Introduction: Coconut Incense Burner
"Incense" is that one word I can never spell correctly on the first try.
Making this incense burner, on the other hand, worked out just fine on the first try.
I don't even like incense, but when the grocery store had coconuts in stock, I looked at them and went: "I could make a sweet incense burner out of that," so here we are.
Time: Moderate. Doable over the course of anywhere from one to four days, depending on amount of time dedicated to project per day.
Skill: Also moderate. Can substitute clay for metal and forgo the lathe work, but will still require the use of some kind of saw and a drill.
Caution: Sawblades and drill bits are designed to cut through wood and metal. Wood and metal are much tougher than human skin. Sawblades and drill bits will make quick work of the flesh of the unwary.
Step 1: Tools & Materials
Required
- Coconut
- Drill bits in various diameters
- Pin vise and/or power drill
- Some kind of saw (preferably a Dremel or other rotary tool with a tiny sawblade attachment)
- Sandpaper in a range of grits, from about 80 up to at least 400 for the smoother finishes
- Metal rod stock in ~3cm and ~5cm diameters OR non-shrinking clay
- Knife. The standard kitchen variety should suffice.
- Small rare-earth magnets
- Toothpicks or other tiny sticks
- Strong glue or epoxy that will adhere to both metal and wood
- Dust mask
- Safety glasses
- Cone-shaped incense
- Lighter or matches
Recommended
- Awl or other small hole-poking tool
- Funnel
- Cup or bottle
- Felt-tip pen
- Vise
- Squishy rubberized vise jaw liners
- Belt sander
- Wood rasps equivalent to about 200grit sandpaper
- Coarse round-head engraving burr
- Lathe and cutters for metal
- Sheet of cardboard or plastic so epoxy doesn't get all over the table when mixing it
- Craft foam, about 2mm thick
- Craft knife, e.g. X-Acto knife
- Wood wax. Beeswax, furniture polish, Renaissance wax, etc.
- Lint-free cloth, e.g., chamois, old T-shirt
- Apron
- Face-shield
- Ear/hearing protection
Optional
- Aluminum foil
- Clay-shaping tools if going the clay route instead of the metal one
- A rock or something else heavy to add weight to a clay base
- Possibly an oven or kiln if it is not air-dry clay
- Paint and varnish
- Technically I suppose the safety gear is all optional, but honestly, not using it would be a dumb idea
Step 2: Get Nutty
Acquire a coconut, which is in fact a fruit (a drupe, to be specific), and not a nut.
Maybe they grow on trees nearby and it's an easy matter to go out and pick one, or maybe it calls for a trip to the grocery store.
Step 3: Drill and Drain
If it is harvested directly from a tree, there will be some other steps in here for removing the husk, but as I have only ever dealt with the already-husked versions, that's what this Instructable will cover. If husking is required, check out any of these Instructables for a how-to:
- https://www.instructables.com/id/How-to-Husk-Coconu...
- https://www.instructables.com/id/Husk-a-Coconut-Wit...
- https://www.instructables.com/id/CoconutMilk/
- https://www.instructables.com/id/How-To-Make-Coconu...
- https://www.instructables.com/id/How-to-Peel-a-Coco...
Use an awl or other stabby implement to poke a pilot hole in at least two of the "eyes" on one end of the coconut. Depending on awl length and diameter, and the toughness of the coconut, it might not be necessary to drill the holes larger. If, however, they are just too small to drain out the coconut water, grab a drill and a drill bit, and enlarge the holes.
A wide-mouthed cup will do fine on its own, but if using a narrow-necked bottle, a funnel can help prevent spillage. Or it can all be drained down the sink if there is no desire to keep any of the coconut water, but that's a waste of usefulfoodstuffs.
Step 4: Making Plans
If using just a big hacksaw or carpenter's saw, skip this part, as doing any sort of detailed cuts with that will be difficult. If using a rotary tool (e.g. a Dremel) with a tiny sawblade attachment, read on.
