Introduction: Sugar Shack
Building my own sugar shack has always been a childhood dream!
Being a father who works full time, 3 seasons have passed between the design and the final construction ... A major work yes, but I am very proud of the result ! I have attached all the necessary documents (3D model, 2D drawings, photos) and I encourage you all to embark on the adventure of making your own maple syrup. Of course, if you have maple trees in your surroundings ;-p
Step 1: 3D Design & Material
When embarking on a construction of this kind, it's better to make a complete design of the project to build.
Several advantages:
- unforeseen events are almost eliminated during construction
- develop a complete list of required materials
- saves costs by maximizing design with standard materials
- allows the development of the required subassemblies, etc ....
I used Autodesk Inventor as a design software ... I've enclosed drawings and final 3D within this instructable. You will also find the list of required materials on the last page of the 2D drawing.
All the wood used for the outside comes from wood crate ...this wood destined to junk will be entitled to a new life!
Step 2: Floor Support
I chose to use poured concrete legs. (cheap and very durable)
I used forms of 10 '' dia. But it could have been easily 8’’ dia. I bought also an adjustable leg system. (That way, it will be easier later on to adjust finely the level of the entire structure)
Start by locating the forms on the ground. Take the support that will be the lowest as reference. Draw a level line and cut the lenght of the other forms. Follow the directions of the concrete manufacturer and pour the forms one by one ... do not forget to insert the adjustable support before the curing process !
Step 3: Floor
To support the floor, I built 2 beams (2 times 2x10 screwed together) with treated wood. These beams are installed directly in the adjustable legs.
Then, I build up the floor perimeter using 2x8'' ... (supported by the 2 beams)
Next, complete the floor with all the joist. (Dont forget to add joist hanger at each end) see photos ... that way, your building will last square for years.
And finally, I used 3/4'' plywood sheets for the top.
(See Drawing for all required dimensions)
Step 4: Steam Exhaust Chimney Sub Assembly
One special feature is needed when building a sugar shack … a steam chimney ... The maple water will boil for hours in the shack, so a lot of steam to evacuate. I decided to make it in a subassembly to avoid a lot of work at height later ... I screwed the shutters to the chimney frame … later on, I will create a simple system to close and open the shutters (accessible from the floor).
See Drawing for any dimensions
Step 5: Walls Sub-assembly
Unfortunately, I did not take pictures of the walls sub-assembly that I built. Mounting walls independently (on ground) will make life a lot easier. I even preinstalled forens on all walls ... always easier and faster to install horizontally.
Unlike on the drawing, I did not mount the roof gables on the front and rear wall sub-assembly... it was finally easier to handle without.
Step 6: Walls Assembly
Start by mounting one of the walls on the floor structure. Fix it temporarily (well level) using a diagonal. Subsequently, place the other 3 walls always well level. Anchor all the walls to the floor and between themselves.
As you can see in the photos, I started putting the steam cheminey in place. I had to get him inside the cabin before closing all the walls ... (he did not go through the door opening). This subassembly is quite heavy ... my first challenge was to mount it over the walls. What I managed to do with a little patience and some homemade levering system.
Step 7: Structural Roof Completion and Steam Chimney in Place
Autumn had arrived ... the colors of the trees were magnificent! What a beautiful time of the year to work outside!
This step consisted in assembling the last roof truss and putting in final place the steam chimney.
Finally, I could see a semblance of sugar shack in front of me! Well happy!
Please refer too 2D Drawing for a every dimension needed ...
Attachments
Step 8: Roof Forrens
Since I had already installed the forens of each walls, I just had to install the remaining forens of the roof.
Beginning of November ... and snow was already there !
The material of the roof were metal profile roofing (Vicwest) ... that's why it wasn't mandatory to put wood sheet under.
Step 9: Roofing
I was looking foward to do that step ... My sugar shack's located right under many trees ... that why I was searching for a roofing solution that is easy to install, economical and most important, low maintenance !
Ultravic (From Vicwest company) fit perfectly my need ... I could even choose the color ... a color that would remind me of the old Quebec sugar shack style !
I have attached the list of material with trim detail above.
I'm pretty satisfied with the result and it would last for years without any maintenance !
Step 10: Siding, Door, Soffit
Last big step before having a shack sheltered from bad weather ... the siding !
One board at a time, nail by nail ... It took me around 12 hours to complete the job ... the most beautiful thing ... it cost me 0$ for all that wood ... (Only my time to remove all staples from the crate) ... but still, a nice way to recycle things !
I bought a really nice and neat door from kijiji (online classified advertising service) ... full metal ... and the color match perfectly with the roof ... almost Magic !
Step 11: Chimney
Another good step was in front of me before my sugar shack was functional ... The chimney ...
I evaluated the different options available on the market ... For a chimney at a reasonable cost ... I opted for the single-walled chimney ... By cons, by making this choice, I had to make sure I had a clearance of 18 " with any combustible material ...
I decided to make a wall passthrough with a concrete slab ... a very economical solution. The steps are pretty simple, make a formwork ... fix in place the desired pipe ends. (In my case, I chose a 36'' pipe that I wanted to let go 24 '' inwards). mix and pour the concrete. Voila !
Then, I made the necessary hole in my cabin, add 2 supports (leg for the slab).
The total length of the chimney should be 3 times the length of the evaporator. with my chimney design, it was not a problem.
I made custom mounts at the back to keep everything in place.
I've done a test, and everything works perfectly! Yéééé !
Step 12: Ready for Sugar Season 2019 !
Only about 1 month left before start of sugar season ! Wooohooo !
I almost cant believe I finally made it ! I'M READY !
To get maple water, the best temperature is between -4°C at night, and 4°C at day ... mostly happen in my region during March ...
Meanwhile, why not decorate the inside ...
I'll post later on an instructable about making your own maple sirup ! :-D !
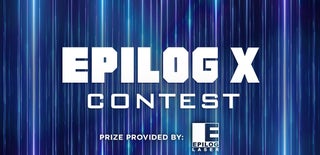
Runner Up in the
Epilog X Contest