Introduction: DIY Sheet Metal Skateboard
Yo dudes!
(Short overview of myself/what I do - as you might (or might not) be wondering how I have the facilities to make these little boards!)
So from a young age I've always been attracted towards board sports; skating, surfing, snowboarding, paddle-boarding etc. - and have always found myself to be somewhat creative as I love making things! Being a creative, I chose to study Product Design at University. Whilst studying I became somewhat experienced with various tools/machines and managed to pick up the odd skill here or there. Currently working as an Engineer in a sheet metal company I managed to stumble upon the contest.. so I thought i'd enter :)!
-Side Note-
This instructable is somewhat advanced in relation to the machinery & processes used, however i'm sure with a little creativity and ingenuity similar boards could be replicated :)!
I've attached all files from CAD parts & Drawings, to .STL, .AI and .NCP files.
Supplies
Processes/Tools/Materials:
Processes (in order):
1. CAD: - SolidWorks
2. CAM: - Radan
3. Sheet Metal Punching (Amada Turret)
4. Grinding
5. Sheet Metal Folding (RAS 'Up Down Bend', Amada Brake Press)
6. Buffing
7. Powder Coating
8. Vinyl Cutting and Peeling (CT0630 Vinyl Cutter, Illustrator for image editing, Vinyl Master for decal cutting)
9. Gripping
10. Assembling
Tools:
1. Amada Turret or similar (punching)
2. RAS 'Up Down Bend', Amada Brake Press (folding)
3. Metal Grinder
4. Metal Buffer
5. Clamps
6. Vinyl Cutter/Plotter (CT0630)
7. Deburring Tool (grip-tape application)
8. Powder Coating Facility & Spray Equipment
9. Wrench & Screw Driver (board assembly)
10. Safety Equipment (Goggles, Filter Mask/Respirator, Safety Gloves)
11. Scalpel & Scissors (vinyl application)
Materials:
1. 1x Sheet of 3mm Galvanised Steel (650mm x 210mm - Per Board Base)
2. 1x Sheet of 2mm Galvanised Steel (650mm x 100mm - Per Board Top)
3. 1x Sheet of Transparent Grip Tape (650mm x 100mm - Per Board - £4.95 Amazon)
4. 1x Roll of Monomeric Matte Black Vinyl Decal (610mm x 5000mm - £7.54 MDPUK)
5. 1x Roll of Clear Application Tape (305mm x min 50m - £17.95 MDPUK)
6. Various Powder Coating Powders (or a spray can :)!)
7. 1x Standard Skate Setup (2x Trucks, 4x Wheels, 8x M5 Nuts, 8x M5 Bolts, 8x Bearings)
Step 1: CAD (SolidWorks):
(Here is where you'll first create the board's design - if you plan to recreate a similar board from metal, be sure to select the "Sheet Metal Parameters" tab for your part).
I've uploaded images of various screen views whilst creating each board component, as well as exploded and assembled views for referencing. Attached is a multi-page PDF including drawing views, folding detailing and component dimensions.
I first created the board base (P1)with a rough shape in mind - including patterned recesses for aesthetics & ease of carrying (the board can be carried with 2/3 fingers from any hole), drop down bends either truck end to lower the board and riders centre of gravity, and minor edge bends along each board side to increase the boards overall rigidity.
Once the board base was created, I simply took a "Pack and Go" of the part, and saved it as "P2"(Board Top). Once saved, I opened up the board top, and did a simple cut extrude from truck to truck along each board side, and removed the excess material to leave a singular tapered panel to sit on top of the boards base.
Now that the board top has been created, adjust the folding parameters (distance from each board end to the drop down fold) - preferably to be at-least minus 2x the sheet metal's material thickness to ensure that the parts fit within one-another. (If you look at the component drawings attached - you'll notice the difference between part dimensions).
