Introduction: Reinforced PVC Crossbow With Laminated Stock
WARNING-Don't be foolish with weapons or power tools they are dangerous.
This is not powerful enough for big game.
I made this for my sister. She has shown some interest in archery and I couldn't think of anything to get her for her birthday. Really I just wanted an excuse. this is my first instructable so sorry for the shotty camera work.The bow is a prod when talking about crossbows
Thanks to nick at backyard Bowyer after seeing his crossbow I had to make one
http://backyardbowyer.blogspot.com/?m=1
His YouTube Chanel is great check it out
http://m.youtube.com/user/BackyardBowyer
I got a lot of inspiration form
http://www.poodwaddle.com/crossbow/?page_id=2
Tools i used are:
Table saw Dremmel with attachments Belt sander Coping saw Various wood and metal files Clamps Awl Chisels
Hand plane Bench grinder
Step 1: materials
I used 6 foot sections of wood. Red oak, hickory, and mahogany. Look for the straitest grain possible. They are 4 in wide
The pvc pipe is half inch in diameter. I ordered colored schedule 40 sections online, but white schedule 40 is best
fiberglass driveway markers
I also used scrap pvc, a gate hinge and some old bolts
Step 2: Cutting and Marking
I cut each board down to 3 feet. I used a miter saw but this can also be done by hand. I was going to make it a little longer but I like the idea of having enough extra for mistakes.
The pvc pipe comes in five foot sections. Again I cut it in half, 30 in,for extra just in case. The boards were then ripped with a table saw. It was my first time using one so I made a few mistakes and was very glad to have the extra material. The red oak was ripped to 1/2 in, the hickory to 1/4 in, and the mahogany to 3/16 in.
Step 3: Laminating and the Prod
Next the boards were sanded lightly in prep for lamination. I used tight bond 3 to glue it all together. After applying glue to the layers smear or paint the glue so it coats the entire board. Then clamp! The more the better! I didn't use as many as I should have. Also they were sandwiched between some scrap 2by4's to try to keep an even pressure while being clamped.
I reinforced the pvc by cutting down two driveway markers to 26 inches. Use a file not a saw to cut! WEAR GLOVES!!! You really don't want fiberglass splinters they hurt, they itch, and you can never get them out.
They were wrapped in vinyl tape after being cut to size. Don't use a lot of tape or you won't be able to get it in the pipe. I used some dish soap to lube them. To get them to to be evenly spaced from the tips I marked 2in on an old socket wrench an hammered it in to the mark. You could easily use a dowl for this.
Next is flattening the pvc. With it being so short I heated it in my oven. Seemed that 230f was the magic number on mine. I sandwiched the pipe between two boards and sat on it for around 10min, clamps could be used here as well.
To curve the tips I simply heated the ends over my stovetop but I normally use a heat gun, both work just as well. Don't burn the pipe! Take your time and heat it slowly. Once it's soft I applied pressure around a tin can.
I used a file to cut the nocks. You want to use the center prong for the string. I cut them a little deeper than in the photo.
Para cord was used for the sting, this is only temporary as I plan to tie a true bowstring in the future. I tied it about two inches shorter the the prong.
Step 4: fixing My Screw Up
After unclamping the boards I shaved it down to remove the uneven edges and make it square. That's when I noticed some pretty significant gaps.
I had never used a table saw before this project and should have run some practice cuts before jumping right in. I purchased some fiber glass resin to fill the gaps.
Before mixing the resin I taped up the boards with wax paper and foil to contain it. After mixing I added a couple drops of red acrylic paint for color.
Pour the resin over the gaps carefully. Then tap the sides to release air bubbles.
After it cured I ran it through the table saw to shave off any excess. Resin doesn't take to chiseling or hand planing well, it chips and cracks.
I felt so relived that the whole thing was salvageable after seeing the end result. I thought it was ruined and that I had to start all over.
On to shaping the wood!!!
