Introduction: Super Hero Foam Helmet
As a super hero fan, I wanted to have a replica movie helmet as decoration in my man cave. This guide is meant to show how you can build a replica super hero helmet for costumes, cosplay, or decoration.
Supplies
- 5mm EVA foam
- Contact cement
- Marker (or pen)
- Exacto knife
- Plasti-dip
- Metallic silver spray paint
- DAP DreyDex Spackline
- Tons of patience
- Heat Gun (Optional)
Step 1: Print and Trace the Pattern
I began by finding the template file online. There are a couple of different options for finding good templates. The first option is a software called pepakura, which can be used for turning 3d models into templates. The other benefit of pepakura is that there are a lot of people who have uploaded pepakura files that are free to download. To find them just type into google "free pepakura files". The second option is to buy templates online. Although it costs money, paid templates tend to be easier to use, come in pdf format, and produce nicer replicas. Just be sure to read the reviews before you purchase.
For my helmet I chose to purchase the files on Etsy. The files came in a pdf and were easy to print. Once I printed the files I cut them out using an exacto knife. I then traced each piece onto the 5mm EVA foam with a marker.
Step 2: Assembling the Helmet
With all my pieces cut out, it was time to begin assembling. Before gluing all the pieces together, I used a heat gun to mold them in the correct shape. The heat gun is optional, but I have found that it makes it easier to assemble. Just be sure to keep the heat gun moving, otherwise you can burn the foam. In addition to molding the pieces, the heat gun also seals the foam which will be helpful when it is time to paint.
Next, I used contact cement to assemble my helmet. When using contact cement it is best to apply a layer of glue to both edges of the pieces being connected. Let it dry for 10-15 minutes, or until it is dry to the touch. Once it is dry, attach the edges, gradually applying pressure. If you don't have contact cement, hot glue will work. Just be sure not to use too much or it will spill through the cracks.
Quick Tip: While cutting out the pieces, I made markings on each piece so I knew where to assemble it.The markings can be seen in the picture above.
Step 3: Filling the Cracks
After assembling the pieces, there may be some gaps or holes between the joints. Before painting, it is essential to fill the gaps so that the helmet looks seamless. There are many different products that can be used to fill the gaps. For this project I used DAP DreyDex Spackline. As can be seen from the before and after photos, it does an excellent job at filling all the gaps and holes.
Step 4: Sealing and Painting
Before we paint the helmet, it is important to seal the foam. EVA foam is known to absorb paint, and without a sealing layer it will take many coats of paint, which is costly and time consuming. My favorite method of sealing is using a product called Plasti-Dip. The product is a liquid rubber spray paint that I used two coats on the helmet.It comes in many different colors but I used white Plasti-Dip so that it could be easily painted over. Be sure to use Plasti-Dip in a well ventilated area so that you do not breathe in too many fumes.
With the helmet sealed it is time to paint. The color will depend on the helmet you are making, but for mine I used metallic silver spray paint. After two coats of paint, it was ready.
Overall I am very happy with how it looks. It is a lot of fun to build, and EVA foam is very easy to work with and the metallic paint looks amazing. The method used to make this helmet can be applied to all types of helmets and even full body armor. I will certainly be making more in the future!
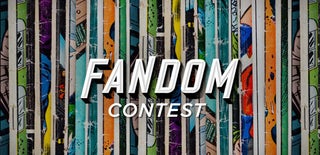
Participated in the
Fandom Contest