Introduction: 3D Printed Bionic Hand Skeleton
So here goes: This is my first personal project, my first 3D printed project, my first Fusion 360 project and my first Instructable ever. (Crowds applauding and cheering and some high school girls whistling in the back). I guess you could say I was a “Virginstructable” before this …
A friend told me to “design something handy!” … so, I did.
I consider this 3D Printable Hand Skeleton as a baseline for a Bionic hand (which I intend to develop into a working Bionic hand with Arduino controllers and actuators). The design was done in such a manner so that all parts can be 3D printed without hassle or supports. I was a bit pressed for time because I really wanted to submit this project for a competition to win a new T-shirt; I really need a new T-shirt …
For THIS instructable the focus will be on how to work the 3D printed parts and how to build the components into something that works.
In this case, it will be a 3D Printed Hand Skeleton that open and close mechanically by means of elastic cords and ribbon.
Step 1: Design
I will very briefly describe the design process.
I designed the hand completely using Fusion 360 and a nice bottle of J&B. I quickly want to thank my girlfriend as well, if it wasn’t for her the design would’ve been done a week earlier. (High school girls in the back get up and leave.)
I found a picture that I used as inspiration to design the skeleton as close to the real human hand as possible. (A GREAT app for viewing the human skeleton and muscles is “3D Atlas of anatomy”! Try it)
I mostly used profile sketches and lofts for the modeling. I experimented with the “Sculpt” tool, but found that for THIS design I had more parametric control using profile sketches.
The rest of the process you can see in the FUSION 360 files. I don’t want to jabber on about all the little design intricacies but note that the main design intent is for 3D printing and motion (A hand without moving fingers is as useful as a wet sock). All components and fits were designed keeping it’s printing orientation and quality in mind. I would like to experiment with snap on ball joints in the future to make the model more accurate. I couldn’t do it in this run due to some limitations (That green paper that makes the world go round, and time!)
The fact that I designed the LEFT hand was completely by accident but if someone asks, “there is a wide range of complicated reasons for choosing the Left hand over the Right hand”.
Step 2: Get What You Need:
For simplicity, I will only include the tools I used. You can use your own discretion to use other tools as you deem them necessary. For instance, if you want to use a motorized chain saw to deburr some of the edges, which I am NOT recommending - be my guest, but please send a video!
3D Printing Service
Most important of all you will need a 3D printing service to print your components. (Kind of obvious, I guess). I am lucky enough to know a guy who knows a guy that owns his own 3D printer, whom I convinced with carefully selected words to give me a hand. Literally.
A Clean workspace
A clean workspace makes building and working much more enjoyable. If you prefer to sit on the floor with your dog licking your face while you grind pieces of plastic you are welcome to do so. I prefer a work table specifically allocated for the project though. It should have good lighting and a power point nearby if you are using any tools which require power.
Necessary Tools
You will most definitely need the following tools:
- · Small Pointed Tweezers - This is the tool that I will attach to my hand (my real human hand) if I could! I did almost everything with this handy little bugger!
- · Two-sided Nail File/Sanding paper - You will use this to finish and smooth out your 3D printed parts. It works best with a nail file that has two sides, one smoother than the other for a good finish.
- · Screw Driver - You will use this to tighten machine screws during assembly. Who could’ve guessed…
- · Scissors - You will have to cut elastic bands and ribbon.
- · A Lighter- We will find multiple uses soon. I am sure of it.
- · Small Hand Saw - Used to cut aluminum tubes into pins.
- · Punches - Used to flare out the pins’ edges
- · Small Hammer- Used to punch the punches, yes, really!
- · Ruler/ Vernier Calipers - to measure things of course.
- · Marking Pen - To mark things.
Optional Tools
The following tools are optional and might aid to accelerate and simplify the assembly and finishing processes.
- · Small rotary hand tool (from here on referred to as “Dremmel”). Can be used to open up some holes, drill holes, sand the 3D printed parts, cut screws to needed sizes, etc. I used a friend’s cordless Dremmel 7.2V. During the steps, I will point out what attachment you can use for the specific step.
