Introduction: 3D Printable Phage (A Guide to Modeling for FDM Printers)
The above image is of my finished product, printed in multiple parts, and snapped together. If you don't know what a bacteriophage is, check the link below, it's awesome, and finally, if you like this project, please vote for it in the untouchable challenge!
http://www.phage-therapy.org/writings/bacteriophag...
For my biology project this year, I was allowed use of the school's 3D printer. I had previous modeling experience for our FRC robot, but had never designed something to be 3D printed. Design for 3D printing diverges from traditional modeling. There is no need to control tolerances, as the printer does not work harder, and in some cases is not capable enough, when inputting higher tolerances. You must design, thinking layer by layer... will this overhang be too severe, is this column to thin, etc.
https://www.thingiverse.com/thing:16496
The above link is of a 3D print I attempted. Always check to see if someone else has done it first, and props to the guy who made it, but this design was simply not ready to be printed. I will go over why shortly, as well as how I designed my own to be easily laid down in plastic.
Step 1: The Phage Itself
If your only interest is in the model, or you are already a 3D printing wiz. Which don't have to be mutually exclusive, here are the STL files of every part. All should be sized correctly to be printed right off the bat... if not, please notify me. Assembly is pretty straight forward, just snap all the bits in the right places, using the photo above as reference. If something is loose, glue it. If something is too tight, file it a bit. The beauty of 3D printing is that you can resize, and do it all over again if need be.
Step 2: Support
The phage I found online looked similar to the ones above, but it was made to be printed all in one piece. This would require a massive amount of support material. The image above is of Scott K on thingiverse's print (check him out @dssguy1). I was not about to remove that amount of material, leaving broken off pieces of plastic all over the final product.
The need for support material arises when prints have overhangs (points in which the next layer of plastic must partially, or full extend beyond the bounds of the previous layer). When modeling my bacteriophage, I looked at the parts of this print, and found how to divide it up to remove unnecessary overhangs. This goes for all 3D prints, overhangs aren't the devil, but being mindful of your prints, and avoiding overhangs greater than 40 degrees will prevent the necessity of support material, vastly improving the quality of the print.
The icosohedron which carries the genetic material was a breeze to print, even with the overhangs at about 30 degrees. The overhang on the legs was removed by printing them on their sides. That of the hexagonal pieces on the top, and bottom of the base were fixed by simply inverting them, and having the "whiskers" print after the base of each object at 40 degrees. These simple improvements improved the quality of the print, decreased the amount of material used, and decreased the overall time the print takes.
Step 3: Complex Geometry
Above is a picture of the base of the print. This section seems very complex, and is not showing the highest quality in certain sections. As we were talking about in the previous section, you don't want overhangs over 40 degrees, but in the case of a circle, it is OK to have a complex overhang, as it will naturally bridge. This part looks intimidating, but with complex designs, it is necessary to get creative.
The original model had all kinds of crazy formations. Particularly, the section where the legs meet the base seemed unworkable. I knew I wanted to print the legs horizontally, and separate from the base. The legs of a phage are at an angle to the body, so I needed to find some interlocking mechanism that would allow this angle. In autodesk inventor, you can angle a hole by anchoring it to a rotated axis, so this is what I did. The legs may then be press fit at an angle. This is a very simple solution to what seemed like a complex problem.
When dealing with complex geometries, calm down, and think critically. most problems can be solved by a simple change of orientation... the base was printed vertically, I flipped it over, and wala, a flat surface. The whiskers were printed vertically, I flipped them over, and wala! A flat surface!... The point is, most complex geometry can be printed as long as there is a flat base, and no severe overhangs.
Step 4: Tolerance
Now you have a whole bunch of parts, how do they go together? Remember what I said before about tolerances not mattering. This is true in the sense that on the basic model, the printer does not care if you use 11cm, or 11.00001cm. But when it comes to the points of connection between prints, tolerance is everything.
Some people use clips, some people use a seperate set of pegs, for this model, and because I already had a good idea of what tolerances the printer was capable of producing accurately, I used pegs built into each part. As a general rule of thumb (at least for this printer), if you want parts to be press fit, subtract .65mm from the hole, and that is the diameter of your peg. Due to printer's inaccuracies, the peg will not have a uniform diameter, allowing for the greater points to lock your peg into place.
Step 5: Scaling
I am not a wizard, I did not design all of these parts to the perfect size. All of the parts had to be scaled up 2 times because they were too small to be printed accurately. The icosohedron was an stl file I found online, and it needed to be scaled up significantly. The legs were too small to be press fit into the base. The point is, you will make mistakes in scaling, but they are easily correctable.
In autodesk inventor, using the derive feature, you may scale the model directly. You will also want to export the stl file in millimeters, I have made the mistake of exporting in inches many times, ending up with a lil baby part. Don't use inventor? Never fret, most slicing software (I use Cura) includes a scaling function that you can view in real time, on your print bed. For a more permanent solution, as I used for the icosohedron, autodesk mesh mixer can be used to scale, and export a new stl file. (this program is great for editing stl files, and other meshes I highly recommend it)
Step 6: The End
I hope you have printed my model with success, and are on track to making your own. There are a few more aspects of 3D printing necessary to getting quality prints. Notably calibration, and clean up. I plan to post tutorials on these subjects, but in the mean time, check out these great sources for learning about 3D printing.
Maker's Muse: https://www.youtube.com/channel/UCxQbYGpbdrh-b2ND-...
What even is this stuff? http://www.3ders.org/3d-printing-basics.html
Why this no work? https://www.simplify3d.com/support/print-quality-t...
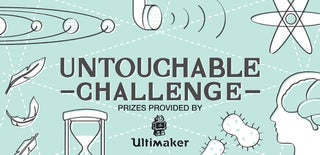
Runner Up in the
Untouchable Challenge
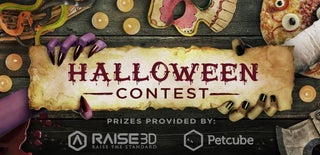
Participated in the
Halloween Contest 2017
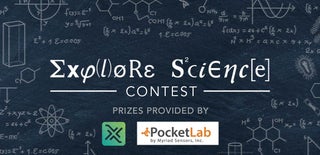
Participated in the
Explore Science Contest 2017