Introduction: Wood and Acrylic Knife Box
We made a custom CNC knife box out of wood and acrylic! We also played with fire...
- Rockler Hidden Barrel Hinges https://amzn.to/2MbDmRZ
- Rockler Small Piece Holder https://amzn.to/2toGhyU
- Magnets https://amzn.to/2M7HRg5
- Acrylic sheets https://goo.gl/Hn2j3R
- Padauk https://goo.gl/eo9K14
- Cherry wood https://goo.gl/JHPnPY
- X-carve https://goo.gl/dBvSAL
- Walnut https://goo.gl/n1HcdF
- Router Table Stand https://amzn.to/2yvTmMw
- Router Table Top https://amzn.to/2JUgg5u
- Router Table Accessory Kit https://amzn.to/2to58mo
- Router Table Dust Collection https://amzn.to/2MIqSC8
- 3d Printer (Taz6) https://goo.gl/oPZBwm
- Matterhackers Black PLA https://goo.gl/BB6jkr
- Shop vac http://amzn.to/2pPPgcO
- Wall dust collector http://amzn.to/2oQA92P
- Ceiling mount filtration http://amzn.to/2oQp1TO
- Shellac http://amzn.to/2oYGSUx
- Natchez Solution wood oil http://amzn.to/2uDQ3zM
- Super glue http://amzn.to/2pbcXeH
We really loved being able to create such precise and custom knife boxes. Making the boxes on the CNC made that level of precision possible, but if you have more woodworking skills than us you could probably do it using non- digital fabrication means. I think one of the key elements of this box is the hidden barrel hinges. They’re so small and not visible from the outside - though we actually like that with the clear acrylic version of the box we can see them! It was fun being able to make a jig that allowed us to run multiple boxes so we could try different combinations of wood, acrylic, etc. Also, any project that lets us use neodymium magnets is a win already.
Step 1: Design
We designed this in Fusion 360 live on Twitch. Here was the general process
- model a simple box half the height of the final box
- draw an outline around the knife (we already had a 3D model) extrude subtract down into the box
- model holes for hinges and magnets
- mirror the box against the top face to get the other side
Our followers suggested that we start with 3D printing to save some time and material cost which we thougth was a pretty great idea!
Step 2: Prototype With 3D Printing
Here are the thing we learned from the 3D printed prototype:
- The magnets we modeled the holes for were way too strong
- The general size and fit was good
- The dimensions that came with the hinges were different from what we measured
Before we did anything in wood we also went ahead and did some more tests with magnets and 3D printing to figure out the right strength to use. We settled with one that is 1/8" thick instead of 1/4" like the first ones.
Step 3: Test Fit and Iterate
With the magnets adjusted and the holes for the hinges deeper we went on to make our first wooden box on our CNC. We used our t-track clamps to hold the raw material down which has been one of the best upgrades to our x-carve. Well... honestly it's the only real one we've made but we love it. We have a video on it here:
After rounding over the edges on our router table and adding the hinges this is what we learned:
- We had originally designed it with a lip to help with opening (you can see it in the early prototyping. Turns out we didn't need it to open the box, so we removed it.
- The holes for the hinges need to be even deeper
- The hinges: they are cool :)
(But seriously, they are installed without any adhesives and expand with some set screws so they are reusable and super easy)
Step 4: Get Fancy
So a few things we did to get fancy:
- engrave logos
- use fancy wood
Looking at this list now I'm realizing we didn't get super fancy. Which why I'm glad we didn't stop there. We made some out of acrylic too!! WHAT?! That's pretty fancy but what's even fancier? Flame polishing it. I should probably stop here. That is best experienced in video form with Evan's evil genius laughter so check out the video at the beginning if you haven't yet.
One tip we have for carving is to make a fixture to repeatedly hold your boxes so you don't have to re-zero your CNC. To program the carving we used the v-carve feature in Easel but for the box we made our own g-code in Fusion 360. If programming your own more complex toolpaths is something you're interested in you should check out our CAM video here:
Step 5: Send Some to Your Friends!! (and Heroes)
We made extra boxes for the knives we made for our friends we've made videos with. Evan also had to make one for his maker hero: Adam Savage.
Hope you enjoyed this tutorial!!
If you wanna see more projects we've made, you can check out our YouTube channel or find us on Instagram at @evanandkatelyn. This post contains affiliate links - thanks for the support!
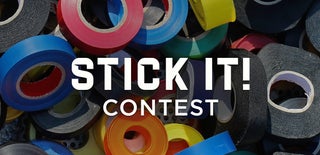
Participated in the
Stick It! Contest