- · IF you use the Dremmel, USE SAFETY GLASSES EVERY TIME!
- · Small heat gun - Can be used to fix the decolored 3D printed parts and to ‘reform’ the hoops through which the elastic and ribbon will be threaded. I used a normal cigarette lighter for this. Told you we will find a need!
- · A pair of working gloves - Tight fit gardening gloves will do the trick.
- · Insulation Tape - Can be used to mark your pins and screws for cutting.
3D Printed Parts
Here are the components you will need for this project. I named the 3D printed parts according to their “medical” names mostly because it is fun to say “phalanx”. I also creatively combined some names for my own personal enjoyment. I list them here in their respective sub-assemblies.
- 1st Digit (Thumb):
- Distal Phalanx 1 (DP1)
- Proximal Phalanx 1 (PP1)
- 2nd Digit (Index Finger):
- Distal Phalanx 2 (DP2)
- Middle Phalanx 2 (MP2)
- Proximal Phalanx 2 (MP2)
- 3rd Digit (Middle Finger):
- Distal Phalanx 3 (DP3)
- Middle Phalanx 3 (MP3)
- Proximal Phalanx 3 (PP3)
- 4th Digit (Ring Finger):
- Distal Phalanx 4 (DP4)
- Middle Phalanx 4 (MP4)
- Proximal Phalanx 4 (PP4)
- 5th Digit (Little/pinky Finger):
- Distal Phalanx 5 (DP5)
- Middle Phalanx 5 (MP5)
- Proximal Phalanx 5 (PP5)
- Metacarpals:
- Metacarpal 1 (MC1)
- Metacarpal 2 (MC2)
- Metacarpal 3 (MC3)
- Metacarpal 4 (MC4)
- Metacarpal 5 (MC5)
- Carpels:
- Captrap
- Hamatum
- Lunoid.
(FYI: These were named at 3am one morning and done for my own enjoyment. I combined the medical terms for the hand carpels:
- Capitate + Trapezoid = Captrap
- Hamate + Triquetrum = Hamatum
- Scaphoid + Lunate = Lunoid)
That amounts to a total of 22 3D printed parts (Excluding “Sample Parts”). Don’t panic!! They are small and easy to print!!
I furthermore suggest that you print a SAMPLE DIGIT (For e.g. print an extra Pinky – DP5, MP5 & PP5; you can use this digit to test some steps on so that you don’t completely mess up a component in the main assembly!).
You can view and download the parts through the following link: http://a360.co/2qmdVpw
Bought Parts:
You will also need the following fasteners / bought parts:
- M3 x 16 ‘CSK Machine Screws’ [QTY 12]
- M3 x 25 ‘CSK Machine Screws’ [QTY 11]
- M4 x 75 ‘CSK Machine Screws’ [QTY 2]
- M3 Nuts [QTY 33]
- M4 Nuts [QTY 2]
- Elastic Cord +Ø2mm [ + 2.5m]
- 3mm Ribbon [ + 2.5m]
- 3mm Aluminum/brass tubes [250 mm]
(*These are all in Metric units - I strongly believe the rest of the world is moving to metric units inch by inch.
*CSK = Counter sunk!)
Step 3: 3D Printing
As mentioned before, this is my first 3D printing project and I am quite the novice (FOR NOW) when it comes to this step. I watched multiple videos with regard to design for 3D printing during the design phase to ensure printable parts. I’m not going into those details too much as it is an Instructable topic of its own.
The friend of a friend was kind enough to give me a few details of the printer and settings he used:
- -Pruza i3 MK2S 3D printer
- -0.4mm Nozzle
- -1 layer raft with 70% infill
- -0.2mm Layer Height
- -3 Top Layers, 3 Bottom Layers, 2 Perimeter Shells
- -Infill +- 15%
- -Extruder 215deg on Layer 1, 205deg on rest
- -Heated Bed 55ᴼ Celsius
- -1.75mm PLA Filament.
Two parts failed that were printed without the raft as they toppled over during the printing.
We concluded that the raft is therefore a
good choice, but not 100% needed, as a lot of parts were successfully printed without any rafts.
