Introduction: 360 CNC Clamps (aka Bit Savers)
Hi guys!
So here i'm going to show you some incredibly simple, super adjustable 360 CNC clamps that I've created.
Short Overview/Need for the Design
So a few months ago I was quite luckily given the opportunity to own an ISEL 4030 3-axis CNC machine. I'm familiar with various machinery ranging from the typical workshop hand tools, pillar drills, and band saws etc., - to the odd Laser Cutter and 3D Printer - however, prior to this opportunity, i'd never used/operated a CNC myself.
As a CNC beginner (which is a generous statement - if there was a level below this - that would be me :)! ) - I began to research and experiment with various software's, general CNC terminologies, and general principals/techniques.
After a few short weeks I was ready to begin some practical experiments. I utilised SolidWorks to create and design parts, which were saved as .STL files - DeskProto to create and modify tool-paths (saved as .NCP) - and finally KAY to read and translate the tooling G-Codes through to the CNC in order for the machine to work.
After a few short runs I grew some confidence - hastily jumping from foams, to model board, and finally to hardwood.
However, each time i'd set the CNC up to run a tool-path (being the impatient maker that I am) - I would try to maximise the amount of space I could machine per material block - almost to within 1-5mm. (This is where the need arose). So, - whilst being impatient and over eager to utilise as much material as possible - with little CNC experience - combined with a desire to get satisfactory results whilst learning as much as possible (with as few mistakes as possible) - I would watch each CNC test - often with my heart in my mouth each time the tooling path grew closer to the ever-so-threatening bulky metal clamps that came with the CNC.
A few test runs in, i'd already hit a clamp once, and very much almost (1-2mm) again on several other occasions. - So I decided that I would need to somehow remove the hazard of a bit clashing with a clamp or similar whilst on an active tooling run.
Insert design solution:
(I would like to emphasise that these clamps are suggested for the intentional use by beginner CNC operators - and it is acknowledged that with progressive tooling/operating experience etc. it is understood that the setup/tool-paths should never interact with clamps or similar - and that these clamps act almost as 'bike-stabilisers' for a CNC - if you will - and have only been designed for the intended purpose of enabling a looser tolerance in relation to error flexibility for beginner operators :)! )
**NOTE**
**One great thing about these little clamps is that they don't have to be made with too much of an emphasis on the degree of accuracy; as-long as the clamps follow the rough suggestions with this instructable and somewhat mimic the premise/technique - because they are completely adjustable - the clamping and tightening functions (through the bolts used) will allow the clamps to almost find their own sweet spot for each piece!
If anything, I think a little wonky/unique may help - as the aim of these clamps is to secure the block to the CNC bed by finding their own positions :)!**
Supplies
Processes/Tools/Materials:
Processes (In order):
1. Cutting, (Metal Band Saw - or a Grinder)
2. Drilling (Pillar Drill)
3. Filing
4. Riveting
5. Cutting (Band Saw)
6. Buffing (Linisher)
7. Assembling
Tools:
1. Band Saw
2. Pillar Drill
3. Metal File
4. Rivnut tool
5. Linisher
6. Allen Key set
Materials:
1. 1x 90-degree folded 3mm Galvanised Steel Bracket (200mm x 30mm x 30mm) - (Dimensions, material and fixings are entirely changeable - feel free to design and tailor the clamps based on what materials you have access to :)!
2. 8x M6 Rivnuts
3. 8x M6 Allen Key Bolts (40mm)
4. 4x M6 Allen Key Bolts (30mm)
5. 1x Wooden Offcut (ideally 100mm x 100mm x 25mm)
6. 4x CNC Bed Clamp Feet (machine/bed specific)
Step 1: Clamp Bases (3mm Galv)
(I was lucky enough to source 2x 3mm thick, 200mm long Galvanised Steel 90-degree brackets at no cost - so I created a second set as a back up :) *See images attached as a reference)
However, essentially the only crucial features here are:
1. The 90-degree bend/angle (a single component strip with two faces at 90 degrees from one another to create a base side and a side face)
2. Suitable space to (*1) drill 2x 8mm diameter holes in the side face roughly 40mm apart (these will each house an M6 Rivnut - which will each in-turn house an M6 40mm Allen Key bolt)
3. Suitable space to (*2) drill a single 6mm diameter hole though the base side (this will house a single M6 30mm Allen Key bolt - connecting the Base Bracket to the CNC clamp foot)
4. For the overall Base Bracket material to be rigid/durable enough to withstand any pressure output from tightening the clamps
Manufacture:
1. Using a Band Saw (or similar) - with appropriate safety equipment - cut the 200mm bracket into 4 even smaller pieces - they don't have to be perfect, we're aiming for function over form :)!
