Introduction: The Fifth Element Stones Pillar Candle Holders
Anyone who's ever seen my work knows I'm a sucker for all things nerdy. My home is, quite literally, a shrine to all of my favorite movies, TV shows, even games. Over the years, I've recreated hundreds of props for friends to use in their cosplay at the local Comicon, which can be extremely satisfying when you see how these props can pull a costume together.
By far, though, my favorite time waster is making display props from hit movies that didn't indulge in merchandising for various reasons, or that whatever merchandise they did create is so rare and obscure as to make it unattainable to the average person. One big stipulation, that I have, is that the props I make need to have form and function. Meaning that, it either has to operate in the same way as it does in the franchise, or it must serve some other practical function besides being a simple display item.
In my top ten list of movies is the film 'The Fifth Element'. Beyond being an amazing film, props and merchandise are extremely difficult to find, and often if you do find something its either an expensive film prop that is profoundly expensive, or a low quality (and equally expensive) representation that can only be bought from specialty sites.
For my project, I wanted to recreate the element stones that were used to kill the 'evil' in the weapon chamber in Egypt. It was evident that the movie versions were made out of polystyrene, but I wanted mine to be a bit more durable and long lasting, and so I ended up manufacturing them out of wood. Also, following my own rules on prop creation, I decided to turn them into functional pillar candle holders that I could use to decorate my dinner table during gatherings, as a conversation piece, or simply as an everyday accent.
One of the problems with creating large triangular blocks is that you need large round blades to cut them properly, and unfortunately my table saw has limitations. The movie version is roughly 9" tall and 4" on each side with a .5" bevel, but because of these limitations, I ended up reducing the sides to 3", with a .5" bevel, though I was able to maintain the 9" length. This turned out to be a bit of a blessing, however, since as a table decoration, their larger size wouldn't have been practical and would have taken up too much space to be usable. If, indeed, you wanted to make perfectly sized 'stones', you can use all of the same techniques outlined in this instructable without much alteration. I'll make notes on the appropriate steps for anyone wanting to make the full size version.
Step 1: Tools and Supplies
Tools:
- Table Saw (optional can use hand saw)
- Router with 1/4" straight bit
- Dremel
- Hand Saw
- 1 5/8" forstner or spade bit
- Round File
- Bench Sander
- Airbrush and Compressor (optional can use brushes)
Supplies:
- 4x4x8' beam (actually 3.5"x3.5"x8')
- Stone paint
- Rubber gloves
- sandpaper
- Black, Brown, Orange and Tan acrylic paints
Step 2: Creating the Sides
The first step was to cut my 8' beam into 22" sections. Each section would create 2 stones, leaving a few extra inches of material for refining the ends. You can use a hand saw, but if you own a miter saw, the process is a lot easier. If your blade suffers the size issue, you can cut 3/4 of the way through on one side, then flip it over and finish the cut on the other leaving a nice flush end.
My saw uses a 10" blade, which doesn't leave a lot of edge, above the table, for cutting. As such, I only had two options; reduce the beam to a usable size, or cut the shape with a hand saw. Since the hand saw wouldn't offer the quality I was looking for, I opted to remove one face of the beam making its final size: 3"x3.5"x22" per beam. The process for 'facing' it is the same as using the miter. Extend your blade fully, then run your piece through which will cut 3/4's of the thickness. Then simply flip the beam over and finish cutting the final 1/4 of the piece.
With the beam narrowed, its time to cut the angles. First, with your blade fully extended adjust its angle to 30 degrees. Then, adjust the distance from the base of the blade to the guard to 1.5". This will create your bevels leaving .5" flat section between them. If you're working with a 4" piece, you'll want to increase the angle to 33 degrees and the distance from the guard to 1.75". Lay your beam with the freshly cut face down and the 3.5" side horizontal. Run your piece through and remove one side, then flip it around and remove the other.
Next you'll want to adjust your distance from the blade to the guard to 3.5", maintaining the angle of the blade. Flip your beam over so that the back is flat against the table and run it through again. This will create the flat edge between the sides. Repeat with the other side to refine its flat edge. No guard adjustments are required as the actual width isn't altered in creating this flat edge.
Your final pieces should resemble the last image in this step.
Step 3: Finishing the Length
Once you've created your two 22" beams, its time to cut them down into 10" sections. Use the same procedure you used on your miter saw, in the last step, to create a nice true edge.
It's a good idea to clean and finalize your edges, making sure that each side and flat section between are straight and crisp. The best tool to use for this is a bench sander where you can lay it flat and let the machine do the work, however if you don't have one, you can accomplish the same task with some hand sanding. Just be ready for some work.
