Introduction: R/c Racing Hovercraft, 2 Channel
this is the predecessor to my microlight hovercraft. this one differs in that it includes a lower chamber that distributes air more evenly into the skirt to make the hovercraft more stable, a higher rpm motor, a molded duct with a curved surface surface to exploit the coanda effect giving extra thrust and making the fan more efficient, and also a more sofisticated link system with rudder to take care of steering.
the results are clearly proven because this one performs far better than the original and in this instructable ill try to explain how to build one that will work just as well.
heres a link to a short video i made
http://youtu.be/YJGAMEHWN84
the results are clearly proven because this one performs far better than the original and in this instructable ill try to explain how to build one that will work just as well.
heres a link to a short video i made
http://youtu.be/YJGAMEHWN84
Step 1: Design
here are a few of the CAD software designs i made. the idea was simply to make everything neat and tidy while being fuctional, hence the bathtub for electronic components which also acts as strengthening for the bottom layer. i used Autodesk inventor for my designs and i chose to use the martini racing colour scheme.
Step 2: Base
to start the base i used some material very similar to depron foam which i had lying around. it is cut to a 300x200mm rectangle and all edges are chamfered to 45 degrees. i then cut a 40x100mm hole in the middle for housing the electronic components. underneath some 8mm thickness pieces of the same material were used to make ribs, placed and glued down in the layout shown.
the underside is a piece of white card cut to the same dimensions as the main base with 15 mm extra on all sides. these extra flaps were folded up ready to be glued to the chamfer onn the main piece and a hole punch was used to make some air leaks into the skirt.
this bottom piece should not be glued on just yet, as the linkage for the steering mechanism is hidden between the main basse and the bottom layer.
the underside is a piece of white card cut to the same dimensions as the main base with 15 mm extra on all sides. these extra flaps were folded up ready to be glued to the chamfer onn the main piece and a hole punch was used to make some air leaks into the skirt.
this bottom piece should not be glued on just yet, as the linkage for the steering mechanism is hidden between the main basse and the bottom layer.
Step 3: Duct
the duct is made from 3 layers of thick printer paper. to find out how long each piece needs to be we can use pi=3.14 for instance if your propelor is 10cm in diameter then 10x3.14 =circumference=31.4cm. so the first ring of paper needs to 31.4 cm long and the next one needs to be a mm longer to make up for the difference in thickness.
the first piece is rolled up and to join the edges (not overlap) and then the next piece is wrapped around with glue stick applied inbetween. same goes for the third and last piece.
the curved surface at the front of the duct that makes the duct look like the end of a trumpet is used tto exploit the coanda effect and is made from two banana shaped piece of polystyrene that have been modelled with a good crafts knife.
the same goes for the tri-shaped inner assembly that strengthens the duct and holds the motor, the centre piece is carved and sanded into a cylindrical shape and a pencil pushed in to create the hole for the motor, while the spokes are pieces of carefully smoothed polysyrene each of the same length that are glued to the centre piece.
one of the spokes also has a channel cut into it which is used to feed the wires from the motor down towards where the electronics will live.
the first piece is rolled up and to join the edges (not overlap) and then the next piece is wrapped around with glue stick applied inbetween. same goes for the third and last piece.
the curved surface at the front of the duct that makes the duct look like the end of a trumpet is used tto exploit the coanda effect and is made from two banana shaped piece of polystyrene that have been modelled with a good crafts knife.
the same goes for the tri-shaped inner assembly that strengthens the duct and holds the motor, the centre piece is carved and sanded into a cylindrical shape and a pencil pushed in to create the hole for the motor, while the spokes are pieces of carefully smoothed polysyrene each of the same length that are glued to the centre piece.
one of the spokes also has a channel cut into it which is used to feed the wires from the motor down towards where the electronics will live.
Step 4: Mounting
the mounting for the duct is achieved by some 90degree triangles with a curved surface to which the duct lyes on top of.
on the bottom i aso added a small piece of paper that the electronic components will lye on.
i also began drawing on my colour scheme with some felt markers and a ruler
once the duct is hot glued onto its mounts a hole is cut to the rear of the duct to channel air underneath the hovercraft. the size of which is not important however the bigger the better without being ridcolous. once this was done i also mounted my motor, the centre aassembly was irst glued into the duct then the motor was pushed into the centre duct and, after checking that it was centred and could spin freely, a couple of dabs of glue were used at the mouth of the centre hub to hold it in place.
on the bottom i aso added a small piece of paper that the electronic components will lye on.
i also began drawing on my colour scheme with some felt markers and a ruler
once the duct is hot glued onto its mounts a hole is cut to the rear of the duct to channel air underneath the hovercraft. the size of which is not important however the bigger the better without being ridcolous. once this was done i also mounted my motor, the centre aassembly was irst glued into the duct then the motor was pushed into the centre duct and, after checking that it was centred and could spin freely, a couple of dabs of glue were used at the mouth of the centre hub to hold it in place.
