Introduction: Upcycle a Hard Drive Into a Clock
If you've ever wondered what you can do with old computer parts, this is the Instructable for you - and just in time for daylight savings time! In this Instructable, I'll be giving you Pro tips on how to upcycle a computer hard drive into a one-of-a-kind clock. You'll learn how to identify the parts of the drive and drill through metal.
My wife's first computer was a PC with a whopping 40 MB hard drive (I'm a Mac guy myself). I have to chuckle at that now because these days storage devices can hold many thousands of times more memory - and my wife can easily fill a 3GB hard drive in just over a year with all our blog photos!
I originally got the idea from my niece who used to make and sell hard drive clocks for spare pocket change. Her father (my brother) owns a computer repair shop so there were always dead hard drives around that were ripe for the picking. She made the one pictured in the video above as a gift for her grandmother.
Step 1: Anatomy of a Hard Drive
Before you can take apart a hard drive, it's good to know the name of the parts. If you get stuck, refer back to this diagram. Not marked above is the motor which is hidden within the spindle hub.
An IT expert reminded me in the comments to wipe the drive clean of data before upcycling it so I'm passing that great pro tip along.
Step 2: You Will Need...
Salvage a hard drive from an old computer. Apart from the hard drive, you'll need just a few items for this project:
- Safety goggles,
- Torx bits (get a kit that includes T6-8 sized bits)
- Screwdrivers (cordless or electric and manual),
- Punch,
- Vise (my favourite vice is a Panavise),
- Drill bits of varying sizes (the largest should be slightly wider than the clock shaft)
- Hammer and
- Clock kit.
Torx bits are made for a screw head that is shaped like a 6-point star. I used a #8 Torx bit. For this particular hard drive, I found that the #8 worked for every screw, but I have had instances where I needed a smaller bit too (i.e. for the spindle).
Clock Mechanism
I'll be using a clock mechanism that I salvaged from an old clock. If you have to buy a kit, the best one for this project is made to be used on a 3/4" thick surface. It's better to find a kit with shorter clock arms; if you have one with long arms, you can probably still use it but will have to cut the arms to fit within the platter.
Step 3: Get Your Wife to Take Apart Her Old Computer
My wife not only donated the raw materials for this project, but she also helped me take apart the hard drive so I could photograph the steps for you. She has much better motor skills than me when it comes to the finer details; I'm not that great with tiny fussy pieces!
Step 4: Remove Circuit Board
To start, on the back, you can remove the screws holding the circuit board and remove it. You can also remove the rubber membrane; it will give you a cleaner look.
Step 5: Remove Front
Turn the hard drive over, then remove the screws from the front of the case.
If you find that you can't remove the front cover, it could be because there are at least one or more screws hiding underneath the label. You can feel for it and use an X-acto knife to score an 'X' to cut it open.
There were six visible screws in this case, but also one hiding under the label.
Step 6: Open Case
Open the case to reveal the shiny mirror-like platter; it's a thing of beauty! Some hard drives contain two platters to store the magnetic data (like the second picture), but this drive had only one. Either one will work as long as your clock mechanism will fit through 3/4" material. Before we can reassemble the drive into a clock, there's more disassembly to do.
Step 7: Remove Screws Around Spindle
Remove all the screws around the spindle (there were six). Save the screws for later; you'll need them when you reassemble. Remove the collar and ring which will free up the platter and set them aside for later also.
Step 8: Getting to the Platter
In some cases, you'll be able to lift the platter out by moving the actuator arm. In this case, the arm wouldn't move far enough to wrangle the platter out. You can try removing the screws holding down the actuator itself, but the second screw was hidden in a place that couldn't be reached. As a last ditch effort, loosen the large screw on the actuator axis.
Just a few turns to the left and the actuator arm popped up enough that the platter could slide out.
Step 9: Lift Out Platter
With the screw loosened, the platter slid out from the back side.
If you're able to get the actuator off, you can reclaim a strong magnet that's attached to it. You'll likely have to put it in a vice and tap it apart using a flat head screw driver to free it up.
By the way, when you're handling the platter, try not to get finger prints on the shiny surface. If you do, it's not a big deal; you'll just have to clean them off.
Step 10: Remove Motor
The motor has to come out next; remove the three screws holding it down.