Grab a marker and sketch out the desired shape of the coconut opening. This part can be freehanded with the saw, but I prefer planning it out beforehand. Measure twice, cut once, and all that. Also keep in mind that if the opening is on the small side, getting the meat out will be a challenge.
I went with something that followed the coconut's natural threefold symmetry because that was the easiest to plan out, and I like flowing with the natural forms of the materials I use when I can do so.
Step 5: Open It Up
Cutting it open is greatly facilitated by a bench-top vise with squishy jaws to firmly hold the coconut while the Dremel does its thing. The wood of the coconut is tough stuff, and I'm glad I was able to use both hands to hold the Dremel, because that little sawblade just loved trying to hare off any which way whenever it snagged on an edge.
Alternately, if no saws are available, dropping it on the floor or hitting it with a hammer and hoping for a good fracture pattern is always an option.
Step 6: Gut It
Scrape out all the meat. Sometimes it comes out easily. Sometimes it's really stubborn. One time my mother snapped a knife in half while trying to de-flesh a particularly ornery coconut. So, safety glasses: not usually considered a kitchen thing, but maybe a good idea?
There are loads of recipes involving coconut, so hang onto the meaty bits.
Step 7: De-Fuzzify
The hairy bits on the outside of the shell are called coir. It's time to remove it, if so desired.
This part will go waaay faster with access to a belt sander. Preferably one without a solid table mounted under/behind the belt, so the sandpaper strip can better fit the contours of the coconut and not leave weird flat spots. No photos of the actual belt-sanding process because I'm not about to try holding my work with only one hand while taking photos with the other. I like having skin on my hands, thanks.
Without access to a belt sander, be prepared for lots and lots of hand sanding. Start with a good 80grit, or even 60grit, because it'll take long enough as it is, let alone trying to do the job entirely with 200grit.
Wear a dust mask.
(This step and the previous step can be swapped around. This is just the order I did it in.)
Step 8: Smoke Vents
The incense smoke needs to be able to waft out of the burner, so to that effect it is time to drill some holes.
Due to a coconut being a naturally grown thing, it will probably not be symmetrical. I still tried to make everything on this one at least a little bit evenly spaced in some sort of pattern. My second still-a-work-in-progress coconut incense burner was drilled more randomly.
Step 9: Holey Smoke
Time to drill the holes. Unpowered hand drills can do the job, but it'll take a long time. Go for the power tools if any are available. Coconut wood is tough stuff, and minus the coir can be very slippery, so I grabbed one of my coarse engraving burrs to cut little starter dimples for each of the holes to keep the drill bits from wandering.
I varied the sizes of the holes to add a bit of visual appeal, but after testing this one out, would suggest keeping them on the smaller side, or at least predominantly smaller with only a few over 3mm in diameter here and there. Too many large holes near the top means most of the smoke will go out those ones instead of filling up the inside and then wafting out of all of them.
Step 10: Sanding
Lots of sanding.
Like really a lot.
Super a lot.
Could a belt sander be used here? Yes, but it runs the risk of putting flat spots in the surface. Hand-sanding may take more time and be hard on the hands (take frequent breaks to stretch), but it will give a much nicer finish in the end, which to me is worth the extra time and effort.
Step 11: Magnetizing
I needed a way to attach the top and bottom pieces together that was secure yet left the top easily removable in order to clean out the used incense ashes and put in new cones, and also helped smoothly bridge the gap left by the saw (called the kerf -- fun fact of the day).
The solution? Magnets!
Magnets are pretty rad, useful things. The 3mm wide x 2mm thick cylindrical rare-earth magnets were the perfect size. Glued them on with Loctite 5min power epoxy, but next time will look for something even stronger, like E6000, because some of the magnets have come loose at least once.
Don't use superglue. It's strong but brittle, and one good whack will break its hold.
