Introduction: Turn a Trestle Table Into a Desk!
Hey peeps,
I'm back with my second instructable. This desk is a little tester for my table that I'm going to build for my apartment. I hope this instructable also inspires some of you to source some wooden furniture that could use some TLC and be re-purposed for your home.
I got some old trestle table tops from a church and a few old ones from a scout hall. Pretty much the tops were sourced via my partner and her relatives, so a BIG thank you to them! I have no idea what wood they are made from, but a few guesses from mates and my grandad reckon they might be made from some old aussie pine, which is near impossible to source now that we grow some fast growing pine that was introduced from the Americas.
So what are you going to need?
-Trestle table tops. I personally thought a good amount of wear and tear was a good thing and I actually thought I sanded it back a bit too much a lost some of old paint and marks left on it.
-Legs. My brother had some Ikea bench legs he was getting rid of which I grab and chop down to size. For these legs I also needed some plastic caps to cap the legs and some extra wood to stabilise the legs.
-Sand paper. 80 grit, 120 grit, 150 grit and 180 grit. You will use them all.
-A general wood or plaster filler.
-A clear coat, I used polyester again (as its the only thing I have). But again what ever your feel like, wax, polyurethane, paint, etc.
-Nails and screws.
-Pop rivets (only if your going to use my style of legs)
What tools you'll need?
-A hammer. Its a handy tool and if they are old trestle tops, they will have nails, pins, staples, random metal objects embedded in them.
-A saw. I just used a circular, its quick, easy and cuts straighter than the jigsaw.
-A Square protractor/ruler.
-A sander. I just used an orbital.
-A drill.
-A paint brush. To coat the desk.
-A Screwdriver
-An angle grinder & pop rivet gun (for my legs, maybe not yours though).
Step 1: Got Your Table. Grab Your Hammer and Saw!
Ok, first thing is real easy. Grab the hammer and pry off any of random things still attached to the table top. I found nails, staples, pins and a hair clip all embedded in the table top. Get these all out.
Cool all done. Have a think about how long you want this table to be. My trestles were 2.7m, and I cut this one down for my desk to ~1.5m.
Measure from both sides in and you'll realise that old trestle tables are ever so slightly out of wack after the 30+ years of heavy use. So to fix this I'm going to chop both ends off. I used my square protractor to measure in from both sides of the table and both ends to create a fairly good straight line, which I marked in pencil. Then I grabbed my circular saw and took my time in trying to cut a straight line. It was tough, I had to lean over the table to do this and saw dust was flying right into my face as I was looking straight down the line I marked. So grab some good protective equipment (glasses/goggles and a mask over your mouth).
After you cut it, you may need to re attach some wood on the bottom to stop the planks of wood from falling apart from each other.
Step 2: Sand and Sand and Sand and Sand.....
Yep, my favourite step peoples. I kid... or do I? Actually sanding down these tables is a double edged sword. You will lose a lot of the cool characteristics from these old tables, But you'll also make them a lot smoother and even out a few surface marks. Check out the pictures, I did lose a few characteristics.
Start with 80 grit and work your way to 180 grit. Go beyond 180 if you want as well. I personally found 180 was quite smooth by the time the whole job was done. That said I'm tempted to go further with my grits when I build my dining table (next project).
Step 3: Fill in the Gaps.
A big thanks to my dad who did this step. He was pretty eager to jump on board and see how it all would turn up. So he was pretty keen to help out :)
In Australia, so most likely everywhere else, we have a nice non-toxic, multi purpose filler. You just apply small amounts of water until you get the consistency you want and then apply it. Just use either a ruler or plastering tools to smooth it all out. My filler product was touch dry in 4 hours and full dry in 24. After this, sand it down with 120 or 150 grit paper.
Unfortunately, I didn't get pictures of this step. The desk I didn't fill in between the jointing of the boards. The 2 pictures are actually from my dining table (work in progress). But overall, the desk pretty much looked the same.
Step 4: Coat Your Desk.
Grab that left over can of what ever coat you have... Or take on the off cuts, give it a quick sand and head down to your local hardware store and discuss what kind of finishes you can achieve and what might you need.
As I said at the start. Polyester was just left over. I did a quick test on an off cut and it looked fine. So I jumped straight in and coated the whole thing. Now the trick I found was go slowly, especially towards the ends and sides of the desk. When you approach the end of the table or sides of the desk, if you go to fast or hard with force, small droplets will spray up and back onto the surface. This will create a bumpy finish and would be noticeable under light.
Also, coat the desk in one direction. This will help give a more even and consistent coat.
Cool. Leave it to dry now (24 hours for me).
Step 5: Rinse and Repeat
Sand back the coat with the last two grits you used. So for me I sanded the desk again with 150 grit and then 180 grit. Then I gave it a fresh coat and waited for that to dry (another 24 hours)
Then again I sanded it back used my last grit this time. So for me I sanded it back with 180 grit only this time and again gave it a fresh coat and waited for it to dry.
Now just give the newly coated top a good stroke. Does it feel soft, smooth, is the texture right? awwww yeh.
Step 6: The Legs
Seriously, you can pull legs off anything, create your own or just go to Ikea and they will have trestle legs, desk legs or bench legs you can use.
I'll explain how to attach the legs I got and how to work with them.
The average desk height is 75cm or 29.5inch. You need to consider that when building your legs and also, do not forget that the trestle top will also add some height.
Once you have measured the distance on your Ikea bench legs that you need to chop off, grab that square protractor again and mark a good straight line around the whole section you're going to cut. Use your angle grinder to cut each leg to the correct height that you need them to be. If you are in Australia, make sure it is not a total fire ban day, as sparks from grinding have been known to cause fires.
Note: Doesn't matter if its a slightly uneven cut. Capping it will create a level surface at the bottom.
Step 7: Tap That Cap in or on :/
Guess what. Best thing ever. I thought, yep, they look like they would need 5cm square caps to cap those ends I've created. Guess what, actually the inside of my bench legs were 43mm, thanks Ikea, go me!
So as a solution, I just grabbed a sharp knife and cut off the corners of each cap. Once this was done, rather than the cap being placed inside and fitting nicely there. It was able to fit tightly around the outside.
To stop them coming off, just drill a hole through the plastic cap and through the steel. Then grab a rivet and just a pop rivet gun to attach the caps permanently to the legs.
Step 8: Stabilise the Legs.
I had some off cut wood lying around, which I attached to the under side of the table to create a solid area on which the legs could be attached to the table.
Step 9: Finally Job Done!... Nearly.
Ok, nearly there guys.
Firstly, use a drill piece that is smaller than the screw you intend to use. Mark out where you want to attach the legs and then drill your holes. This creates a hole that is small enough that your screw won't fall out, but also just a bit more space for your screw to go in more easily. This will also help prevent cracking to the filler on the other side by doing this as there is a lesser chance that your screw would start forcing the wood/filler upwards and out of position.
Cool, all done? Screw and tighten all the legs into place!
Step 10: Done!
Sweet job guys, admire it for one brief moment and then place your new desk into the spot you wanted it! :) well done.
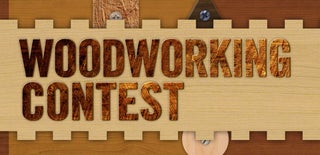
Participated in the
Woodworking Contest