Step 4: Part Post Processing
The first thing to do after you have received your parts is to give the bloke who printed your parts (even if that bloke is yourself) a big hug and a bottle of whisky, or ice tea, or cold hard cash. In my case it was cold hard cash.
The parts will need a bit of attention now to ensure good fits. They were all designed with generous (but not TOO generous) tolerances. I fitted the parts directly after printing and removing the rafts, and found that they all fitted well, but the motion was “scratchy” because of the contact surfaces and that the elastic cord was slightly too big to just slip through some of the loops. I decided to smooth out the contact surfaces, open the loops a bit and remove some irregularities.
So, there are two main objectives in this step:
- Ensure smooth movement and fits between parts.
- Ensure the loops for the elastic cord and ribbon are big enough.
Smoothing Surfaces and Clearance Holes
You will need the following tools for this step:
- M3 CSK SCREWS AND NUTS
- Nail File / Dremmel
- Tweezers
Assemble the respective fingers using the M3 x 16 CSK SCREWS AND NUTS-M3 X 25 CSK for the Thumb pieces. You might have to use the tweezers to remove some strands of PLA in the holes and on the bases. I just fidgeted the screws through in most of the parts and removed the rafts with tweezers.
Push, pull and rotate the different parts (don’t BREAK the parts, you animal!). You will be able to feel and hear which joints need the most attention. Then proceed to gently file and round the heads and bases of the parts. Gently file them as if you are an elderly woman sitting in a salon getting your hair permed. Test them regularly to feel the difference you have made. When you are satisfied with the movement, you can use the Dremmel with a polishing head OR the smooth side of the nail file to finish it off. After that you can gently use the heat gun on your worked surfaces to fix the decolorization. (I didn’t do this because I don’t have a heat gun and stuffing the parts into the oven seemed a bit excessive).
You don’t have to worry about the insides of the bases too much. You can use the tweezers to remove some unwanted strands on the inside, but the smoothed heads will be good enough for smooth motion.
Note: If you used the Dremmel, be careful not to completely destroy your parts!! Use low settings and GENTLY graze the surface with the tool.)
Opening up the Loops
This step needs to be handled with a lot of caution and should only be done if it is absolutely necessary!
PLA is extremely sensitive to heat but you can use it here to your advantage (and certainly at your own risk). Practice this a bit first on your SAMPLE PARTS before applying it to your main parts!
You will need the following:
- Tweezers
- Lighter (Or heat gun)
- Small piece of elastic rubber and ribbon
FIRSTLY, try to fit the elastic band and ribbon through the loops. Identify the loops that will need some opening. I only had to open up the loops on the Distal Phalanges (DP1-5) and MP5.
Gently apply the flame to the loop that needs opening. Not more than 2 seconds! And quickly but GENTLY stretch the loop with the tweezers’ points. The PLA hardens fairly quickly so you need to “Ninja” this step. You will most probably only have to do this to the inside part of the finger.
I stress again: PRACTICE this step on your SAMPLE parts first! In the pictures, you can see I used a failed print to practice with.
Now that our 3D printed parts are all processed and ready to mingle, you can preassemble them. Use the M3 screws to keep your parts in their respective subassemblies. (Build the fingers so that you can see where each part goes! You don’t want to end up with messed up fingers … Nobody does).
We can now move on to the cutting of our pins and screws.
Step 5: Cutting the Pins, Screws, Elastic Cord and Ribbon
The objectives of this step are fairly well described in the title of this section:
- Cut the pins to size
- Cut the screws to the right sizes
- Cut the ribbon and elastic band to usable sizes.
Note: If you use the Dremmel, you need to hold the parts with a piece of cloth or a glove. The parts get quite hot during the cutting process! The specified lengths are ‘more-or-less’ and you don’t have to worry if you have cut it slightly smaller or larger.