Step 12: Un-Spacing Out
Once the magnets on one side are firmly in place, it's time to line up the other piece. Due to the saw cuts from back when the coconut was sliced open likely not being even, some filing and sanding will probably need doing to close up any gaps between both sections. The magnets won't grip as strongly if there is open space between them.
Step 13: Stick Together
Once the magnets are firmly attached to one side, it's a simple enough matter to use them to glue the matching magnets to the other side.
Step 14: Making the Incense Holder
A coconut is made of wood.
Wood is flammable.
The use of incense requires setting it on fire.
The smouldering incense needs to not come in direct contact with the coconut.
Time to make a little table to hold the incense cones.
I turned mine out of a piece of brass stock using the Bergen hackerspace's lathe, which, despite its general unfantasticality and the fact I don't trust it with work needing any degree of extreme precision, is still better than no lathe at all, and I'm glad I have access to it. Used brass because it's easy to machine and it's what I had lying around.
I only have a few photos due to safety reasons. Don't try to multitask while using power tools. The photos that do exist of the piece-in-progress were mostly taken by my fellow Hack Bergen member and usual partner-in-crime, Karlmag.
Lathe work is an entire encyclopedia all on its own, so I will not be providing a how-to here. For further info here are some other Instructables to check out:
For people without a lathe and/or with no lathe skills to speak of, clay is a good alternative. Some packs of incense cones will come with a little metal tray to put the incense on, and it should be a simple enough matter to sculpt a clay support for it. Just don't permanently attach it to the inside of the coconut yet.
3D printing is another option for those with access to a 3D printer that can sinter metal (e.g. via a company like Shapeways).
Step 15: Making the Base
The base of the whole incense burner is basically the same thing as the little interior incense cone table, just writ larger. The one I made is solid brass, so it has a fair bit of weight to it. This helps a lot with preventing the incense burner being knocked over during use.
As before, people with no lathe, or limited or just plain terrible lathe skills can substitute clay. If it's a clay that dries rather lightweight, I'd suggest getting a rock or something else heavy to seal inside the base to add stability.
3D printing is, again, another possibility, and something I'd like to try for future iterations of this project. Imagine a sturdy yet elegantly filigreed base in any of a number of different materials and colours.
Step 16: Attaching the Base
Get a permanent adhesive that can bond wood and metal (if using metal; clays are probably a mite easier to glue). Go with something that will dry clear, or at least be an unobtrusive colour. I used Loctite 5-minute power epoxy again.
Step 17: Attaching the Incense Holder
Pretty much the same idea as gluing the base on, except instead of wood on top of metal, this time it's metal on top of wood.
Step 18: Wax On, Wax Off
Optional, but I think it gives everything a nice finish and a good shine to the coconut shell.
I used Renaissance Wax, but beeswax or furniture wax should do a decent job too. Clay may need painting or varnishing instead to properly seal it.
Step 19: Anti-Scratch Coating
Craft foam, or EVA foam, is versatile stuff. Here it is being used as an anti-scratch, no-slip layer on the underside of the base. Could also use felt, leather, rubber, any other kind of fabric that can be glued to metal. More Loctite epoxy here.
Step 20: Use It
Get out a cone of incense, place it on the tray, light it and close up the burner. In a few seconds aromatic smoke should start to billow out of the holes in the coconut. Sit back, relax, and enjoy your new incense burner.
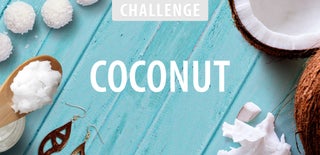
Grand Prize in the
Coconut Challenge
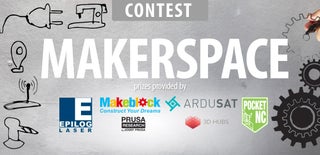
Participated in the
Makerspace Contest
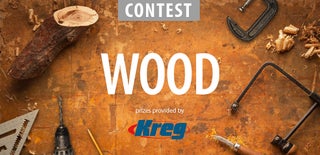
Participated in the
Wood Contest 2016