Step 11: Remove Centre of Spindle
Once the motor is released, you'll need to secure it in a vice and tap out the centre spindle/bearing. I looked everywhere for my vise and couldn't find it, so I did the next best thing; I drilled out a hole into a piece of wood using a hole saw.
The hole was just big enough so I could nestle the motor in it. I inserted a punch into the centre of the spindle and gave it a few taps with the hammer. As you can see in the last picture, the spindle was pushed out the bottom.
Step 12: Separate Two Halves of Motor
With the spindle removed, you can take apart the two pieces of the motor (mine was held together magnetically so give it a good pull to separate it). The second picture shows the pieces of the motor that the punch and hammer helped get apart. We'll be drilling through the aluminum part shown on the right side of the second picture.
Step 13: Clock Mechanism
Pictured above is the clock mechanism I'll be using; as I mentioned, it's one I reclaimed from an old clock. It has a convenient metal tab for hanging on the wall.
Step 14: Safety First
Pro Safety Tips:
- Be sure to secure your vice to your work surface. If you don't bolt down the vice, the drill can send it flying like a propeller (trust me on this, I know!)
- I can't stress enough the importance of eye protection; wear safety goggles or a full face shield to protect your eyes from flying bits of metal. As a pro, I buy the best goggles money can buy. A good pair has a soft flexible face seal on the top, bottom and sides, fits over prescription glasses, has fog free lenses and has an adjustable headband for a secure fit (the last picture shows the ones I prefer).
Comparing Eye Protection
If you're buying eye protection for this project, choose the pair that provides you with a full seal around the face. In the first picture, the top pair of goggles is ideal. As compared to the second pair of googles, you'll be protected from metal that could potentially fly up from underneath or down from the top too - not just the sides.
Step 15: Drill Out the Motor Cover
As you can see in the first picture, the holes in each side of the motor are too small to allow the shaft of the clock mechanism to fit. If you want to be a purist and reuse every piece of the motor, you can widen both of them with a drill in order to get the clock mechanism through the holes. However, it's really only necessary to drill out the aluminum motor cover. Secure the piece of metal in a vice.
Drill out the hole in stages: first with a small drill bit then working up to a larger bit that's slightly larger than the width of the clock shank. Each bit you use should be slightly larger than the hole, but should fit snugly into the middle so you can work your way up to a larger hole each time. I used three bits (second picture) to achieve the final size.
Drill the hole slowly; slow and steady wins the race. Aluminum is a soft metal, so you don't need a lot of pressure either. When you're finished drilling, test it with the clock shank to to make sure the hole is large enough.
Step 16: Assemble the Clock Mechanism
Now you can reverse engineer the pieces previously removed and install the clock mechanism. Place the clock mechanism behind the hard drive. I used double sided tape, but you should really use permanent glue to secure the mechanism to the back of the hard drive - especially if you'll be hanging it.
Place the motor cover over the clock shaft, followed by the ring, mirrored platter and then the collar. Secure it with the screws you previously saved.
Re-tighten the screw holding the actuator arm to snug it down.
Step 17: Add the Hands
Assemble the remaining pieces of the clock onto the shaft. If you're using a kit, you can following the directions. Otherwise, add the washer, hex nut, two arms, smaller nut and lastly the second hand, if your mechanism comes with one.
Step 18: Install a Battery
Insert a AA battery and set the time. If you like, you can add clock numbers onto the face, but I prefer it just the way it is.
Step 19: Enjoy!
You can either hang your clock on the wall using the tab on the clock mechanism, or add a bracket so it can sit on a desk. As shown in the previous step, I found a spare pull handle and glued it onto the back so I could prop it on a desk.
Time to find another project!
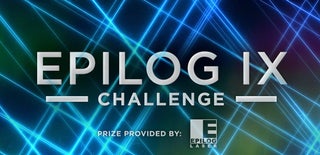
Participated in the
Epilog Challenge 9
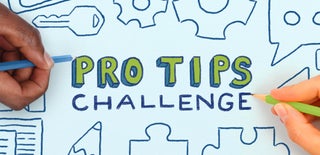
Participated in the
Pro Tips Challenge
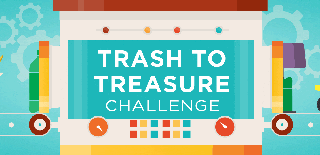
Participated in the
Trash to Treasure