Introduction: 3D Printed Bike Light Cheap and Lifelong V2
Hi everyone,
There it is, a second version of the battery free bike light.
I really wish you'll enjoy making it for yourself, maybe with friends, maybe upgrading it ( please do it) but at least riding a bike with an eco friendly and lifelong working blinking light.
What a pleasure ! ( and made by yourself !
Ready ?
Step 1: Materials
There it is !
As I wanted this thing to be easy to reproduceI prepared a kit but also listed everything below for makers who'd like to make it by themselves in another way.
So here is the kit I prepared :
https://www.creationsab3d.com/products
or
in several links on eBay if you prefer :
https://www.cafr.ebay.ca/itm/302530409715
http://www.cafr.ebay.ca/itm/302530413178
And here is what you need in any case. You can find anything in your near hardware store or your favorite electronic shop :
- Relay 12 VDC
- LEDs x 2 red and x2 white at least 10 000 mcd
- Strongest neodymium magnet possible
- 1 x 10-32 screws and bolt
- 6 x 4-40 small screws
- 1x hose clamp
- 15 meters of PETG or ABS filament
- 3D models linked to the kit : everything is here my dear : https://www.thingiverse.com/thing:2643838
In order to avoid several deplacements, shipping fees,3D remodelling to fit with components etc....I personnaly thought it's way easier to regroup everything in a kit.
But as everyone has its own fun, I would be really happy to hear what you did and found out.
Step 2: Step 2 : Tools
About tools :
- a 3D printer able to print ABS or PETG ( you can try PLA but I don't advise it).
- a soldering iron
-a flat, philip and square ( yiii I know but it's so good) screwdriver
Step 3: Time
If you want to do workshops, or prepare this as a present or because you decided to become zero waste starting with this project as I did, believe it or not it takes less than 1 hour to assemble and mount it but around 4 to 6 hours of printing.
A bit long ?Well, that's right, but it works life long ! Try it, and you'll tell me what you think once riding.
- Count 1/2 hour in front of the screen to download and slice the 3D parts
- Count 4 to 6 hours of printing ( could be exponential if you print 0.05mm height - OMG ! - print speeds , etc ....)
- 15 minutes soldering and assembling the light
- 15 to 20 minutes to mount it on your bike.
Ready ? Let's go !
Step 4: Download and Slice 3D Models
There it goes !
https://www.thingiverse.com/thing:2643838
Actually there is no order in the way to do it but I just advice to do it this way
First : Print the first part called "liens" so that you can learn from your material if it's your first time with PETG ofr instance. It's an easy part to print permitting to check you do well.
Liens_angle = the rear light
Liens_droit = the front light
Infill 100% or at least enough perimeters so that the screws could be screwed very tight
Second : print boitier_k_44 (AB3D if you want to try having letters on it :))
I advise to print it as shown on the picture without any support it bridges pretty well
Infill 100% _ inside_out , same comment that above, at least enough perimeters to fill 100% the part.
Third : Magnetic supports or "supports_aimants"
I'll advise perimeters = 5 or more, same principle, mechanical forces would be applied.
At this time . I advise starting the next step of assembly as heating the soldering iron or .... having a break if you need one.
I personnaly started to learn how to draw ;)
For busy people, checking mails works very well.
Step 5: Soldering and Check Leds Direction
Aaaah this moment we all love .... Soldering !
Here is a bit tricky but only 3 components ( 2 LEDs, 1 coil).
1) Place the LEDs in the support so that the LEDs are in an opposite direction each other
(when magnet will pass over the coil it will make a positive and negative voltage AC to be said, check the video to better get it )
2) Place the coil as on the picture
3) Solder the LEDs on the coil
4) switch off the solder iron
and you know what ? That's it !
Congrats ! You made it !
N.B : Just check that LEDs work well, one should light when the magnet approaches and the other one when the magnet goes away.
If not you soldered both in the same direction, which is the wrong way.
Congrats ! You're making AC power !
Step 6: Put Everything in the Box and Screw Screw Screw !
As the title and the picture say.
Just put the last assemble in the box with the transparent top red or transparent transparent for the front light.
If you use glue, just don't use acrylic one to seal. It will blur the leds and drastically alffects the brightness
I advise epoxy if required ,normally it works press fit.
Take the largest screw, the "link" part and start screwing all the parts together.
( To be said, I deep fried the light in epoxy to seal it, and was pretty suprised of the finish, did I discover THE way to finish 3D printing ? hmmmm it's smooth but not perfect, would work on flat surface only but it hides very well the famous 3D printed lines).
Step 7: Pick Up the Magnets Supports
Are the supports of the magnet baked ? if not come back to this step when it's done.
Yes ? yyyyeeeee !... Ready then !
Place magnets on each sides of the support so that it will magically stand.
This is the best way I found to make them stand.
i know metallic support will help, but I'm afraid of rust, to be honest I'm working on it, while typing those words.
If you have any guess, I'll be happy to build together.
Step 8: Screw the Magnet on the Wheel
Time to install everything together .... trlrlrlrlrlrlrlrlr ( drum roll) ...
So screw the magnet supports on the wheel as shown on the picture. About middle height of the wheel.
( too high, the magnet will go too fast, no force, no light. Too low, will work ! but not as bright as half placed).
Notice : it must be pretty tight.
Not too much to crack the plastic but clearly enough to stay in position while turning high speed.
If you never experienced the well known "centrigual force" a crash course is gonna be offered to you.
In few words, you'll propulse in the air what you tried to fix on the wheel.
Anecdote : My first try was on my friend's bike ( I was very happy to film my first prototype way far from this model !). This guy just sprinted and in half a second, I could just hear " chbling " (magnet support leaving the wheel) followed by a " wwwwuuuu" (flying in the air)... might still be in orbital around the Earth.
Sir Musk or if you hear about it, please keep me informed. I try as much as possible to recycle the plastic I use.
Thanks by advance ;)
Step 9: Fine Tunning
Last step before the ride.
Slightly adjust the light on the bike frame. I must be very close to the turning magnet installed on the wheel.
it must be as close as possible ( 1 or 2 mm) without touching it. Adjust using the big screw.
And here is why printing at 100 pecent or 5 perimeters infill makes all its sense. you can screw very very very tight and then it won't never crack and neither move !
Lift the bike and give the wheel a spin...
There it goes Induction light is here.
Congrat yourself you did well, very well !
Step 10: Enjoy and Share
There it is ! Ride your bike !
( I'm actually waiting for my friend to film if it's still empty after the 20th of November 2017 mail me)
But ...
You made it ! YOU MADE IT ! Awesome !
You used the 3D printer to do something, useful, ecofriendly and zero waste.
THANK YOU for that ! I really hope you enjoyed doing it.
If you have any comment, remark to go further, I'll be more than likely to build it together.
Looking forward reading from you, I wish you the best everyday !
Regards,
Alex
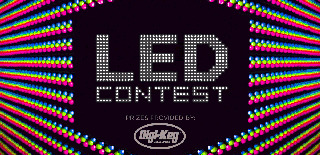
Participated in the
LED Contest 2017