Introduction: Tricycle Cupcake Car
Cupcake Cars are amazing! Just look at the first example above and realize that it puts a smile on your face. We've seen this again and again as we've built and exhibited Cupcake Cars in San Diego. The reactions from onlookers as we drive and pirouette gives us great joy ... and angst.
Why angst? Primarily because kids are among those who react most favorably and they're the least likely to be able to drive Cupcake Cars. These cars are large and heavy and fast. They're typically powered by mobility scooters and are largely for adults to drive and for kids to admire. We think that's sad. Wouldn't it be wonderful if kids could drive cupcake cars too?
Thankfully Chris of Tom Sawyer Labs asked and answered this question long before we did. He prototyped and developed the idea of powering a Cupcake Car with a tricycle. Better still, he addressed the single biggest hassle of operating these cars: getting in and out. Above you can see the rendering and picture of the wide opening which makes access easy. We were thrilled to discover these cars on Facebook, then see them at Bay Area Maker Faire and finally to meet Chris.
This Instructable takes his creation and turns it into a project which you too can build. We did this so that more people are empowered to bring Cupcake Car joy to children. Here we document our build and share resources. With Chris' approval, you too now have a how-to guide for building your own Tricycle Cupcake Car.
Read on ...
Step 1: Overview
We've broken the build process into five steps. Many pictures and files are provided but in each step we always provide an overview, an assembly description and a parts list. However, it's not perfect so please feel free to ask questions and we'll do our best to respond. We'd appreciate your help with improving this Instructable.
Note on File Formats: The file formats we use include Corel, DXF, and Gcode. If these don't mean anything to you then here's a brief summary of the role they play. Corel (.cdr) was our design software. We output from Corel to the ubiquitous AutoCAD format (.dxf). We used VCarve Pro to define our tool paths and output Gcode (.nc) with our CNC control software to cut our plywood.
OK, we're ready to get started.
Attachments
Step 2: Cuts and Parts
The frame made up of 1/2" plywood and metal hardware but at its heart is a tricycle.
The tricycle chosen is from Harbor Freight (of all places) and can often be purchased for $55. As makers, one feature that we really like is the square tubing which makes it easy to build on. With adjustments other tricycles can be used but for this project our files assume the All-Terrain Tricycle.
Cutting with a Large CNC
The wood in this project is cut from three 48"x48" pieces of 1/2" furniture grade (5-ply) plywood using a 0.25" square 2-flute end mill and 1/8" drill bit. You can see the three cut sheets in the first images above which were screen captures from within Corel Draw (.cdr), the design software we used. Those Corel designs were then exported (.dxf) to Vectra's VCarve Pro to set up tools and paths and exported as gcode (.nc). All the files that we used are provided with this Instructable.
Cutting with Hand Tools
The vast majority of us won't have a large CNC so we'll have to cut using hand tools. The wood can be cut from the same 48"x48" pieces using three tools: a jig saw, a drill and a Dremel. The bits you'll need for the drill are a 1/8" and a 1/4" while the Dremel's accessory you need will be a 565 Multi-Purpose Cutting Kit which come with router bits for cutting the uniform depth plunge cuts. Above you'll find five PDF files to use with a 36" wide printer or plotter to create the templates. By aligning and taping the two which pair (see pictures) you'll have the three cutting guides you'll need to tape or glue to your wood. Your cuts should progress from drill to router (Dremel) to jig saw; we did all our jigsaw cuts from the outside and worked toward the middle. For one cupcake tricycle car the cutting with this approach took about 12 man hours. Note: this approach will be less precise and require minor adjustments during assembly but, hey, in the end you'll still have a cupcake tricycle car!
A sense of the cutting and resulting wood can be seen in the last picture in the above sequence.
All this wood is held together with wood glue and metal hardware. We detail all the bolts, hinges, L-brackets, screws, etc throughout this document. However, below we've consolidated all hardware in one list so you can shop for all your hardware at once. This should allow you to progress quickly through the build.
Parts:
- wood glue
- 2" rectangular hinges x 8
(2 used in Hinged Lower Ring)
(6 used in Back Hinged Arch) - 4" long strap hinges x 4
- wood screws x 14
- 0.25-20 t-nuts x 48
- L-brackets: 1.5" wide x 2" x 2" x 2
- 0.25-20 bolts 2" long with wingnuts x 3 (for securing spacers)
- 0.25-20 bolts 2.5" long with nylon lock nuts x 2 (for lower linkage)
- 0.25-20 bolts 2.5" long with acorn nuts x 2 (for upper linkage)
- 0.25-20 bolts 0.75" long with t-nuts x 6 (L-bracket to base)
- 0.25-20 bolts 2" long with t-nuts x 8 (base to tricycle rear axel)
- U-bolts: 1-1/2" center-on-center, 3-1/2" height with 2" threads (such as McMaster 8875T853) x 2
- 28" length of 1/2" pipe x 2
- 1/2" outer diameter irrigation tubing, 100 feet
- 1.5" finishing nails x 36
- 6" zip ties (a bag 50 will do the trick)
Attachments
Step 3: Hinged Lower Ring
The top and bottom halves of this project are separated by two flat rings.
