Introduction: Walnut and Alabaster Sea Dragon Tobacco Pipe
Hello! This is my instructables debut, and just in time for the woodworking contest! This pipe was inspired by the beautiful sea dragons that I saw on a recent trip to an aquarium. Made from walnut and alabaster, this pipe stands at around 8 inches tall and is a real eye catcher. Although I do sell my pipes through my etsy store (www.etsy.com/shop/soapstonedpipes), this one was for my personal collection.Some of this process is adapted from Dan Miller's technique and he has an excellent step by step of one of his pipes on his website at www.dmpipes.com.This was a fairly time consuming project, but well worth it in the end. Although I do use some specialty-ish tools, this can be done with minimal tools and a lot of patience and elbow grease.
Tools:
Paper
Scissors
Planer
Mitersaw
Tablesaw
Bandsaw
Drill press
Lathe
Basic lathe chisels
Dremel with flex shaft
Dremel cutting bit
Carbide and diamond burrs
Assorted rasps
Sandpaper 60 grit to 220 grit
Assorted clamps
Benchtop vice
Tape measure
Butane torch
Materials:
Hardwood (walnut in my case)
Alabaster (or other stone, check www.sculpturehouse.com )
Adhesives and Finishes:
Ca glue
Wood glue
Beeswax
Wipe on poly
Let's get started!
Step 1: Drawing Your Design
Prior planning prevents poor performance. With some pipes that I make I will just wing it and see where the material takes me. But with a pipe this complex (lots of turns and connection points), it really pays off to take time to draw it out and think carefully about what steps to take and in what order. The end result will surely vary from the original drawing but it really helps to have something to work from.Once I have my general design finalized, I draw it full size and cut it out carefully with a sharp pair of scissors. Now we have our template!
Step 2: Gathering Materials
The next step is gathering your raw materials. I'm fortunate enough to have beautiful trees all around me and a shop stocked with some really nice pieces of walnut, cedar and oak. After some digging around I found a piece of walnut with some great grain patterns.After laying the template on it to make sure it fit, I made a few marks and brought the board over to the saw. The very end had a few splits in it so I took a few inches off the end and then cut a piece that was a few inches longer than the template so that I would have plenty to work with.I also made the choice to use a light blue alabaster that I had laying around for the bowl piece. The contrast of light stone and dark wood should look pretty cool. It's a slightly harder stone than soapstone, but still easily carved. You can also choose to make your bowl out of wood. African blackwood and briar are fairly common woods used for bowls, but there are plenty of options out there. Get creative!
Step 3: Planing
If you are working with store bought dimensional lumber you might be able to skip this step and the next one. Because I started with a 2 inch thick, rough sawn board I needed to plane it to get rid of the saw marks and get a nice flat surface to go up against the fence of the bandsaw. This also makes it so that the grain will continue all the way around the pipe.If you buy two 1 inch boards that are nice and flat you can sandwich those together instead of splitting a board down the middle. You'll see what I mean. I started at 2 inches and planed it down to 1 1/2 inches.
Step 4: Splitting on the Bandsaw
For this step I measured to find the center of the board and then moved the line over 1/8 inch from center to compensate for the air hole. This will ensure that your air hole is centered. Be sure to measure twice, cut once, and adjust your saw accordingly to keep tension on the blade to ensure a nice straight cut.
Step 5: Planing Again
Next I had to take the two halves back to the planer and took off just enough to get rid of the bandsaw marks. This is important because when you glue these two halves back together you don't want any imperfections that could cause an air leak.