2. Utilising a Pillar Drill & Vice follow steps (*1. & (*2) above
- Feel free to use the images uploaded as a reference guide - although, as mentioned - these clamps may benefit from being somewhat unique in relation to symmetry/accuracy - so don't worry too much about making them perfect :)!
Step 2: Rivnuts/Threads
Using 2 rivnuts per clamp, insert each rivnut through the two 8mm diameter holes that are on the brackets side face, and secure them in place with a rivnut tool. (If you do not have access to rivnuts, or are using a different material, you could always use a tap and die set to add a thread to your Clamp Base).
Once you have your rivnuts secured (or a thread created) - simply screw a 40mm M6 Allen bolt through each rivnut/thread. - These bolts will act as your fasteners, and will essentially push the wooden corner blocks into the CNC material block - creating a clamping action.
Step 3: Clamp Blocks (Wood)
Here we are looking to create some little corner blocks that will serve as cushion pads in order to bridge the connection from the Clamp Base to the material block when the Allen bolts are tightened.
Utilising a Band Saw or similar (and the correct safety equipment) cut your 100mm square block diagonally from corner to corner twice (like bread!), to make 4x smaller triangular blocks.
Once you have your 4 smaller triangular blocks, leaving the outer sides that previously formed the squares edges - carefully cut out a small 90-degree triangle from the tip of each block.
(If your triangle part has its flat base edge facing you - with a corner each pointing left and right - the corner pointing forwards is your target. Simply cut two lines to form an arrow/triangle at roughly 90-degrees so that you essentially have a smaller triangle pointing towards you) - this cut wants to be roughly 10mm per edge.
After you are satisfied with your wooden blocks give them a quick sanding with some coarse sand paper or a linisher to ensure that the edges are mostly rounded - this will make it easier for the block to slide into position when the bolts are tightened :)!
Step 4: Assembly
Once you have your Clamp base created with 2x 40mm Allen bolts threaded through the rivnuts (or similar) - you're ready to attach the CNC bed feet to the Clamp Bases.
Slide the remaining 4x 30mm M6 Allen bolts through the Clamp Base holes and thread on the CNC bed feet.
(Assembly should reference the uploaded images with this instructable)
Step 5: Demonstrative YouTube Video
I've created a short demonstrative video of setting up these mini clamps with my ISEL 4030 to show how quick and easy they are to use.
I typically set up each block that I am milling with 5mm Acrylic spacer pads under the block base to function as waste-board (I find it easier than having a constant base that I have to replace, and feel somewhat more comfortable knowing that not only will my CNC bit be safe if it diverts off course - but it will also have a lovely empty void under the part in case the tooling depth encounters and error. (Acrylic was chosen as it is consistent in its thickness, and is reasonably soft in-case a bit ever went into it).
**SIDE NOTE**
In the video I demonstrate how I set the clamps up from start to finish. The two larger metal clamps that directly contact the surface block either side (left and right) are the original clamps that came with the CNC. Towards the beginning of using this machine I typically removed the side Z-axis clamps once the corner clamps had been sufficiently tightened - however as I have progressed with operating the machine I have begun to leave these on for additional grip as I have developed an understanding of the machines tool-path and parameter capabilities.
Step 6: Finish
And there we have it.
Thanks to anyone whose stuck with me throughout this instructable.. it would be great to see if this inspires anyone to replicate similar clamps or use a similar corner clamping method - as I really have found them to be a life saver on multiple occasions in relation to human/machine error and saving my beloved bits! (No pun intended :)! )
Happy CNC'ing!
Mike
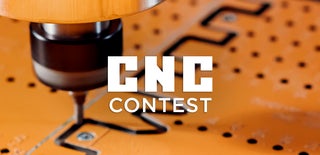
Runner Up in the
CNC Contest