Introduction: My Vacuum Former
Before I set out to build my own vacuum former I did alot of research on various DIY sites. I found alot of helpful tips and designs. Ultimately I settled on components from several different designs. My design is by no means perfect, but it gets the job done, and was fairly cheap to build. It is capable of forming a piece 33" x 22".
Step 1: Basic Box
I started with a basic five sided wood box out of half inch particle board. This will be the infrared "oven". 24 inches deep, 35 inches long, 24 inches wide. Thats pretty straight forward.
Step 2: Heat Source (also Keeps Your French Fries Warm)
As I said, I researched many different designs before I started and found that I preferred the infrared lamp as my heat source because, well frankly, I thought I'd burn my house down if I tried to build my own heating element. I even considered buying three electric pancake griddles, bolting them side by side into a box, and placing that over the plastic sheet. I tried it with one griddle and it worked pretty well, though my wife was not pleased with me disappearing into the garage with it.
I used a total of ten infrared heat lamps that you can purchase at any hardware store. There are four 250 watt bulbs, six 125 watt bulbs, and one 1200 watt patio heater. I had the patio heater already so i incorporated it, but i'm sure I could have used 4 more 250 watt bulbs in its place. This gives me a total of nearly 3000 watts of heating.
The bulbs are mounted with ten porcelin standard 120 volt, 600 watt light fixtures. The kind you find mounted on a rafter in your attic, or in a garage, or basement. They do not have a pull string or switch built into them.
When figuring the placement of the bulbs I had to take into account the thickness of the insulated panels, which I will explain later.
Step 3: Wiring (not My Strong Suit)
I'll be upfront...this part worried me the most. I would have liked to have used junction boxes and romex for all the wiring but I decided to throw caution to the wind when the budget ran thin. 40 feet of wiring cost $3.00 versus all the romex and junction boxes costing $60.00. I did however oversize the wiring, and use a whole roll of electrical tape on each wire nut to put my mind at ease. I connected the wiring in three circuits to avoid tripping breakers in my house. One circuit is the patio heater alone. The second circuit is the four 250 watt bulbs in the middle. The third circuit is the six 125 watt bulbs on the outside. Each circuit has its own cord. This configuration was designed to minimize load on any one breaker in my house. I can plug the whole thing into my garage circuit, but I don't simply because I'm paranoid that the builders of my tract house did a crappy job with the wiring. This configuration has the added benefit of allowing me to control the heat required for different thicknesses and material types. For thiner materials I can just use the patio heater, or the patio heater and the four 250 watt bulbs. For thicker material I can turn on the six 150 watt bulbs.
I mounted the whole thing on the bottom of an old janitors cart I had. The bottom shelf serves as a cavity for the wiring to be stored and protected.
Step 4: Insulated Panels
Obviously particle board and enough heat to cook a turkey in about an hour aren't a good combination so I thought I should insulate the heat box. I found that the insulated panels would serve several purposes. First, they keep the particle board from getting too hot. Second, because the plastic sheet serves as a kind of cap for the heat chamber, the insulated panels help hold the heat under the plastic rather then letting it disipate into the air. Third, the panels are made of galvanized steel which help diffuse the infrared radiation as it moves up towards the plastic. (I assure you I only made half of that up).
The insulated panels are 24 gauge sheet metal panels. They are composed of two square "pans" that have a one inch blanket of insulation between them. The pans were then rivetted together. One of the pans has a longer edge at the top where I formed a channle to hook onto the wood side. I am a sheet metal worker by trade so I have made similar panels before, and I have easy access to the materials for free. If I didn't have access to the metal I could have just used the insulated blanket, which had one foil side, and foil taped it directly to the wood. Since the bottom of the box is not exposed to as much heat I settled for just using the insulation material to cover it. The panels have worked remarkably well. There is absolutely no noticeable rise in temperature on the outside of the box or the internal surface of the wood, even though the inside reaches 450 degrees.
Step 5: Vacuum Table
The vaccum table consists of 3 layers of 3/4" particle board. The top layer has roughly 500 3/16" holes drilled an inch apart on center. There is a two inch boarder of foam rubber tape to give a good air tight seal between the frame and the vacuum table. The second layer is just a frame with a two inch boarder which will provide a void between the top and bottom layer. The third layer is a solid board with a single 1 1/2" hole cut into it for the vacuum hose to be attached.
I inserted a 1 1/2" male thread to 1 1/2" female slip pvc fitting into the hole on the the bottom of the vacuum table and glued it in place with a strong epoxy. The 1 1/2" fitting was a perfect fit for my vacuum. The electrical tape in the picture was just a cheap way to make the connection in a non permanent manner.
Step 6: Plastic Holding Frame
Most instructions I found for building frames used some sort of aluminum window frame. With my design, I went with a wood frame with several bolts holding the two halves together. I did this because the wood doesnt transfer much heat to my hands when I pick up the frame to place it on the vacuum table, and I already had the wood laying around.
Finally, the hot box, the vacuum table and the frame are stackable for easy storage, and the whole thing rolls right into an out of the way corner of my garage.
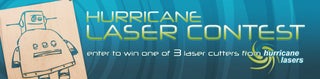
Participated in the
Hurricane Lasers Contest