The lower ring is double hinged and is supported by two struts. Understanding this is important so let's take time out to watch the first video above. As Doug demos the opening and closing of the tricycle note two things: 1) when the upper ring is pushed up it rides on a frontarch of the lower ring and 2) as the rear of the upper ring is raised or lowered it moves in the opposite direction of the backarch of the lower ring. The front and back arches each ride on hinges of a short supportarches which are held up by two struts connected to the Cupcake Car base. Review the notes in picture 2 to get oriented to the pieces and their names.
There is no more important concept to understand in this project so take a minute to think it through.
(The upper ring is unbroken, supports the dome, and is something we will get into later.)
Before we move on to assembly we need to talk about alignment. If this process is not followed correctly then the tricycle car will not come together correctly due to a lack of the pieces aligning properly. We'll explain how to do this right but be forewarned that not paying attention here can cause a major fail in the project.
OK, on to the fun stuff ... assembly.
In the big picture we'll be installing the six rectangular hinges to assemble the lower ring (and removing the back arch then attaching the struts to the short support arches (and reattaching the back arch). Now is when it takes shape!
Assembling the Lower Ring: It will help if you look closely at a few pictures first. Picture 3 shows where holes from a hinge were marked and pilot holes were made for screwing. Picture 4 shows one of the rectangle hinges in the process of being attached. Picture 5 shows the hinged lower ring fully assembled, albeit, on a completed assembly. Getting this right requires a couple of special insights.
The video shows a strap hinge on either side of the strut. What you see is in the picture is one strap hinge for the back arch (the second hinge is behind the strut). You may find it necessary to cut a small notch into the strut to allow the hinge to be correctly positioned: 1) you'll want the pivot of the hinge to be aligned with the gap in the wood AND 2) you'll want for all the bolt holes to be well within the plywood so the straps can be secured.
You will assemble your lower ring flat on the floor and once completed it will look like a (perfect) hinged circle. (Now, temporarily remove the large back arch as it's a bit of a nuisance in the next step.)
Attaching the Struts: The magic of proper alignment comes in this next step. It is now when the struts will be installed connecting the base and the hinged ring. To set the stage you'll install the tabbed structural supports in the base (2) and in the back arch (2), as shown in pictures 6, 7, and 8. Now, with the base on the floor with slots up, position the two front and two side strut as annotated in picture 8 while the other end of each strut is inserted in the slots shown in picture 9. During assembly you'll be gluing and screwing these into position. When you're done, the top of the support triangle will look similar to picture 10 while the overall support structure will look like picture 11. (Note: Once the glue dries you can reinstall the large back arch.)
With precisely milled wood and smart engineering, now is when this design really starts to shine.
Assembly:
- Properly position the four pieces to form the hinged ring on the floor.
- Mark, pilot and attach the two rectangular hinges to the front arch, one per side.
- Mark, pilot and attach the four strap hinges to the back arch, two per side.
- Remove the back arch before moving on to the next step.
- Glue and insert the tabbed braces in the base (2) and the back arch (2).
- Glue, insert and wood screw one end of four struts in the proper slots in the base.
- Glue, insert and wood screw the other end of the struts in the proper slots in the short support arches.
- Place structure in a safe place and let it dry for 24 hours.
- Reattach the back arch.
Parts:
- wood glue
- 0.25-20 t-nuts x 32
- 2" rectangular hinges x 2
4" long strap hinges x 4
Step 4: Back Hinged Arch
Supporting the back of the lower ring is a hinged, collapsing arch.
Before we start I suggest you again review the first video but this time focus on the back of the lower ring where Doug has his left hand. There are a few things to note about this supporting arch: 1) at the base it is hinged, 2) about a third of the way up are hinges and 3) at its top it's connected with a hinge to the lower ring. Review pictures 3 - 7 to get your head wrapped around this and see picture 8 to see the end result. As you can see, this assembly is largely about screwing the rectangular hinges in place but it starts with a little gluing.
In the video you probably saw a linkage connecting the supporting arch with the upper ring. In our last activity on this page we'll be installing the linkage mount on the upper ring and creating the linkage itself from a length of pipe. Then we'll install the link by securing both ends with bolts through holes in the flattened ends of the pipe.
