similarly. However, a piece of thermocol starts as the base material for filling the hollow space inside it, such that it does not crush on impact. Refer to the image in step 4 for completed attenuator.
4) Now, for attaching the fuselage parts to the wing, put little glue using the glue gun on the mating surfaces of the parts and the wing, i.e., by coinciding centrelines and starting point of the fuselage is the starting point of the slit in the wing where the motor comes. The upper fuselage is expected to overshoot the wing and the lower surface is expected to reach the starting line of the wing strakes, as shown in the solidworks model. Apply a little pressure and then leave it to dry.
5) The control surfaces are not stuck using glue gun but using tape, as the joint is to be hinge joint. If small hinges are available, then they can also be used. The elevator and the rear wing surface are brought close together, leaving a small gap. The two edges are then tightly joined using tape (such that the tape doesn't sag), first on upper/lower surface and then on the other surface.
Similarly, the ailerons are attached to the wing . Extra area on the ailerons, which overshoots the wing span, is cut off and a straight wing tip is maintained.
6) The vertical tails are trapezoids pieces of coroplast, with vertical braiding. A cycle spoke/control rod bent into L-shape and inserted from a hole made from the bottom of the wing at the position where the tail is to be attached. It is attached there by a little bit of glue and a strip of tape. The part of the rod that stands vertical is inserted into the appropriate braiding of the coroplast tail and the tail is lowered down to a line of glue sitting on the wing where the tail would be attached. The tail is held vertical for a while and when the glue dries, is secured by tape.
This concludes the framework of the F-22. Good job getting here! All that's left is installation and configuration of the electronics and first and subsequent flights!
Step 7: Electronics Installation
1) BLDC motor
-- The motor is fixed to the motor mount (we had a '+' shaped motor mount) with screws.
--This configuration is then placed in the middle of the fibreglass (between 5cm x 5cm and 6cm x 6cm) piece and the locations of the screws are marked. The 4 holes are carefully drilled onto the fibreglass sheet.
--Now, a (6cm x 6cm) piece of coroplast is taken and the fibreglass is stuck to it with the help of a glue gun. Holes are punched into the coroplast from those in the fibreglass.
--The motor along with its mount is then screwed onto the fibreglass-coroplast piece with motor on the fibreglass side.
--Glue is applied at the ends of the fuselage (upper and lower fuselage form a 6cm x 6cm square) and on the coroplast side of the motor mount combination. Both are held firmly together until glue dries and then the configuration is firmly secured by tape (if required). Make sure that the wires from the motor come towards the upper surface of the wing.
2) Servos and Control
-- 2 Rectangular holes of the size of the servos are made on the aileron sides of both the tails (as near the tails as possible to avoid much rolling moment about the CG) for aileron control and 1 in front of the elevator for elevator control.
-- The servos are inserted into the holes and glued down using glue gun (if any servo needs to be replaced, glue can easily be removed using a cutter).
-- Control horns are attached to the control surface near the servo using a plastic packaging sheet with an area much bigger than the control horn surface, so that it doesn't rip off during flight due to high aerodynamic loads. (Control horns should be placed near the servo to avoid bending of control rods)
-- Distance between the control horns and the servo arm is measured and the control rods are bent at the required distance and fixed to the servo arm and control rods.
Step 8: Connections
1) Battery Insertion
-- The battery is inserted from the front part of the hollow fuselage as shown in the figures. (Fig1)
--Two stacks of coroplast are put beside the battery while inserting it so that battery doesn't sway in flight. (Fig2)
--Next, a thermocol piece is inserted behind the battery to push it to the required CG position and the attenuator closes the front of the fuselage. (Fig3)
--The battery connector is accessible through a slit made in the fuselage near the CG, for inserting all the other electronics. (Fig4)
2) ESC Connection
-- The 3 wires from the ESC are connected in any way with the 3 Motor wires. The BLDC motors can run in CCW or CW directions and swapping two wires can reverse the direction.
3) RX Connections
-- Each channel can control a separate function, i.e. a single servo, speed controller, etc. The configuration of different receivers is different.
--If marked, the wire from the ESC is put into Throttle and the servos into the other pins, which are configurable in the Transmitter (Remote). Differential aileron/Flaperon servo configuration, which are used here can be configured following this article:
http://flitetest.com/articles/How_to_Hook_Up_2_Ail...
-- Have a look at this article for more information on TX-RX pairs.
http://www.flitetest.com/articles/hobby-king-2-4gh..
4) Plug in the battery to configure controls and motor direction.
5) Mount the propeller on the motor to check if its in pusher configuration. Be careful not to hurt yourself while doing this. Best not to push the throttle more than 5% while doing this.
Step 9: Fly It!! (Video Will Be Uploaded Later)
Before flying,
Test the CG of the plane. A nose-heavy plane is always stable in pitch, so adjust the position of the battery such that the Center of Pressure (CoP) is aft (behind) the CG. The position of the CoP was found out in the simulations. After a first few flights, it will be apparent where the CG should lie for a smooth level flight.
Test the control surface deflections. No one wants to get up in the sky and then find out that they had the aileron controls all wrong.
Test Battery Voltage. Low voltage LiPo batteries are dangerous and if the voltage drops below a certain level, the branded chargers may refuse to charge them, saying LOW VOLTAGE. Also test TX batteries.
Test TX range in the datasheet. Believe it or not, the day we were flying it in the video, we had a bad crash because we went too far out of range.
Fly in an open ground. It is quite dangerous to fly an airplane, even with tons of experience, for both the airplane and people nearby. It is advised to fly the airplane in a large open area so that in event of crash no one gets hurt. Also, it gets on the nerves of most beginner pilots if there are many people around.
Check out this article for pre-flight checklist.
http://www.flitetest.com/articles/first-flight-qui...
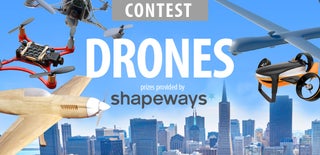
Participated in the
Drones Contest 2016