Introduction: Vines Marshall Amp Head Shell
I'm in a guitar building guild - Guys Building Guitars - and we display every year at the Dallas International Guitar festival. I like to build one of a kind never before seen creations to draw people into our booth as we seek new members. Last year I built the Iris cab which is here on the Instructables site.
This year I wanted to feature something that paid homage to H H Giger, the artist that did the conceptual art for the Aliens movies. His geometric patterned tentacles called to me and I wanted to reproduce these in wood. I also had a bunch of beautiful figured scrap wood from other projects that I couldn't throw away to utilize.
Step 1: First Cuts and Finger Joints
The main body wood is padauk. It is easy to work with and carves well. But it has a bit of a drawback in the microscopic dust it creates when cut. A good dust collection system and a dual filtered mask are recommended as the dust gets everywhere. A shower after cutting it is highly recommended as it turned my pillow orange.
I like to use finger joint as it adds an interesting texture to the mating edges of the case. I've found the key to good fingers is a very consistent jig to minimize run out as the cuts go across the edge. Also a high quality carbide dado blade set. And lots of test cuts and patience! Also also - test fit and measure as you go to catch problems before you cut up your beautiful project wood. Don't ask me how I know this...
I cut the top and sides so they are 1/16" 'proud' so the fingers protrude a freckle above the mating side. Once glued the freckle is sanded flat. To save figured wood I put a piece of plywood as the bottom side.
Step 2: Time to Cut the Vines
I have a small band saw - one the indispensable shop tools - and used it to cut undulating 'vines' on the sides. I then stuck the top piece into the sides and used them as a guide to start the top's cuts. I didn't cut all the way through the sides for several reasons - strength, to cover the boring chassis side of the amp inside and mostly sanity as I only had five pieces of padauk to ride herd on instead of nine.
Step 3: Cross Vines
Now the fun really starts. I wanted a contrasting figured wood to 'cross' the main vines and chose curly maple. The figure on the maple was perfect as I wanted it to 'follow' the movement or undulation of a vine as it snakes about looking for room to grow. I contemplated dado cuts on the underside of the padauk and then fitting the maple to it for strength as the structure would be the carry handle for a 50lb amplifier. A cooler headed friend reminded me of the bonding strength of modern glues so I chose to cut and sand to fit maple blocks in between the padauk vines.
I put the block on the underside of the padauk vines and traced the curves. I moved to the next open space and turned the maple to follow it's curve through the jungle. A few cuts on the band saw and some sanding to fit on an oscillating sander then on to the next piece.
At this point the top and sides were dry fitted into test finger joint blocks. Once I glued the top padauk and maple together I ran them through a drum sander to mill them down to the same height. The sides were glued and milled to finished thickness - 3/4".
The chassis was glued together. I put two pieces of scrap on the bottom plywood as edge 'caps' to conceal it. I also utilized more padauk scrap for 'fake' fingers to fill and conceal the joints on the bottom edge of the sides.
Step 4: Geometric Pattern Madness...
The curly maple lent itself well to simulating a living vine growing in the jungle. Alas, the padauk for all of it's wonder coloration, semi straight grain and beautiful carving structure - failed. Utterly. Completely. So began the six week adventure into the dark and unknown [to me] world of bias relief carving.
Knives and chisels and dremels - OH MY!
A full fifteen iterations on the scrap wood cut from the top. Snake scales, pyo dragon scales, geometric patterns by the bucket load were carved, tinted, epoxied, cussed and discussed at length. The scrap started at almost an inch in thickness and was sanded down to 3/8" by the time I found a solution.
Simplicity, a plunge router base for a dremel and scrap zebra wood to the rescue.
Step 5: Router Madness
I built a pair of bearings for a Stewmac plunge router base to force the 12,000 rpm cutting bit to at least follow the outside edge of the vine I was working on. The sides and where the maple crossed the padauk were entirely cut free hand - not as hard as you would think as I only cut a .050" depth slot. 208 slots later...
Step 6: Inlay Foolishness
I swore when I started making cabinets and guitars that I would never ever, no way in hell, do inlays. Hell thundered into my existence in the form of a deadline. The guitar show was three weeks away and the padauk vines didn't look 'viney'
Enter the zebra wood scrap - 1/2" wide, .070" thick, 16" long strips. I cut each piece to the rough length I needed and sanded them to fit. I cut them in sequence to keep the prominent wood grain 'flowing' as the pieces marched across the vine. Each one clamped and then sanded to fit and be flush.
I was informed later that you cut the inlay pieces first THEN cut the slots... Supposed to be easier.
Step 7: Jungle Faceplate
This being a Marshall I wanted the face plate to announce that in a slightly tarnished overgrown jungle way. With a bit of curly maple scrap from the Iris cab build I proceeded to 'string box' cut the maple. This is done on a band saw to cut in the gently curved arcs. Those cuts were then filled with a 1/8" thick strip of padauk and glued back together. Cut and repeat. You might be tempted to cut several arcs to speed up the process as I did. Don't. The resulting oozing, squirming mess was a clamping nightmare. In honor of the madness this project requires I made 22 string cuts.
The resulting Frankenboard was cut to fit and the control panel notch was cut and shaped as well. The original design intent called for chunks of the maple to be removed so a Marshall logo could be seen through the face plate as if the jungle had over grown it. The oozing, squirming, clamping nightmare convinced me to find another way.
Utilizing the bit of carving experience gained on the failed scales I carved the logo into the maple leaving the padauk growing in front of it. I filled the logo with an epoxy and brass powder mixture and sanded the entire face plate flat. A bit of CA [super glue - a wood worker's best friend] to fill the gaps and it was hit with a black tea wash [3x] to make the grain pop then lacquered.
Step 8: Finish Time
I like to finish sand with an orbital sander - cutting in all of the round overs using 80 grit then 150 and finally 220. I generally don't grain fill as I like the complexity it imparts to the finish. Padauk is a very 'rude' wood as it tends to color everything around it. This required a staged lacquer application. I 0000 steel wooled the curly maple to clean off the orange rudeness and sealed it first. I use a brush to apply finishes as I find it easier to fix. Then the paduak was sealed. As the cab inside is exposed I sanded and finished the inside as well.
Step 9: On to the Show
The Vines amp received lots of touching & use during the three day show. Most of the comments were very favorable with the occasional 'Are you mad?' observations. As usual I do this mainly to learn and worship the beauty of nature in wood.
I already have a design idea to take the vine concept from the 2D realization of this build to a full 3D using curly maple.
Thank you for coming along on the build!
Russ
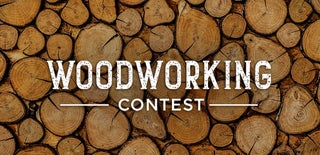
Participated in the
Woodworking Contest