Once you're happy with your boards design - if creating it from sheet metal - be sure to "Flat-Pattern" and unfold all bends to create a flat view to be punched from the 3mm & 2mm Galv sheets (P1 3mm, P2 2mm)- you'll want to be sure to save your part as a ".STL" file (I've attached the individual STL's with this instructable if you wish to replicate the design) - your STL files will essentially create an outline/stencil of the boards overall shape - this is crucial for programming/manufacturing, regardless of the method of manufacture.
Attachments
Step 2: CAM (Radan):
Once you have the STL's for your separate parts, you'll want to program the tooling profiles in Radan (or similar) in order to punch the desired parts (if using sheet-metal punching - If not, - you could always print your STL's as outline guides and plasma cut them :)! *safety equipment required*)
- I've attached the Radan files with this instructable, however please bear in mind, these will only work if you are utilising an Amada turret. Feel free to use the uploaded Radan screen images as a reference guide!
Simply drag and drop your STL files into Radan, select the tooling punches required/available, and create the tooling profiles - be sure to ensure that all parts have corner tags.(corner tags are specified gaps in-between tool punching - typically 0.3mm - 0.5mm (if using 2/3mm Galv) - evenly spaced along straights and corners to ensure that the designed shape has enough valid material remaining to allow a bridge connection from the components to the rest of the sheet material).
Once your profiles are complete, you're ready for manufacture!
Step 3: Manufacturing:
Once correctly setup, your turret should take care of the punching - for this project the total quantity of boards created was 3, with a total of 6 parts nested (no. of parts on a sheet) - 3 bases (P1) in 3mm Galv, and 3 board tops (P2) in 2mm Galv - the total profile punching time for the 6 components was 85 minutes.
Post-punching you'll need to 'break out' your board components from the sheet metal - take extreme care here, as the pieces may still be sharp.
Once broken out, the board pieces will require some small refining and finishing pre-powder coating.
Corner, edge and tag Grinding:
Here we aim to remove all sharp edges and points from the punched pieces - this will include corners (if using a circular punch consecutively to create an external curved edge - see images attached), all part tags, and along all sharp board edges - leaving the pieces completely smooth.
Folding:
Here we are going to utilise a RAS 'Up Down Bed' and an Amada Brake Press in order to create the boards two drop-down features and edge folds.
-You'll require the folding drawings attached to this instructable (PDF) if using similar sheet metal folding machines. Unlike punching, sheet metal folding has a little more flexibility (no pun intended) in relation to tolerances and setup - therefore, regardless of the machining & tools used - the attached drawings should still be adequate as functional instruction :)! Owing to this reason I have not added any linear instructions here, as the drawings and dimensions themselves function as a guide.
Buffing:
Ensuring you are wearing adequate safety gear, clamp all of the punched/folded components to a secured surface and simply buff out any and all face scratches - leaving all the pieces completely smooth and ready for paint.
Step 4: Powder Coating
At this stage you'll be deciding the visual colour aesthetic of the board(s) you'll be making!
(Owing to mobile devices being highly restricted in spray booths instructional images could not be added here).
Ensuring that you are again wearing adequate safety equipment (Face Mask and Respirator, Suit, Boots Gloves), fix or hang each component to be individually sprayed with the chosen colour - carefully and slowly manoeuvre your way around each piece ensuring that no areas are missed. It is advised that less spraying with more layering is attempted as a process if this is your first time spraying - this will ensure that no 'drips' form while the paint settles due to over-spraying. It is also advised that for best results (paint and gun dependant) - to spray with a minimum distance from nozzle to part of around 200mm - 300mm.
A total of 6 individual powder colours were used here - however feel free to have a play and get creative!
If you are replicating the designs - be sure to research whether your spraying process & material require any additional sanding, priming or finishing pre or post spray! (Additionally, if you are using a spray can, be sure to ensure that there is adequate venting, ...or spray outdoors! :))
Step 5: Vinyl Cutting
Here we are going to add some groovy decals to each board giving them their final appearance!
