Introduction: Tooling an Ammonite in Leather
Ever since I was little, or, more accurately, about when the first Jurassic Park movie hit theaters, I always wanted to be a Paleontologist. Life, opportunities, circumstance and simple bad luck saw to it that I would be heading in a different direction, however I had the great fortune of living in a state in which fossils were in abundance, so became my hobby of collecting them. As part of this activity, it's always good to keep on hand a notebook to record, sketch, and catalog what you find and where you find it, and perhaps someday could serve to further the scientific research of fossils in the area. So I figured, "Why not make my own?"
Allow me to introduce another of my hobbies: leatherworking. Anyone can work leather, if you're patient enough. So, being a DIY-er AND a fossil enthusiast, I thought perhaps I'd put together a little instructional on how to tool everyone's favorite mollusk into a piece of leather destined to be a journal cover, but can be used in any craft or project. Skills learned in this instructable will be invaluable in future projects involving leather, so stick with me and see how I use leatherworking tools to make a 3-d image of a shell using little more than a beveler stamp, hammer, water, and a knife. Oh, and leather, of course.
Step 1: Your Leather.
The canvas for your masterpiece is going to be vegetable-tanned tooling leather. That means that the leather is unfinished, leaving its pores open for whatever you put on it. It cannot be sealed leather, uphostery leather, or the kind of leather you find in the "remnants" bags at hobby shops. Trust me, I've tried. The point is to be able to saturate your leather with water: if water beads on your leather and you can wipe it off without the leather absorbing any and turning dark, you've got the wrong kind of stuff. Look for keywords like "tooling" and "veg-tanned" when shopping.
This leather will be undyed, so save your colors for later. You should also trim it to the project you want. Basically, finish as much of it as you can before you start adding things (like paper textblocks, rivets, or fabric) that can be ruined when you apply dye or finishing sheen. That being said, you should also keep in mind that until you finish your design and your piece dries completely, you leather will be susceptable to the tiniest pressures and scratches.
Keep an eye out, too, for faults in the leather, which often happen naturally. Animals, especially cattle, can have rough lives and the results can show up as scars or blemishes in the leather. This can add character or ruin your design, depending on your tastes. Also understand that blemishes can dye darker or lighter than the surrounding leather.
Once you have your "canvas", lay it out on a flat surface that will be able to absorb hammer taps, like a poly cutting board, and that is preferably waterproof. If it won't lay flat, carefully wetting it down and weighting it with another (waterproof) flat surface might help (just watch for those scratches and debris! Think of wet leather as very firm clay.) Also, be sure you're using the smooth side, not the suede.
When you're ready to sculpt, sit down, turn on some lights, and get comfy.
Step 2: Your Design.
Any design you're planning on using should be either done by you, gotten from a royalty-free site, or used with permission from the artist. Ammonites are mathematical, geometric, and perfect (it's super tough to get one just right), so I recommend a template of some sort. After doing them a while, feel free to start free-handing your designs, adding embellishments, or stylizing the design. We're gonna stick with the basics today. I used a lid from something for the main bit and eye-balled the rest. Hey, even nature's not perfect.
Once you've got your template on regular copy paper (tracing paper's too thin), chop it down so you can see it on your leather, but don't follow the outline exactly. You'll need to trace those later. Finangle it to where it looks best, keeping in mind space for the other parts of your project (binding space, borders, sewing lines, etc). Also make sure nothing is upside down. You'll make that mistake once or twice making wallets, trust me.
Step 3: Casing and Tracing.
Time to case your leather. Casing is when you use a sponge and clean water to wet the surface of your leather until it turns a dark brown, then returns to its normal color and feels dry, but cold.
Now find a mechanical pencil that has a plastic tip and take out the lead. Use the tip to trace your outline on the leather. Use paint tape to hold it down if you like (watch out for tape residue) and press VERY lightly (remember, wet leather is like firm clay!). Use long, steady movements instead of short, feathery sketches, and turn your piece as you need. Get used to turning your leather back and forth, you will be doing that a lot. Take peeks to make sure you went over everything alright, but as long as you have the outline you can usually eyeball it from there. You should just barely see the design on the leather if you're using the right pressure.
Step 4: Cutting in the Design.
Using a leather-cutting knife (which often comes in any kits purchased for leather-tooling), trace the outline of the ammonite. You're not trying to cut completely through the leather, just between 1/2 to 3/4 of the way through, so be careful. Hold the knife with your pointer finger in the swivel saddle at the top, between your most distal and second most distal joints, and use your thumb and other fingers to swivel the knife as you need to trace the outline, always pulling towards yourself. As you can see in the picture, I have not followed my own advice. Oh well. Do what's comfortable and safe, I'm an instructable, not a cop.
