Introduction: 3D Printed DIY Steampunk Coat Hook
Our back entry is the place where our family does most of its coming and going, and though we have some coat hooks on the wall, there never seem to be enough. Not only that, one particular family member is an independent four-year-old who doesn't want help from anyone, yet isn't tall enough to reach any of the coat hooks. I am sure you can guess how fun that can make the coming and going process....
I was sent a 3D printer to try out (the Lotmaxx SC-10-paid link), so I figured why not try and design some unique coat hooks that we could install at an appropriate height for our daughter. That way, I could organize the space in our entryway and keep a little girl happy at the same time.
Here are the tools and materials I used:
- The stl files I made during the course of this project. They are free on my webpage.
- 3D Coat : The modeling program I used to design the coat hook.
- 3D printer: I used a FDM printer, the Lotmaxx sc-10 (paid link)
- PLA filament: I used Esun PLA+ (paid link)
- Super Glue: For gluing the halves together, the swirly sides, and the center strip.
- Paint: I like to use artists acrylic paint. I used Liquitex Basics: Mars Black as well as DecoArt Americana Decor Metallics: Vintage Brass (paid links)
- Sealer: I used Pledge floor gloss (paid link)
- Rubber Gloves: For applying the metallic paint, and while gluing.
- Heat Gun: For forming the center strip and side swirls. I used the awesome Furno 700 (paid link)
As an Amazon Associate, I earn from qualifying purchases, which means if you make a purchase after clicking one of these links, you won't pay any more, but I will receive a small commission. Thanks!
Step 1: Design Time
Most of my designs are steampunk related, and this one was no exception. The concept I had was of an old switch that might be used to turn on and off some kind of cool, neo victorian contraption. The lever of the switch would be the actual hook for hanging things on. I also wanted to add a bit of over-the-top style to the coat hook, so I decided to add a few fantastical embellishments.
In order to hide the screws that would hold the hook to the wall, I decided to make the actual lever section separately from the base, with a friction fit to hold it in place, hiding the screws.
I split the toggle section into two parts to reduce the layer lines and overhangs on the final piece. I added some holes for alignment pins so that it would be easy to glue the halves together.
The one gripe I have with a lot of 3D printed objects is the obvious layered look that can happen, which is why, sometimes I would rather have a slightly more complicated build if it will mean that the final project will look more realistic or cut down on the amount of cleanup after printing.
I designed these pieces using a program called 3DC printing, which is a scaled-down version of 3D coat software.
Step 2: Slice It Up
Slice the files in preparation for printing. I used Cura, but use whatever slicing program you are comfortable with.
You can see the settings I used in the second picture, but you may need to use whatever settings work best for your particular printer.
Step 3: Get Printing!
Print the parts.
I printed the design twice, once using Overture PLA filament, and once using Esun PLA+.
Step 4: Sand It Smooth
Sand the dome and toggles to remove the layer lines.
I sanded everything using wet/dry sandpaper with water on it to keep the plastic from melting with the friction and to prevent the sanding dust from getting in the air.
Use 80 Grit sandpaper first to remove the lines and then 150 grit to smooth out the coarse sanding marks and then some 320 grit to get it all really smooth.
You can use a piece of wood to wrap the sandpaper around in order to get in nice and close along the edges and to keep the rims nice and flat.
Don't bother sanding inside the dome as you don't want to change the fit of the toggle piece.
Sand only the front and back flat sections of the toggle as well as the little cylinder handle bit. The gear section would be more trouble than it is worth and looks fine with the layer lines left in it.
Step 5: Test Fit the Toggle
Insert the half-cylinder alignment pins in the toggle and push the two halves together. If it is too tight, sand a little off the alignment pins beforehand so it is not too hard to get apart again!
Step 6: Two Halves Become One
Apply a little super glue to one-half of each of the three alignment pins, and push them all the way into their holes.
Apply glue to the flat inside of the toggle, as well as the protruding section of the alignment pins.