Cutting the Pins
You will need the following:
- Hand Saw/ Dremmel with Grinding disk (AND SAFETY GLASSES)
- Ruler or Vernier Calipers
- Ø3mm Aluminum/Brass tubes
- Optional: Insulation tape & Nail File/ Sanding paper
I suggest executing this step in the following manner: Measure-Cut-Measure. Your tool will remove a segment from the tube so rather cut a piece, THEN measure out the next piece. Push the piece you want to cut firmly on the long side with the edge you want to cut hanging over an elevated edge. I used a piece of offcut wood. You want to have your work piece pushed down firmly before you start the cutting. Make a small marking with your cutting tool and gradually work through the work piece. This applies to the cutting of the screws as well.
You will need to cut the following lengths and quantities of aluminum pins from the tubes:
- +- 15mm, QTY =12
- +-18mm, QTY = 2
Cutting the Screws
You will need the following:
- Hand Saw/ Dremmel with Grinding disk (AND SAFETY GLASSES)
- Ruler or Vernier Calipers
- M4 x 75 CSK screws [QTY = 2]
- Marking Pen
- Optional: Insulation tape & Nail File/ Sanding paper
You want to cut the two long screws so that they don’t stick out at the bottom of your assembly. You can mark them with a marking pen or use the tape. Stick a piece around the inside of the screw to mark the edge where you want to cut.
You will need to cut two M4 x 75 CSK screws to the following sizes (measured from the head to the tip):
- 58mm
- 56mm
You can finish off the cut edges of the pins and screws with a file or sandpaper if you find it necessary.
Cutting the Elastic Band and Ribbon
You will need:
- Ribbon and Elastic Cord
- Scissors
- Lighter
- Ruler or Vernier Calipers
You need to cut the following lengths and quantities. You will find later that you need much shorter lengths but it’s always easier to cut a piece off than it is to sew it back on; that’s why I suggest the following lengths:
- Ribbon: 350mm; QTY = 5 PIECES
- Elastic Cord: 300mm; QTY = 5 PIECES
Cut a triangular tip on the one side of each piece of ribbon and tie a triple knot in the other end of it; you can snip off the short end coming out of the knot. Use the lighter to slightly singe the tips of the elastic cord and ribbon. Prepare 5 pieces of each.
Note: The knots in the ribbon will be used as a “Stop” in the assembly. Make sure it doesn’t slip through the hole on the tips of DP1-5 if you pull on it. IF it slips through- just tie another knot over the existing one.
Good. Now we have all the parts to start the assembly. But first I think you should put a band aid on that nasty cut on your finger and remove the piece of grinding disk from your eye because you didn’t wear your safety glasses. (WEAR YOUR SAFETY GLASSES!)
Step 6: Assembly
We will assemble the hand in the following manner:
- First the fingers/ Digits and their respective Metacarpals.
- Then the Base – With the Thumb digit included
- Lastly, we will attach the Digits to The Carpels/Base.
Digit/Finger Assembly
You will need:
- Punches
- Hammer
- Tweezers
- 3D Printed Parts
- Cut Pins
- Cut Ribbon & Cord
I will only demonstrate and guide you through the assembly of one digit. The rest are done in exactly the same manner. The 2nd to 5th Digits use the 15mm pins. The 1st Digit Uses the 18mm Pins. You can choose to keep the fingers assembled with the M3 x 16 screws, but they will cause interference in the assembly and restrict motion of the fingers.
First, we will slide the cord through. If you have opened up the hoops correctly, this step should be fairly easy. Gently push the one end of the cord through the hoops ON THE INSIDE as indicated. You can use the tweezers to assist you. Leave a generous piece sticking out at the tip as we will tie that into a knot soon.
Next you want to slide the piece of ribbon through. Slide the end that you cut through the small hole in DP1-5 from the bottom. The knot you made should not slip through the hole. Pull on the ribbon to ensure the knot does not slip through. You can proceed to slide the ribbon through the remaining hoops.
Now tie the knot in the cord on the end that sticks out the end of the finger - make sure it’s tight and doesn’t fit through the hoop.
