Introduction: Xylano. Piano Meets Xylophone
So my daughter loved this little toy piano that used xylophone bells to make sounds, and this got me thinking....could I make a better one? The answer was yes, but it took quite some time and a bit of trial and error.
The first thing I did was start looking at piano actions and how they work- most of which were too complicated and had features that were just needed for strings. However, I eventually stumbled across the pianoforte, which is an early style of piano played by Bach and Beethoven. My first attempt in picture 4 did not work. I quickly learned that I was going to have to be much more precise if this was going to work properly. I found a good photograph of just the action, and from this picture I made a scale drawing in audocad to get the above plans. The last picture shows the working model built off of these plans.
Step 1: Materials and Tools
I bought a nice maple board from the lumber yard, also a 3/4 inch sheet of birch plywood, and a 1/2 inch of birch plywood. The xylophone was bought used off Amazon after losing two auctions, and almost a third. I never knew there was such a competitive market for a used xylophone! The tools I used were a drill press, table saw, circular saw, miter saw, band saw, belt sander, and various hand tools.
Step 2: The Keys
Making the keys was straight forward. The most important consideration was having everything measured properly- including the saw kerf. Once I started ripping the individual keys, I did not reset the guard until they were all finished. This ensures each key is uniform. I would recommend having a good blade for your saw, because the maple is very hard and will start to burn with a dull blade. The arm that holds the hammer was a bit harder to make- mainly due to me not having a Dado blade to cut the slot. So I used the band saw, and with some patience they came out right. I set a jig clamped to the drill press so drilling the holes would be uniform.
Step 3: The Hammer
The Hammer was a bit harder due to some of the complicated angles. However using a protractor, and a bit of geometry, I was able to get the angles right. Next was to rip the individual hammers out and cut away the excess using the band saw. I set up another jig to drill the holes & for drilling the wooden balls used as the striking surface. Finally to attach the hammer to the key, I used finishing nails with both ends cut off and epoxy to hold it all in place.
Step 4: The Catch
The catch was done in the same way. I did use the table saw and multiple passes to cut the channel, and then the same nails and epoxy to secure them. A jig was used to drill the holes on both the catch and the catch base to make sure all parts were uniform.
Step 5: The Deck
To mount the keys to the deck, I used the same nails that were used for the hammer and catch. The pivot point is a dowel cut in half, and the padding is there to quiet the action so all you hear is the bells. The back stop will determine how far you can depress the key. The chanel cut in the back of the deck is for catches to be mounted in, and for their pivot point to be level with the top of the deck. There are two pins that hold each key, and the spacing was the biggest problem to overcome. The point where the hammers rise when the key is depressed is the same across the board. The Xylophone bells are different sizes, and this means the center where they need to be struck will not be a straght line across the deck unless they were mounted on an angle. Once the Xylophone is mounted on an angle it changes the distance between the center striking points. To find my new center to center of the bells, I made a 1 to 1 scale drawing of the Xylophone. By drawing a line from the center of the smallest bell to the center of the largest bell, I was able to determine the center to center distance of the bells in their finished mounted position. This measurement was then used to mount the pins on the deck.
Step 6: Putting Things Together
To set the keys I first made a another jig to drill the holes for the pivot and the forward pin. This ensures that every hole is the same for every key. Next I modified the jig to allow the holes to be redrilled at a slight angle, and this allows the key to pivot back and fourth. At this time I numbered each key because many had to be slightly adjusted so as not to catch the pins they were on. After each key played smoothly, I set the catch for each key in the channel that was cut in the base. Rubber bands were used to pull the catch towards the hammer on the back of the key, on a real pianoforte this is done by a leaf spring. But rubber bands are cheap, easy to replace, and easy to fine tune to get more or less force by using a bigger or smaller one. I had some African mahogony from another project that I turned into key toppers. They were finished with danish oil and buffed with a finishing wax. I used trial & error to find the height that would be best for the bells to be hung above the deck. Finally, when the bells were hung, I was able to fine tune the action by sanding the catch, the hammer, or using a different combination of rubber bands. Once it played smoothly, it was time to design and build the body.
Step 7: Building the Case
For the case I used 1/2 inch birch plywood. I started by cutting out all four sides, and then attaching a 1 inch strip of 3/4 inch plywood. This strip allowed me to screw from the top of the deck into the strip and would hide all the screws. On the back and front where the boards would overlap the plywood was ripped down to just the top layer, thus hiding the end grain. Bracing blocks were glued into the back two corners for extra support. I then ripped strips of just the top layer of the birch plywood and used it to hide any exposed end grain. The legs are poplar, and a Dado blade was used to notch the wood so they could be put together using glue only.
Step 8: Building the Top
I no longer had a piece of half inch plywood for the lid, due to a mistake, so I joined to pieces with a biscuit joiner, glued, and clamped. I then finished the lid the same way to hide the end grain. The front was a bit trickier, because I wanted to be able to remove it to work on the inside if needed. I made some wooden latches, (shown in picture 4) similar to what you would find on a picture frame. This not only holds the front on tight, but makes it very easy to remove. Once the front was on, I positioned the lid and attached it with a continuous hinge I had left over from another project.
Step 9: Finishing
Before I started sanding, I used wood filler to fix any gaps. Most of the gaps were made when gluing the strips to hide the end grain. The filler worked well and once it was dry it was time to sand a whole lot. When I was happy with the final look, I started staining.
Step 10: Finished
Finally done! It took me a about a year and a half to finish, and I did so the day before Christmas. It was, however, a very much on again/off again affair. I never built anything into the design to hold the lid up due to fear of my little girl letting it down on her fingers. I may add that at a later date when she's a bit older. Even with the lid closed, it is still quite loud though. So long story short, I won Christmas at my house this year. :)
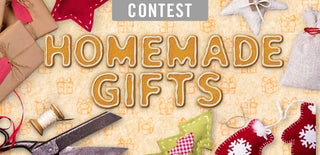
Participated in the
Homemade Gifts Contest 2015