Introduction: 1 Plywood Sheet = 1 Console Table
The title says it all, one sheet of plywood can turn into this beautiful, bold console table. Since it's completely made from plywood, you get the style of a solid wood table while remaining lightweight and easy to move around the house. I've seen tables like these sell at luxury furniture shops for well over $1,000 but if you keep your cuts straight and your angles at 90°, you'll have your own single sheet console table for much, much less!
Purchasing through the following affiliate links supports me as a maker :)
Supplies
Necessary supplies:
¾ inch sheet of 4' x 8' plywood. (I used Sande veneered plywood from Home Depot)
Useful tools:
Table saw (or circular saw with a guide)
Miter saw (or circular saw with speed square)
Paint brush and old T-shirt
Step 1: Size & Layout
The challenge was to fit an ideal sized console table into the footprint of a single sheet of plywood. Holding to this requirement, the proportions felt best when the table size was 60" long x 30" tall x 14" deep and the body was a consistent 5" thick.
I designed the assembled table in CAD first and exported the individual panels into a new file that arranged the pieces into a flat plane on the outline of a 4' x 8' sheet of plywood. This way, when I modified that assembled shape, I could check the flat file to see if the pieces would fit in one sheet of plywood. These dimension can be modified and traded for different proportions of console table while still remaining on one sheet of plywood (i.e., you could make a table that is a consistent 3" thick and 15" deep instead).
I've attached the assembled and flat STEP files here if you'd like to edit or build this same table!
Step 2: Design
To achieve the solid wood aesthetic, I needed to hide all joints to make sure none of the layers in the plywood were visible to disrupt the wood grain. This means lots and lots of 45° rip cuts. Thankfully, every cut is either at 45° or 90° so it was quick to switch back and forth. While I was building it, I was concerned about stability since the only thing holding this table together is glue, but I have one of these tables in my house that has been strong and stable for 2 years. You are welcome to add supports or ribs to strengthen the table, but I didn't feel like that was necessary. The cut list for this table is attached as a PDF and please pay close attention to the direction of the miter (it's very easy to cut the 45° rip in the wrong direction!)
Attachments
Step 3: Ply Prep
I always find it is easier to sand the entire sheet of plywood instead of sanding each piece individually after cutting. This sheet was relatively smooth to start with so I went over it with 240, 320, then 400 grit sandpaper in my orbital sander. Remember not to push down when sanding to avoid putting scratches and pigtails into the surface!
After some light pencil marking to map out my shapes, I used a combination of my table saw and circular saw with a guide to get all the miters and angles right. This is a great point to stop and do a sanity check to make sure all the pieces are cut the correct direction and size (confession: mine were not but I was able to make a sneaky fix!).
Step 4: Glue Front Face
I found it easiest to start by gluing the front face together first. These angles are pretty reliably 45° and will provide much of the strength and accurate shape of the table. I laid a small piece of plastic film under the joint to keep the wood glue from bonding the pieces to my workbench and clamped them in place. I came back about 2 hours later when the glue had set.
Step 5: Glue Outside Faces
This part gets tricky. I had to get creative with my limited selection of clamps and some spare bricks but it worked out well enough. Start with the top face and then do the side faces after the top face has dried. Just spread the wood glue as evenly and apply pressure where you can. I don't recommend the painters tape method for these joints since it will block visibility of the joint to see if it lines up correctly. I found these right angle guides to be super helpful to clamp to. Don't worry too much if you have a gap or overlap since we'll fix that with some wood filler and sandpaper later and no one will ever know!
Step 6: Glue Inside Faces
These faces were much easier since I had an edge to clamp against on the other side. I put some scrap 2x4s inside the table as spacers to lay the inside faces against. Again, start with the bottom inside face and come back to glue the inside side faces once the glue is dry.
Step 7: Sand and Wood Fill
With my limited ability to clamp the pieces together precisely, I ended up with gaps and overlaps all over the table. For the gaps, I found that wood filler was a much better solution over wood glue + saw dust because of how large the gaps were and the ability to stain after it dried. After the wood filler dried, I went over all the edges with 400 grit sandpaper by hand until I was happy with the shape.
Step 8: Cut to Height
This is a great time to check it's overall dimensions and how it will sit in the house. I found that the length of my legs were not perfectly even with each other which was causing the table to tilt out into the room. My circular saw took care of that by cutting a new flat and level plane on the bottom of the legs.
Step 9: Quick Comment on Stain and Finish
At this point, the table is finished and the last few steps detail how I prefer to condition, stain and seal the soft plywood. You are welcome to finish the table however you like best, but keep in mind that the veneered plywood is very soft and needs some love to take stain well.
I suggest keeping some of your plywood offcuts and do lots of stain tests before doing anything to your band new table!
Step 10: Wood Conditioner
DON'T SKIP THIS STEP!
Since I was using softwood veneered plywood, I needed to douse the table in oil-based wood conditioner. If I hadn't conditioned it thoroughly first, my stain would have been a blotchy mess with light and dark patches all over. Conditioning may seem extravagant or unnecessary, but I promise the result will be 10x better if you take the time to condition it.
My favorite conditioner is the Varathane Pre-Stain Wood Conditioner but the Minwax one is excellent as well (it just cures in the can faster than Varathane).
Use a rag or a brush and apply lots of this conditioner to your table. You want the wood to drink it up and leave the conditioner on there for about 30 minutes. Then, use a rag to wipe any extra conditioner off the surface and wait about 2 hours for it to cure. It's a good idea to condition some offcuts of the same wood so you can do some test stains.
Step 11: Stain
Before you stain, I recommend doing a couple test runs on some spare off cuts of the same conditioned wood. I like the Varathane oil-based wood stains (not the 2-in-1 stain and sealers, those are streaky).
Once your wood is conditioned and dried, wipe away any sawdust with a rag and get ready to stain. I work in small areas because the darkness of the stain depends on how long you leave it on the wood. Using a brush, I generously coat the wood with the stain and quickly wipe any excess off with a rag. I find that wiping quickly also gives less chance of there being blotchy areas in the stain.
Step 12: Polyurethane Finish
This is also an important step not to skip! If you don't seal your work, any water or moisture will leave raised areas in the surface of the wood and obvious discoloration.
Again, I like the Varathane oil-based polyurethane and usually cut it with a small amount of mineral spirits so it goes on smoother (but takes longer to dry). I use a fine brush and apply in large areas to avoid any streaks or gaps in the finish.
After my first coat, I gently go back over the dried finish with 800 grit sand paper. This is just to flatten any dust that got in the curing polyurethane and knock down any grain that may have risen up. Second coat goes on with a brush again in large areas. For an interior piece, 2 coats is usually sufficient but I went for 3 on this one because I had some streaks in my second coat.
No matter how well I lay down my final coat, I always have a rough surface when I'm done. My secret trick is to cut up a brown paper grocery bag and use that like sandpaper over the whole table. I picked up this trick a while ago and the texture of the bag mixed with the wax coating they put on grocery bags is perfect to gently knock down any imperfections in the final coat and leave some silky smooth wax behind. After I use the brown bag trick, the surface feels like a mirror!
Thanks for reading and I hope to see your table soon!
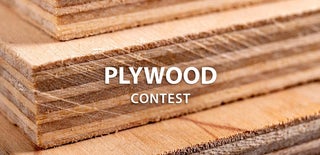
Second Prize in the
Plywood Contest