Step 6: Laying Out Your Template
Now that you have your two halves you can lay out your template. Take some time and observe how the grains are running and how different patterns might affect the overall look of the pipe. In my case there was a bit of spalting (discoloration caused by fungus), on one edge. I placed the side of the pipe that will face the user on top of it so that it would be clearly visible. After playing with the position and contemplating deeply, I decided I wanted to extend one line on the pipe by about a half inch. I simply cut it and spaced it out until I was happy with how it looked. Don't be afraid to stray from your original design. Just make sure that you think through how the changes you have made might affect the process. In my case it didn't change much.Once you have your template positioned where you want, tape it down and trace it and remove the template. Make sure your lines are good and dark. I then made another line outside of the one I just traced that added about another 1/4 inch, again to make sure there is plenty of wood to work with. Once I had it traced I put the two halves back together and secured them with a few screws. Just make sure that you keep the screws away from the pipe so you can easily cut them out.
Step 7: Cutting Out the Stem
Now this step is a bit time consuming. Because I'm using a larger bandsaw, I can't just cut out the shape. I needed to make relief cuts so that the material could be easily removed as I was cutting. This keeps the saw from binding up and makes the whole process easier. Take your time, do it in sections and think about what you want the last cut to be. I wanted to leave at least one screw in for as long as possible so my middle screw was the last piece of wood to come out. And now one of the most nerve racking parts of the project is done!
Step 8: Making the Air Hole
Now that you have your rough shape cut out, it's time to make the air hole. I use a dremel with the dremel workstation, but you could also use a drill press with a cutting bit or you can chisel it out. Set the depth of the cut to 1/8 inch. I usually make my first pass on a medium speed and then slow it down to clean it up. I drew a point on each turn that I had to make and drew a straight line from point to point. Pick an end and start cutting. Don't mind the awful scream coming from the cutting bit. Take your time and don't worry if it gets a little bit squiggly. You can slow the dremel or drill press down and make a few more passes to get it smoothed out. Then I folded up a piece of sandpaper and smoothed it out further.
Step 9: Cutting It in Half
This is another step that is dependent upon your design. In my case, I knew that with this many curves it would be impossible to get a pipe cleaner through to clean it. Also, thanks to gravity, most of the gunk that builds up drips down to the lowest point. Because of this, I decided to add a cleanout right at this lowest point. I made sure that I would have at least 1/2 inch of straight air hole on either side of my cut so that I can add a tenon to hold the two halves together. Then I cut it with a small hand saw, using the reflection to help keep it at a 90° angle. This could also be done on a bandsaw.
Step 10: Glueing the Stem
Now we are finally ready to start putting some pieces together. Using the wood glue of your choice (I use gorilla wood glue, tightbond is good too), take a small brush and apply the glue to the side with the air hole cut in it. Take care to keep the glue away from the air hole so that you don't end up smoking it. Another good trick, if you don't have a ton of curves, is to use a thick piece of cotton string or bend a pipe cleaner to fit inside the air hole, wet it, and then place it in the air hole and clamp the pieces together. Once it is clamped you can pull the wet pipe cleaner or string out and it will wipe off any excess glue that might have squeezed into the air hole.Check your glue for drying times and follow them. Nothing worse than a piece falling apart while you're working on it because the glue wasn't cured all the way. Besides, there's other stuff we can do while that's drying.
Step 11: Turning the Tenon
In order to get the two pieces of the pipe to hold together, there needs to be a tenon of some kind. Some pipe manufactures use plastic ones (delrin), but there are plenty of choices out there. If you have a small enough pipe, or a big enough lathe, you can turn the tenon on the pipe itself. I had neither so I made a separate piece by taking a small scrap piece of walnut and squaring it with a table saw.You can get the table saw set up quick if you put the width of the piece of wood you want in between the blade and the fence (picture 2). Make sure to lower the blade to just above the wood (picture 3), and use a push stick to keep your fingers away from the blade (picture 4).Next I took the piece to the drill press and drilled a 1/8 inch hole through the middle. It is important that the hole is centered and that you use a good sharp bit and go slow to keep the bit from wandering. Use a vice and line the wood up with the drill bit to make sure it is straight up and down.Now that the hole is drilled we can put it on the lathe (always drill before you turn), and round it out. I used a four jaw check and a dead center on the tailpiece.Set a caliper or micrometer to 3/8 inch and use this to check your tenon regularly. If you don't have a caliper use a 3/8 inch drill bit as a guide. You want it to be a light tight fit so try to be as exact as possible with this.Once the wood was in the round I took a pencil and made a mark at 1 inch. I used a small square chisel to keep the tenon as even as possible then sanded it until it was just the right size. Once you are positive it's just right, cut it off with a hand saw or bandsaw. This actually turned out to be too short and didn't give the pipe enough stability. I made another tenon about 1 1/2 inches long using bamboo, mostly because it was late and I really wanted this part to be done before I could go to bed. No worries, I can use the walnut tenon to attach the bowl piece later on.