Step 5: shaping the Stock
I cut down the board to 33 in. This just felt better put up to my shoulder. Then I freehand drew a rough outline. I started the cut with a jigsaw but quickly switched to a coping saw. I prefer hand tools to power tools because, to me, it is way to easy to make a large mistake in a blink of an eye.
After it was cut roughly to shape I took out some old files and went at it. I'm sure there's some easier way to do this but I really enjoy using hand tools. For the butt end of the stick a belt sander was used.
To cut the nock for the prod I measured the length and width of the flattened pipe and marked on the wood so it would be recessed and at an angle to reduce wear on the string. Holes were drilled in the corners, with help from my son. Another hole was drilled at center two inches back from end. This is for the rod to lash down the prod. I strung my coping saw through the holes and cut it out. I ended up filling it down to size.
After seeing it shaped in decided to cut some more off to give it more of a traditional stock look.
I marked down 15 in and drilled a center hole all the way trough the stock. This is for the trigger. Then on either side a hole was drilled an inch in. These are for posts to hold the string.
To make the arrow channel I first ran a dremmel down the center line to make a groove. Then I wrapped a dowl in sandpaper to get the right width.
I used boiled linseed oil to seal the wood after sanding tool marks out. I used a lot of thin coats over a couple days. You could use any kind of finishing oil or varnish. I thought about staining it but I like to let the true color of the wood speak for its self
Step 6: hardware
For the posts to hold the string I found this little squared rod in my scrap box. It was cut in half and notched around the bottom to grip better. I gently hammered them in after putting a couple drops of two part epoxy in the hole first. You could use nails or dowls or anything strong enough to hold the string. I used this set up so notched arrows could be used between the two posts. I then tried out the bow to see if the posts would hold. I ended up filing them both down a bit and rounded the edges.
I cut a steel rod down to 41/2 in. and hammered it in the hole behind the notch for the prod.
For the stirrup I used a decorative gate hinge. It had the other end of the hinge ground off and the end shaped to size. I free handed it by it ended up 8 1/2 in long. It was epoxied before being screwed on and the screws were predrilled. I planned on bending a steel rod to fit in the hinge for the foot hold but never got to it. If I do I'll update. Para cord was looped through for a foot hold.
Next I flattened two scrap pieces of pvc. White schedule 40 for the bolt holder and grey schedule 40 for the trigger. Both were heated in my oven and then clamped down between two 2x4s. The white pvc was cut in half before being flattened. I free handed the shape of bolt holder after being cut down to 8 in. The grey was cut to 13 in and rounded at the corners. I shaped them after careful heating over my stovetop, again a heat gun works as well, and molded them by hand. It took a long time and a lot of trial and error to get them the way I wanted. After the pieces were screwed on I cut a bolt down to size and rounded the edges. It's not pretty but I works well.
If you can tell from the pictures the bolt lays flush in the stock but when pulling the trigger it pushes upward, releasing the bolt. With the posts and the trigger being in line with one another it cannot be dry fired, it pushes up on a nocked bolt not the string.
Step 7: attaching the Prod
First I cut a price of scrap cloth four inches wide and a foot long. You may need more or less depending on how tight the fit is to the stock. I then wrapped it neatly around the center of the prod using a little contact cement to hold it on.
I used para cord again to lash the prod on the bow. Use a cross pattern to hold it tight. It's not pretty but it holds.
Step 8: final Thoughts
After the build I would have changed the length of the prod, 36in and the rods 32in. Being so short I have heard some uncomfortable creaking when cocking. At 30in it's pulling at 80lbs give or take. Will still have plenty of power for shooting if the prod is longer.
I forgot to add that I waxed the part of the stock the string comes in contact with bees wax.
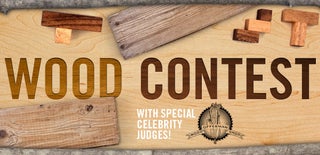
Participated in the
Wood Contest