Introduction: 200 Foot Outdoor Staircase Made From Pallets
The lakefront is down a 200 foot hill, dropping at least 40 feet in elevation. Its a great sledding hill. In the summer the old folks need a staircase to get up and down. I'm quoted around $45,000 to build it: not gonna happen. So here is how I built it for about $2000, using pallets and supplies from the home improvement store.
Supplies
1) 50+ pallets: used, new, anything not totally falling apart, sized at 40x48. check craigslist, facebook, someone is always trying to give these away.
2) bucko numbers of cinder blocks and cement pads: these are between $1-2 you'll need dozens of them. they are 16" x 8" x X" big where the "X" is 2", 4", 6", and 8". I also stacked them in some cases.
3) 300+ 1x6x72" dog-eared pressure treated fence pickets:. - these are also $1-2 and they are the cheapest pressure treated wood I found that I could use to cover the pallets. They are so cheap they are typically not sanded, this actually works in our favor and now the stairs and decking are not slippery.
4) buckets of deck screws:. - much better than nails. 1 5/8" was my goto size, but on occasion I needed 2", and 3" versions as well.
Step 1: Basic Concept
Pallets are great material. They are generally made of hard wood so they last. You can usually get them for free, business are always trying to get rid of them. They are also designed to handle a lot of weight they are very strong. The issues with them are: 1) they are butt ugly and usually all beat up. 2) getting useful wood out of them is not worth the effort, 3)They are still wood, so they will rot.
This build addresses all of those issues. First off, we are going to "skin" or completely cover the pallets with a finished uniform wood surface so it doesn't make any difference what they look like. Secondly we will not modify them for the most part (except to cut them shorter for the "half steps" (the steps that go between the full pallets when we are on a particularly steep section.) and finally, by using the concrete pads and cinder blocks, we avoid having any wood in direct contact with the ground: this is crucial to stop the pallets from rotting out.
You will also notice throughout this build I have a supply of concrete pads and cinder blocks. They all are 16 x 8 inches with a height of 2,4,6,or 8 inches. this is so I can level each of the pallets based on the actual terrain of the hill. This makes for minimal digging, no footings to be poured, and all around a very simple way to build things. All I do is dig a sort of flat spot on the hill on the 4 corners of the pallet put the 4 concrete blocks to get them to be level (for example, the 8" high ones downhill, and the 2" high ones uphill.) If there is a double fall line (skiing term, meaning the hill changes slopes in two directions,) mix and match or even stack the blocks to get a level 4 corners for the pallet. I realized early on I could use the uphill 8" of a pallet to be the front support of the next uphill pallet, so I soon adopted only needing 2 concrete supports on the uphill side on the ground for every pallet step.
It should be noted that I built these stairs from the bottom up for this reason. I also was too lazy to dig up stumps of trees, and also followed the property line, added some decking areas the exact same way, and it ended up really a great conversation piece.
Step 2: The Construction
the structural components are really quite simple: level 4 points in the ground to put the concrete blocks, place the pallet on top of it, shim with flat pieces if it rocks a little. This actually takes about 10 minutes to do. I actually have each of the pallets tilted slightly uphill so if someone falls, I hope they don't roll down the staircase. The slats of the pallet are pointed with the staircase. That is the 40" measurement of the pallet. Across the hill is the 48" width of the pallet and I've already cut down all the dog-ear pickets to 48". I line them up cleanly on the good side of the property and let the bad edge (if I'm uneven) stick out on the woods side. The dog ear pickets are not really strong enough to support weight like deck slats, but the slats of the pallets are so close together its totally fine.
Step 3: Working With the Terrain
one of the nice things about this technique is its ripe to work with the actual terrain of the property. My woods bowed in at the bottom, there was a few stumps of fallen trees here and there, and I just used my imagination to link the pallets together to weave around them.
When you tack the boards down to the pallet, make yourself a space block of wood or two to put between the two boards so they are spaced evenly. look at the pictures or pdf this out for more notes.
Step 4: Up the Hill We Go!
what can I say; wash rinse and repeat. note how the nice the zig-zag follows the edge of the woods. I won't bother mowing on the woods side, just let the woods grow in. The last pic shows when I cut up a pallet into 3 sections of 12"x48" You add a 2x4 and some board pieces across, and for the big vertical steps when the hill is steep, make what we call the half step. Half step is a bad name. its a full step, just made out of "half" (ok less than a third) of a pallet. Screw that half pallet With longer deck screws to the lower full pallet so it doesn't move around on you.
Step 5: A Little Flair
well the tree line at the top cut back quite a bit and then went off at a diagonal. Plus Uncle Bob (70 year old smoker,) will be quite tired after all those stairs; wouldn't it be nice to have a little place to rest before the rest of the climb? So lets make a 2x6 grid of pallets (7'x12') deck to cover the traverse the distance back to the tree line (a 40"x12' walkway would of looked a little spindley, We call this deck "basecamp 4" after the last stop on Mt Everest before the ascent to the peak.
Step 6: Panel Work.
this really cleans up the project and gives it the wow factor. you want to panel the side. the dog ear pickets came at 72", and I cut them down to 48" that left me with a huge pile of 22" boards that I just pieced together to make the panels.
Step 7: Extra Credit.
Being 250 feet from the house, and down this staircase. who wants to lug the beach stuff? I'm an expert at ground level decks now, and stairs, so lets put in a shed for the lawn chairs, floaties, etc, and tie it all together.
Another thing nice about this style is the stairs are right off the ground. you are welcome to step off the stairs onto the lawn and back again where ever you like.
I do know I don't have a railing on it yet, (except for the one piece I have at the walkway at the bottom, see the pics,) but its coming. It will be made from metal pipe and on the woods side of things. Still working the kinks out of how to get that installed.
Step 8: Enjoy Time!
Step 9: Update 2020/09: Adding Railing.
I really didn't want railings, but some folks needed them so It's time to add them. Again, I'm trying to do this on the cheap, but I still want it to look nice. The cheapest but usable solution was using the 2" x 2" pressure treated balusters, some 1x2's for diagonal supports, and the rails themselves are made from 1 3/8" chain link fence top rail pipe in 10' sections. I also needed some 90 degree elbows for the pipe (4 of them) and the pipe cap holder thing.
Now the 2x2 wood is a little small to hold the cap, so I thickened it up by gluing 4 squares of paint stick around the top. This made a snug fit for the cap, and then I drilled from the side of the cap and put a wood screw to keep the cap on the wood.
All the pipes were connected with the connector pieces that are part of the pipe, but as I don't want them to separate when someone is pulling on the pipe, I drilled them and put a 1/4" screw in.
The reason it took me so long to put the railing up is I hated the look of the galvanized pipe railing on my nice wood stairs. Wood railing would be ridiculously expensive, and not to mention heavy, so I would need a lot more than just 2 3" screws to steady it. (the balusters are just screwed into the stairs at the bottom) I toyed with the idea of painting the pipe a wood color, but paint peels off galvanized pipe. I finally found 1 1/2" shrink wrap tubing that comes in colors, specifically tan. I put the shrink wrap over the tube, and put the tube in a gutter. I then used a heat gun to blast the shrink wrap and it tightly fit around the pipe. The gutter keeps the head concentrated instead of dispersing.
This got me the color I wanted, will not chip or peel, ended up being a a nicer finish that I could every hope to paint.
The whole railing cost me about $350, with the shrink wrap tubing costing $100.
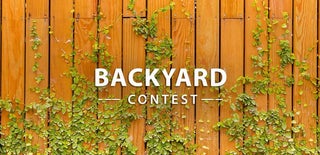
Participated in the
Backyard Contest