Introduction: Oven Hood Incandescent to LED Conversion
Had an old oven hood that never seemed to have a bulb that worked or fit. Decided to upgrade it to have 24 watts of white LEDs. Using 8x 3w LEDs supported on 1.5" aluminum bar from the hardware store, powered with a Mean Well constant current supply that I bought for a different project that never happened. So I have been wanting to utilize it.
Pretty simple project, excluding the oven hood ran about $40. And the LED/heatsink assembly will be easily reutilized when it comes time to replace the oven hood. I would more like to demonstrate the techniques that I used to do this other than expecting people to go out and try to recreate it. This oven hood is well above the cook top, and I have monitored the temperature with a infrared thermometer, but in a lot of cases the LEDs could get to hot from use and stove/oven being on, so bear that in mind.
DISCLAIMER: Of course modifiying anything and using AC wall voltages can be dangerous, anyone recreating or following the instructions on this project does so at their OWN RISK.
Attachments
Step 1: Materials and Tools
- 3w Cool White LEDs on star heatsinks, I used 8.
- Some High-temp or silicone insulated wire, 20ga or so.
- Constant Current Regulator, from AC I used a Mean Well LPC-35-700, 48v @ 700ma constant current output, 100-240VAC input.
- Aluminum Bar, I used 24" of 1.5" wide, available at hardware stores such as Home Depot.
- Various screws bolts, nuts and washers
- Thermal Compound/Thermal Adhesive
- Wire, 18-20ga, high-heat insulation
- Silicone Sealer
- A sheet metal oven hood.
- Soldering Iron
- Hack Saw
- Drill and bits
- Tap(optional)
- Electronic tools, wire snips, strippers ect
Step 2: Prep the Hood
Look over and and make a not of how things are connected and wired. But simply the only electronics that get altered is the bulb socket gets switched with a constant current regulator.
- Find the bulb socket and remove it by clipping it off with a wire snips, keep note of those wires, and mark which one is AC hot and which one is AC neutral, most constant current regulators request to be hooked up to the AC correctly.
- Remove any covers, grates, anything that isn't needed.
- There should be 2 switches, one 2 way for light on/off and the other a 3-way for the fan.(most hoods I have seen) leave them alone for now.
- If the hood is used, wipe it off, get any grease and spatters off. I used some orange based degreaser cleaner that works and smells great.
- Figure out the best way to mount the aluminum bar to the hood, this will vary greatly between types of hoods, I found a spot right up against the front, resting a lip of sheet metal, not as much contact with the hood as I would like to help dissipate the heat. But some aluminum bar posts and thermal compound at either end will help handle the heat.
- Test fit the constant current supply, leave some space around it so it can breathe, and make sure the wires will reach to where they need to go.I had just enough wire to get to either end of the aluminum bar.
- If your constant current supply has mounting holes like mine did, mark the holes now.
Step 3: Prep the Heatsink
Mark for the LEDs:
- Lay down the chosen length of aluminum bar, I used 24" by 1.5" wide.
- Space the LEDs evenly across the bar. See Diagram.
- Position the LEDs as pictured and mark their mounting holes with a sharpie.
- Test fit the bar in the oven hood and mark where the mounting bolts/screws will go.
Drilling:
- Drill out the LED mounting holes, I drilled and tapped the holes for a 4-40 screw.
- Drill out the mounting bolts, I used 1/8th bit that matched the sized bolt, not tapped, easily slides in and out.
- Tap the LED mounting holes with the appropriate tap.
Fins:
- Lastly I finned the ends of the aluminum bar with a hacksaw, hammer and pliers.
Step 4: Solder the LEDs
Mounting the LEDs:
- Put a drop of thermal compound in where the LED will sit
- Place the LEDsso they can be wired in series, arrange them so their soler pads + or - are in order.
+LED1- +LED2- +LED3- +LED4- ect
- Then screw in the LED, make sure the screws aren't in contact with the solder pads, use a V-shaped/flat/countersunk type screw
- Mount All the LEDs
Soldering the LEDs:
- Start by turning your soldering iron up quite hot, upwards 250c and flux the solder pads if they aren't already
- Using some 20ga or thicker high-temp or silicone insulated wire, start connecting linking the solder pads as they were laid out
+LED1- +LED2- +LED3- +LED4- ect
- Then the constant current regulator gets connected. Connect the regulators V- to an end LED- and the regulator's V+ to the LED+ on the other end of the string.
- Lastly silicone or hotglue any places where it looks like the wire could bend or move and touch the aluminum bar.
No wires should ever touch the aluminum bar, it would most likely destroy the constant current regulator. Make sure they are insulated.
Step 5: Mount LED Assembly and Wire
Mount the LED Assembly:
- This will vary greatly depending on oven hood and setup.
- Seen in the images, I used 3 bolts and the edge of part of the sheetmetal oven hood to support the aluminum bar with the LEDs on it.
- Using quite a bit of thermal compound to areas of the aluminum bar that would touch the hood, then bolted it in to the holes I drilled and tapped.
Wiring The Current Regulator:
- If not already mount the constant current regulator.
- Most hoods have an on/off switch for the light and a on/off or 3 speed switch for the fan.
- The bulb socket should have been clipped off in Step 2 and the wires labeled which one is AC hot and which one is AC neutral
- Figure out which is which and forget about the fan and focus on the light on/off.
- Using a wire nut connect the AC hot wire from the switch to the AC hot connection of the constant current regulator.
- Wire the AC neutral to the AC neutral of the constant current regulator.
- Position and bundle up the wires with some zip ties
The 2 wires that connect to the AC voltage should be un-conencted.
Step 6: Diffuser
Diffuser: Makes the light less intense, and evens it out.
- See the Photos. Not going to cover it to much but I used some cloudy HDPE plastic sheets, about 60mil thick. And some plastic edging from Home Depot. Attached it all with some VHB double sided tape. With some copper wire supports. Could also use those plastic diffusers for dropped ceilings and flourescent lights.
- The diffuser was made in 2 parts and it slides into the plastic eding.
Step 7: Reassembly & Installation
Now that all the custom parts are installed, its time to put the rest back together.
- First if you have the ability, hook the oven hood up to an AC cord and test if it is working correctly.
- The cover I had taken off to mount the constant current regulator no longer fit, so I used some scrap sheet metal to make a cover.
- Installed the cover over the regulator and all the wires,
Installation: Do not attempt if you are untrained or unsure. Continue at your own risk. AC voltage can be dangerous.
You should have wrote down or remembered how it gets wired back up before it got taken apart.
- Mount it up like any other oven hood, there should be a hole in back that the house-wiring can be accessed from.
- Using a wire nut, Connect the AC Neutral Wire(white in USA) to the neutral on the constant current regulator, to the switch and to the fan if there is one.
- Using a wire nut, Connect the AC Hot(black in USA) to the switch, which is connected to the AC Hot of the current regulator.
Try it out.
Step 8: All Done.
Visit My Profile To View More Instructables or Visit My Project Page.
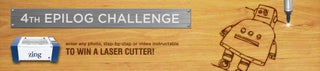
Participated in the
4th Epilog Challenge
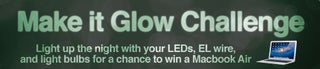
Participated in the
Make It Glow Challenge
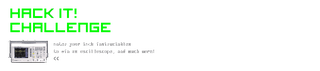
Participated in the
Hack It! Challenge