Introduction: Wedding Chest Guestbook
Asking your girlfriend to marry you is the ultimate way to say I love you. So that's what I did, and luckily she said yes. We planned the wedding more than a year after that I asked her, so there was plenty of time to do some wedding projects along the way. She made her own Wedding Dress and I designed my own cufflinks and had them printed by Shapeways. You can imagine my little project didn't take as much time as the dress, so it was time for another wedding project.
Furthermore, at many weddings and other celebrations, people have a guestbook. This book is read maybe once or twice in the weeks following the wedding, and after that the book is put away and won't be looked at for quite a while. We didn't like that, so we needed something else. Since we already got a large treasure chest in our living room and I asked her with the engagement ring in a very small treasure chest we thought it a good idea to go with a small wedding chest for a guestbook. This is the result.
Enjoy reading this Instructable.
Step 1: Inspiration
The inspiration for the wedding chest came from multiple places. Let's start with the pirate/steampunk costumes for both of us we're working on for quite some time now. Besides that we restored a nice treasure chest somewhere along the way. And because of these pirate projects I asked her to marry me with the engagement ring in a small version of a treasure chest. Both these treasure chests can be seen in the images included in this step.
We were first planning to use the chest as a box in where people could put notes. On these notes they could either write their names, best wishes or whatever they wanted to share with us. However, notes are even worse than a guestbook, you read them once en then throw them away. That's when we though about a present we once gave one of our friends when she graduated from university. We gave her a lampshade with all the names of the people who participated with one big gift instead of a boring postcard with all names. A little search on the internet and we soon found a couple of examples of the direction we wanted for the chest.
Step 2: Materials & Tools
Plenty of options on how to build such a chest, but here is a list of all materials and tools that I used for constructing the chest, so you can follow along.
Materials:
- Wood, I used 16x50mm rough sawn lumber.
- Dowels, I used 6mm of unknown material.
- Wood glue
- Chest hardware
- Handles
- Hinges
- Sheet metal 0.75mm, I made my own metal bands.
- Lock
- Screws, in the correct color, so I don't need to paint them later on.
- Chain
- Metal paint
- Wood lacquer
Tools:
- Miter saw, can be replaced by circular saw and even a hand saw.
- Drill press, can be replaced by a normal (cordless) drill.
- Clamps, make sure you have enough.
- Sanding equipment, with sanding paper up to at least 180 grid.
- Angle grinder, only used for making my own metal bands, so isn't necessary when metal bands are used instead off sheet metal.
- Hacksaw
- Files
- Screwdriver, depending on the type of screws you use.
- Marking tool, this may be as simple as a pencil.
- Measuring tool, this may be as simple as a ruler.
- Painting equipment.
Step 3: Making a Paper Mockup
Before starting on the actual build I first made a cardboard mockup to determine the size. Once satisfied with the size I drew on where and how I wanted the metal bands. And besides that I added some design elements which I will later add to the chest. Either made with sheet metal, pyrography or wood carving.
Step 4: Woodworking: Making Panels
The construction part of the wooden chest is roughly divided in two parts, creating panels and assembly. Remember to remove excess glue before it dries because it can 'soak' in the wood, creating ugly spots when a stain is applied.
Start by cutting the wood to the desired length. Make sure you cut the pieces longer than necessary such that they can be cut to length after assembly of the panels. In order to create sturdy panels, I used dowels and wood glue. The holes for the dowels were drilled using a jig I made, but it is just as easy to mark the hole positions before drilling. Probably the holes are not perfectly positioned, which means the panels need to be flattened after assembly. Once all the holes are drilled you can start assembling the panels. Make sure you use enough clamps and try to keep the panels as flat as possible during clamping.
For the curved top I used the table saw to cut the sides of the beams at an angle. Make sure you calculate the angle you need before starting your cuts. Tape was used during glue up, see the image above where the top is taped. Once all the panels and the curved top were glued I used the miter saw again to cut all the panels to length. In order to cut the top, I made an insert for extra strength during the cut.
Step 5: Woodworking: Assemble Chest
Once all the panels are cut to size a little sanding is needed as explained in the next step and after that it is time for the assembly. The chest is first assembled as a closed box and thereafter the lid is cut off. Make sure you remove excess glue before it dries, just as in previous step.
I did the glue up in three stages. First a glued the front and back to the bottom panel. This was followed by the top and finally the sides were glued on. After the glue up cut the chest in two using the table saw. Be carefull when making this cut since there is a high change of kickback. The last step is adding dowels to most panels both for strength and looks. Therefor carefully mark the positions where you want your dowels, drill the holes and glue the dowels in. Finally I added a chamfer to the front and sides of the bottom part of the chest so the metal band of the lid fits better during closing.
