Introduction: Whiskey Barrel Bar Stools
Sun and weather take a toll on outdoor furniture. I had four outdoor bar stools covered with plastic resin wicker that had cracked and split. I priced new outdoor bar stools, ($75 and up x 4.) I figured I could renovate my old stools for about the price a single new chair. The plastic wicker had to go, but the powder-coated steel frames still looked good. I repurposed an old whiskey/wine half-barrel to provide all the material for the seats, backs and bracing. If you are even a little bit handy, possess basic wood working skills, and have some ordinary tools, you can knock this out over a couple of weekends. I wound up with great looking and very serviceable barstools from a single half-barrel and a hand-full of screws.
Step 1: Remove Resin Plastic Wicker
You can see how the plastic had cracked and split. I cut away the plastic wicker from the barstool frames using a utility knife; taking care not to scratch the powder coating.
Step 2: Materials List
• 1-Oak Half Barrel w/ Hoops
• Barstool frames (up to 4)
• Zink Coated Phillips Screws (per barstool)
14 - #10 x 1-1/2” Oval Head
8 - #10 x 1-1/4” Pan Head
9 - #12 x 5/8” Pan Head
• 1 qt. 'Spar' exterior polyurethane - oil based
• 1/2 pt. Wood Stain - oil based
• Sandpaper - Belts (80 grit)
• Sandpaper - Sheets (120 & 220 grit)
Optional *
* 1 pt. Rust Remover (for barrel hoops)
* 1 qt. Wood Bleach (oxalic acid)
Step 3: Tools & Personal Protective Equipment
• Circular Saw • Belt Sander
• Electric or Cordless Drill • Palm Sander
• #2 Phillips Bits and Holder • Jig Saw
• 7/64” & 1/8” Steel Drill Bits • Hand Saw
• Angle Grinder • Hacksaw
• Utility Knife • Sanding Block
• Wood Chisel • Wood Rasp
• Rubber Hammer or Mallet • Quick - Clamps
• Tape Measure • Torpedo Level
• Steel Brush • Long Handled Scrub Brush
Use the correct PPE (safety equipment) to prevent injury
• Dust Mask • Long Sleeve Chemical Resistant Gloves
• Face Shield • Hearing Protection
• Safety Glasses • Disposable Gloves for Staining
Step 4: Disassemble the Barrel & Barrelhead
The first thing I did was to pull out the barrel staves, taking care not to damage the hoops or barrel head. The barrel head was also made of oak sections that had been put together with dowels. Because the barrel was empty and allowed to dry out, it came apart easily. The dowels were pushed into the holes and cut flush. I sorted and stacked the staves by size.
I did a mock-up to determine the count and placement of staves to get an idea of the positioning and proportion. I settled on using three of the larger staves for the back and five smaller ones on the base. I needed a total of 32 staves to do the four chairs and there were only 30 in the barrel. So I ripped the two largest staves in half with a circular saw.
Step 5:
A clamping worktable held the uneven staves securely so I could sand off the charring. The belt sander and 80-grit sandpaper made quick work of this part of the project. Be sure to use eye and hearing protection as well as a dust mask when doing any sanding. I did all my sanding outside to make cleanup easier. What sawdust the breeze didn't take away, I blew into the lawn with a leaf blower. Just how much charring you ultimately take off is up to you; but at least remove all the loose bits. I sanded off nearly all of the char.
Step 6: Prep the Hoops
I wanted to use sections of the barrel hoops to maintain a rustic look and provide additional bracing for the back and seat. The barrel hoops had powdery red rust covering both sides. I needed to remove or neutralize the loose rust so that the polyurethane would better adhere. I coated the hoops with a rust removing gel and worked it into the metal using a steel wire brush. Warning! This chemical is acid! Follow the instructions on the container! Use heavy rubber gloves; both eye protection and a face shield. I let the hoops sit and after about an hour (or however long it took me to sand the staves.) I used plain water and the steel brush to clean-off the gel. I dried the hoops thoroughly with an old rag.