Squeeze the two toggle halves together and hold them tightly as the glue cures.
Step 7: Toggle Trimming
I made two of these coat hooks using different filaments and different printers. On one, the toggle fit perfectly into the base, but on the other, it was a little too tight.
You may need to sand down the outside of the tab, as well as trim a little off the edges with a knife until it will slide down into the slot with only moderate pressure.
Step 8: Forming the Side Swirls
The absolute best thing about PLA filament is that you can heat it up and it becomes super flexible without becoming sticky or deforming too badly. I love it!
Put on a pair of insulating gloves.
Slowly heat the swirl piece with a heat gun until it gets a little bit floppy. Don't heat it too fast or it could overheat. I had my heat gun set at 340 deg C (650F) but it may depend on the heat gun you use.
Press the swirly piece against the dome and hold it there until it cools.
If there are parts that aren't completely formed to the dome, you can repeat the procedure until it fits perfectly.
Repeat for the second swirl.
Step 9: Glue on the Swirls
Put on a rubber glove.
Glue the swirls on to the sides of the dome with super glue.
Step 10: Bend and Glue the Rivet Strip
If your center seam isn't perfect, that's okay because now you can cover it up with a strip of rivets.
Using your heat gun, slowly heat the strip until it becomes flexible. Then quickly form it around the toggle.
Glue it in place with super glue.
Step 11: Just a Little More Sanding
Now that the swirls are glued on, you have a nice solid base to sand against, so sand out those printing marks.
Step 12: Paint It Black
Paint everything black.
I used artists acrylic paints, but you can use whatever paints you prefer.
The reason I like the acrylics is that they are thicker than sprays, and so cover up some of the sanding marks you may have left behind.
Don't paint the slot in the dome or the tab on the toggle, as you don't want the paint on the two parts to stick together when you assemble the coat hook. Then it might be really hard if you ever need to access the screws to remove the hook.
Step 13: Do Some Finger-painting
My favorite metallic paints tend to change over time, but right now I am liking DecoArt Americana Decor Metallics Vintage Brass for the brass look.
My technique for creating an antique metal look is as follows:
- Put on a tight-fitting rubber glove. This keeps your hands clean and prevents fingerprint smears in your metallic coating.
- Put a small blob of metallic paint onto a piece of scrap cardboard or paper.
- Dip your fingertip lightly into the paint and then rub it onto a clean section of cardboard.
- Rub in a circular motion until almost all the paint is off your finger.
- It is especially important to watch the tip of your finger because paint can build up there, so you want to rub off any accumulation that occurs.
- Rub your finger on the parts that you want to paint. Slowly build up the metallic colour, repeatedly going back and getting more paint on your finger.
Step 14: Getting in the Cracks
If there are places your finger can’t reach, you can use a small, dry paintbrush. Dip the brush in the paint and then dab most of it off on the cardboard. Use a vertical dabbing motion to apply the paint, again building it up slowly. It is good to stay away from inside edges as the antique look requires sections that would get less wear to look darker.
Once the paint was completely dry I applied a coat of Pledge floor gloss to seal and protect the paint, but you can use whatever sealant you prefer.
Step 15: Go Hang Up Your Coats... or Boots.
Time to put that hook on the wall!
Make sure you use an appropriate fastener for the type of wall you are anchoring it to.
That's it, you now have some sweet steampunk toggle coat hooks!
The hooks I made were reasonably strong, however, that depends on how well they are printed, so it is your responsibility to make sure they are strong enough for whatever you are going to hang from them.
Thanks for hanging out with me! If you'd like to see more of my projects you can find me here:
Subscribe to my YouTube Channel
Follow me on Instagram
Check out my pattern shop
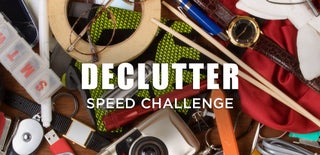
Participated in the
Declutter Speed Challenge