Step 4: The Four Elements
There are a lot of variations to the stones, so I opted to take the patters directly from the movie, which I profusely enjoyed watching for the 50th time. The four element stones in order to the image, use four distinct line patterns;
The Air Stone: 6 wavy lines what wrap 90 percent of the way around and are at the top of the stone. The wave rises on the left and falls on the right
The Fire Stone: 5 wavy lines on the back, 4 on each opposing side. Lines are vertical and at the bottom of the stone. **My thought on why they didn't use 6 lines was that they created the stones using polystyrene and more lines would have created thinner, more fragile walls between.
The Earth Stone: 6 straight lines that wrap 90 percent of the way around and are at the bottom of the stone.
The Water Stone: 6 Wavy lines that wrap 90 percent of the way around and are at the bottom of the stone. The wave rises on the right and falls on the left.
Because of the different technique in creating each stone, I'll tackle them independently, giving each its own step. Note that the water/air stones use a similar design that is simply reversed.
Step 5: The Earth Stone
The earth stone was the easiest of the bunch. The best place to start is with the back cuts since they go all the way through. With the router set in the table, I installed the 1/4" straight bit and adjusted it to a cutting depth of 1/4". I then moved the guard back 4" from the bit creating a small .5" gap between the piece and the blade. Next I marked, directly on the table a line running 45 degrees to the guard and passing directly through the center of the bit. From there I marked 6 additional lines to the left, and 6 more to the right of the center line, at 7/8" spacing between them. This would create the distance, on center for each of the grooves in the stone.
The way it works is, by clamping a straight edge along the lines, you can set a guide jig that will help you cut symmetrical channels as you draw the stone toward you. The reason for this is that its easier to create a straight line pulling towards yourself than it is by pushing away. For the back side, you'll only be working with the 6 lines to the left of center. Set your guide bar at the first line to the left of center and, pulling toward you, carve your channel. Move the guide bar one line over and repeat. Continue until all 6 lines have been created.
Unlike the back, the lines on the two opposite sides do not go all the way through edge to edge. They connect to the back lines, however they stop .5" from the front edge of the stone. Adjust the guard so that it is 2.5" from the center of the bit. This time you'll plunge the piece onto the bit and then draw towards yourself. Repeat the process using the same 7/8" adjustments as you did on the back until all 6 lines are cut.
To do the other side, you'll need to flip the piece over and use the 6 lines on the other side of the table. Continue, as you did on the first side until all six lines are cut.
Step 6: Air, Water and Fire Stone Template
It's much easier to create your lines for the remaining three stones if you first fabricate a template. I used a scrap piece of board to create a 'french curve' that would assist me in making the lines and used my scroll saw to cut it out.
The pattern is simple; For the fire stone, the lines are 5" long and have two waves. I started by drawing a line dividing a 5" piece of board half way down its length. I then drew a line dividing its width into two 2.5" sections. Then using a large round object, I created a wave form with one 2.5" section rising above the center line and one 2.5" section falling below it. I then split my board down this wave and smoothed it on the bench sander.
For the air and water stones, they are essentially the same wave but reversed. I repeated the process I used for the fire stone, however I divided it into 1.5" sections making a smaller wave. Splitting it down the wave gave me two mirrored pieces which would work for the air and water stones respectively.
Step 7: The Water and Air Stones
Water:
To create the water stone you need the pattern half that rises on the left and falls on the right. As with the earth stone, the lines on the back go edge to edge however the on the sides they stop .5" from the front.
**Note** Normally I would clamp the piece I'm working on down and use my pattern as a guard to run the router along making perfect lines, however, due to the odd shape of the stones, this was nearly impossible. Trusting in my ability to make straight lines, the old fashioned way, I simply marked the position of the line and created them manually, drawing towards me on the cut.
If you intend on freehanding it, as I did, then the process is simple. Mark 6 lines on the bottom of the stone, using your template, spaced .75" apart. When you create the sides, pay attention to the rise and fall of the wave and adjust your pattern accordingly. The line should wave fluidly around the stone stopping short of the front edge on each side exactly .5".
Air:
The process for making the air stone is identical to the water stone, with the exception that the wave flows in the opposite direction, and the lines are at the bottom of the stone
If you figure out how to clamp this odd shape down and use your template as a guide, feel free to let me know in the comments. My lines turned out as good as I could have hoped, but it can be a bit nerve racking doing them freehand.