Step 5: Steering
the steering system consists of a rudder and shaft a linkage to connect this to the servo and a mountings for the shaft.
there are two mountings, one at the top of the duct and anoother in the air chute which i will now explain.
the air chute is there to channel a quarter of the fans air down into the skirt, i used a another piece of the depron-like foam and cut it into a small rectangle 80x36mm and made a 45degree chamfer on the two long edges this then fit snugly behind the duct as shown in the first picture. next to the chute there are also some nicely carved pieces of polystyrene that stop air escaping from the sides of the chute and make the hovercraft look a bit more aesthetically pleasing.
the chute can now be prepared for the mounting of rudder, a small hole is made with a pin in the very centre of the the top of the duct to take the paperclip shaft, speaking of which this is simply a large paper clip bent out straight but with a small kink at the top as shown in the second picture.
the paper clip is then pushed through a hole made in the top centre of the duct and dowm through the hole in the chute. once done a rectangular piece of thick paper with hot glue applied to one side is folded around the paperclip shaft so the halfs meet and stick together.
now working underneath the hovercraft, another mounting can be made as shown but is not neccesary. the bottom end of the paperclip is bent out at 90degrees to the rudder.
some finished pictures are shown of the hovercraft so far, i must confess that i accidentally stood on mine and in the process of rebuilding the duct i added an extra spoke.
there are two mountings, one at the top of the duct and anoother in the air chute which i will now explain.
the air chute is there to channel a quarter of the fans air down into the skirt, i used a another piece of the depron-like foam and cut it into a small rectangle 80x36mm and made a 45degree chamfer on the two long edges this then fit snugly behind the duct as shown in the first picture. next to the chute there are also some nicely carved pieces of polystyrene that stop air escaping from the sides of the chute and make the hovercraft look a bit more aesthetically pleasing.
the chute can now be prepared for the mounting of rudder, a small hole is made with a pin in the very centre of the the top of the duct to take the paperclip shaft, speaking of which this is simply a large paper clip bent out straight but with a small kink at the top as shown in the second picture.
the paper clip is then pushed through a hole made in the top centre of the duct and dowm through the hole in the chute. once done a rectangular piece of thick paper with hot glue applied to one side is folded around the paperclip shaft so the halfs meet and stick together.
now working underneath the hovercraft, another mounting can be made as shown but is not neccesary. the bottom end of the paperclip is bent out at 90degrees to the rudder.
some finished pictures are shown of the hovercraft so far, i must confess that i accidentally stood on mine and in the process of rebuilding the duct i added an extra spoke.
Step 6: Electronics
the electronic components that i used were from an old remote control airplane so the so the the receiver, esc and servo motor are are all mounted on an integral circuit board the battery and motor simply plug in.
the nature of the integral circuit board led to the the reason for the design of this hovercraft as the linkage for the rudder to the servo comes through a small hole in the rear rib. it lyes between the main base and the bottom layer which is yet to be attached.
some pictures show how the linkage is attached to the remaining end of the paperclip shaft and how it is shaped to fit onto the servo pin. all that is needed is some carful bending of the paperclip and some precise measurements.
the circuit board is glued down onto the paper in the bathtub and the battery lies just in front of it. this means everything is tidy and a canopy can be made to go over them.
the nature of the integral circuit board led to the the reason for the design of this hovercraft as the linkage for the rudder to the servo comes through a small hole in the rear rib. it lyes between the main base and the bottom layer which is yet to be attached.
some pictures show how the linkage is attached to the remaining end of the paperclip shaft and how it is shaped to fit onto the servo pin. all that is needed is some carful bending of the paperclip and some precise measurements.
the circuit board is glued down onto the paper in the bathtub and the battery lies just in front of it. this means everything is tidy and a canopy can be made to go over them.
Step 7: Skirt
before attaching the skirt the bottom layer of the hovercraft structure needs to be glued on. its easiest to first glue one edge then apply hot glue to all the ribs and press down the main surface of the bottom layer before glueing down the remaining edges.
once done a piece of plastic supermarket bag can be cut out to the same dimensions as the hovercraft but with an extra 20mm or so on all sides, mine measured 24x34mm. then cut a rectangular hole into the sheet of plastic about 60mm in from the edges.
the hovercraft can now be layed on top of the plastic sheet and the edges folded over leaving a bit of slack. then stick the edges down with cellotape. i used cellotape because it works just as well as hotglue but means the skirt be more easily removed and replaced if it gets damaged.
this kind of skirt is known as a wall skirt and is the simplest kind to make but still works suprisingly well giving a lift height of about 15mm.
once attached properly the hovercraft can be given a test run.
once done a piece of plastic supermarket bag can be cut out to the same dimensions as the hovercraft but with an extra 20mm or so on all sides, mine measured 24x34mm. then cut a rectangular hole into the sheet of plastic about 60mm in from the edges.
the hovercraft can now be layed on top of the plastic sheet and the edges folded over leaving a bit of slack. then stick the edges down with cellotape. i used cellotape because it works just as well as hotglue but means the skirt be more easily removed and replaced if it gets damaged.
this kind of skirt is known as a wall skirt and is the simplest kind to make but still works suprisingly well giving a lift height of about 15mm.
once attached properly the hovercraft can be given a test run.
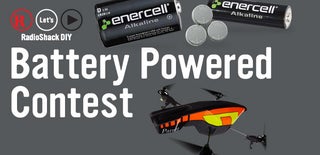
Participated in the
Battery Powered Contest
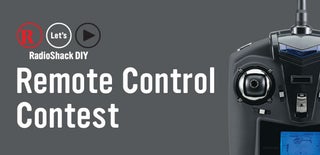
Participated in the
Remote Control Contest