Introduction: 2 Shovels to Repair and to Improve
My father helped his neighbour to remove some large bushes from his garden. Those bushes had some thick roots so just digging around the roots was not easy. My dad used a lot of force on his shovel and the wooden shaft broke. Then the neighbour came with his shovel and some hours later the shaft of that shovel also broke at exactly the same position.
In the evening they had dinner together and during dinner they discussed about the broken shafts. They agreed that it would be better to get a shovel with a shaft made from steel. Such shovels are commercially available but usually very expensive. My dad said that his daughter might be able to weld such a shaft and the neighbour mentioned that he had a piece of stainless steel pipe in his barn, so they decided to ask if I wanted to repair their shovels.
I like welding and I also like the fact that these two men were helping eachother, so I agreed to repair their shovels for them. I am quite sure that shovels with a wooden shaft always break at the same point, so I decided to document the repair process because it is likely that some of you also have had a broken shovel before.
Supplies
Materials:
- Broken shovel
- Stainless steel pipe with nearly the same diameter as the original wooden shaft. I used a 1" schedule 40 pipe.
- Welding equipment.
Step 1: Remove the Remaining Wood From the Socket
There is a pin which holds the wooden shaft in the socket. I used a grinder to remove one of the ends from the pin and then I could remove the pin quite easily with a hammer. From one of the shovels the wooden end came out relatively easy, but in the second shovel the wood was stuck inside. There I used a long drill bit and drilled some holes in the wood until it came out of the socket.
Step 2: Reduce the Diameter of the Steel Shaft Near One End So It Will Fit in the Socket
The stainless steel pipe that I got had the same diameter as the original wooden shaft. But the wooden shaft has a sharp point so it will fit in the socket. To get a strong shovel, I wanted the stainless steel pipe also to fit in the socket of the original blade.
I measured the diameter of the socket and decided that I would cut 4 wedges from the end of the stainless steel pipe over a length of 15 centimeter. You can see the wedges on the photo. They are 6 mm wide at one side and just 1 mm wide at the other end. Then I used a clamp to push the metal of the shaft to the position I wanted and welded the pieces together. You can see on the photos how I did that.
After welding I brushed the welds to remove the discoloration.
Step 3: Weld the Shaft Into the Socket
I pushed my stainless steel shaft into the socket to a point where it was stuck. Then I welded the shaft to the socket by filling the groove, filling the two holes of the original pin and I also welded the circumference of the end of the socket to the shaft. Now it is very strong and it is unlikely that it will ever break again.
Step 4: Make a Handle Grip
I cut a short piece of stainless steel pipe to the same width as the original handle grip. I used a hammer to make the ends a bit flat and cut a small piece from a strip to make end caps. Then I welded the end caps on the handle grip and brushed the welds to make them shiny.
Step 5: Attach the Handle Grip to the Shaft
There is an easy trick to make a T-shaped connection on two pieces of pipe. Just cut at an angle of 45 degrees as shown on the photo with a grinder. The two pieces of pipe will fit together quite well and can be welded.
Step 6: Brush the Stainless Steel to Make It Shiny
Stainless steel pipe can be made very shiny by brushing it with a stainless steel brush. The left shaft on the photo was already brushed and the one at the right not yet, so you can see the difference.
Do not use a steel brush as tiny particles of steel will contaminate the stainless steel and will cause corrosion.
I used a stainless steel wire wheel on the grinder for this.
Step 7: Paint
I decided to paint the parts where I welded the new stainless steel shaft to the steel blade to protect the welds and to make the shovels look better.
Of course the paint will not last very long on the blade itself during digging, but for now it looked good.
Step 8: Ready
The shovels are ready so I gave them back to the owners. I am sure it will now be much more difficult to break the shovels again.
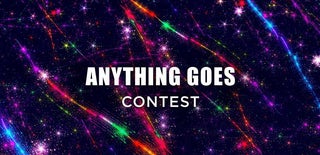
Participated in the
Anything Goes Contest