Step 8: The Fire Stone
The fire stone is unique, in that its the only stone that doesn't have 6 lines per side and that its lines are vertical. My guess is that, since they were using polystyrene to make the props for the movie, there was a concern about them being to fragile with too much design work on it. As such, the movie version had 5 lines on the back of the stone, and 4 on each opposing side.
To create the lines, measure exactly half the stone at 5" and draw a line all the way around. This is the topmost stop point for your lines. Next, using your template make your wave in the same direction that you see in image #2, spacing them .5" apart on the back side (5 lines) and .6" apart on the two opposite sides (4 lines).
Again, carefully draw your router toward yourself and trace the contour of the lines, plunging to start the cut at the top.
Step 9: Refining Your Lines and Adding Cracking
To refine your lines, you can wrap a piece of sandpaper around a dowel or pen and use it to smooth the contours of the lines, however I found it faster and more effective to use my dremel with a conveniently sized stone bit. I just simply traced all of my lines I created with the router, smoothing any bumps that may have occurred while freehanding the stones.
Cracking:
For the cracking, I switched to a micro wood sculpting bit in my dremel and started to carve lines using a bit of chaos. Now, for mine, I didn't follow the movie precisely, copying every single crack and pit in the stones, but rather opted to freehand my pattern. If you did want a more screen accurate pattern, they do follow a bit of a formula. 90 percent of the cracking on the movie stones starts in the top left corner and flows in a lightning bolt pattern down and to the left, often originating in the flat space between the sides.
**Note** Make sure your lines are deep enough and prominent enough as the paint we will be using is extremely thick. If your lines get covered during painting, don't worry. You can use a screwdriver the trace them, while the paint is still curing, to ensure they stand out better.
Final sanding;
After you've cleaned the edges of your grooves, and created your cracking pattern it's a good idea to give your stones a final sanding. Because we'll be using a stone textured paint, you don't have to worry about sanding with too fine a grit. 150 should be sufficient to get any major burrs out.
Step 10: Drilling the Tealight Recess
To drill the recess for the tealight, mount a 1 5/8" spade or forstner bit into your drill press. If you don't have a drill press, don't worry, this can be done quite easily with a cordless drill. Measuring from the center of each .5" space, to the side that's opposite to it, make a line, then repeat for the other two sides. You should now have the center of your stone. Use a nail set and mark it.
You'll need to secure your stone in a clamp or vise as the width of the bit will cause it to buck otherwise. Once your stone is clamped into your drill press, drill down .75" into the top of the stone, You can drill deeper if you intend on using longer tealights, or actual candles.
Step 11: Painting
For my stone texture, I used Rustoleum stone accents in a tan color. Its very difficult to get into narrow spaces with this paint, so I recommend first painting the stones inverted, letting them dry a bit, then painting them again from the top down. It took two full coats of paint to finish the stones which ended up being two full cans, so it was fortunate that they were on sale.
Once your paint is sufficiently dry, I recommend going over your stones with some 100 grit sandpaper, with very light strokes. You only want to tame down any excessive bumps the paint leaves behind and not reduce it to bare wood.
Step 12: Details
For my detail work, I used my airbrush and some basic acrylic paints. I generally mixed my water/paint ratio at about 20-1, making it extremely thin. The colors I used were brown, tan, black and orange. Brown was used inside the grooves to darken them and give them contrast, with small shades down the stone. The black I used around the base of the stones, and around their centers where they would be held by dirty hands. I then gave them an overall light blast with the orange to make them look a bit more like desert sand, then the tan, to blend it all together.
You don't have to use these exact colors as aging things is an art form unto itself. These are just my suggestions as to what I found worked best for me.
Step 13: Finished
That's it. Next time you have a dinner party, you can set some mood lighting with your element stone candles that will have your guests asking questions. I put my stones outside near my star gazing bench so that I can have a bit of dim light as I look up at the sky.
I hope you enjoyed the instructable, and as usual, thanks for following.
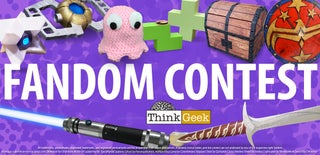
Second Prize in the
Fandom Contest
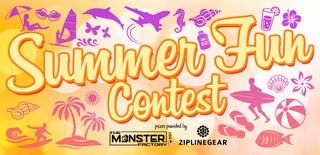
Participated in the
Summer Fun Contest
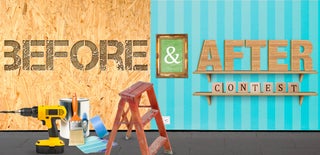
Participated in the
Before and After Contest