Introduction: Your Brain on Pier 9: CNC Milled Corian
Towards the end of my residency at Autodesk / Instructables @ Pier 9 I got inspired to create a piece about the residency at the pier and how it affected me. If you haven't heard of the Artist-Rn-Residency Program at Pier 9, check out this video that summarizes what it's all about!
When I started the residency, my brain was overwhelmed with stimuli and what was possible at the pier. In addition to having all the tools / toys an engineer / designer / artist could dream of, the people at the pier are some of the most inspiring individuals I've ever met. Conversations at the pier tend to be mind blowing, informative and comical! Ideas are turned into prototypes in hours.
Ideas and projects evolve rapidly through feedback and insight through the making process. Sometimes, you end up talking more than making, but thats okay, because eventually when you end up making something, its usually out of this world. After you've spent enough time making at the pier, your mind will forever be altered and will never be the same.
For my final piece at the pier I created a visualization of a brain on pier 9. I used output from a reaction diffusion visualization to create a brain like 3D surface. In this instructable I'll describe my process and show the steps involved in making sculpture!
Step 1: Visualization & Metaphor
I used the same application that I made for my 3D Printed Reaction Diffusion Patterns instructable to visualize how pier 9 affects your brain. I seeded the reaction diffusion process with a rendering of a brain (which I made by downloading a model of the brain and rendering it Maya).
The video above shows the visualization as it evolved over time. First, you can see new wrinkle and folds form after the reaction diffusion process is seeded by the photo of the brain. To me this represents what happens to your brain when you get to the pier. Your brain explodes and expands as you learn and interact with the people at the pier. Then the video shows the process reaching equilibrium. This represents your brain adjusting to the new environment and its constant flow of inspiration and knowledge. Then the video shows wrinkles and folds forming and branching inside. This is your brain internalizing and growing and creating new ideas and forming new perspectives on what is possible. Finally, the entire space is covered with folds and wrinkles. This represents how you've become part of the pier and its community of people who inspire and make.
Step 2: Surface & Solid Creation
After the visualization reached equilibrium, I pressed the EXPORT button in the Great Scott Application. This created a MEL Script. I ran the MEL script in Maya. Then selected the curves (made by running the script) and lofted (Surfaces -> Loft) them. Then I selected the surface and exported it as an IGES file (you might need to load IGES Importer / Exporter the plugin if you don't see the option for IGES). To enable the "DirectConnect.bundle" Plugin (Window -> Settings/Preferences -> Plug-in Manager).
Then I imported the IGES file into Rhino and changed the Units to inches. After that, I scaled the surface so that it was exactly 24 inches wide by 24 inches tall. Then I selected the surface and use the "DupBorder" command twice. Then I selected one of the newly created borders and moved it down 3 inches and duplicated the surface and moved it down 3 inches. I then selected the all surfaces and created a solid. Then I used Analyze -> Bounding Box to create a solid bounding box. Then moved the bounding box down one inch and scaled it in the x & y directions by 1.1 and then subtracted the bounding box from the surface solid. Finally, I saved the file in Rhino and booted up Windows to run Inventor HSM 2015.
Step 3: ToolPath & GCode Generation
I've summarized the instructions for the step. Check out my previous Instructable on how to setup toolpaths in Inventor HSM for all the details regarding toolpaths and configuring HSM.
After opening Inventor HSM 2015, I imported the Rhino file and set the home view as shown in the first photo. Then I pressed the CAM Tab and set the stock origin to the bottom left hand corner. Afterwards, I set the stock size to 30 inches by 30 inches by 1 inch. Then I imported the DMS tool library. Do this by right clicking on brain and Select Import Tools from Library. Navigate to the Pier 9 DMS HSM tool library (shown in the fifth photo) and press OK! Then I created the tool paths shown on the left side of the fourth image, then renumbered the tools in the order shown. Then I Post Process all the tool paths individually. Finally, I created a Setup Sheet via Inventor.
Step 4: Stock Material Preparation
The corian sheet I got for this project was originally 72 inches by 30 inches by half an inch. First I used Isopropyl Alcohol to clean the corian surface. Then I used sand paper to remove paint/ink marks on the corian surface. I used the table saw at pier 9 to cut the sheet into two 30 inch by 30 inch squares. I used corian glue to laminate the pieces together. Be careful when gluing the sheets together. You'll need a lot of glue, (at least 4 glue cartridges for a 30 inch by 30 inch slab), a well ventilated area, and a couple friends to help spread the glue quickly and evenly. After gluing the pieces together, clamp down the entire piece and let the piece sit for 24 hours.
Step 5: CNC Milling
I used various clamps to secure the corian to the acrylic bed of the DMS. Then followed the instructions in the Pier 9 DMS User Manual to mill out the piece. I'd highly recommend taking a look at this instructable: https://www.instructables.com/id/DMS-Gotchas-Things-U-Wish-U-Knew-B4-U-MILLING/ before getting on the machine.
Step 6: Post Processing
After milling, I removed the piece from the DMS and cleaned up. Then I used the table saw to cut out the piece's border. Finally I used a handheld router with a flush trim bit to make sure the edges were perfectly straight.
If I missed a step or didn't describe enough, please leave a comment below. Thanks for reading! Happy Making.
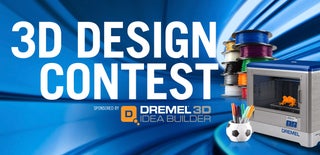
Participated in the
3D Design Contest