Introduction: Tina Piracci's 'Making Hands'
This instructable was created in fulfillment of the project requirement of the Makecourse at the University of South Florida (www.makecourse.com).
This project, Making Hands, is a recreation of M.C. Escher's Drawing Hands. Instead of graphite drawing as seen in the photo, I have created a sculpture of two robotic hands haphazardly fixing themselves.
Materials:
-Arduino Uno Board
-wire connections
-Proximity Sensor (HCRS04)
-Micro servo motor
-9 volt battery (or optional power source) and battery housing
-holding box (I used box provided by course)
-modified Plexiglas
-silicone molds of hands with metal wire skeleton along with other mold making materials
-2 screw drivers
-screws
-strings (I used "invisible" sewing string)
-3-D Printed cog (I have included the file)
-misc. wires for aesthetic purposes (as seen coming out of the wrists)
Molding the Hands:
materials: 2 kits of alga-safe, warm water, dragon skin silicone, silc-pig brand silicone pigment, two 2-liter bottles, quarter inch metal wire, mixing utensil and large bowl.
I bought my mold making supplies at http://www.smooth-on.com/
(they have a student discount if you order over the phone!)
They have very helpful videos, as the one I used for direction here:
First of all, since you are most likely going to be molding your own hands, you would be better off with an assistant as mold making is a timely manner.
-Before starting, make 2 simple metal skeletons out of the quarter inch metal wire. The skeleton must at least be in the thumb and pointer finger at the same distance bones would be from the wrist down the fingers. This allows the hands to hold the screw driver by themselves. Save these for later after you have created the negative with the alja-safe, and before you pour the silicone.
-Prepare two sets of the wires that you would like to protrude from the wrist. You could use about 5" of any scrap wires you have at home. I was picky and selected my wires at Lowe's according to color and size. These will be put in the negative after the skeleton has been placed.
-First, cut about 4 inches off the tops of the liter bottles (as seen in photo) and recycle the top piece.
-Then, prepare equal parts of warm water and alja-safe. With the warm water in a large bowl, simultaneously mix and pour the alja- safe into the warm water. Mix quickly and thoroughly while trying not to add bubbles into the mixture until powder is completely dissolved. MOVE FAST! Alja- safe dries within the first 5 minutes so beware.
-Rinse hand being used for mold with water and place hand in desired position in liter bottle and slowly pour the mixed alga-safe in, keeping your hand in the same position. Let dry for 10 minutes. Hold still!
-Wiggle hand out of mold. Be gentle and focus on allowing air into the mold to release the suction. Now you have the negative of your mold!
-Place the metal skeleton inside of the negative where it is anatomically correct.
-Mix dragon skin equal parts of part A and part B and a quick drizzle of silc-pig flesh pigment thoroughly until it is all one solid color. Be careful not to create bubbles! As you pour the silicone into the negative, tap and rotate the mold the prevent any bubbles from being in your mold. Bubbles will create imperfections in the mold. Let dry for at least an hour to be safe.
-Then, crumble the one-time-use mold off with your hands, and remove the silicone hands.
Assembly: Place all components inside of the box and mount the servo motor in the center of the base of the box with epoxy (and let dry). Then, attach the center of the bottom of printed cog to the servo motor with the tiny screws that should have came with the servo as mounting equipment. For the Plexiglas lid, I routed out a circle for my printed cog to fit in and angled the edges at a 45 degree angle for aesthetics and drilled four holes the countersunk the screws that attach the lid to the box. Before screwing the lid on, drill two screws into the lid in a way that they face out upwards when you close the lid. The placement of these screws should be the midpoint between the cog and the top and the cog and the bottom if you were holding the box with the long side horizontal. View sketch of lid to avoid confusion.
Then, to attach the hands onto the lid, you must first pre-drill a hole into the hand that is slightly smaller than the diameter of the screws in the lid. The location of the the hole may vary depending on your specific hand mold, but to determine the location, place the hands on top of the screws in different ways to achieve the same positioning as seen in the final product picture. Make sure that the placement is not touching your printed cog, as that would prevent movement. Once the holes have been drilled, aggressively push the screw into the hands drill hole for a sturdy fit. This type of attachment allows the silicone to be more free with its movement while still remaining in place.
Now, attach two separate strings to opposite sides of the cog at any given rod with one end attached at the rod and the other around the fingers of the hand. Again, depending on your hand mold, placement of the strings will vary, but you are going to want to attach them somewhere around the fingers by either wrapping it around the fingers, or threading a needle and sewing it through the fingers. For instance, in my piece, one of the hands was sewn and one was wrapped.
With the wire skeletons, you should now be able to simply place the screwdrivers in the hands.
Arduino board set up:
Coding: View Attached file named MakinghandscodeFinal
Circuit Schematic:
Pin setup:
HCSR04: Programmed to activate when object is within 5 feet
gnd --> negative placement on breadboard and 5V on Arduino board
echo--> pin 8 on Arduino
trig --> positive placement on breadboard
Vcc --> pin ~10 on Arduino
Micro servo motor: Programmed to quickly rotate 180 degrees clockwise and then back 180 degrees counterclockwise infinitely when proximity sensor is triggered.
(1) ground --> negative placement on breadboard and ground on Arduino
(2) power --> positive placement on the breadboard
(3) data --> pin ~ 9 on Arduino
View photos for clarification.
Printed cog file: View attachment named cog.ipt
This cog was build on Autodesk inventor and printed with black ABS plastic
If your interested in more of my art projects, feel free to check out my website at www.tinapiracci.com
Thanks!
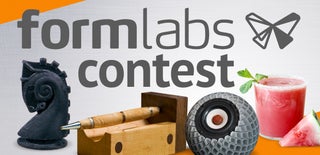
Participated in the
Formlabs Contest
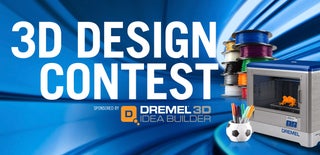
Participated in the
3D Design Contest