Step 12: Attaching the Tenon
Now it's time for some drilling. Again, this is the first tenon that I made out of walnut. In later pictures you will see the bamboo tenon. I STRONGLY recommend using a drill press for this step. As you will see, it's pretty crucial that this stuff all lines up. Clamp the pipe into a vice and line the bit up with the air hole as best as you can. Mark the depth you want on the drill bit with a piece of tape and check, double check and triple check. You want this to fit pretty perfect.Once you are confident that you have it all straight, go for it. Take it slow and be sure to back the bit out often to remove the shavings from inside the hole. This may plug up your air hole but you can clean it out easily. As you can see in the picture, my holes did not line up perfectly. Little bit frustrating, but that's why we left so much material when we cut out our rough shape earlier. There is enough wood here to shape it back and it shouldn't make a huge difference on the end result. Don't be too hard on yourself.Once you are happy with the fit, go ahead and glue it into one side or the other. Put just a tiny bead of wood glue on the tenon, not in the hole. This will keep the tenon from pushing the glue into the air hole. Again, follow your drying time and let it dry all the way. You want this connection to be finished and functional for the next step...CARVING!
Step 13: Rough Carving
Before I could start shaping the pipe, I needed to get it down to the right width. This can be avoided by planing your boards thinner in steps 3 or 5, but I don't mind sanding and like having the extra material just in case. To sand down to the right thickness I put the two sections of the pipe together and simply put it on a belt sander. If you don't have a belt sander I would suggest starting with thinner wood as I mentioned before.To get the edges rounded and get the rough shape that I was looking for, I used a variety of tools. I prefer using fairly rough rasps. It may take a little bit more effort but I find that long passes with a rasp gives me smoother lines. A dremel with a sanding disc or metal burr can be very helpful for tight corners like my mouthpiece in picture 8. Also, a flex shaft for your rotary tool is worth it's weight in gold. You can find them for a reasonable price and they make the tool much more versatile. A bench top vice is also a life saver, but be sure to use some scrap wood on each side to protect the wood from the metal vice or it can leave indentations.
Step 14: Attaching the Second Tenon
Before I started shaping the smaller section of the pipe, I went ahead and drilled and attached the tenon that will hold the bowl piece in place using the same methods explained in step 12.
Step 15: More Carving
Now with the two halves connected, I started to shape the middle where they attach, as well as the legs that the pipe will stand on. By making three legs, two in the back and one in the front, I created a tripod that will keep the pipe upright and free of wobbles. Even the most elegant pipe can become a pain in the butt if it doesn't stand up right.
Step 16: Cutting and Drilling the Stone
As I mentioned earlier, the stone that I am using for the bowl is alabaster. If this is your first time working with stone carving I might suggest soapstone. Alabaster is slightly harder and takes a bit of patience to work with. I started by eyeballing about how tall I wanted it to be and then cut off the excess. I use a diamond coated hacksaw blade. Other blades work as well but will dull very quickly.It has been my experience that it's always best to drill your holes while you still have a good size piece. I have found that if there isn't enough material around the hole that you are drilling that there is a better chance the stone will fracture and crumble before your eyes. Always drill first.Use a drill press to keep it straight and be sure to back the bit out frequently or the dust will bind up the bit and could fracture the stone.
