Introduction: 100+ Year-Old Church Door Red Oak Coffee Table
In this article I'll show you how I made a coffee table (20" wide x 40" long x 18" high) from an old church which was replacing the old red oak doors. These 4 red oak boards were 8/4 (1.75" thick final thickness) when I got them and yielded the final thickness of 1.25" thick when the table was finished. A bit of stain, polyacrylic, and some 17" long 3 rod 1/2" hairpin legs finished out the project.
To start this project you will need:
Wood and Materials:
5 - 8/4 boards 5.5" wide and 38" long
4 - 17" Hairpin Legs of your choosing
Stain (or not)
Sealer (if staining)
Finish (your choice)
12 - 1" self-tapping wood screws
8-12 - 1/2" washers (or what will fit your screws)
6 - 3/8" wood dowels
Wood glue
Biscuits (#20) or Dominoes (6mm)
Various grits of sand paper
Stain/Finish applicators
Clean cotton cloths
Tools (basic list):
Table saw, jointer, planer, router, router table, sander, biscuit jointer, drill/driver, circular saw, straight bit, 1/8" round over bit, rabbeting bit, hand saw, 3/8" drill bit, vix bit, scratch awl, philips/square head driver, 24" clamps, mallet. (Some things may have been left out or over looked, if so, feel free to let me know in the comments)
Let's begin.
Step 1: Milling the Lumber
I always start my milling with a jig saw as the boards may be warped. Warped boards can pinch the blade of a circular saw and cause a kick back of the tool which is not a fun experience. Binding can still happen while using a jig saw but the action of the jig saw produces no kick back therefore it's a safer option for breaking down rough or reclaimed lumber. I cut the pieces to rough length first leaving about 1 inch of extra material. (Be sure to remove any metal from reclaimed or urban lumber)
Over at the jointer I flatten one face of each board. Maintain downward pressure on the outfeed table once the board has passed the cutterhead. This produces a flat face and reference surface for the next step. Flatten one face of each board in this manner paying attention to grain direction.
The planer is the next step in the milling process. Put the jointed face down on the planer bed and feed the board into the planer removing about 1/16" or less per pass. You can see where there were nails in this board. I milled the boards to just over 1.375" thick to get rid of the hinge mortises.
Back at the jointer I place a reference face up against the fence (which is 90 degrees to the table) and joint an edge flat and square to the faces.
Cut List:
4 - 6/4 x 5" x 35" boards for the panel (add 4" if making integral tenons on the panel for breadboard ends)
2 - 6/4 x 3" x 21" boards for the breadboard end (overhang will be trimmed)
*Keep some scrap for loose tenons if you make breadboard ends as I did.
Step 2: Rip to Width and Arrange
Over at the table saw the jointed edge is referenced on the fence and the boards are cut to their final width of 5". They are then placed on a flat surface and arranged in a pleasing manner. Any defects are pushed past the final length area for trimming.
Step 3: Optional: Dominos/Biscuits for Alignment
Because I have a Festool Domino I used them to align the boards so I had less planing to do after the glue up. I like to make one board with a tight mortise on each end and the rest loose for easy alignment. This makes it easy to fit the boards together when glue has been applied.
Step 4: Glue, Dry, and Scrape
Edge joining boards is really easy. A little bead of glue on each board, rub them together to spread the glue and squeeze out the air, add a little clamping pressure for good measure and wait a few hours for it to dry.
Because I used the dominoes for alignment I had to only remove glue squeeze out from the surface of the boards. I use as carbide scraper for this as it makes quick work of the dried, brittle glue.
Step 5: Trim to Final Length
You can do this with a circular saw following a chalk line, a circular saw on a shop made track board, a crosscut sled on the table saw, or as I did with a track saw. Just be sure to get a good flat end for the next step.
Step 6: Making the Breadboard Ends
This can be done several ways. A quick Google search will show many videos on the process. I first used a rabbeting bit in a hand held router to make a rabbet on each end and face of the coffee table panel, essentially giving it a really long shoulder-less tenon. Then with a straight bit in the router at the router table I made a groove in a 3" wide board (the same thickness as the rest of the material) which was the same width and depth as the tenon on the panel (actually about 0.004" wider as that will make the fitting easier when glue is applied).
The Domino XL excels (see what I did there?) at making bread board ends. I made 3 sloppy mortises in the rough center of the panel (the tape references the starting locations) and do the same for the mating pieces with the grooves. Loose tenons are milled and fit into the mortise. Glue all of the tenons in now keeping them fully seated and in the center of their mortises. Let the glue dry completely for the next step.
Step 7: Attaching the Breadboard Ends
To save time and clamps I drawbored the underside of the breadboard end. Again, a quick Google search on the topic of drawboring can easily give you more info on this technique. Essentially, the holes in the tenon are set about 1/16" closer to the rabbeted edge so when a dowel is driven into the end board the offset hole pulls the end board tight to the panel's shoulder.
Step 8: Sanding and Round Overs
I sanded the surface with 80, 120, 150, 180, 220, and 320 grit paper on my Random Orbital Sander. After sanding with 180 I profiled the edges with an 1/8" round over bit in my trim router. Then continued with 220 and finished with 320 grit discs. Normally I would finish with 220 but I decided to stain the table so I wanted less scratches for the dye to settle into. Scratches are seen very quickly when staining wood.
Step 9: Staining and Sealing
This is a method I learned from Gregory Paolini. It is usually used on white oak but it looks just as good on red oak. The fist step is to dye the surface with General Finishes Vintage Cherry Water Based Dye Stain. Cover the surface evenly with a foam brush or applicator pad and wipe off the excess with a dry cloth when the surface has been covered. Let that dry for a few hours. Now with Minwax Walnut Oil Based Stain (I know, oil over water?) rub the walnut stain into the grain any way you can and wipe off the excess with a clean dry cloth immediately. This darkens the wood grain but leaves the nice reddish brown from the vintage cherry dye. Let this dry for at least 8 hours. Now apply a coat of Bullseye SealCoat Dewaxed Shellac to seal in the stain so the finish coats don't reactivate the color.
Step 10: Finishing
I used Minwax Polyacrylic in my HVLP spray gun to apply the top coat. You can brush it on or use any other finish you choose.
Step 11: Attaching Hairpin Legs
I like to have two drivers and two squares ready with me when I attach hairpin legs. The squares help align the legs to the side and end and the drivers make drilling holes and driving screws fast. Other things like vix bits and scratch awls make work easy too. One main thing to remember is wood moves. If you don't make the holes in the leg plates bigger to allow for the screw to move with the wood you will have the wood split on you or the table will warp with the seasonal changes in humidity. Notice the washer in the last photo to support the screw over the larger hole. Be sure not to drill through your finished table. It may be reclaimed wood but it is far from rustic at this point.
Step 12: Flip It Over and Place It!
You're finished! Go move it into your house, add some coasters, magazines, or some socked feet as you relax and admire your handiwork.
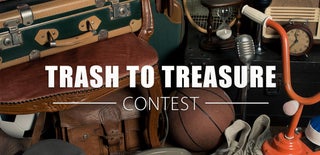
Participated in the
Trash to Treasure