For the pin connections, we will punch the punches! Take a pin that you have cut and slide it through the connection point. I kept the fingers assembled with the screws up to this point. Take the screw out and replace it with the pin. Position the work piece so that the pin’s one end rests on a hard surface (I used a small piece of scrap aluminum sheet) and the other end is open for punching. Insert the punch and hold it carefully. Gently tap the top of the punch with a hammer. Do the exact same thing to the other side. Two hits on each side and one on the thumb did the trick for me.
You will have to put in 14 pins like that.
Note: Make sure you attach the correct 3D printed parts to each other in the correct orientation - When the pins are flared out it is extremely hard to remove them without damaging your 3D printed part!
The final step for the digits is to tension the elastic cord on the inside and tie another ‘stop knot’. Hold on to the MC part and pull on the cord - the finger should “close” when you do this. You can slightly tension the chord and tie a knot that is bigger than the loop. Tie one to two knots so that the cord doesn’t slip through the loops.
I played with the tension a lot and found that you don’t want to pre-tension the cord a lot. You basically want to close the finger and tie the knot. The finger should be closed now by default. You can experiment with the tension of the cord. Play with it by holding the base piece (MC2-5) and pull on the ribbon. When you are happy with the tension, cut off the excess cord. Do this with the 2nd to 5th Digits (DO NOT tie the bottom knot in the cord for the Thumb/1st Digit).
Congratulations- you have now made a few AWESOME looking shrimps!! Note that the thumb’s cord does knot have a not at the bottom (see what I did there?).
Base and Thumb assembly
You will need:
- 3D printed parts
- Screw driver
- The cut M4 SCREWS and NUTS
- M3 x 25 CSK SCREWS [QTY 9]
- M3 NUTS [QTY 19]
- Tweezers
- Insulation tape
- Scissors
Take the M4 screws and put it through parts as indicated. The Captrap gets the longer one of the two.
Use the tweezers and screw driver to tighten the parts together. Make sure that the “Captrap” part is not tightened too much and that the thumb can freely pivot around the screw. Also ensure that the screw’s head sits flush on the inside so that it doesn’t interfere with the fingers later on (picture).
Pull the thumbs cord through the middle of the Captrap and Hamatum. I slid it through the crease from the top. Now tension the cord so that the thumb moves inward and tie yet another ‘stop knot’ in the cord. Cut off the excess cord if you are happy with the tension.
Now assemble the fingers to the base. Use the M3 x 25 CSK screws and nuts to fasten the fingers to the base. Slide the loose ribbon ends through the hoop at the back of the base.
We are almost done!
We will now make small make-shift handles to operate the fingers with.
Take a M3 x 25 CSK SCREW and 3 nuts. Fasten two nuts to the middle and one on the end as indicated. Cut small pieces of tape and wrap it around the two sides of the screw.
Tie the loose ribbon end to the screw in the middle. Wrap it around a few times at the length you wish to have it and tie a knot. I suggest you have a bit of 'rope' so that you can easily grab the little handles.Do this 5 times.
Step 7: Congratulate Yourself!
Congratulations! You have now officially built the baseline for a Bionic hand (applause and cheers!). You can now proceed to play with your new left hand (a sentence a think no one will ever want to hear again)! Pull on the little handles and make the individual fingers move. Pull on all 5 to open up the palm of the hand. You can see in the video that I attached the Model to a piece of wood. I screwed in some hooks just to keep the ribbons in tension so that I could take photos.
I have mentioned this, but keep in mind that I have done this project with the intent for further development, which I am busy with. This entire project cost me about R450, with the 3D printed parts at about R400. You can play around with the configurations of the ribbon and cord, you can attach servos and actuators, you can make design changes to have ball joints on the fingers - you can do ANYTHING you want - just have fun!
If you do something cool with it- Please feel free to let me know!
I hope you enjoy this project as much as I did!
Step 8: STL's
As requested- STL files! Please post pictures on here when you print the project. Would like to see it!
Woop Woop!
Attachments
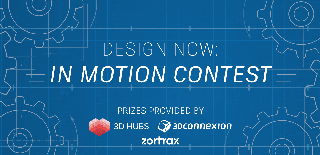
Second Prize in the
Design Now: In Motion Contest