Assembly:
- Glue and clamp the pivot locks to the lower stems paying careful attention to orientation and let dry.
- Position, mark, screw on the two 2" rectangular hinges to complete the supporting arch structure assembly.
- Position, mark, screw the 2" rectangular hinges connecting arch to the base (note position relative to slots).
- Position, mark, screw the two rectangular hinges which secure the top of the arch to the lower ring in back.
- Using three 2" square pieces of 1/2" plywood scrap insert three spacers in front between the two rings.
- Position as marked, drill holes and secure the three spacers with the three 2" bolts and wingnuts.
- Insert four 2.5" bolts in the slots at ends of the two linkages points and measure center-to-center distance.
(Note: do this in the locked position, i.e. with arch legs straight and the back hinged ring up as in picture 11) - Pound flat the last inch of each pipe length, mark and drill 1/4" holes for proper center-to-center positioning.
- Place the linkages on their bolts and secure them with nylon lock nuts (lower) and acorn nuts (upper).
Parts:
- 2" rectangular hinges x 6
- 0.25-20 t-nuts x 16
- wood screws x 8
- 0.25-20 bolts 2" long with wingnuts x 3 (for securing spacers)
- 28" length of 1/2" pipe x 2
0.25-20 bolts 2.5" long with nylon lock nuts x 2 (for lower linkage)
0.25-20 bolts 2.5" long with acorn nuts x 2 (for upper linkage)
Step 5: Tricycle Mount
Now we will secure the trike to the cupcake structure and provide support for the front of the car.
With this step we begin the biggest gluing job of the project wherein we create a triple-thick mounting structure. Picture 1 shows the parts we'll use while picture 2 shows the assembly, clamped after gluing and in the process of drying. Picture 3 shows the mounting of the L-bracket which has been bent to 75 degrees so the mount will be flush with the stem of the tricycle. All that's left is to secure the L-brackets to the base and the trike to the mount.
Lastly, you'll be securing the back of the trike by inserting bolts through the back axle and base board.
This completes the bottom of the tricycle cupcake car, next you'll be moving onto the muffin top dome.
Assembly:
- Glue and clamp the four pieces which make up the tricycle mount arch.
- Bend the 90-degree L-brackets to a more accute 75 degrees.
- Attach the L-brackets to the bottoms of the mount arch with wood screws.
- Position the mount arch over the base pockets and mount the L-brackets with bolts and t-nuts
- Insert the U-bolts over the tricycle neck, through holes and steel plates, then secure with nylon lock nuts.
- Drill 4 to 8 0.25" holes through the back axle and wood base and secure with 2" bolts through t-nuts.
Parts:
- L-brackets: 1.5" wide x 2" x 2" x 2
- 0.25-20 bolts 0.75" long with t-nuts x 6 (L-bracket to base)
- wood screws x 6 (L-bracket to arch mount)
- U-bolts: 1-1/2" center-on-center, 3-1/2" height with 2" threads (such as McMaster 8875T853) x 2
0.25-20 bolts 2" long with t-nuts x 8 (base to tricycle rear axel)
Step 6: Muffin Top Dome
This step of building the top will give you a quick sense of accomplishment.
It's a relatively straightforward process of cutting lengths of tubing, weaving the sections of tubing into a dome structure, and finally securing your work. The result is a domed muffin top. Note: the inner ring of holes is not used and all the sections of hose will be inserted into the outter ring of holes.
Finishing this you've completed the mechanical build of a tricycle cupcake car, congratulations.
Next stop?
Giving it personality with a skin.
Why not write your own Instructable about it?
You can see an example skin done by Peggy in the pix above.
Thanks for powering through this and adding another tricycle to the fleet!
Oh, and send us a picture of your completed cupcake. We'd love to start a gallery to share with the world!
Assembly:
- Cut 1/2" tubing to nine lengths of 44" and nine lengths of 55".
- In every other hole insert one end of a 44" length and clockwise insert the other end nine holes later.
- In every other remaining hole insert one end of a 55" length and clockwise insert the other 13 holes later.
- Hammer finishing nails through the edge of the wood through the hose lengths in each hole.
- Shape the dome by adjusting the lengths and, when satisfied, lock it in by wrapping overlaps with zip ties.
Parts:
- 1/2" outer diameter irrigation tubing, 100 feet
- 1.5" finishing nails x 36
- 6" zip ties (a bag 50 will do the trick)
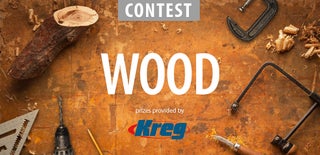
Participated in the
Wood Contest 2016