Introduction: Wood Lathe Duplicator With Angle Grinder
This Lathe Duplicator was inspired by The Homestead Craftsman, and his video entitled Homemade Wood Lathe Duplicator using an Angle Grinder. The differences in the designs are the type of cutting blade, table top and pattern mounting method. The goal of this design was to create turnings with finer detail and less clean-up, as well as adding versatility and adjustability to template mounting on the table top.
Step 1: Operation of the Duplicator
The Angle Grinder Assembly is assembled with the center line of the arbor at the same level as the center line of the lathe, and the rotational axis parallel to the bed of the lathe. An adjustable follower is attached to the front of the Angle Grinder Assembly, and calibrated to be inline with the cutter as seen in the photo.
A table with a steel top is bolted to the bed of the lathe between centers. The steel provides a smooth surface for the duplicator to slide over, and the steel provides a magnetic surface for the Magswitches on the template mounts. The bottom should be waxed with paste wax to reduce friction.
Patterns are one half of a full scale profile split on its center-line, printed on paper and glued to 3/16" (5mm) plywood. These are attached to a template mount with screws, and positioned on the table in relative to the stock location between centers as well as the center line of the lathe. Finally, the template mounts are locked into location with the Magswitches.
Loosen the handle on the follower, and adjust the depth of cut turret to the highest setting. Move the follower until the calibration screw contacts the depth of cut turret and tighten the handle again. The duplicator will work if the lathe is turning in the forward direction, but I recommend running the lathe in reverse. Now, start the lathe and adjust the speed to 650 RPM. This is the recommended speed suggested by the manufacturer of the cutter. Next, start the Angle Grinder, and begin taking cuts on the stock. Follow the edge of the template, and work the stock down slowly in the deep sections of the template. After each pass, stop the Angle Grinder and adjust the depth of cut turret to the next level, and make another pass.
Roughing the stock is much easier and safer if shims are used to guide the duplicator along the piece to remove only the desired depth of cut. The best results are made with a slow steady movement, and less aggressive material removal.
WARNING!
The cutting blades recommended for this project are very aggressive, and can remove a lot of material at once. You must, and I repeat MUST remove the material slowly and with shallow passes, or the blade could grab and cause some damage to the work piece OR worse yet - YOU. Hold the duplicator (Angle Grinder Assembly) with both hands against the table while cutting.
Step 2: Parts and Materials
Angle Grinder Assembly with Template Follower:
- 1 ea Carbide Cutter for Duplicator D-15-90-5 - Viel Tools, Inc. OR
- 1 ea King Arthur's Tools 45822 Lancelot 22 tooth, 5/8" center hole
- 1 ea 4-1/2" Angle Grinder
- 1 ea Press-Fit Ball-Nose Spring Plunger - McMaster Carr
- 1 ea T-Slot 5/16"-18 1-1/2" - Rockler
- 1 ea Plastic Two Arm Knob 5/16"-18 - McMaster Carr
- 1 ea Spring - 1/2" Height
- 1 ea #10-24 Screw 1-1/2" with Flat (Countersunk) Head
- 1 ea #10-24 Screw 1" with Pan Head
- 1 ea #10-24 Nylock Nut
- 1 ea Washer for #10-24 Screw
- 1 ea Threaded Insert - Brass - #10-24 - Woodcraft
- 2 ea Cable Ties 10"
- Universal T-Track - Rockler
- Plywood 11/16" (18mm) thick
Materials for Template Mounts:
- 3 ea (Minimum) MagSwitch - MagJig 150 Switchable Magnet - Woodcraft
- 3 - 4 ea Threaded Insert - Brass - #10-24 per Template Holder - Woodcraft
- 3 - 4 ea #10-24 Screw 1/2" with Pan Head
- Sandpaper 100 grit - enough to cover bottoms of Template Holder
- Plywood for Template Holders should be 3/4" (19mm) thick to accommodate the MagSwitch
- Plywood for Templates should be 3/16" (5mm) thick
Materials for Table Tops:
- 3 ea Carriage Bolts 3/8"-16 8"
- 3 ea Fender Washers 3/8" - 1-1/2"
- 3 ea T-Nut 3/8" x 16 - Woodcraft
- 3 ea Wood 30 x 35 x 200 mm
- Plywood 11/16" (18mm) thick
- Plywood 19/32" (15mm) thick
- Melamine White Panel 3/4" (19mm) thick
Step 3: Angle Grinder Assembly
This design uses 11/16" (18mm) plywood, and could easily be constructed with 13/16" or 3/4" plywood as long as the plans are modified accordingly. The goal is to mount the angle grinder at the proper height and orientation, and secure it firmly in the cradle of this assembly. These plans were designed to fit a Makita Model 9557NB Angle Grinder. Therefore, the cradle size and shape will vary depending on the manufacturer of the grinder.
All of the pieces are butt jointed, glued and screwed to each other. The last piece to attach to the assembly should be the 70 x 62mm block that bolts to the angle grinder as seen in the photo. The bolt hole in this block is at an angle of approximately 80º, and should be drilled and fitted before securing the block to rest of the assembly.