Step 7:
I used a coarse plastic-bristled brush to work wood bleach into each stave. The main component of the wood bleach is oxalic acid; commonly used to remove stains and weathering from outdoor wooden decks. Warning! This chemical is also acid! Follow the instructions on the container! Use heavy rubber gloves, long-sleeves, eye protection as well as a face shield to prevent burns! After letting the bleach work about 30 minutes, I rinsed the surface with plain water and let dry. The bleach removed most of the weathered gray color, but it hardly touched the black stains left by the steel hoops. You can eliminate this step depending on how you want the finished surface to look. You could just sand everything down to the bare wood. Or if you want to keep the patina as is, lightly sand the surface and after removing the charring, apply an exterior (spar) polyurethane.
Sanding down the the bare wood and protecting the surface with with a clear finish will give you a rich honey colored surface.I used a palm sander with 120 grit sandpaper to smooth out the back and prepare both sides for staining.
Step 8: Braces for Seat and Back
The staves were too short to span the full length of either the seat or the back. With a jigsaw, I cut cross braces from the barrel head pieces. I positioned the back brace about ¾ of the distanced from the top and the seat brace roughly the same distance from the front. I sanded, prepped and stained all sides.
When I did the mock-up, I saw that I needed to notch the stays for the seat-back to get a solid fit against the cross-brace and also sit flat against the curved back. I cut a tapering notch into the seat-back side pieces and took 3/8” out of the center stave (now repurposed as chair slats.) I used a handsaw, a wood rasp and a wood chisel to cutaway the wood a little at a time until I go a good fit.
Step 9: Stain and Finish
After a quick once-over with a tack cloth to remove any remaining sawdust, I brushed on a dark walnut oil-based stain; wiping off the excess with an old t-shirt. I let the stain dry overnight before applying a thin coat of oil based exterior spar polyurethane. I recommend using either the semi-gloss or satin finish. Stir the urethane often or the solids used to de-gloss the finish will stay on the bottom of the can. Don't shake the urethane; it causes bubbles and will ruin your finish. It took only a few hours for the first coat to dry. I roughed up the surface with a 220 grit on a hand sanding block and applied another light coat of polyurethane finish. The second coat also dried very quickly. You could shorten application and dry times by using a combination stain and varnish aerosol spray.
Step 10: Attaching the Barces
When the pieces were dry, I attached the seat and back braces using #10 x 1-1/2” oval head screws; one at end of the each brace. I used quick clamps to hold the braces in place. For the back-brace I angled the screws from the top of the brace into the steel frame. The seat brace was attached by angling the screws from the front into the steel frame. I held the braces in place with quick clamps while I drilled the 7/64” pilot holes and attached them. Drilling pilot holes will prevent the screws from splitting the oak.
Step 11: Attaching the Back and Seat Slats
The slats designated for the seat backs were attached to the frame with one 1-1/2” x #10 oval head screw at the top and one 1-1/4” x #10 screw through the back brace. Again quick clamps were utilized to hold the slats in place while they were being fastened. The seat slats were attached from the bottom to hide the screws 1-1/4" x #10 pan head screws. The outermost seat slats were attached to both the brace and the metal frame with the 1-1/4" x #10 screws.
I cut the hoops to fit with a hacksaw and used a metal file to remove any sharp edges. Each piece was attached with three 5/8” x #12 pan head screws; two sections for the back and one on the seat. Using an angle grinder, the screw heads were ground flat to look more like rivets. A piece of 18 gauge sheet metal with a hole drilled the diameter of the screw-head was used to protect the surrounding area while the grinder did its work.
Step 12: Ready for the Patio Party
I now have four refurbished bar stools that are surprisingly comfortable and will hold up to the elements. The half barrel sells for about $30 at one of the big box home improvement centers. Adding in the screws, stain, polyurethane and other materials I spent less than $80.
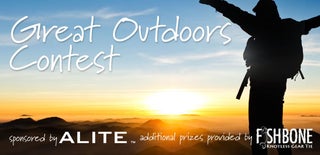
Participated in the
Great Outdoors Contest
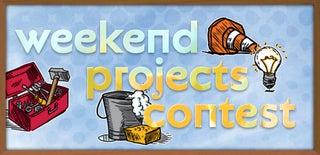
Participated in the
Weekend Projects Contest