Trace around the entire ammonite outline, then put the knife away.
Step 5: Outlining
Get cozy with your two best friends: a hammer and the beveler stamp. That's how you're going to make your design pop from the background. Starting at the farthest point away, wedge the beveler tool into the cut you made and tap it with the hammer. You should use something small and light, like a rawhide hammer, but a small jeweler's hammer will work so long as you don't mind dents in the face.
Does the imprint look dark? If so, keep going! If not, you need to re-case your leather. Keep an eye on the color and depth of your imprints for occasional re-casing as you work. Keep that leather from drying out. Also keep in mind any rings, jewelry, or fingertips resting on the leather while you work as these can leave their own imprints.
You're tapping, not striking. You may be suprised at how little effort it takes to work around your outline, pressing down the leather outside of the ammonite. Turn your piece as you work always on the farthest point, letting you see exactly where you're going. Keep the stamp tilted: if your imprint is a rectangle instead of a fading-away shadow, your angle is too steep. Tap back and forth over stuttering edges to smooth them out, and soon you'll get good enough to tap while you move, holding the stamp lightly in your hand. If your hand starts to cramp, you may be holding it too tightly. Let the hammer do the work, you just guide.
Sometimes you will slip and stamp a little into your design. That's ok, we might be able to cover it up later. Just keep stamping.
Step 6: Inner Peace(es)
Now we're getting into the nitty gritty. We're about the play with just how versatile this stamp is. Starting from the opening of the ammonite, we're going to outline the inner portion of the first cavity. We are going up to, but not against, the line we traced. I tap the stamp with medium pressure as I go. I then go all the way up to the line of the vein spreading out to the outline. This line I use hard pressure, creating more of a shading effect. As I reach the outside, the hard pressure continues, and because I'm not meeting the indentations we'd created already on the outside, a positive space vein will emerge. Keep an eye on the positive space outlines being as consistant in thickness as possible, whether you want them thicker or hair-thin. This will really tie the piece together. Remember to swivel your project as you need to stay comfortable and have your eye on your tracing. Always sit back to see where you're going: ammonites can really lose you.
The first cavity of many is now finished.
Step 7: The TAPPENING
So you think you've got this, do you? Let's move on to the second cavity. Do you remember the pattern?
The innermost line is done with medium pressure, and the side and closest (outside of the ammonite) lines are done with hard pressure. But now we have the right side of the cavity to work on. Turn the work so that the opening of the ammonite is facing towards you. Right next to the vein you stamped in with hard pressure, your going to ever-so-lightly stamp along it to create a faint, raised vein. Your hammer should barely make a noise when making these stamps, giving you three levels of depth: the vein, the cavity above it, and, deepest, the cavity below. Each mark you made with the pencil is going to be a RAISED line. Try not to over-stamp!
Step 8: Keep on Keepin' On...
This is the pattern you follow for nearly the whole shell. Work on each cavity the same way, facing the same direction, with the same pressure. Top part of the cavity medium pressure, left part hard pressure, bottom part hard pressure, right part feather-light.
Turn, stamp, turn, stamp, repeat! And keep an eye on your color so you know when to case the leather again.
Thinking about skipping ahead? Just keep an eye on your pattern, think twice before stamping, and give your hands frequent breaks.
Step 9: Home Stretch
Cavities are getting a bit small, aren't they? Reduce your work a little, do the heavy-hitting sides only, the bottom and left. As long as you keep with the spiral, your ammonite will still look just fine.
Getting even smaller? Now you get to make each cavity with a single stamp of your tool, turning your work as needed to get to the center of the spiral. As your space gets smaller, tilt the stamp to use only the very edge to make the smallest marks.
Step 10: Finished!
Congratulations! You've survived the spiral!
Now's a great time to take a break and come back to nitpick all the parts that don't look right to you. Refine your edges a little more or deepen some shadows. Use background tools for the rest of the leather (ball peen hammers make great "stone" effects).
When you're done and satisfied, you get to let everything dry and finish your leather as you like, with dyes, acrylic paints, finishes and gloss.
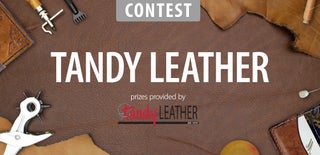
Second Prize in the
Tandy Leather Contest 2016