The middle support was initially designed to use metal hose clamps, but switched to cable wraps which secure the grinder adequately in the cradles along with the bolt mentioned previously. Therefore, you may have noticed a metal support along the top of the middle to reinforce the pressure from the hose clamps. This metal support shouldn't be necessary unless hose clamps are used.
Note: See the following step about drilling the holes for the turret assembly.
Step 4: Follower and Depth of Cut Turret Assembly
The STL files for the follower and three turrets can be found at Wood Lathe Duplicator Components on Thingiverse. A dust shield (highly recommended) for the angle grinder is also available Dust Shield for Makita Angle Grinder.
After printing the parts, use a #10-24 tap and thread hole at the rear of the follower. Screw the #10-24 Nylock nut onto the 1-1/2" #10-24 Screw with Flat Head. Next screw this into the back of the follower. This screw will be adjusted after the turret has been mounted.
Drill a 3/8" pilot hole for the threaded insert 21mm above the center of the T-Slot. Drill a 1/4" hole for the ball-nose plunger 34mm above the top of the base and 13mm from the edge as indicated in the photo. Drilling these holes can be done after assembly, but it will require long drills. Chamfer the 1/4" hole so the plunger will sit below the surface a small bit. Next, screw the threaded insert into the hole until it is flush with the surface.
Assemble the turret, spring, washer and screw, and screw it into the threaded insert. Adjust the screw until the turret rotates and snaps into position.
Step 5: Alignment of Follower and Cutter
Mount the angle grinder so the cutter is 15mm forward the edge of the base. Temporarily install the follower and align it with the forward edge of the cutter. Position the duplicator on a flat surface facing you, and with the use of a square adjust the position of grinder until it is vertically aligned with the follower tip. Secure the grinder in place with the bolt and cable clamps. After assembly and installation of the follower and depth of cut turret, place the turret at the lowest position and position the flat head screw of the follower on the lowest position of the turret as seen in the photo. Next, adjust the flat head screw on the back of the follower until the tip of the follower is in alignment with the tip of the cutter. Tighten the Nylock nut on the flat head screw to secure it in place.
Step 6: Table Top Assembly
Thus far, I have two table tops. The smaller table is 610mm x 450mm x 19mm, and the larger base is 712mm x 450mm x 19mm, and uses four Magswitches.
The tables are constructed of 3/4" Melamine board, which was the flattest and largest piece of scrap sheet good that I had in the shop. All of the support fixtures on the underside of each table are constructed of plywood. The smaller table (pictured above) was constructed of three pieces joined together to form a couple of wings on the side to give me more table surface to support the grinder, and a wider variation of work piece lengths. These tables should be made of one solid piece to maintain flatness. The top of these tables has a sheet of 16ga steel contact cemented to the surface for use with the Magswitches. The tables are mounted to the lathe bed with a piece of plywood that fits tightly in the slot between the lathe bed ways.
The head of each 3/8"-16 8" long carriage bolt slips into and locks in the slots on the bottom of the table. The table is lowered onto the bed of the lathe with the bolts suspended beneath. The wooden braces are slipped onto each bolt followed by a washer and the plywood nut assembled from the 70mm round plywood piece and one T-Nut 3/8"-16. Tighten each of the plywood nuts as seen in the photos.
Step 7: Template Mounting Assembly
I use a different size template mount for each table size. One large (710 x 85 x 19mm) template mount with holes for four Magswitches, and a small (460 x 85 x 19mm) template mount with three holes for Magswitches. The layout of each template mount can be seen above. The 3/8" holes are for the #10-24 Slotted Threaded Inserts. These provide a means of securing the template firmly to the mount.
The small 40 x 20 x 5mm blocks on top of the mounts will register the location of the template on the mount while marking the hole locations from the back side with an awl or using #10-24 Transfer Screw Set.
The bottom of each template mount is covered with 100 grit sandpaper to assist in the adhesion of the mounts to the steel table tops and prevent movement. Contact adhesive (3M Super 77 Spray Adhesive) was sprayed on the back of the sandpaper, as well as the back of the template mounts after using painters tape to mask the holes and edges. Per adhesive manufacturer drying time, the sandpaper was applied to the back and trimmed for a "permanent" bond. Holes were cut in the sandpaper for the Magswitches and the Threaded Inserts as seen in the photo above.
Step 8: Templates
If the you're building period furniture, one book I highly recommend is Furniture Treasury by Wallace Nutting. This book is readily available (used) on Amazon for a few bucks, and is full of working drawings that can be scanned, scaled and printed full size. I use BigPrint by Matthias Wandel at Woodgears.ca. There are other means of printing full scale such as SketchUp and other software, but I am not familiar these methods.
