Introduction: How to Make the Ring Lamp
Here is the list of things you will need:
- 40x LED's of your choice(i used straw hat)
- Red and black multi-core wire
- 12x 82ohm resistors & 2x 220ohm resistors
- Polyurethane resin with its hardener
- Plaster cast
- Bandages
- Thin acrylic sheets(A2 size)
- Scrap wood(MDF)
- 1x toggle switch
- 1x mains adapter AC to DC converter
- Male and female sockets
- Acrylic rods
- Large piece of Ash or wood of your choice
- Latex and thickener
- Soldering kit(including flux, solder, iron, pliers,cutters and a sucker)
- Disposable brushes
- Screw driver
- A Lathe and tools
- Sand paper(lots of grades)]
- Drill with drill bits
- Circle cutter
- Gloves
- Goggles
- Scales
- Mixing pot
- popsicle stick
Step 1: Drawings
These will probably help explain the making of it.
Step 2: Rings
Casting the resin rings takes a while as you have to make all of the moulds and leave it to set. I accidently dropped a couple so i had to do them again. BE CAREFUL!!
To make the mould you must first turn or mould a pattern that fits the measurement of 250mm outer and 220mm inner. the depth of the ring should be 10mm. You can do this using modelling clay however I used a Lathe as it created an even, symmetrical ring.
Once the pattern has been made you need to make a mould using a vacuum former i used one in a local workshop but you can make them quite easily(https://www.instructables.com/id/My-vacuum-former/). So place the pattern onto the tray and heat up the acrylic sheet to make it semi-molten. Form the plastic around the pattern and leave to cool.
Remove the mould from the pattern and add a layer of latex with a little thicker added to the under side of the vaccum formed mould. Leave this to dry then add another with more thicker added. leave to cool. repeat the process, adding more thickener each time, continue until the colour of the mould can not bee seen through the latex.
Leave the latex to completely set the mix up plaster with warm water. pour the plaster into the upturned mould with the latex still inside. wait until this has set to. To strengthen the cast apply bandages to the rim of the mould and slap on a thick layer of plaster. Make sure it is leavl using a large flat piece of wood to level it off.
Now that that's done and dried you can start to pour in the resin. Take the latex out and the cast too before hand. then place the latex over the cast again and pour into it. Depending on what type of resin you get measure out the quantities needed.
Once all is set and dry remove the ring and keep it safe!!
Step 3: Inner Ring
Turning the inner ring require a lathe a little practice.
Mark up a circle of wood just over 250mm in diameter and 30mm in thickness, cut it out using a saw and mount it to a lathe. face it off and reduce the diameter to 250mm exactly.
Mark up a ring with outer diameter of 250mm and inner diameter of 220mm. Within this boundary mark up a ring with inner diameter of 225mm and outer diameter of 245mm. On the late using a ruler, to check every now and then, create a depth of 10mm. this is where one of the PCBs will sit. go 10mm in depth on the outer outer ring which you have marked up.
Create a dove tail recess in the centre of the wood and remove it from the lathe. turn it around and using the dove tail recess remount the wood. Using the same measurements as the other side. Do the same turning.
At this stage you may wish to sand the ring whilst it is on the lathe. Once it is all neat you need to cut all the way through on the inner diameter line using the lathe tools. This may need an extra person to support it as it will suddenly pop off from the rest of the wood.
Step 4: Circuitry
I have looked and looked to find a circuit that would fit inside the ring but could not find one. So i designed and made my own.
Using a thin sheet of acrylic mark up the diameter of the groove which has been cut using a pen. using a pretractor and a ruler mark up two holes every 18 degrees( these are where the LEDs will go. Every third LED bar the end two mark up another two holes(this is for the resistors. Set up the hole cutter in the pillar drill and cut out the acrylic. this need to be done twice for the other PCB. Drill out all the holes and sand any rough edges.
Now that you have two PCB rings for the inner groove you can solder them up. Make sure the LED's point in the right direction.
Leave the ends of the red and black wires free on each board. give about 60mm extra.
You can also solder up the connection and the power supply at this stage.
Step 5: Base
The base consists of three pieces of MDF. Each one with a curve so the ring can sit nicely in it. Using a Jig saw and a bobbin sander create the curve necessary for your ring to sit on the base. At either end of the centre piece of MDF drill a hole. one for the connection socket and one for the toggle switch. Once these have been drilled turn it upside down and chicle out the bottom, this is for the completion of the circuit later.
Now that all is drilled out etc, glue the two outer parts of the MDF to the Centre piece. You may paint or vacuum form over the MDF, if you vacuum form make sure to drill the holes again at a slow RPM.
Once this has been done drill a small hole big enough for the wires from the PCB's to fit through.
Step 6: Assembly
Connecting everything together.....
This is where the Acrylic rods come into play. using small wood screws, screw the PCB's down to the groove, drill a small hole near the bottom of the ring so all the wires can be feed through to attach the base.
slice up the rods into small discs and place them evenly around the groove, using araldite to hold them to the PCB's. Place a small dot blob of araldite on the top of each disc and carefully line up the resin rings. hold these down with a book or block of wood until the araldite has set.
The two hold which have been drilled for the wires can bee lined up and the wire may be feed through. solder the positive wire to the switch first then to the plug and the negative wire straight to the plug. To insulate the wires and stop them from touching I filled the base with hot glue.
To weight the lamp, cut out a thick piece of steel sheet the same size as the area of the base. Drill holes in each of its corners and attach it to the base using screws.
I'd like to be able to make many more of these lights as well as the ideas that keep popping into my head, however due to the precision needed by some of them i would like to own a laser cutter, this would help out very well.
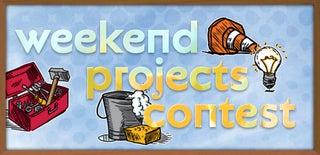
Runner Up in the
Weekend Projects Contest
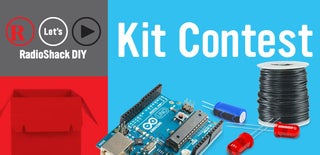
Participated in the
Kit Contest
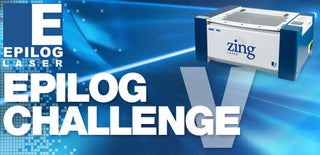
Participated in the
Epilog Challenge V