With access to a suitable Vinyl Cutter/Plotter (you could always purchase custom decals sourced online if not), source and download the chosen images/artwork as .PNG's or .JPEG's and open the designs in Illustrator.
Following the images uploaded to this instructable - highlight each image individually and select:
Object > Transform > Image Trace > Make and Expand
This will convert the images downloaded into outlines that are readable by the Vinyl Cutting machine. If any parts of the image that have been converted to outlines are visible that you do not wish to keep - simply separate them from the rest of the design and delete them.
Additionally, if any images have been converted into outlines are somewhat wobbly or flaky (see the attached Instructable Robot image) - highlight the image and select:
Object > Path > Simplify
This will convert the outlined design into simpler smooth lines (easier for the machine to cut, and for you to peel :)!)
Once you are satisfied with the outlines to be cut, save each design individually as a .AI file - be sure to select do not use compression when prompted to save - this is crucial to allow your Vinyl Cutter to be able to read the files.
Once successfully saved as .AI files, you're ready to set up the Vinyl Cutting machine to cut the designs. Choose the desired vinyl roll (Matte Black Monomeric was used for this project) - and feed the material into the machine ready for it to be cut.
Next, open up each design in Vinyl Master and select:
File > Cut > Cut/Plot > Cut Now
Post-cutting you're now ready to peel and separate the desired decals from the undesired external material - this takes some focus and patience, so be sure to go slowly :)!
Simply cut the chosen decals from the roll with some scissors and carefully peel the leftover decal material from the stickers (a scalpel or similar is recommended here as depending on the designs, peeling the material from the sheet requires some intricacy).
Next you're ready to apply the peeled decals onto some application tape - this allows the decals to be peeled from the vinyl backing material - and applied onto the intended surfaces :)!
- See the images attached to this instructable for referencing
Once successfully applied to the application tape, simply cut the decals out and place them in the desired positions (Instructables font decals to the P2 Board Tops - and Instructables Robot decals to the underside of the P1 Board Bases). Once placed, peel off the application tape and discard.
Step 6: Grip-tape Application
Bear with me - you're almost done :)!
We're now going to apply the transparent grip-tape to the board tops.
-A good trick here is to use a burr-removal tool (typically used to remove the burrs from wood) - this can be done with any grip-tape application to a board, and will remove the hassle from application!
Carefully peel and place the grip-tape to each component - ensuring that there are as few bubbles underneath the tape as possible. Choosing clear grip-tape here allows for the powder coating and vinyl decals to still be seen giving a unique aesthetic while still remaining entirely functional as grip :)!
Once the grip-tape has been placed, using some scissors cut roughly around the components shape leaving anywhere from 10mm - 1 inch around. Next, you're going to grab the burr-removal tool - using the sharpened angled edge, simply pull the tool towards and along the boards edges - this will leave an incredibly clean and consistent cut - compared to using a knife or scissors which can be increasingly frustrating.
Once all 3 pieces have been applied and peeled, simply assemble the board tops to the bases, attach the truck setups with the required bolts/nuts... and you're done :)!
Step 7: Finish
A big thanks to anyone whose stuck with me throughout this instructable, I hope it's made sense as its the first I've created, -and i'd love to see whether anyone replicates or modifies similar boards using anything I've uploaded :)!
(The rider imaged is 8 stone - a maximum of 9 is the estimated maximum owing to the material properties - the feedback received was "an incredibly smooth ride with reflexive spring from board to rider").
I received some awesome feedback on these little boards at my local indoor skate park.... and i'd love to hear any feedback/comments online :)!
Cheers!
Mike
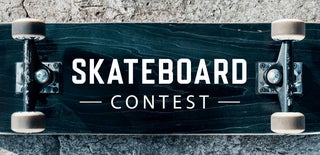
Second Prize in the
Skateboard Contest