Once the full size print is assembled (if necessary), glue it to the surface of 3/16" (5mm) plywood with contact adhesive (3M Super 77 Spray Adhesive) per manufacturers directions. When glue has dried cut along the edge of the pattern (leaving the line) with either a jigsaw, coping saw, bandsaw or scroll saw. The edge of the template should be sanded or filed to the line, and all rough areas and saw marks should be removed.
The width of the template must allow all front edges of the template that contact the follower to overhang the template mount. Therefore, the narrowest section of the template must be greater than 35mm from the back edge. Increasing that to 40mm would allow for sawdust accumulation.
As mentioned previously, center the template on the mount against the 40 x 20 x 5mm blocks on top. This will register the location of the template on the mount while marking the hole locations from the back side with an awl or using #10-24 Transfer Screw Set. Drill the holes with a 5mm (#9) drill for a tight fit. Use 3 or 4 #10-24 Screws 1/2" with Pan Head to secure the template to the mount.
Step 9: Template Mount Alignment to Lathe
There are at least two (maybe more) methods of aligning the template & mount to the lathe. The first method uses a piece of square plywood (1/4") with a height greater than or equal to the height of the spur on the headstock and tailstock. A corner of this jig is cut out with a height equal to the height of template + template mount, and a depth greater than the depth of your largest template ~50mm. This vertical edge of this jig is aligned to the center of the spur on the head or tailstock, and with the Magswitches OFF move the template until the center-line of the pattern is in alignment. Lock the Magswitches, and you're set.
The second method uses a collet chuck in the tailstock, and in the example above the collet chuck is used in the headstock as well. In these examples, the pattern depth at the tailstock was 1/2", and the headstock pattern depth was 5/16". Therefore, I inserted the shank of 1/2" router bit in the tailstock, and placed a square on the table and against the shank of bit. I move the template until the edge of the template touched the front edge of the square. I performed the same procedure with headstock except with a 5/16" Drill bit mounted in a collet chuck. The tape seen covering the shanks of the bits was to add a little extra material to be removed latter during sanding.
Step 10: Tool Rest
A tool rest is a must for this duplicator. I experimented with two types of tool rest, and found the one with an old tool rest base (banjo) was much more versatile. It provided the ability to adjust the tool height where as the other was fixed. Each of the versions utilized a base with Magswitches which provided excellent stability.
The adjustable tool rest consist of a banjo mounted on a 200 x 230 x 18mm plywood base with two holes for Magswitches, and 100 grit sandpaper glued to the bottom. I purchase the banjo for another project many years ago, and at the time it wasn't very expensive. Recently, I priced a similar banjo for $85. Fabricating an adjustable tool rest out of wood shouldn't be to difficult.
Plans for the fixed height tool rest can be seen above. These plans are for the one pictured above, and constructed with the wood I happened to have on hand. It is also designed for the center height of my lathe (JET Model JWL-1642EVS).
Step 11: Results
I've had mixed results with this method of lathe duplication, but overall I am satisfied and still use this device. My expectations were high. I hoped to duplicate intricate turning details, but found this technique produced chip-out on details such as a quarter rounds, beads and v-grooves. It should be noted at this point in time, the only species of wood I've used thus far has been hickory/pecan which is notorious for chip-out. I hope to get better results with hard maple, but my expectations are much lower now. Avoiding chip-out required a modification to the templates with epoxy glue to fill in the areas of vulnerable pattern details.
The intricate details are completed with regular woodturning tools, and the use of a tool rest and banjo that can be Magswitch mounted to the table. One of the greatest benefits is the ability to create many pieces that look identical with a little extra hand turning and sanding. Several years ago I built a four poster bed, and each post is a little different. Most people won't notice, but I always will.
I mentioned the King Arthur's Tools 45822 Lancelot 22 tooth cutter in the Parts and Materials section, but I do not have any experience with cutter. One reason I didn't use the Lancelot was the width of the kerf and it would require sharpening more often than the carbide Viel cutter. I've seen the results of this cutter in several videos (for example The Homestead Craftman), and the finish looks satisfactory. This cutter cannot reproduce detail either as a result of the kerf size. I choose the Viel Cutter because it was used on a commercially available Lathe Duplicator at the time I purchased it...So, it must be great. Right?! Currently, this duplicator and Angle Grinder Attachment don't appear to be available...Enough said. The Viel Carbide Cutter is still being sold, and is still very expensive.
I would recommend this device if you have the need to reproduce several identical turnings. But, don't expect a perfect finish after the final pass. However, the finish is good enough to refine in a short period of time with sandpaper. The proof of the results can be seen in the 60+ spindles I produced. I am extremely satisfied. More information about how I turned these spindles can be found at Woodturning Slender Spindles.
Finally, build and use this device at your own risk. Firmly hold the duplicator, and remove material slowly. Use shims as shown above to help size the piece.
Enjoy!
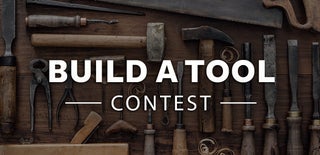
Second Prize in the
Build a Tool Contest