Step 6: Woodworking: Sanding, a Lot
This step took a lot longer than hoped. The panels I made were a lot less flat than I hoped by using the jig. This probably happened because the jig wasn't properly clamped to the drill press and shifted a little bit during drilling. I therefor needed to flatten all panels, which can be done using a thickness planer. Since I didn't have one I did it using a belt sander with a rough grid belt. All panels were flattened before the assembly, and all the sides which make up the inside were finely sanded to a 240 grid.
After assembly the top was roughly sanded to a curved top rather than the segmented look after glue up using the belt sander. The entire outside was sanded thereafter to a 240 grid.
Step 7: Metalworking: Bands
The metal band for the chest can be either bought or be made from sheet metal. I made mine from sheet metal, because this way I had more control over de desired width of the bands. On the sheet metal the bands were marked. Using a piece of a metal beam as a guide, I cut the sheets to size using an angle grinder. Once all bands were cut the sharp edges were removed using a file. Thereafter the bands were bent where necessary and holes for mounting were marked using a centerpunch and drilled. The final size of the bands were cut using a hacksaw for a more precise finish. Finally all edges were sanded to remove left over sharp edges.
Step 8: Hardware
The hardware for the chest was ordered online. We were going for black hardware but we still ended up buying rust colored hardware instead, because these looked the best (shape) in our opinion. When the hardware arrived, it turned out it was not only rust colored, but really rusted and the rust wasn't properly sealed with lacquer (guess why it was so cheap). This meant all the rust had to be removed which was done using a wire brush wheel on the drill press. Once the rust was removed the hardware was installed and in case of the hinges adjusted to fit the curvature of the lid.
Step 9: Metalworking: Front Decorations
When the rest of the chest was finished, we decided to go with decorations made from the sheet metal. A double ring logo was designed with the date of our marriage and our names in it. The logo was printed and the design was transferred to the metal. Using a fret saw the letters were cut out. A dremel with a cut-off wheel was used for roughly cutting out the ring shape. The final shape of the ring was obtained using files.
Step 10: Pre-Wedding Painting
During the wedding the guest will be writing on the chest. When written on untreated lumber, the marker lines will show run-out on the wood. To make sure this won't be the case the chest is painted with 2 coats of lacquer. Also all the hardware is finished before the wedding, this includes the hardware and the metal bands. When painting, make sure to read the instructions for optimal painting conditions. Once everything is painted, the chest is assembled.
Step 11: Wedding Preparations
Now we only need to make sure our guest know what to do with the chest. Therefore we made a manual which we printed for the guest to read. Also we made sure one of our masters of ceremonies would keep an eye on the chest if someone didn't quite understand what we had in mind.
We also lined the chest with narrow tape. The tape constructs area's which the guest should fill. First we calculated the space on the chest and divided that space by the amount of people who should write on the chest. This was approximately 27cm2, so we printed out a bunch of rectangles 3cm by 8cm, a little under 27cm2. This way we made sure we could fit enough rectangles for our guest such that some areas remained unfilled for extra decorations after the wedding. The chest was filled with the rectangles and finally lined with the tape.
Lastly, we made a 'How to DIY your wedding book'. We initially made this book because my wife made her own wedding dress and she wanted to show everyone how she did it. But since we were making such a book already we decided to include most of the wedding DIY things we made. I included the images from the book to the end of this step.
Step 12: Get Married
The most fun part? Yes, definitely.
Just make sure the chest is put somewhere where the guest will be and that they are aware they need to write on it. Our masters of ceremony took care of these tasks. See the images for yourself how our wedding turned out.
Step 13: After Wedding Finishing Touches
At some point on your wedding day the fun comes to an end. The drinks have been drunk, the feet are tired and if everything went according to plan, the chest has largely been filled. For some reason everyone had the same idea on where to put there names on the chest. So the extra space we had counted on was all in approximately the same spot. We initially had in mind filling the blank spots with hearts, butterflies, etc. But due to the large area to fill in one spot, that wasn't really possible anymore. So we decided on putting some of the element of our wedding silhouette cake on the chest.
The cake was mainly designed by ourselves, so we had images of most of the silhouettes on our computer. We printed the ones we wanted on the chest in the size we wanted them and transferred them to the chest using carbon paper. Once transferred, we used the markers to draw them on the chest. Optionally you can spray lacquer the chest after being finished with all the drawings. If you do it make sure to use spray lacquer, otherwise you maybe blur the marker.
Step 14: Finished Wedding Chest Guestbook
And that's it all finished. Thanks for visiting my Instructable and happy building.
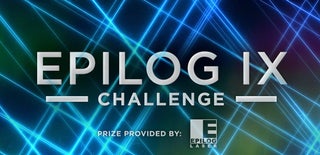
Participated in the
Epilog Challenge 9