Step 17: Rough Shaping the Bowl
Now that the stone was drilled I used a dremel with a diamond coated bit to open up the air hole to accept the tenon. I also roughly shaped the end of the wood that will connect to the bowl so that I could trace the shape onto the stone. I do this because it is much easier to get the rough shape of the bowl before it gets attached.I mainly use rasps when working with stone. Files clog up too quickly. A belt sander can also be really helpful but be sure not to go too far. You want to attach the bowl to the stem for final shaping so that you can be sure that the wood will flow seamlessly into the stone.
Step 18: Attaching the Bowl
After getting the bowl to the rough shape I wanted I attached it to the walnut tenon using ca glue. Make sure to wipe the dust out from inside the hole in the stone or the glue won't adhere. Just as before, the glue should go on the tenon side in order to keep the any glue from getting into the airway. Clamp in place and refer again to your glue's drying time.
Step 19: More Carving
While the glue way drying I continued to shape the stem. The mouthpiece was the last area to rough out. Using a narrow rounded rasp I made a spine on the top and bottom.
Step 20: Final Carving
Once the glue was fully cured on the bowl, I finished carving the stone and stem. I wanted sort of a tulip shape on the bowl so, using assorted shaped rasps, I carved away the stone until it was flush with the wood. Then I finished shaping the wood around the connection and eventually got to my final shape with 60 grit sandpaper. I then finished the bowl by using a flat, cylindrical diamond burr to add a little bit of depth. I shape the inside of my bowls so that it is conical until the very bottom, at which point I create a small recess with a hard edge so that a screen will stay in place.
Step 21: Finish Sanding
This is a tedious and time consuming step. It isn't exciting, and there aren't many pictures. I started with 60 grit and worked up to 220 grit. Make sure to get every nook and cranny. Once I had sanded up to 220, I wiped it down with a damp rag. This will raise the grain and any imperfections. Once it dried completely, I started again with 100 grit and worked back up to 220. One thing I wanted to point out is that as I was sanding and shaping the bowl, a very slight natural crack in the stone appeared. It wasn't enough to cause any kind of air leak, and I actually like the look, but this serves as a warning that anything can happen with natural materials.
Step 22: Finishing the Bowl
I started by finishing the bowl with beeswax. I did the bowl first because it involves heat and I didn't want to torch the poly finish that I planned on pouring on the wood. I started by taping of the wood so I didn't get any wax on it. Then I took a small butane torch and melted some beeswax and wiped it up with a rag. Then I took the torch and heated the stone until it was barely too hot to touch, about a minute. Once the stone was good and hot, I rubbed the beeswax over the outer surface. It should melt right on and get absorbed into the stone. Wipe off any excess and let it cool.
Step 23: Finishing the Stem
For the stem I decided on a wipe on poly. This finish is easy to apply and dries quickly so it's easy to keep it dust free. I also like using a paste finish, but it requires a lot of polishing to get a good shine. I started by taping off the bowl. Then I applied the finish with a clean cotton cloth. After it dried for about 2 hours I went over it with 220 grit sandpaper again, then applied another coat. I repeated this process once more for a total of three coats, and I think it looks pretty good! Once the finish is fully cured all that's left to do is to put a screen in it and puff away!
Step 24: You're Done!
As I said in the intro, this is my first instructable and I was motivated to document this project by the woodworking contest. So let me know what you think and if you like it, go vote for it! Also feel free to ask any questions that you might have in the comments section.This is one of the more complicated pipes that I have attempted, but the process is fairly universal. This is also not my first pipe so I felt comfortable winging a few of the steps. If this is your first attempt, try a more simple design first. There are also plenty of great pipe making instructables out there, so do some research and when it's time to start make sure you have a solid game plan. But don't be afraid to stray from your plan here and there, so long as you think it through. There are many hours in this pipe over many days, so take your time and be patient and you can make killer pipes too!
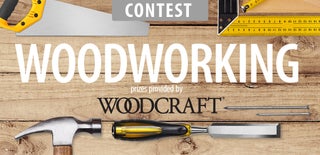
Third Prize in the
Woodworking Contest 2017